Instrukcja obsługi V-TAC VT-AU450-36V
V-TAC
panel słoneczny
VT-AU450-36V
Przeczytaj poniżej 📖 instrukcję obsługi w języku polskim dla V-TAC VT-AU450-36V (1 stron) w kategorii panel słoneczny. Ta instrukcja była pomocna dla 17 osób i została oceniona przez 2 użytkowników na średnio 4.5 gwiazdek
Strona 1/1
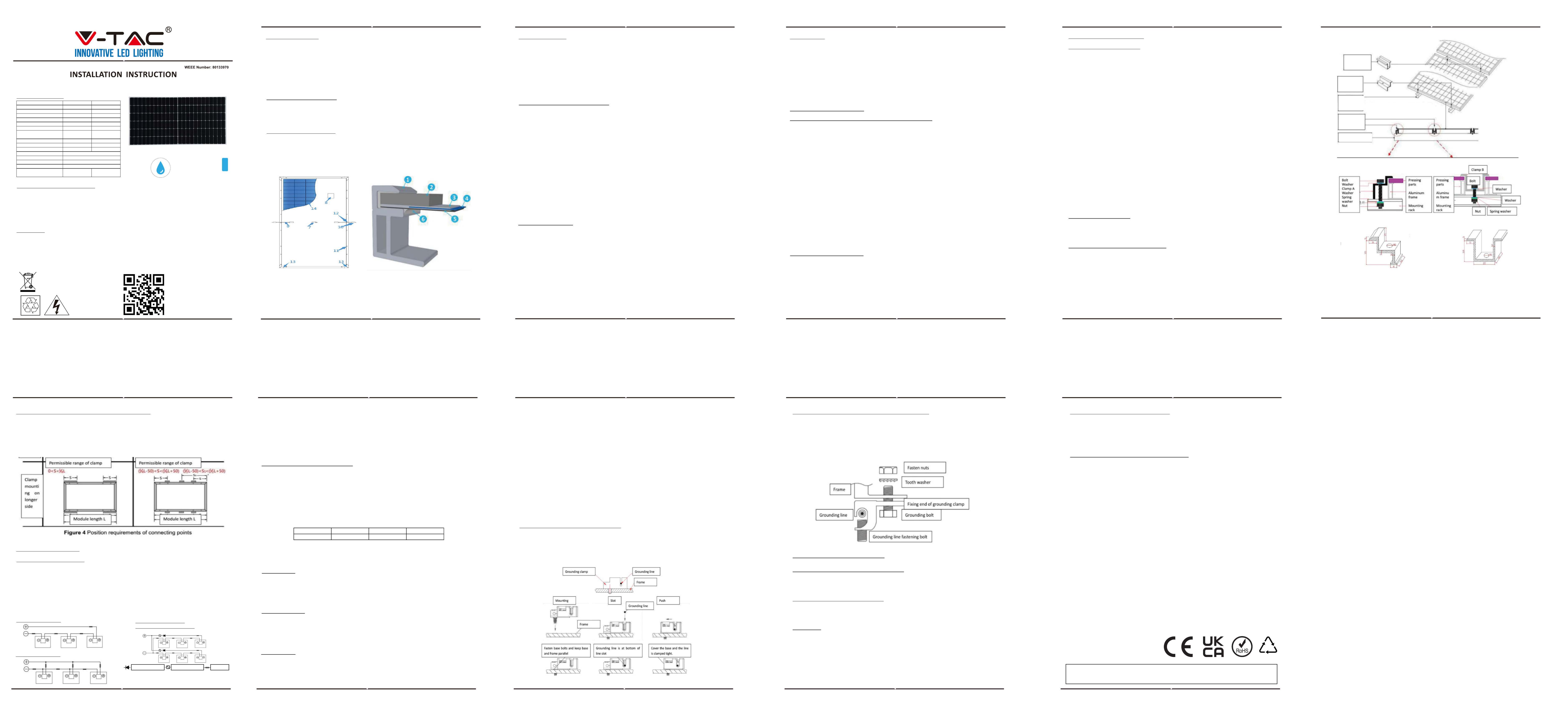
MONO SOLAR PANEL
TECHNICAL DATA:
INTRODUCTION & WARRANTY
Thank you for selecting and buying V-TAC product. V-TAC will serve you the best. Please read these instructions
carefully before starting the installation and keep this manual handy for future reference. If you have any
another query, please contact our dealer or local vendor from whom you have purchased the product. They are
trained and ready to serve you at the best. The warranty is valid for 10 years from the date of purchase. The
warranty does not apply to damage caused by incorrect installation or abnormal wear and tear. The company
gives no warranty against damage to any surface due to incorrect removal and installation of the product. This
product is warranted for manufacturing defects only.
This installation manual does not entail any explicit or implicit quality warranty and does not stipulate on
compensation schemes for losses, module damages or other costs caused by or related to module installation,
operation, utilization and maintenance process. If patent rights or the third party rights are infringed by use of
modules, V-TAC will not take any responsibility. V-TAC reserves the rights for modifying product manual or
installation manual without notice in advance.
If customers fail to install modules as per requirements set forth in this manual, the quality warranty provided
for customers during sales will become invalid. In addition, suggestions in this manual are to improve safety of
module installation, which are tested and proved by practices. Please provide this manual to PV system users
for reference to and advise them of safety, operation and maintenance requirements and suggestions.
V-TAC module is considered to be in compliance with IEC61215 and IEC61730 only when the module is mount-
ed in the manner specified by the mounting instructions below.
When the module is installed on roof, it is necessary to take the overall fire rating of the finished structure as
well as later overall maintenance into account. The roofing PV system shall be installed after assessment by
construction experts or engineers and with official analysis results for the entire structure. It shall be proved
capable of supporting extra system bracket pressure, including PV module weight.
For your safety, please do not work on the roof without safety protective measures which include but not
limited to fall protection, ladder or stair and personal protective articles. For your safety, please do not install or
handle modules in unfavorable conditions including but not limited to strong wind or gust, damp or sandy roofs.
INTRODUCTION Regular safety
Low/normal load working condition applies to most environments: the maximum static load for backside is
1600Pa*1.5 (equal to wind pressure) and the maximum static pressure for the front side is 1600Pa*1.5 (for 4
clamps installation) (equal to wind pressure and snow pressure).
Higher load applies to severe environments (such as wind storm, heavy snow): the maximum static load for
backside is 1600Pa*1.5 (equal to wind pressure) and the maximum static pressure for the front side is
3600Pa*1.5 (for 6 clamps installation) (equal to wind pressure and snow pressure).
The number of modules in series connection in each strand shall be calculated as per requirements. The open
circuit voltage value under the expected lowest temperature shall not exceed the maximum system voltage
value stipulated for modules (V-TAC module maximum system voltage is DC1500V according to IEC61730) and
other values required by DC electric parts.
Maximum series overcurrent protective device, where required.
If there is reverse current exceeding the maximum fuse current flowing through the module, use overcurrent
protection device with the same specifications to protect the module; if parallel connection strands are more
than 2, there shall be an overcurrent protection device on each strand of module. See Figure 5.
The grounding device shall be in full contact with inner side of the aluminum alloy and penetrate the frame
surface oxide film.
Do not drill additional grounding holes on module frame.
To get the optimal power output, V-TAC suggests that DC negative pole of the module array shall be grounded
in installation of modules. Otherwise, the system power output will be reduced.
Module installation methods can not lead to electrochemical corrosion between module aluminum frame and
different metals. Electrochemical potential difference of contacting metals shall not exceed 0.6V as is recom-
mended in IEC61730 Appendix Flat Plate Photovoltaic Modules and Panels.
Holes on the frame shall be drilled in advance and grounding signs shall be indicated. These holes are only used
for grounding but not for installation of modules.
A module with exposed conductive parts is considered to be in compliance with IEC61730 only when it is
electrically grounded in accordance with the instructions presented below and the requirements of the National
Electrical Code.
Where common grounding hardware (nuts, bolts, star washers, spilt-ring lock washers, flat washers and the
like) is used to attach a listed grounding/bonding device, the attachment must be made in conformance with
the grounding device manufacturer’s instructions.
V-TAC recommends must thoroughly detail the attachment means in the module installation instructions.
Common hardware items such as nuts, bolts, star washers, lock washers and the like have not been evaluated
for electrical conductivity or for use as grounding devices and should be used only for maintaining mechanical
connections and holding electrical grounding devices in the proper position for electrical conductivity. Such
devices, where supplied with the module and evaluated through the requirements in IEC61730, may be used
for grounding connections in accordance with the instructions provided with the module.
Grounding methods below are permissible:
Grounding by grounding clamp
There is a grounding hole with the diameter of Ø4.2mm at the edge of the module back frame. The central line
of the grounding sign and that of the hole overlaps and is consistent with the frame length direction.
Grounding between modules shall be confirmed by qualified electricians and grounding devices shall be manu-
factured by qualified electric manufacturer. The torque is recommended to be 2.3N•m. 12 AWG copper core
wire is used for the grounding clamp. And copper wires can not be pressed damaged in installation.
Mounting holes on modules that are not occupied can be used for installing grounding devices.
1.Align grounding clamp to the frame mounting hole. Use grounding bolt to go through the grounding clamp
and frame.
2.Put the tooth side of the washer on the other side and fasten the nuts. The recommended torque for nut
fastening is 2.0Nm to 2.2Nm.
3.Put grounding lines through the grounding clamp and grounding wire material and dimension shall meet
requirements in local national and regional law and regulations.
4.Fasten bolts of grounding lines and installation ends.
In module design, adopt enclosed connecting boxes with the protective level of IP68 for onsite connection to
provide environmental influence protection for wires and connections and contacting protection for non-insulat-
ing electric parts. The connecting box has well connected cables and connectors with the protective level of
IP68. These designs facilitate parallel connection of modules. Each module has two independent wires connect-
ing the connecting box, one is negative pole and the other is positive pole. Two modules can be in parallel
connection by inserting the positive pole at one end of wire of one module into the negative pole of the adjoin-
ing module.
Cables connecting modules shall satisfy the module maximum short circuit current. Adopt the special PV
system sunlight resistant cables.
The minimum standards of cables connecting modules are:
When cables are fixed on the bracket, avoid mechanical damage to cables or modules. Do not press cables by
force. Adopt special designed light resistant wires and clamps to fix cables on the bracket. Though cables are
light resistant and water proof, it is still necessary to prevent cables from direct sun radiation and water immer-
sion.
Please keep connectors clean and dry. Make sure connector nuts are fastened before connection. Do not
connect connectors that are damp or dirty or under other status. Protect connectors from direct sun radiation
and water immersion or fall onto ground or roof.
Wrong connection may lead to electric arc and electric shock. Please make sure that all electric connection is
reliable. Make sure all connectors with lock are fully locked.
Module electric performance parameters such as Isc, Voc and Pmax nominal values have ±3% error with those
under standard testing conditions of: irradiance of 1000 W/m2, cell temperature of 25 and air mass of AM1.5.C
Under normal conditions, a photovoltaic module is likely to experience conditions that produce more current
and/or voltage than reported at standard test conditions. The requirements of the National Electrical Code (NEC)
in Article 690 shall be followed to address these increased outputs. In installations not under the requirements
of the NEC, the values of Isc and Voc marked on this module should be multiplied by a factor of 1.25 when
determining component voltage ratings, conductor ampacities, overcurrent device ratings, and size of controls
connected to the PV output.
When modules are in series connection, the final voltage is sum of that of the single module. When modules are
in parallel connection, the final current is sum of the single module. See Figure 5
Modules with different electric performance models can not be connected in one series.
Position of installation connecting points
Cables and connecting lines
Grounding by unoccupied mounting holes
Figure 7 Way of Installation
The third party grounding devices
Operation and maintenance
Connector
V-TAC solar module connecting box contains bypass diode which is in parallel connection with the cell strands.
If heat spot occurs locally with the module, the diode will come into operation to stop the main current from
flowing through the heat spot cells with the view to restrain module heating and performance loss. But bypass
diode is not the overcurrent protection device.
If the diode is found or doubted to get out of order, the installer or system maintenance supplier shall contact
V-TAC. Please do not try to open the module connecting box on your own.
Bypass diode
In design of modules, the anodized corrosion resistant aluminum alloy frame is used for rigidity support. For
safety utilization and to protect modules from lightning and static-electricity damage, the module frame shall
be grounded.
Grounding
Electric installation
Electric performance
Please consult local laws and regulations before installing modules and abide by requirements on building fire
protection. Fire rating of V-TAC modules is TypeC according to IEC61730.
The roof shall be coated with a layer of fireproof materials of such rating for roofing installation and make sure
that the back plate and the mounting surface are fully ventilated.
Difference of roofing structures and installation modes will affect fireproof performance of buildings. Improper
installation may lead to fire disasters.
To guarantee roof fire rating, the module frame shall be at least 10cm from the roof surface.
Adopt proper module accessories such as fuse, circuit breaker and grounding connector according to local
regulations.
The fire rating of this module is valid only when mounted in the manner specified in the mechanical mounting
instructions.
Please do not use modules if there are exposed inflammable gases nearby.
The modules can only be used on earth but not in outer space.
Do not focalize sunlight with mirrors or magnifying glass artificially onto modules.
V-TAC modules shall be installed on proper buildings or other appropriate places (such as ground, garage,
building outer wall, roof, PV tracking system) but shall not be installed on any mobile vehicles.
Do not install modules at such places as that are possible to be submersed. V-TAC suggests that modules be
installed in the working environment with the temperature of -20 to 46 which is the monthly average highest
and lowest temperature of the installation places. The extreme working environment temperature for modules
is -40 to 85 .
Make sure that installed modules do not suffer wind or snow pressure that exceeds the permissible maximum
load.
Modules shall be installed in places free from shades throughout the year. Make sure there are no light-blocking
obstacles in the installation places.
Carry out lightning protection for modules installed in places with frequent lightning and thunder.
Do not install modules in places with possible inflammable gases.
Modules can not be used in environments with too much hails, snows, flue gas, air pollution and soot or in
places with strong corrosive substances such as salt, salt mist, saline, active chemical steam, acid rain, or other
substances corroding modules, affecting module safety or performance.
Please take protective measures to ensure reliable and safe installation of modules in severe environments such
as heavy snow, cold and strong wind or islands close to water and salt mist or deserts.
Make sure that module installation mode and bracket system are solid enough to bear the expected load,
which is requisite assurance that the bracket installer must provide. Installation bracket system shall be tested
and inspected by the third party testing institution with static mechanical analysis capacity in accordance with
local national or international standards.
Module bracket shall be made from durable, corrosion resistant, ultraviolet proof materials.
Modules shall be fixed on the bracket solidly.
Use higher brackets in places with heavy snow accumulation so the lowest point of modules will not be
covered by snow for a long time. In addition, make the lowest point high enough so as to avoid sheltering of
vegetations and woods or damage of flying sands and stones.
If modules are installed on brackets parallel to the roof or wall, the minimum gap between the module frame
and the roof/wall shall be 10cm for air ventilation so as to prevent module line damage.
Do not make holes on glass or frame of modules.
Make sure the building is suitable for installation before installing modules on roof. Moreover, seal permeable
parts properly to prevent leakage.
The module frame has thermal expansion and cold contraction so the frame interval between two adjoining
modules shall be less than 10mm.
Make sure that back plate of modules will not contact bracket into the module or building structures,
especially when the module surface is imposed by pressure.
V-TAC Solar Modules have been certified for a maximum design static load on the back of the
Modules of up to 1600Pa*1.5 (i.e. wind load) and a maximum design static load on the front of the
Modules of up to 3600Pa*1.5 (i.e. wind and snow load), depending on the clamp mounting (please refer to
follow installing data for this information). And this is printed on the label of modules.
Module installation methods can not lead to electrochemical corrosion between module aluminum frame and
different metals. Electrochemical potential difference of contacting metals shall not exceed 0.6V as is recom-
mended in IEC61730 Appendix Flat Plate Photovoltaic Modules and Panels.
Modules can be installed horizontally or vertically.
Fire safety
Installation conditions
Mechanical installation
Installation site and working environments
Regular requirements
Module and bracket system connection can be realized by clamp or embedded systems. Installation shall
follow the demonstration and suggestions below. If installation mode is different, please consult V-TAC and
obtain approval. Otherwise, modules may be damaged and quality warranty will become invalid.
Way of installation
Use the special clamp to install modules. See Figure 3.
A. Fix modules on the bracket by metal clamp. The following clamps or those clamps recognized by module
system installer are recommended.
Width: no less than 40mm;
Thickness: no less than 3mm;
Material: aluminum alloy;
Bolt: M6.
B. Torque range for bolt fastening: 18N•m to 24N•m
C. The clamp shall not contact glass or make module frame deformed in any case. The contactingsurface of
the clamp and frame front side shall be neat and smooth. Otherwise, frame and module may be damaged.
Make sure that the clamp will not produce shading effect. Drain holes can not be
sheltered by the clamp.
Use clamps to install modules
Tilt angle of modules: Included angle between module surface and horizontal surface; the module will obtain
the maximum power output in direct facing of sunlight.
Modules are preferred to be south-facing in the north hemisphere and north-facing in the south hemisphere.
A specific installation angle shall be determined according to installation guide for standard modules or sugges-
tions from PV module installer.
V-TAC suggests that module installation tilt angle be no less than 10° so module surface dust can be washed
away easily by rainfall and times of cleaning can be reduced. And it is easy for ponding to flow away and avoid
water print on the glass due to long time of water ponding which may further affect module appearance and
performance.
Selection of tilt angles
PV products will produce DC in the sunlight, so there may be electric shock or burning when touching module
connecting line metals. 30V DC voltage or higher voltage can be fatal.
In case of no connected load or external circuits, modules can also produce voltage. Please use insulation tools
and wear rubber gloves when operating modules in the sunlight.
PV modules doe not have switch. PV modules can only stop work when they are kept from sunlight or covered
by cloth, hard board or light-proof materials or when front side of modules are placed on smooth and flat
surfaces.
To avoid electric arc or electric shock hazards, please do not break down electric connection in loaded condi-
tions. Wrong connections will also lead to electric arc or shock. Keep connectors dry and clean and make sure
that they are in good working condition. Do not insert other metals into the connectors or carry out electric
connection by whatever means.
Snow and water in surrounding environments will intensify light reflection and lead to increase of current and
output power. And module voltage and power will increase under low temperature.
If module glass or packaging materials are damaged, please wear personal protective articles and isolate
modules from the circuit.
Working is only allowed in dry conditions by means of dry tools. Do not operate when modules are wet unless
you wear the proper electric shock protection device. Please operate following the cleaning requirements in
this manual when cleaning modules.
Electric performance safety
Do not open V-TAC Package in transportation and storage process unless the modules arrive at the installation
site.
Do not damage the package and do not make packaged modules on pallet fall directly.
Do not exceed the highest layer limit indicated on the packaging carton when piling modules up.
Put packaging carton in the ventilated, rain-proof and dry places before unpacking of modules.
Open V-TAC’s packaging carton following unpacking instructions.
Do not hold the connecting box or wires to lift the entire module in any cases.
Do not stand or walk on modules.
Do not pile one module onto another.
To avoid glass damage, do not put heavy objects on module glass.
Be careful when placing modules on a surface and at corners in particular.
Do not try to unpack the module or remove nameplate or parts of modules.
Do not paint surface of modules or apply any other glues.
Do not damage, grad or scratch back film of modules.
Do not drill frame of modules, which may reduce frame loading capacity or lead to frame corrosion.
Do not scratch anodic coating of aluminum alloy frame except for grounding connection.
Scratch may lead to frame corrosion and reduce frame loading capacity.
Do not repair glass or modules whose back film is damaged on your own.
Operation safety
Mechanical and electrical installation of PV modules shall follow proper regulations such as electric law, build-
ing law and electric connecting requirements. These regulations differ with different installation sites, such as
building roofing installation, vehicle-mounted application. Requirements may also differ with installation
system voltage, DC or AC. See specific clauses in local authorities.
Laws and regulations
Each module is pasted with 3 labels providing information below:
1. Nameplate: It describes product type, standard rated power, rated current, rated voltage, open circuit
voltage, short circuit current under testing conditions, certification indicator, maximum system voltage, etc.
2. Current level label: Divide modules as per their optimal working current and there are values: H, M or L (H
means the highest current level). The best practice is to install modules with the same current level (such as
H) in one strand in the process of installation.
3. Serial No.: Each module has a unique serial number which is solidified inside the module permanently and it
can be seen from front top of the module. Each serial number is put in before laminating of the module.
Module identification
WARNING!
1. Please make sure to turn off the power before starting the installation.
2. Installation must be performed by a qualified electrician.
3. The light source of this luminaire is not replaceable, when the light source reaches its end of life the whole
luminaire should be replaced.
4. If the external flexible cable or cord of this luminaire is damaged, it shall be exclusively replaced by the
manufacturer or his service agent or a similar qualified person in order to avoid a hazard.
5. Proper grounding should be ensured throughout the installation.
Caution, risk of
electric shock.
This marking indicates that this
product should not be disposed
of with other household wastes.
IP68
RATING
1. Aluminum alloy frame
2. PV tempered glass
3. Packaging EVA
4. Cells
5. Back plate
6. Silica gel
7. Connecting box
8. Nameplate
9. Cables
10. Connector
11. Mounting hole
12. Grounding hole
13. Leakage hole
14. Cell
Figure 1 Module Section Structure and Components
Clamp B
At least 2
Clamp A
At least 2
Bracket
PV module
Mounting rack
Clamp B
Clamp A
Clamp A for tail end module edge Clamp B for middle modules
Figure 3 Clamp Illustration (unit: mm)
Figure 5: Series connection and parallel
connection circuit diagram
Serial connection
Serial connection
Parallel connection
after series connection
DIODE CONNECTOROVERCURRENT PROTECTOR
Testing standards Wire diameter Temperature range Voltage
IEC62930 4mm² -40ºC to +85ºC 1500V
Figure 6 Grounding Clamp Installation
Note: TYCO. 1954381-1 (recommended) is used in figures above
The third party grounding device can be used for grounding of V-TAC modules but such grounding shall be
proved to be reliable. Grounding device shall be operated in line with stipulations of the manufacturer.
Carry out regular inspection and maintenance for modules and this is the user’ responsibility
within the quality warranty period in particular; and, inform the supplier within two weeks when
modules are found to be damaged.
Cleaning
Accumulated dust on module surface glass will reduce the power output and lead to local heat
spot, such as industrial waste water and birds droppings. The degree of influence is determined by
transparency of wastes. Small amounts of dust will affect sunlight strength and evenness but are not
dangerous and power will not be reduced remarkably in general.
During operation of modules, there shall be no environmental factors projecting shades or shelter
partial or the entire module, including other modules, module system bracket, birds, dust, soil or
plants. These will reduce output power. V-TAC suggests that the module surface should not be
sheltered in any case.
Frequency of cleaning depends on dirt accumulation speed. In normal situations, rainwater will
clean the module surface and the cleaning frequency is reduced therefore. It is suggested to use
damp clean water sponge or soft cloth to wipe the glass surface. Do not use acid and alkaline
detergents to clean modules.
Module appearance inspection
Check module appearance defects visually, especially:
1. Module glass cracks.
2. Corrosion at welding parts of the cell main grid: it is caused by moisture into the module due to damage
of surface packaging materials during installation or transportation.
3. Check whether there is burning traces on the module back plate.
Inspection of connectors and cables
It is suggested to carry out a preventive inspection once every 6 month:
1. Check connector sealing and cable connection solidness.
2. Check whether sealant of the terminal box is cracking with gap.
IN CASE OF ANY QUERY/ISSUE WITH THE PRODUCT, PLEASE REACH OUT TO US AT: SUPPORT@V-TAC.EU
FOR MORE PRODUCTS RANGE, INQUIRY PLEASE CONTACT OUR DISTRIBUTOR OR NEAREST DEALERS.
V-TAC EUROPE LTD. BULGARIA, PLOVDIV 4000, BUL.L.KARAVELOW 9B
20
PAP
Model VT-450 VT-545
Rated Maximum Power (Pmax) 450W 545W
Tolerance (Tol) 0-+3% 0-+3%
Voltage at Pmax (Vmp) 41.50V 41.93V
Current at Pmax (Imp) 10.85A 13A
Open-Circuit Voltage (Voc) 49.30V±3% 49.90±3%
Short-Circuit Current (Isc) 11.60A±3% 13.92±3%
Nominal Operating Cell
Temperature (NOCT):
45±2°C 45±2°C
Maximum System Voltage 1500VDC 1500VDC
Maximum Series Fuse Rating 20A 25A
Operating Temperature -40°Cto+85°C -40°Cto+85°C
Output Cables
Application Class Class A
Cell Technology/Number of Cells Half Mono/144 cells
Body Type
Aluminium Alloy & Tempered Glass
4mm² cable 55cm (Including MC4 connector)
2094x1038x35mmDimension
10
YEAR
W A R R A N T Y
MULTI-LANGUAGE
MANUAL QR CODE
Please scan the QR code
to access the manual in
multiple languages.
2279x1134x35mm
Specyfikacje produktu
Marka: | V-TAC |
Kategoria: | panel słoneczny |
Model: | VT-AU450-36V |
Potrzebujesz pomocy?
Jeśli potrzebujesz pomocy z V-TAC VT-AU450-36V, zadaj pytanie poniżej, a inni użytkownicy Ci odpowiedzą
Instrukcje panel słoneczny V-TAC

8 Października 2024

8 Października 2024
Instrukcje panel słoneczny
- panel słoneczny LG
- panel słoneczny Sharp
- panel słoneczny Dometic
- panel słoneczny Enphase
- panel słoneczny Reolink
- panel słoneczny Tesla
- panel słoneczny Imou
- panel słoneczny KKT Kolbe
- panel słoneczny Jackery
- panel słoneczny Kenwood
- panel słoneczny Sungrow
- panel słoneczny Deye
- panel słoneczny Mestic
- panel słoneczny BLUEPALM
- panel słoneczny Furrion
- panel słoneczny Biltema
- panel słoneczny Viessmann
- panel słoneczny Perel
- panel słoneczny Growatt
- panel słoneczny Velleman
- panel słoneczny Victron Energy
- panel słoneczny Anker
- panel słoneczny SereneLife
- panel słoneczny CyberPower
- panel słoneczny EcoFlow
- panel słoneczny BenQ
- panel słoneczny Technaxx
- panel słoneczny Vivanco
- panel słoneczny EasyMaxx
- panel słoneczny Xtorm
- panel słoneczny Gre
- panel słoneczny Salicru
- panel słoneczny Aukey
- panel słoneczny Energenie
- panel słoneczny Steren
- panel słoneczny Arlo
- panel słoneczny Fantini Cosmi
- panel słoneczny Projecta
- panel słoneczny Cedel
- panel słoneczny Paulmann
- panel słoneczny SolarEdge
- panel słoneczny ECTIVE
- panel słoneczny Tru Components
- panel słoneczny FOX ESS
- panel słoneczny Goal Zero
- panel słoneczny BlauHoff
- panel słoneczny Sunset
- panel słoneczny Tycon Systems
- panel słoneczny Renogy
- panel słoneczny Fimer
- panel słoneczny Sunrise
- panel słoneczny Sunware
- panel słoneczny APSystems
- panel słoneczny Longi
- panel słoneczny Yingli Solar
- panel słoneczny SunPower
Najnowsze instrukcje dla panel słoneczny

28 Marca 2025

27 Marca 2025

11 Marca 2025
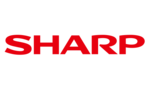
5 Stycznia 2025
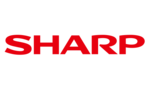
5 Stycznia 2025
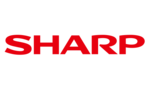
5 Stycznia 2025
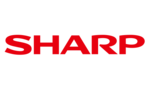
5 Stycznia 2025
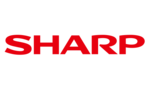
5 Stycznia 2025
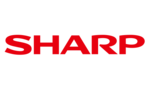
5 Stycznia 2025
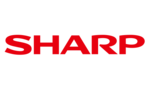
5 Stycznia 2025