Instrukcja obsługi Indian Springfield (2016)
Przeczytaj poniżej 📖 instrukcję obsługi w języku polskim dla Indian Springfield (2016) (199 stron) w kategorii Silnik. Ta instrukcja była pomocna dla 6 osób i została oceniona przez 2 użytkowników na średnio 4.5 gwiazdek
Strona 1/199
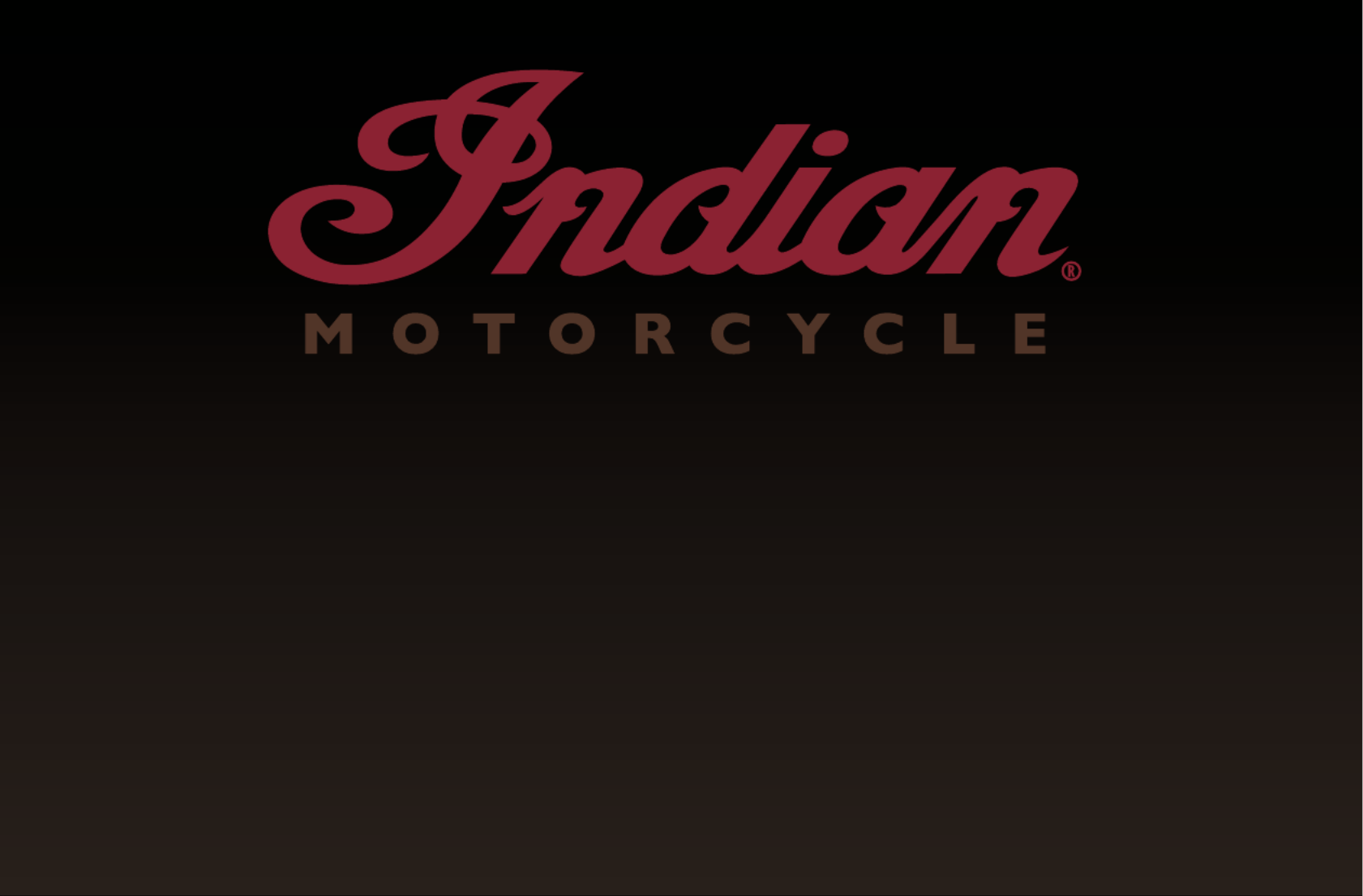
2016 RIDER’S MANUAL
Chief Dark Hse ®
Chief ®Claic
Chief ®
Vintage
Indi Springfield ™
Chieftain ®Dark Hse ™
Chieftain ®
Roadmaster ®
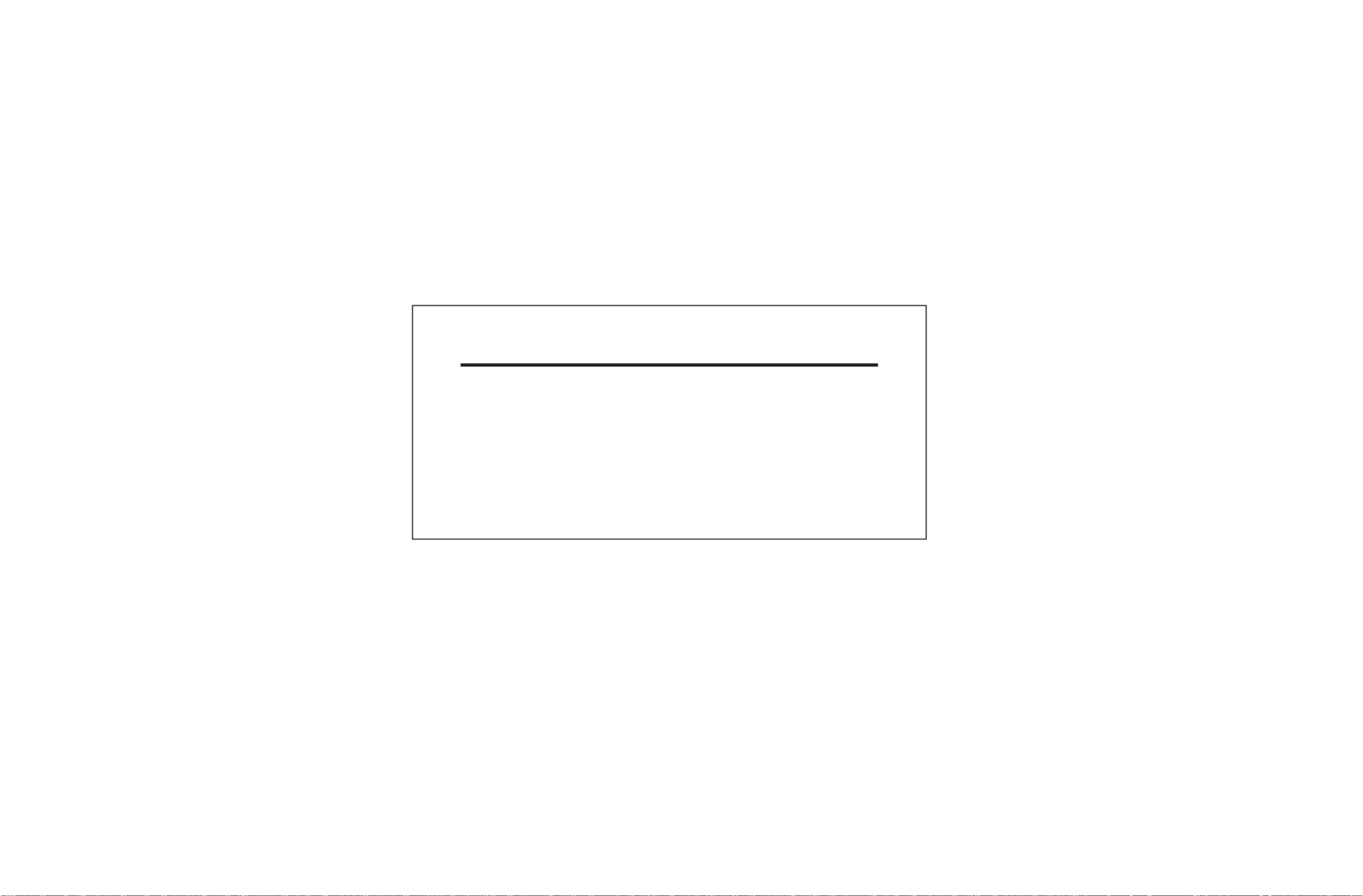
California Proposition 65 Warning
This product contains or emits
chemicals known to the state of
California to cause cancer and birth
defects or other reproductive harm.
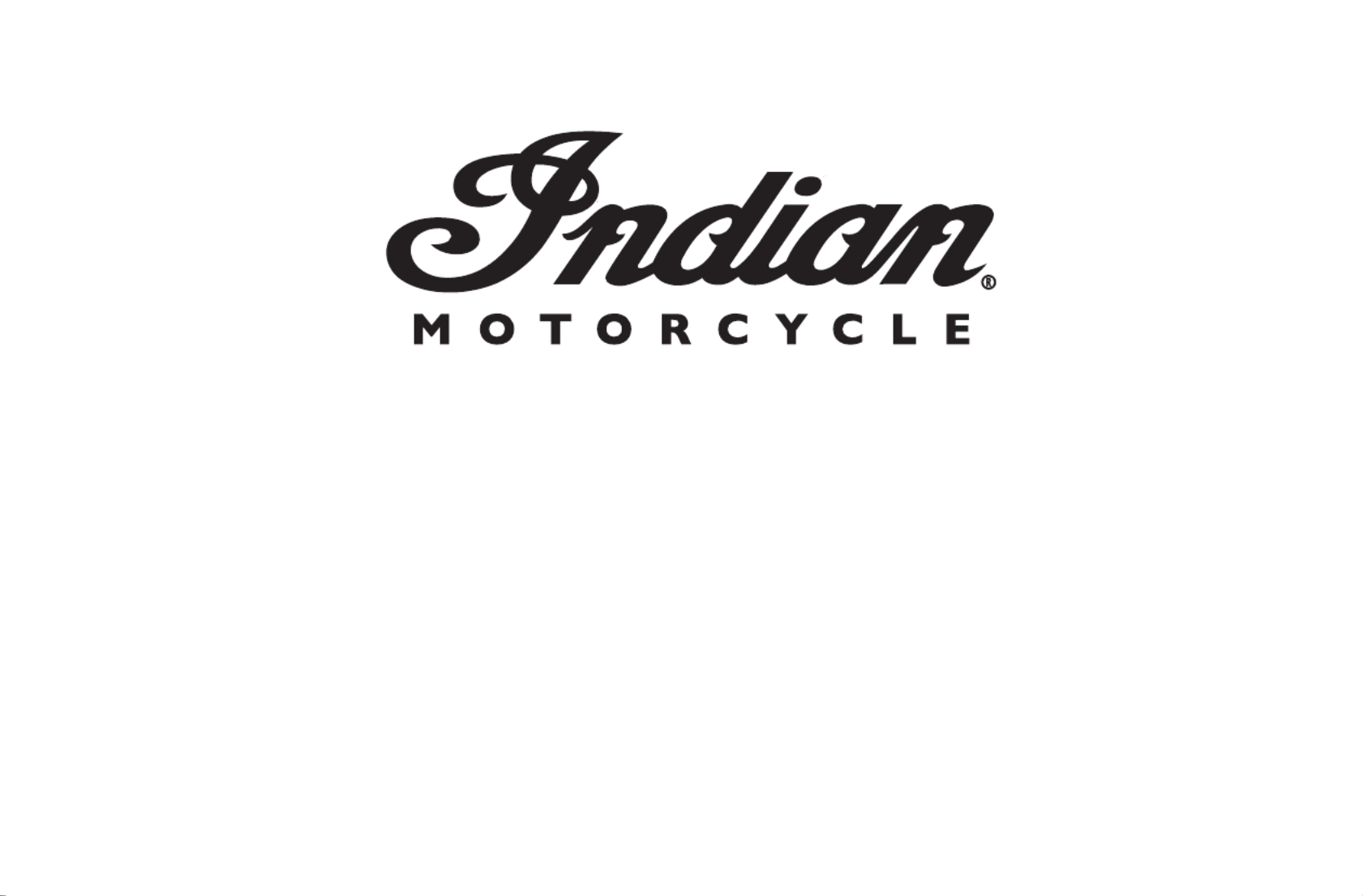
1
2016 Rider’s Manual
Chief Dark Horse ®
Chief ® Classic
Chief ® Vintage
Springfield™
Chieftain ® Dark Horse™
Chieftain ®
Roadmaster ®
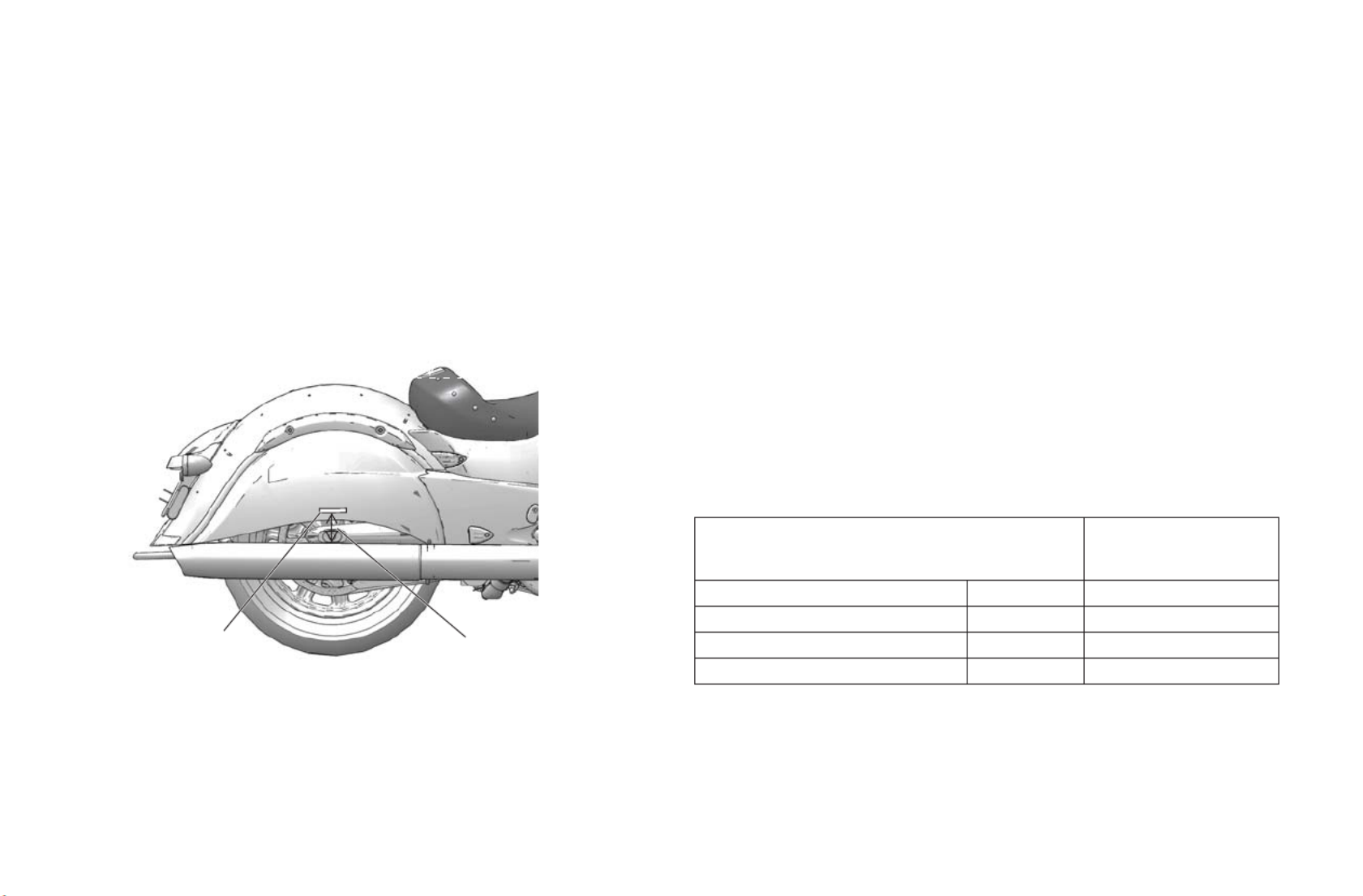
98
Maintenance
Rear Shock Preload (Ride Height) Inspection
Periodically inspect rear shock preload. For the most
comfortable ride and proper ground clearance, adjust
preload if ride height is out of specification.
1. Verify that tire pressure is at specification. See page 114.
2. Secure the motorcycle in an upright position by
clamping the front wheel in a wheel vise.
3. Remove the saddlebag (if equipped).
4. Apply a strip of tape to the rear fender directly over the
center of the rear axle.
5. Using a suitable lift, raise the motorcycle until the rear
shock is completely extended.
6. Measure the distance (in millimeters) from the center of
the rear axle to the bottom of the tape. Record the results
as measurement M1.
7. Lower the motorcycle and remove the lift.
8. Load the motorcycle with all intended cargo. Wearing
your riding gear, bring the motorcycle to the upright
position and sit on the operator's seat. If you plan to
carry a passenger, have the passenger (with riding
gear) sit on the passenger seat.
9. Have an assistant measure in the same location. Record
the results as measurement M2.
10. Subtract measurement M2 from M1. The result is the
measured rider sag. (M1-M2=Sag). Adjust preload as
needed.
Measure Here
Tape
CHIEF DARK HORSE shown
Recommended Suspension Sag Adjustment
Procedure
CHIEF Models 35mm See page 99
SPRINGFIELD 45mm See page 100
CHIEFTAIN Models 45mm See page 100
ROADMASTER 45mm See page 100
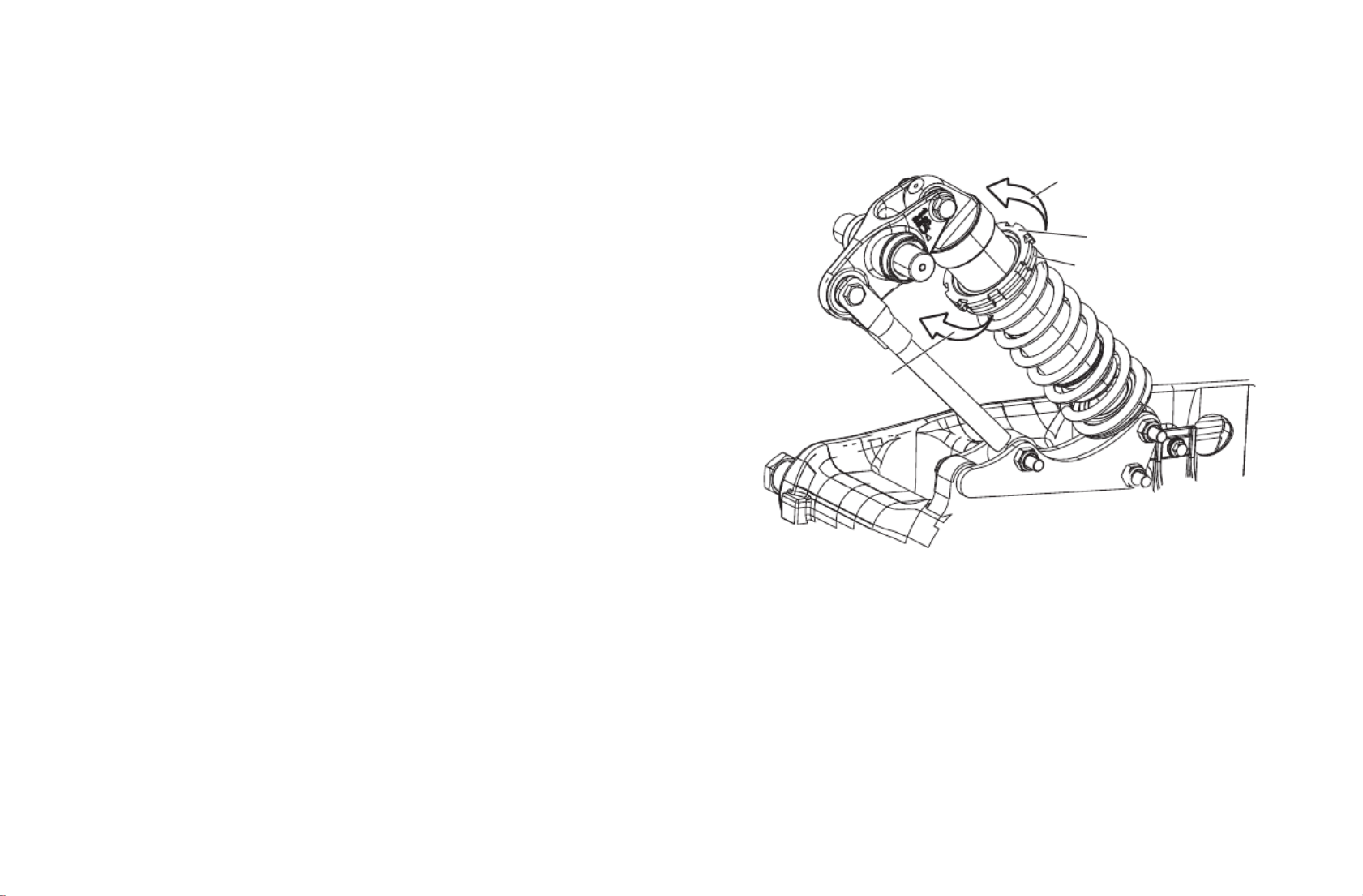
99
Maintenance
Rear Shock Preload (Ride Height) Adjustment
Applies to: CHIEF DARK HORSE/CHIEF Classic/CHIEF Vintage
1. Park the motorcycle with the sidestand down on a firm, level
surface. Remove all riders and cargo.
2. Remove the seat. See page 117.
Tip: Using the INDIAN MOTORCYCLE spanner wrench PV-46993 will make
rear suspension adjustment significantly easier.
3. The upper spanner nut on the shock is the lock nut. The lower
spanner nut is the adjuster nut. Loosen the lock nut by turning
it counter-clockwise (as viewed from the top of shock) with the
spanner wrench.
4. Spray a light lubricant on the adjuster nut where it contacts the
spring.
5. Adjust shock preload by rotating the adjuster clockwise (as
viewed from the top of shock) to INCREASE preload (firm) or
counter-clockwise to DECREASE preload (softer).
6. Recheck the preload measurement after adjusting.
7. Tighten the lock nut securely against the adjuster nut.
8. Reinstall the seat.
Increase
Preload
(more firm)
Decrease Preload (softer)
Adjuster Nut (lower)
Lock Nut (upper)
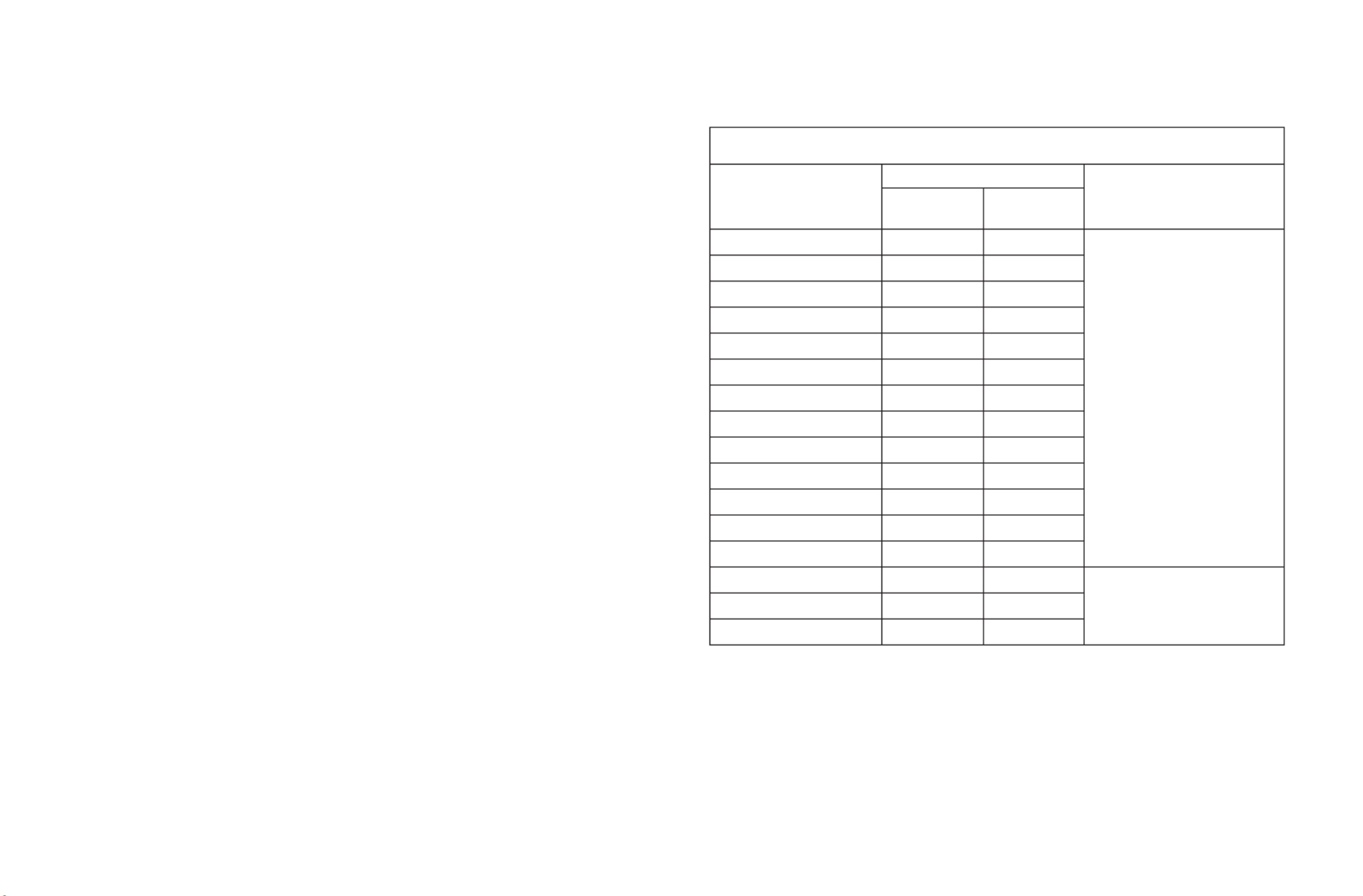
100
Maintenance
Shock Air Pressure (Ride Height) Adjustment
Applies to: SPRINGFIELD/CHIEFTAIN Models/
ROADMASTER
For riding comfort and to ensure proper ground clearance,
adjust rear shock air pressure. Refer to the label located on
the inside of the left side cover. The label shows
recommended pressures based on potential load weights.
Always inspect and adjust shock preload (ride height)
based on your actual load weight, in addition to adjusting
shock air pressure. See page 98.
Follow these guidelines when adjusting:
• Park the motorcycle with the sidestand down on a firm,
level surface. Remove all riders and cargo.
• DO NOT exceed 150 PSI (1034 kPa) in the shock.
• Use the INDIAN MOTORCYCLE Air Pump and Gauge (P/N
7043487). Follow the instructions on the following pages.
If the recommended air pump is not available, use a gauge
and a pressurized air source with a maximum line and
gauge pressure of 150 PSI (1034 kPa). After using the
alternate gauge, remove it quickly to minimize leakage.
Expect to lose up to 5 PSI (34 kPa) with each pressure check.
Use only a dry air source, such as a system with a water
separator or air line dryer, to prevent moisture from
entering the shock.
CAUTION! Air pressure increases VERY quickly when using
pressurized air. Wear eye and face protection.
Air Suspension Adjustment
Total Cargo &
Occupant Weight
(lbs)
Air Pressure (psi) MAX PRESSURE:
150 PSI
No
Trunk
With
Trunk
0 0 0
SELECT PRESSURE
CORRESPONDING
TO TOTAL CARGO
AND OCCUPANT
WEIGHT. REMOVE
ALL PASSENGERS
AND CARGO
BEFORE SETTING/
CHECKING SHOCK
PRESSURE. SET
PRESSURE WITH
BIKE ON SIDE
STAND.
150 0 0
175 0 10
200 0 23
225 10 30
250 23 38
275 30 48
300 38 60
325 48 71
350 60 85
375 71 100
400 85 122
425 100 134
450 122 145
475 134 N/A
500 145 N/A
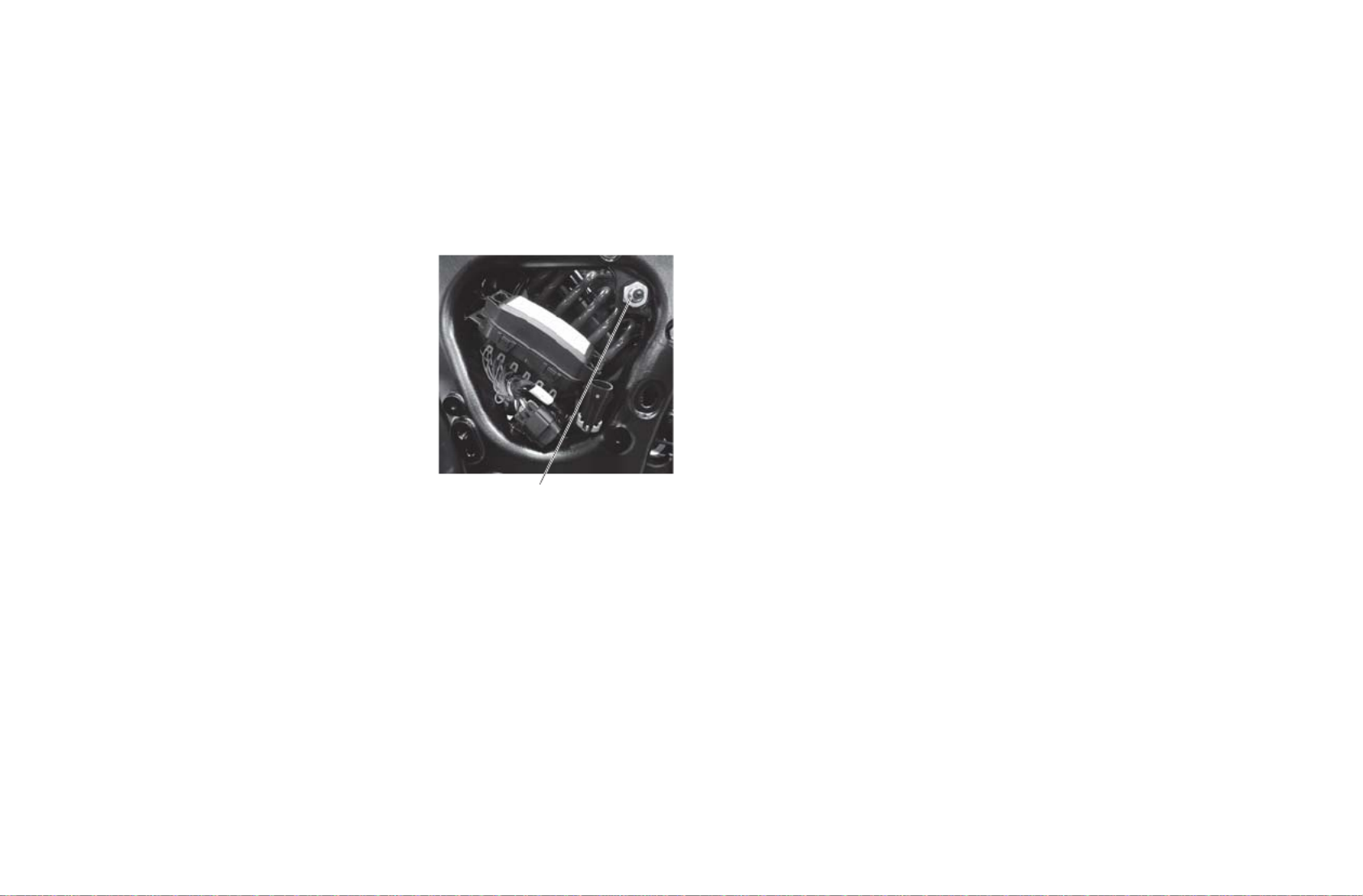
101
Maintenance
Shock Air Pressure (Ride Height)
Adjustment
Applies to: SPRINGFIELD/CHIEFTAIN Models/
ROADMASTER
1. Park the motorcycle with the sidestand down on a firm,
level surface. Remove all riders and cargo.
2. Remove the left side cover.
Remove the cap from the air
fitting.
3. Determine the recommended
rear shock air pressure. Refer
to the label located on the
inside of the left side cover.
4. Install the hose fitting of the
recommended gauge securely
onto the air fitting. Read the air
pressure on the gauge.
5. To reduce air pressure, push
the bleed button on the gauge. Bleed pressure in small
amounts until the desired pressure is attained.
6. To increase pressure, pump the handle until pressure
increases to the desired amount.
CAUTION! DO NOT exceed 150 PSI (1034 kPa) in the shock.
7. Remove the hose from the air fitting and reinstall the
cap.
Tip: Expect to lose up to 5 PSI (34 kPa) with each pressure check.
8. Repeat the preload inspection to verify proper preload.
See page 98.
Swing Arm/Rear Axle Inspection
1. Sit in the operator's seat and slowly bounce the rear
suspension a few times. Make sure the suspension
moves freely without binding. Listen for abnormal
noises.
2. Elevate and support the motorcycle with the rear tire
slightly off the floor. See page 128.
CAUTION! Make sure the motorcycle is stable when elevated.
Injury may occur if the motorcycle tips or falls.
3. Grasp the rear wheel and attempt to move the wheel
side-to-side. If there is movement at the front of the
swingarm or in the axle area, see your dealer for
service.
4. With the transmission in neutral, slowly rotate the rear
wheel. If the wheel does not rotate smoothly, see your
dealer for service.
Air Fitting
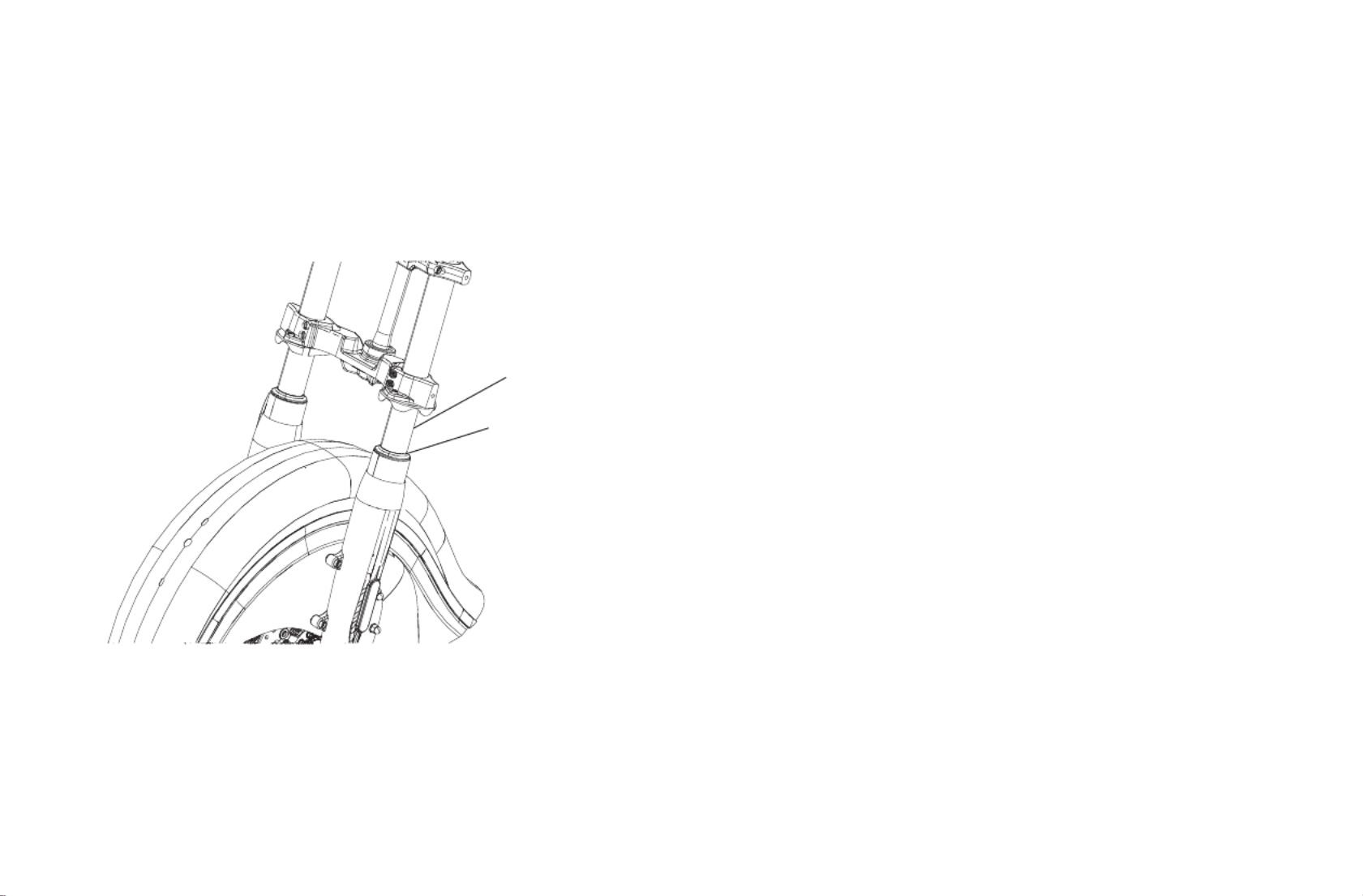
102
Maintenance
Front Fork/Suspension Inspection
1. Place the motorcycle on the sidestand and inspect the
front forks. If fork oil is present on the outer tube, do not
ride the motorcycle. See your dealer for service before
operating. If fork oil is present around the fork seals or
inner tubes, replace the fork seals.
2. Clean the fork tubes to remove bugs, tar or buildup
which may cause seal wear or leakage. Inspect the outer
surfaces of the inner fork tubes for scratches or damage
from foreign objects.
3. Straddle the motorcycle and bring it to the fully upright
position. Apply the front brake and push downward
(hard) on the handlebars several times. The front
suspension should operate smoothly and quietly.
4. Fork oil condition and level affects front suspension
performance and internal component wear. Replace
fork oil at the recommended intervals. Special tools are
required to perform this procedure. See the INDIAN
MOTORCYCLE Service Manual or an authorized INDIAN
MOTORCYCLE dealer.
Fork Inner
Tube
Fork Seal
General Representation
Fork Seal
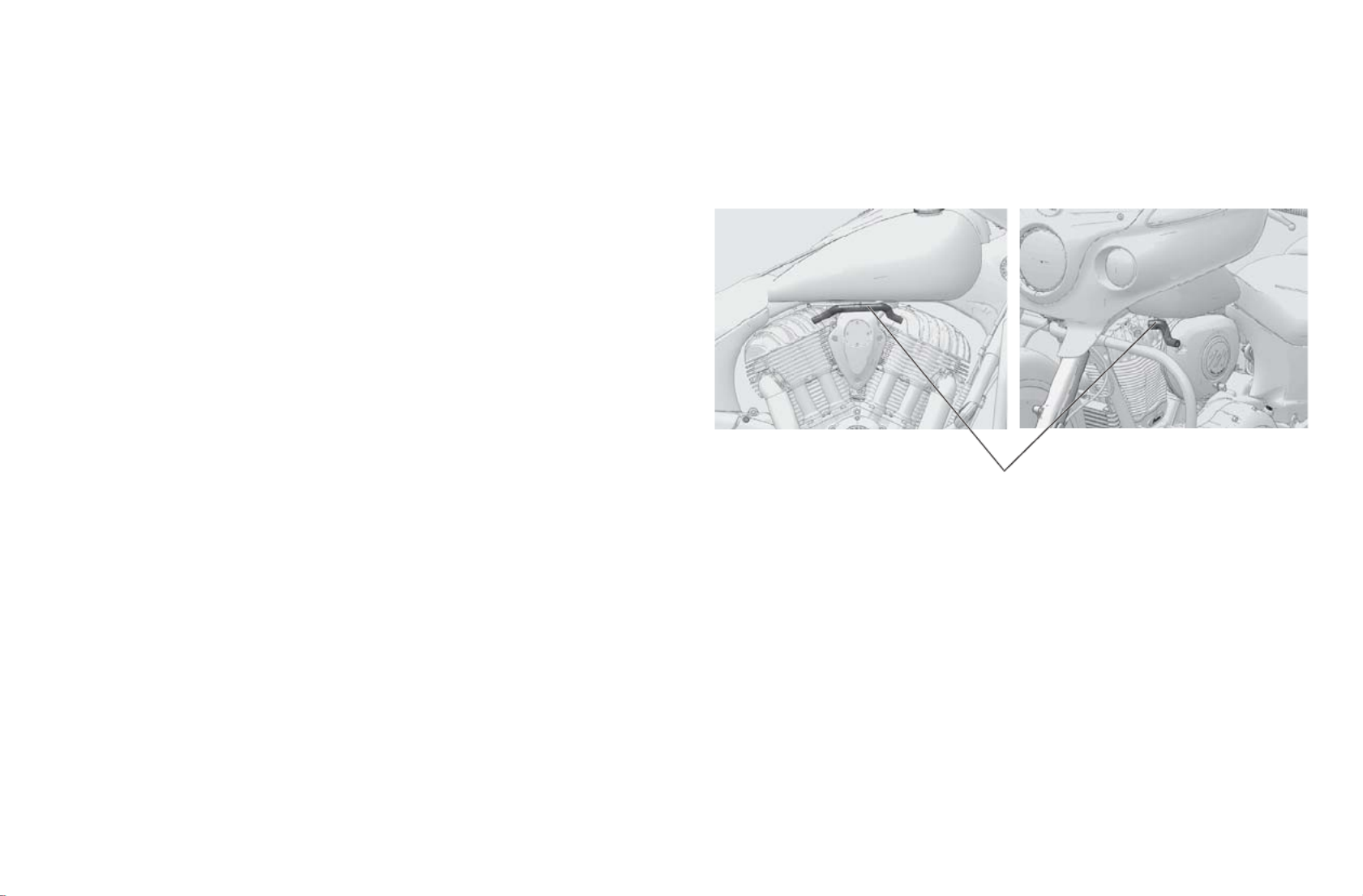
103
Maintenance
Steering Head Inspection
1. Elevate and support the motorcycle with the front tire
slightly off the floor. See page 128.
CAUTION! Make sure the motorcycle is stable when elevated.
Injury may occur if the motorcycle tips or falls.
2. Turn the handlebars from stop to stop. The action should
be smooth but not loose. Make sure wires, hoses and
control cables do not interfere with smooth steering.
3. Position the front wheel straight ahead. Grasp the front
forks near the front axle and attempt to move the wheel
front-to-back. If there is front-to-back movement at the
steering head, see your dealer for service.
4. If steering binds, feels rough or uneven, or if movement
is detected at the steering stem, see your dealer for
service.
5. Rotate the front wheel and inspect for smooth rotation of
front wheel bearings. If roughness or unusual sounds
are present, see your dealer for service.
6. Turn handle bars full right or left and hold against the
fork stop. Attempt to move front wheel side-to-side. If
movement is observed, see your dealer for service.
Crankcase Breather Hoses
Inspect both breather hoses along their length and at both
ends. Make sure hoses are not restricted, kinked, cracked or
otherwise damaged. Replace any worn or damaged hoses.
Breather Hoses
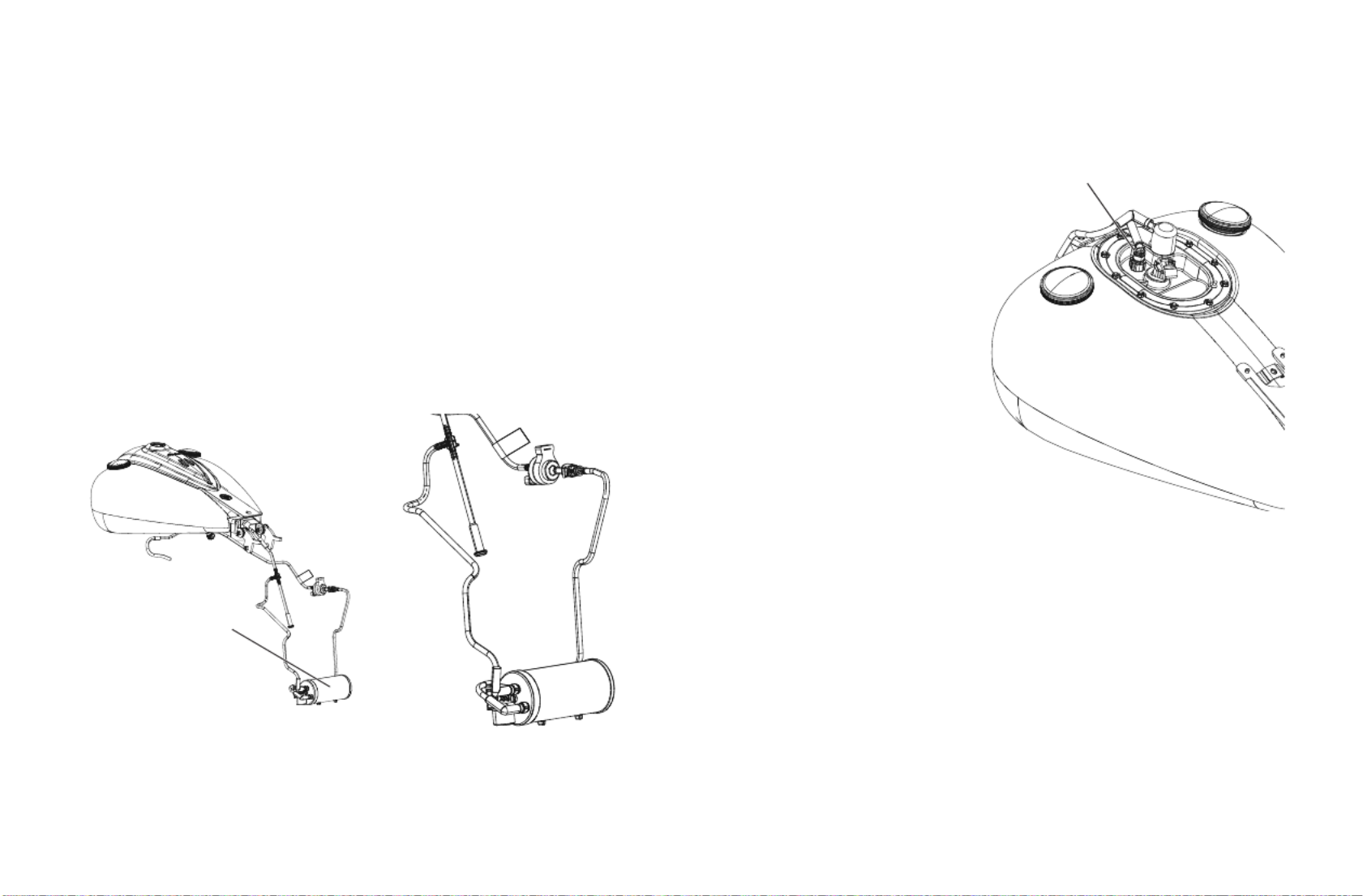
104
Maintenance
Evaporative Emission Control System
(California Models)
1. Inspect all evaporative emission control system hoses
and connections. Make sure all connections are tight
and locked.
2. The canister is located under the rear fender. Make sure
it is securely fastened to the mounting bracket.
3. Inspect connections at the evaporative emissions
canister to be sure they are secure. The vent line coming
from the tank should be connected to the black port. The
purge line should be connected to the gray or natural-
colored port.
Fuel System Components
1. Inspect fuel hoses for
cracks or damage.
2. Inspect hose
connections at the fuel
tank and at the fuel rail
for dampness or stains
from leaks. The tank
connection for the fuel
line is under the tank
console.
3. The fuel system is
under pressure and
caution must be used
when inspecting and
servicing the fuel
system. See the INDIAN
MOTORCYCLE Service
Manual or an authorized
INDIAN MOTORCYCLE dealer.
Evaporative
Emissions
Canister
(California
Models)
Fuel Line Quick
Disconnect
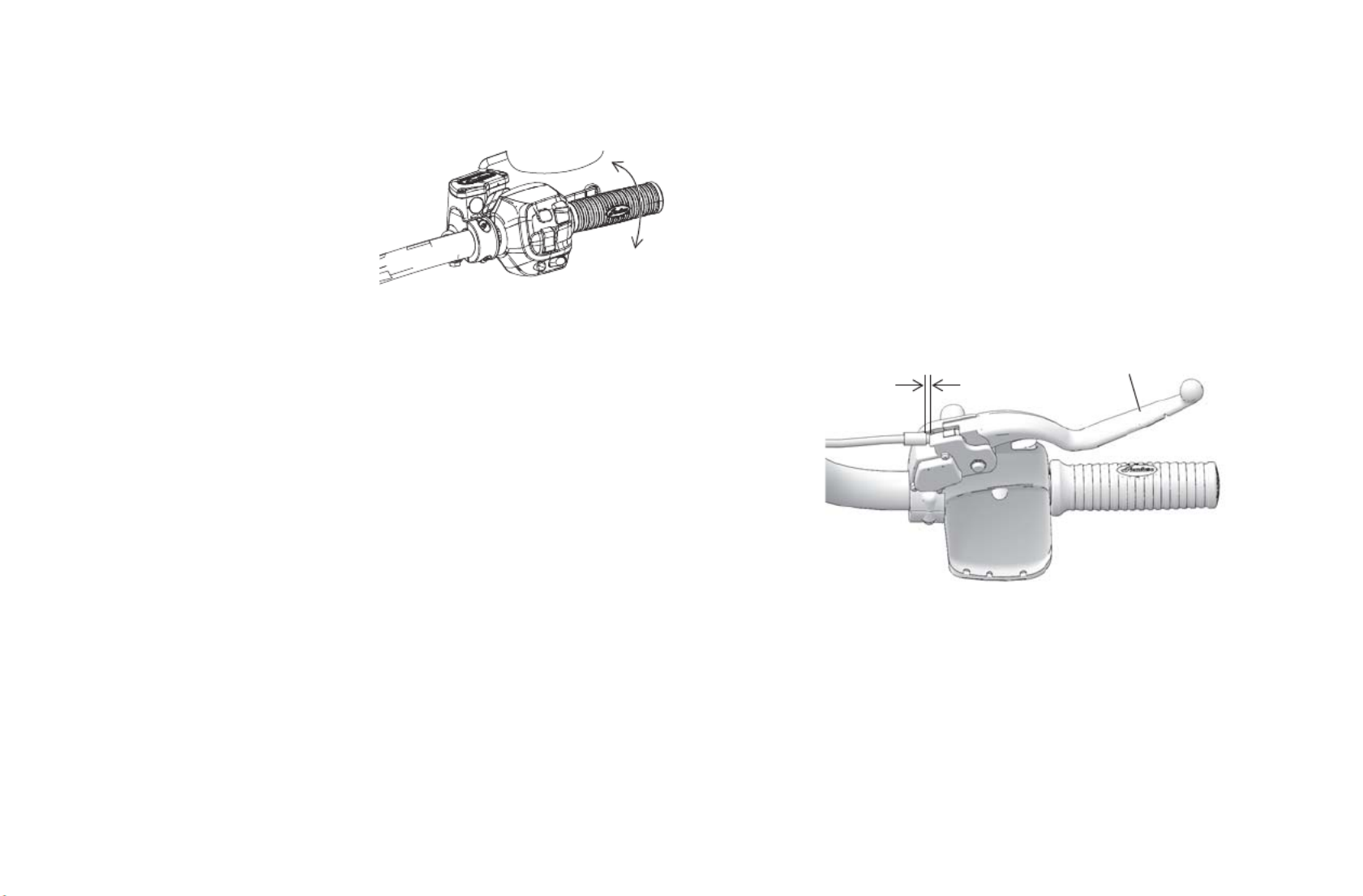
105
Maintenance
Throttle Control Inspection
1. With the engine OFF,
rotate the throttle control
grip fully open and then
release it. It should rotate
smoothly from the rest
position to the
completely open
position. It should return
to the rest position
quickly when released.
2. Repeat the twist and release process with the
handlebars turned fully right and fully left.
3. Service the throttle system if throttle operation is not
smooth or if throttle grip does not return properly. See
the INDIAN MOTORCYCLE Service Manual or an
authorized INDIAN MOTORCYCLE dealer.
Sidestand Lubrication
Periodically lubricate the sidestand bushing. See page 73
for sidestand inspections.
Mechanical Clutch Lever Freeplay
1. Position the handlebars in the straight-ahead position
before measuring clutch lever freeplay.
2. The clutch cable adjuster nut is located alongside the
left down-tube. Hold the clutch cable. Slide the rubber
protective cover away from the lock nut. Loosen the lock
nut.
3. Turn the cable adjuster inward or outward until clutch
lever freeplay is 0.5-1.5 mm.
4. While holding the cable, tighten the adjuster lock nut
securely.
5. Verify that the safety switch activates properly. The
engine should not start in gear with the clutch lever
released.
Tip: The starter interlock switch is dependent on the clutch lever
freeplay being set correctly to ensure activation of the clutch
safety switch.
Clutch Lever
0.5-1.5 mm
Freeplay
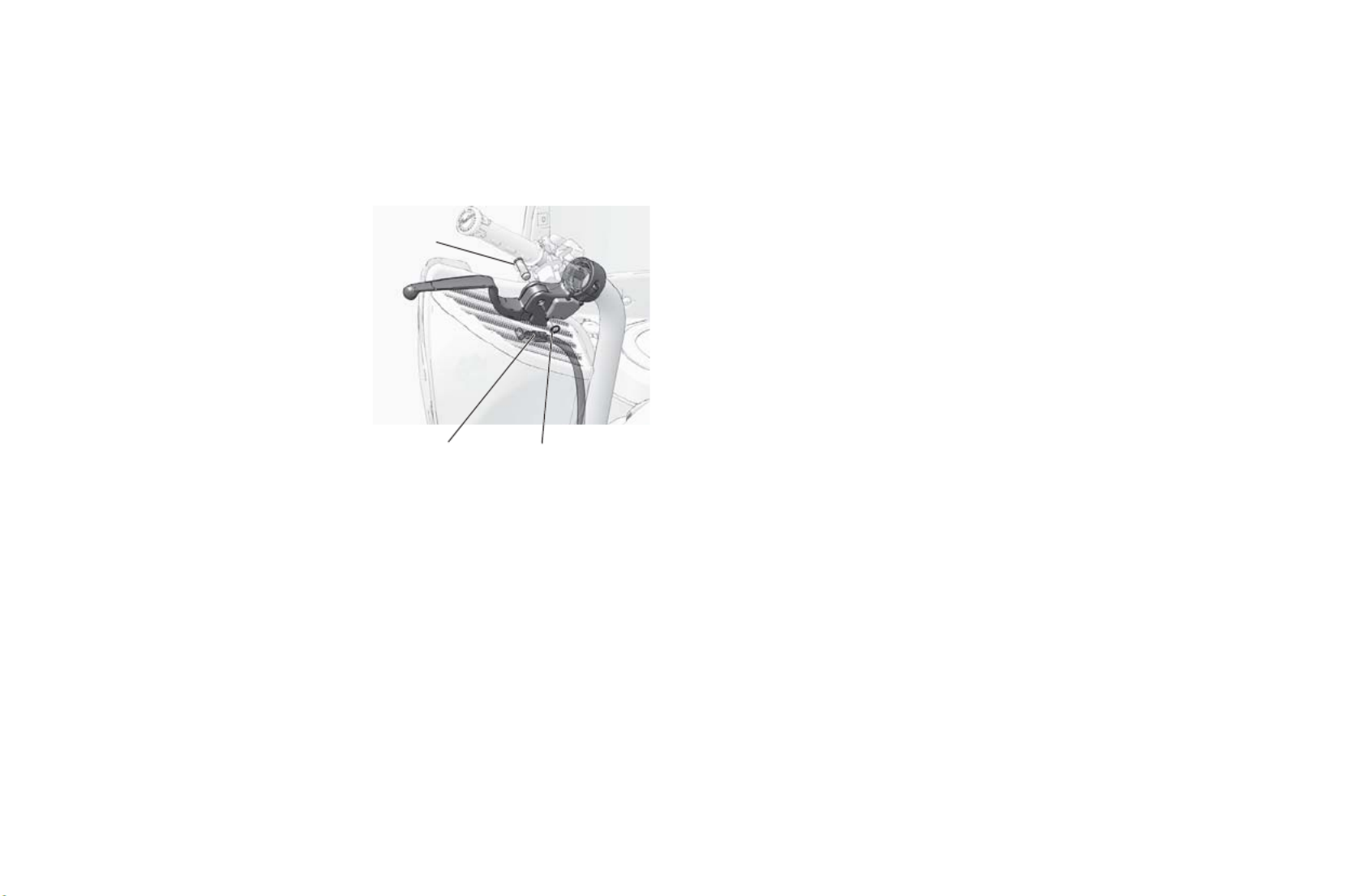
106
Maintenance
Mechanical Clutch Lever Lubrication
1. The clutch cable adjuster nut is located alongside the
left down-tube. Slide the rubber protective cover away
from the adjuster. Loosen the lock nu
t.
2. Turn the cable adjuster
completely inward to
provide maximum lever
freeplay.
3. Remove the clutch lever c-
clip and pin. Disconnect
the clutch cable from the
clutch lever.
4. Remove any old grease
and dirt from the lever and
housing. Lubricate the
clutch lever and pin with
moly assembly grease or
all-purpose grease.
NOTICE: During installation of the lever, be aware of the
internal clutch switch. Improper assembly can
cause damage to the switch.
5. Reconnect the clutch cable. Reinstall the lever C-clip
and pin.
6. Adjust clutch lever freeplay. See page 105.
7. Tighten the adjuster nut and slide the protective cover
over the adjuster.
Mechanical Clutch Cable Lubrication
Lubricate control cable ends at the intervals recommended
in the periodic maintenance table beginning on page 91.
NOTICE: External casings are factory-lubricated. Additional
lubrication could be detrimental to cable performance.
Verify proper routing and smooth movement. Inspect for
damage to the external casing, and inspect exposed cable
wire for fraying, kinks or corrosion. Replace any damaged,
sticky or sluggish cable.
1. Disconnect the cable at the clutch lever and at the
primary cover.
2. Lubricate the barrel ends with all-purpose grease.
3. Reconnect the cable and adjust freeplay as needed.
Clutch
Cable
C-Clip
Pin
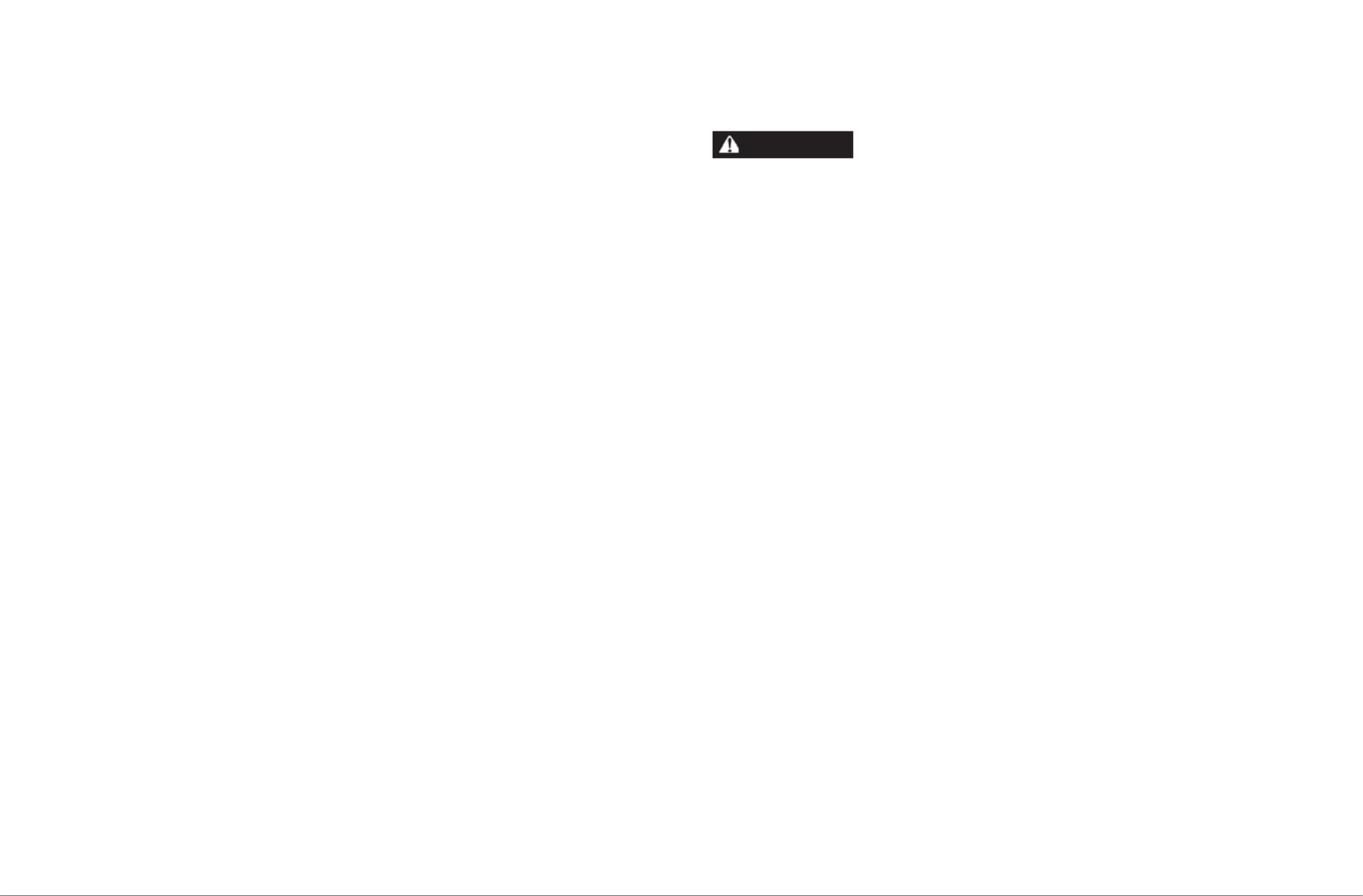
107
Maintenance
Rear Brake Pedal
1. Lubricate the pivot bushing at the intervals
recommended in the periodic maintenance table
beginning on page 91. Also lubricate any time binding
is evident. Use all-purpose grease.
2. Inspect brake pads as outlined on page 110.
Brake Hoses/Connections
Inspect all brake hoses and connections for dampness or
stains from leaking or dried fluid. Tighten any leaking
connections and replace components as necessary. See the
INDIAN MOTORCYCLE Service Manual or an authorized
INDIAN MOTORCYCLE dealer.
Brake Fluid Precautions
Using the wrong fluid or allowing air or contaminants into the fluid
system can damage the system seals or result in a malfunction that
could lead to serious injury or death. Use only DOT 4 brake fluid from
a sealed container.
Do not operate the front brake with the reservoir cover removed.
Fluid could overflow from the reservoir and allow air to enter the
system. Air in the brake system could cause the brakes to
malfunction.
An over-full reservoir may cause brake drag or brake lock-up, which
could result in serious injury or death. Maintain brake fluid at the
recommended level. Do not overfill.
NOTICE: Brake fluid will damage painted surfaces and plastic parts.
Always clean spilled brake fluid immediately with water
and a mild detergent.
WARNING
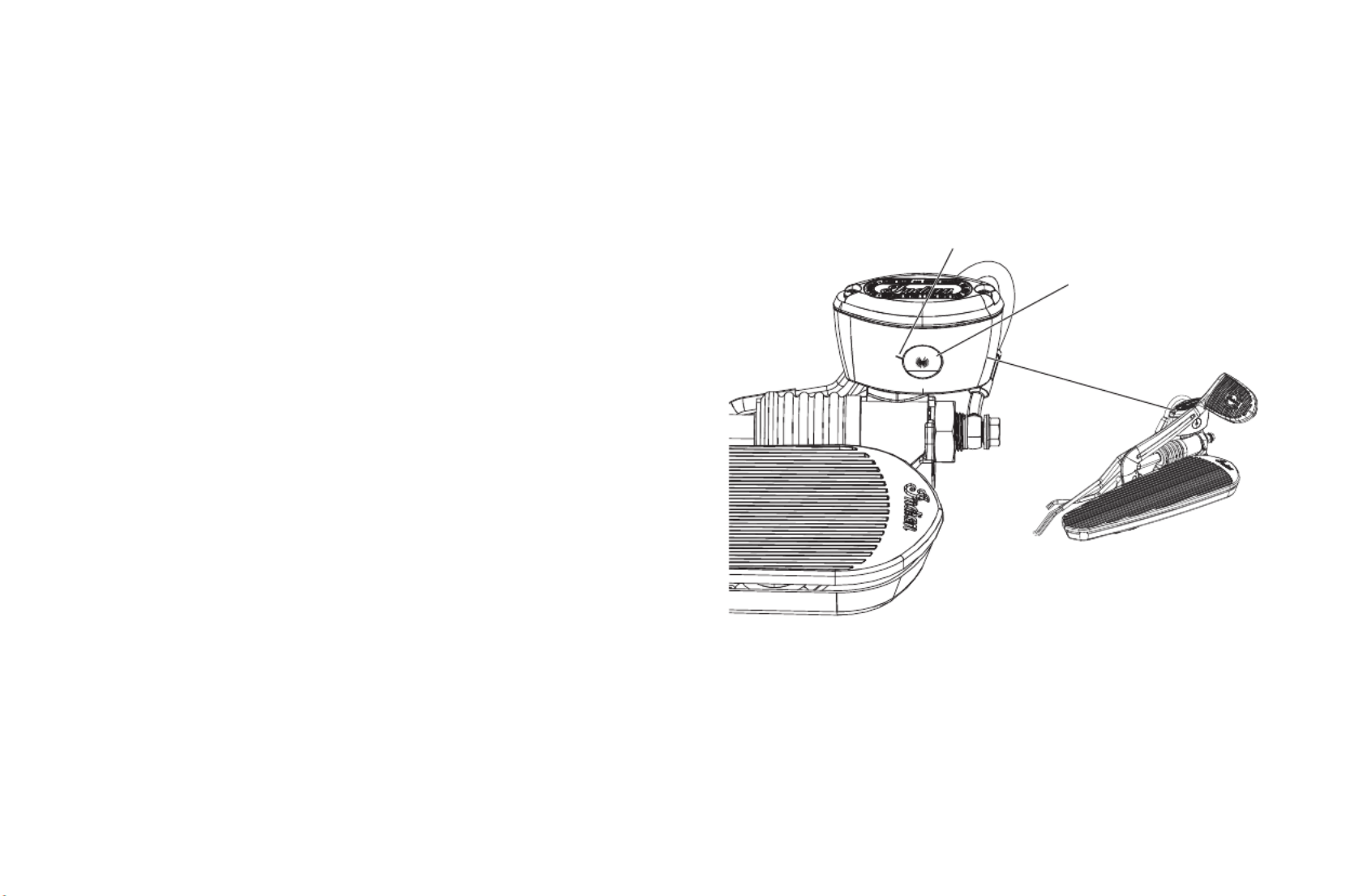
108
Maintenance
Rear Brake Fluid
Change the brake fluid at the intervals recommended in the
periodic maintenance table beginning on page 91. Always
add brake fluid from a new, unopened container. Always use
the recommended fluid. See page 149.
1. Position the motorcycle on level ground in the fully
upright position.
2. The rear brake fluid reservoir is located near the rear
brake pedal. View the reservoir from the right side of
the vehicle.
3. Wipe the fluid container and the area around the
reservoir cover with a clean cloth.
4. If the fluid level is low, inspect brake pads as outlined on
page 110. If pads are not worn beyond the service limit,
inspect the brake system for leaks.
5. Remove the cover and diaphragm. The fluid level should
be above the minimum indicator mark on the reservoir
body. Add brake fluid as needed. Do not overfill.
6. Reinstall the cover and diaphragm.
7. Wipe away any fluid spills. Check for signs of brake
fluid leaks around hoses, fittings, reservoir, and brake
calipers.
Minimum
Level Mark
Sight
Glass
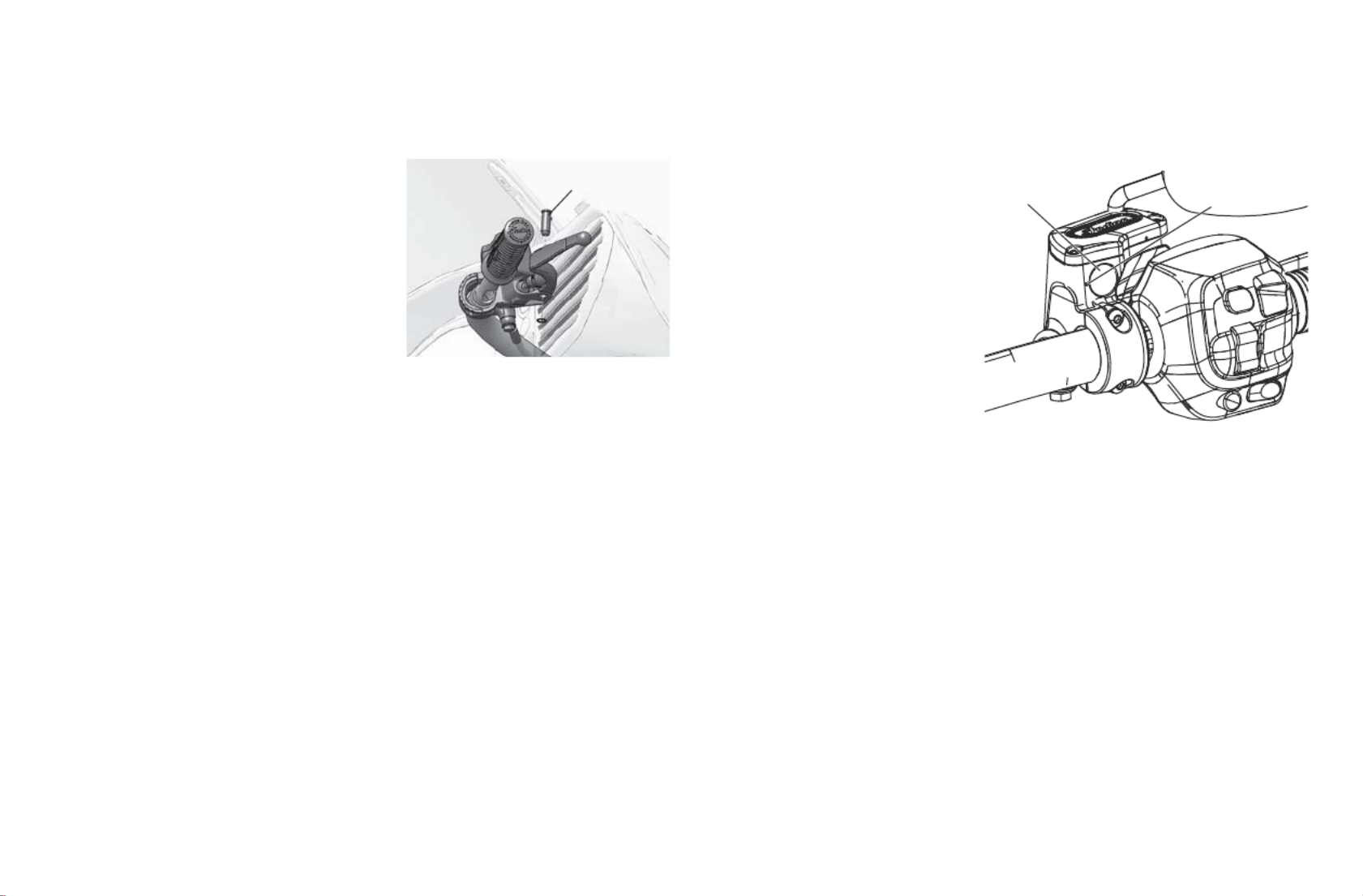
109
Maintenance
Front Brake Lever
1. See page 62 for front brake lever reach adjustments.
2. Lubricate the pivot pin
and brake lever hinge
points at the intervals
recommended in the
periodic maintenance
table beginning on page
91. Also lubricate any
time binding is evident.
Use all-purpose grease.
3. Inspect brake pads as
outlined on page 110.
Front Brake Fluid
Change the brake fluid at the intervals recommended in the
periodic maintenance table beginning on page 91. Do not
attempt to change the anti-lock brake system fluid. Please
see your dealer for this service. Always add brake fluid from
a new, unopened container. Always use the recommended
fluid. See page 149.
1. Position the motorcycle on level ground in the fully
upright position. Position the handlebars so that the fluid
reservoir is level. Wipe the fluid container and the area
around the reservoir cover with a clean cloth.
2. If the fluid level is low, inspect brake pads as outlined on
page 110. If pads are not worn beyond the service limit,
inspect the brake system for leaks.
3. To add fluid, remove
the reservoir cover
screws. Remove the
cover and diaphragm.
4. The fluid level should
be above the
minimum indicator
mark in the sight
glass. Add brake fluid
as needed. Do not
overfill.
5. Reinstall the
diaphragm, cover and
screws.
Torque: 13 in-lbs (1.4 Nm)
6. Wipe away any fluid spills. Check for signs of brake
fluid leaks around hoses, fittings, reservoir and brake
calipers. Check for deterioration of hoses.
Pivot Pin
Sight
Glass
Minimum
Level Mark
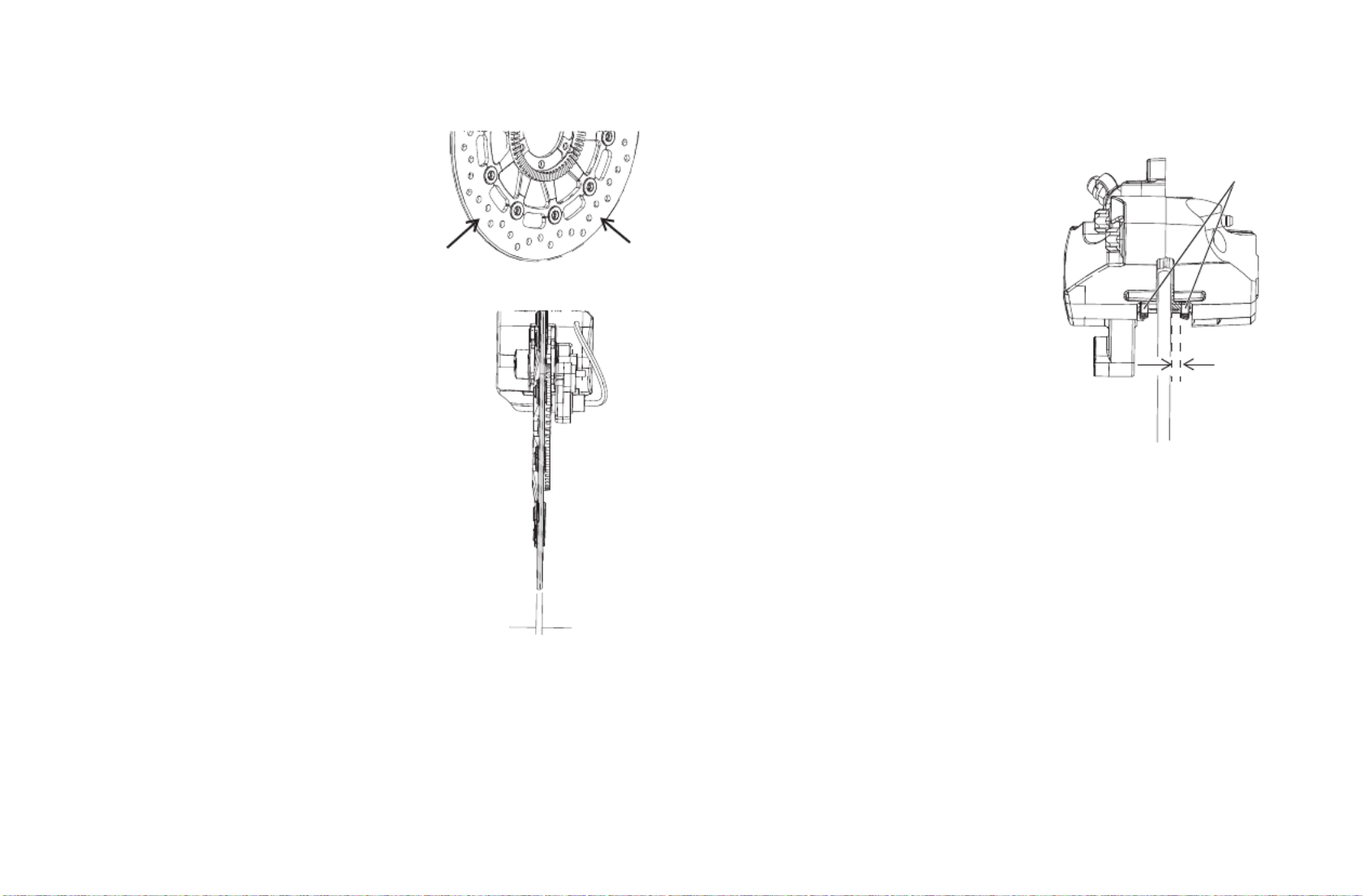
110
Maintenance
Brake Disc Inspection/Cleaning
1. Inspect brake discs for nicks,
scratches, cracks or other
damage. Inspect the thickness of
each brake disc at four or more
locations around the disc. If any
disc is worn to the minimum
thickness at the thinnest point, or
if a disc is damaged, see your
dealer for replacement.
2. Clean discs if minor squeaks
develop due to dirt or dust. Apply
brake cleaner to a clean shop
towel and wipe the discs. DO NOT
allow brake cleaner to contact
painted or plastic parts. Read all
precautions on the label.
Brake Pads
Inspect each front brake pad on
both sides of the front disc. Inspect
each rear brake pad on both sides
of the rear disc. Replace brake
pads when the thinnest point of the
friction material has worn to 1.0
mm. Please see your dealer for
this service.
Tip: After replacing pads, allow up to
250 miles (500 km) of operation in
urban driving conditions (not
highway cruising) to allow pads to
mate with new rotors. Brakes
should be used frequently. During
this time brake performance will
be less effective. Avoid using
brakes harshly unless in an
emergency. Brake efficiency will
gradually increase during this seating period.
When checking brake pad friction material thickness, check
each brake caliper for dampness or stains from leaking or
dried brake fluid. If inspection reveals signs of fluid
leakage, do not operate the vehicle. See your dealer for
service.
Minimum
Thickness
Front: 4.5 mm
Rear: 6.5 mm
Inspect Surface
Friction
Material
Minimum:
1.0 mm
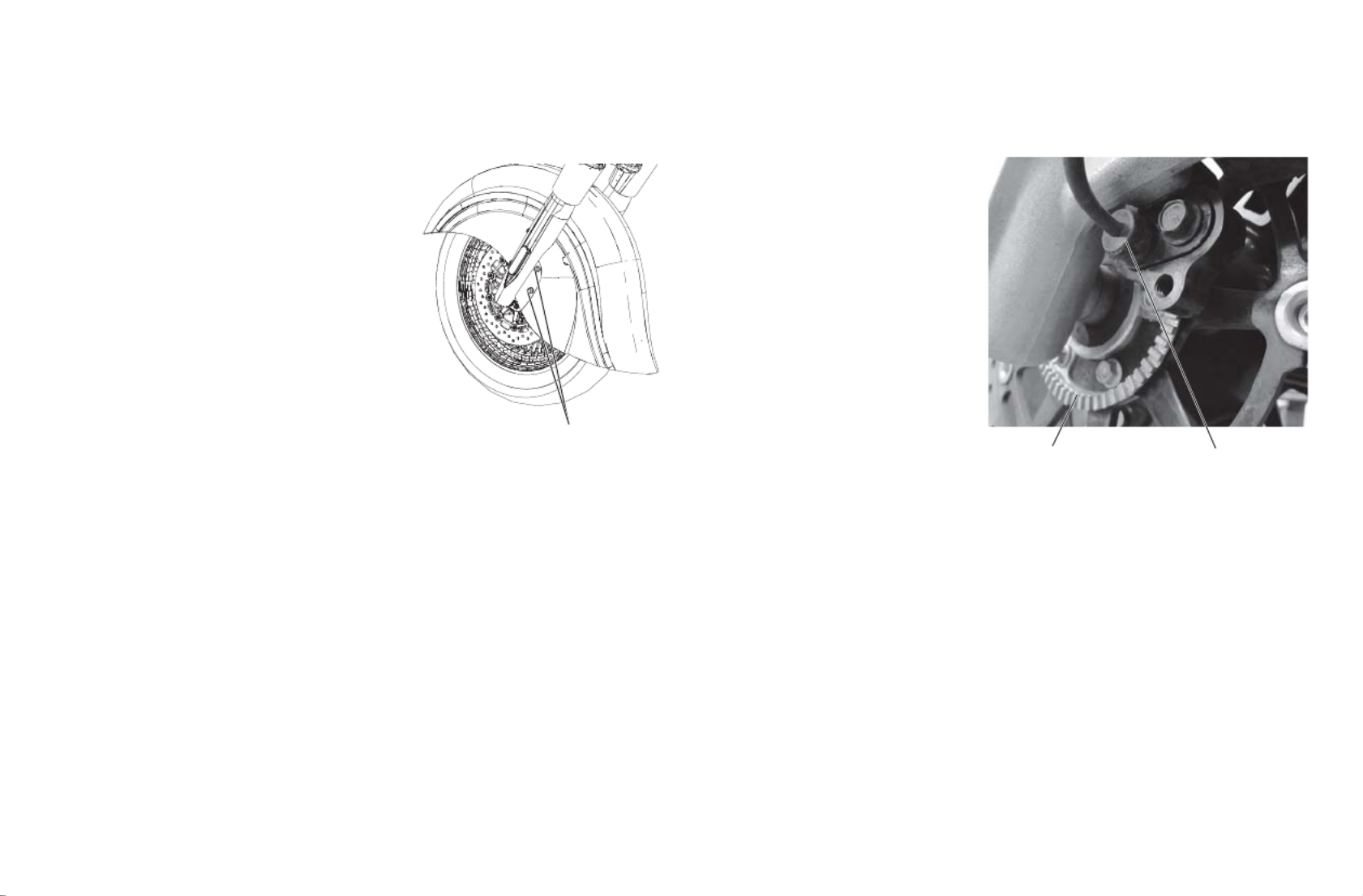
111
Maintenance
Brake Pads
Front Brake Pad Inspection
1. Remove the two acorn nuts
and one screw securing
the protective caliper
covers. Remove the
covers.
2. Use an inspection mirror,
positioned at the front side
of the caliper, to view the
friction material.
3. Reinstall the caliper
covers.
Torque: 18 ft-lbs (24 Nm)
Rear Brake Pad Inspection
1. Position the motorcycle on the sidestand with the
handlebars turned to the left.
2. Use an inspection mirror, positioned at the front side of
the caliper, to view the friction material.
Anti-Lock Brake System (ABS) Tone
Ring/Sensor Inspection
1. Visually inspect for
damaged teeth on the
front and rear ABS
tone rings. Inspect for
nicks and dents on the
face of the teeth. The
teeth edges should be
consistent in
appearance. If a tone
ring is damaged, see
your dealer for
replacement as soon
as possible.
2. Inspect for debris
adhering to the end of
the wheel speed
sensors. If contamination is observed, or if you are
unable to visually inspect, slide a thin towel across the
face of the sensor between the sensor and the tone ring
to remove any potential debris.
Front Caliper Cover Nuts
Tone Ring
Teeth Wheel Speed
Sensor
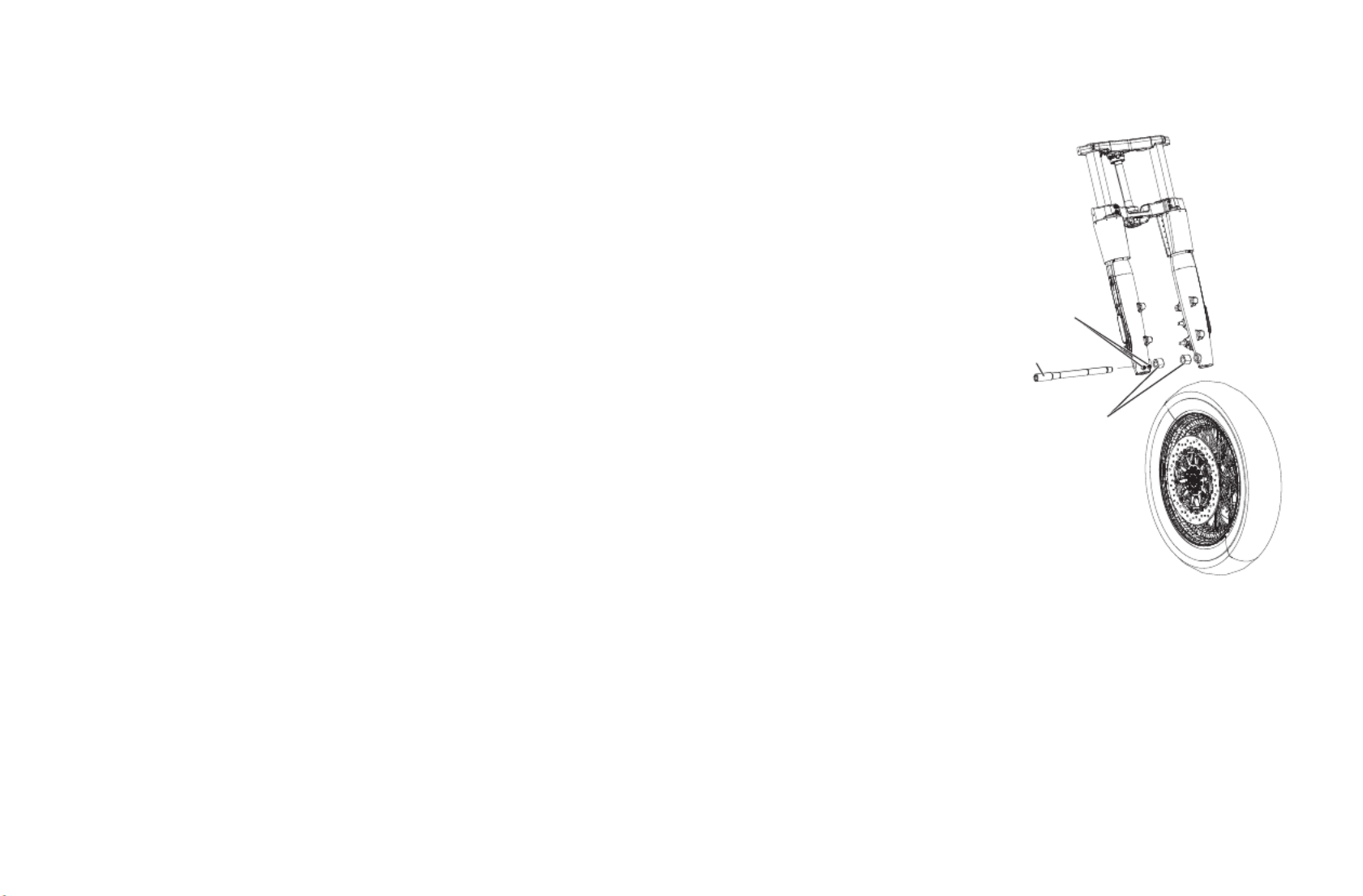
112
Maintenance
Wheel Spokes (if equipped)
Inspect both wheels for loose, bent, broken or missing
spokes (if equipped). To identify loose spokes, grasp each
spoke and try to move it side to side or up and down. All
spokes should be equally tight and have the same amount of
flex. Tighten loose spokes and replace bent, broken or
missing spokes (see an authorized dealer).
WARNING! Spokes adjusted or replaced improperly could distort
the wheel, make the motorcycle difficult to handle, and cause loss of
control.
Wheel Inspection
Inspect both wheels for cracks or damage and replace
damaged wheels promptly. Do not operate the motorcycle if
wheels are damaged or cracked. See the INDIAN
MOTORCYCLE Service Manual or an authorized INDIAN
MOTORCYCLE dealer.
Wheel Alignment
Inspect rear wheel alignment at regular service intervals,
whenever the rear wheel is removed and when the rear
drive belt is adjusted. Please see your dealer for this
service.
Front Wheel Installation
If the front wheel is
removed for any
reason, it must be
reinstalled in the
correct rotating
direction.
Clean all wheel
components before
installation. Apply a
light coat of all-
purpose grease to
the axle and both
spacers.
Axle Bolt
52 ft-lbs (70 Nm)
Right
Fork
Tube
Left
Fork
Tube
Wheel Spacers
0.925 in. (23.5 mm)
Pinch Bolts
18-19 ft-lbs
(24.4-25.7 Nm)
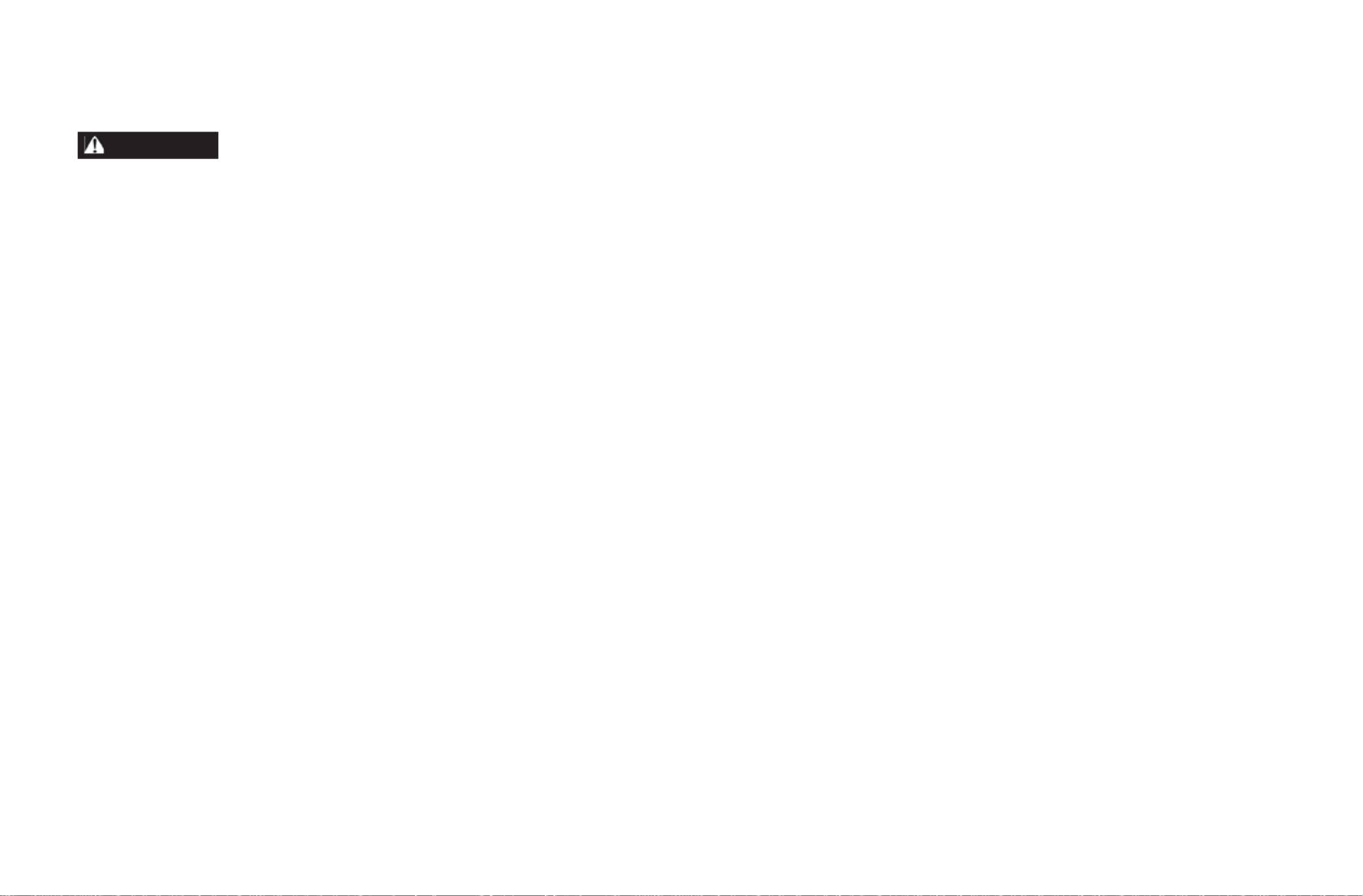
113
Maintenance
Tires
Operating the motorcycle with incorrect tires, incorrect tire pressure
or excessively worn tires could cause loss of control or accident.
Underinflation can cause a tire to overheat and result in a tire
failure. Always use the correct size and type of tires specified by
INDIAN MOTORCYCLE for your vehicle. Always maintain proper tire
pressure as recommended in the rider’s manual and on safety labels.
Tire Replacement
NOTICE: On models equipped with a TPMS, the sensors are located
180° from the valve stem. Use caution when servicing tires.
To avoid damaging a sensor, break the bead at the valve
stem, then at 90° and 270° from the valve stem as required.
Tires, rims, innertubes and air valves must be correctly
matched to wheel rims. Use only the proper size tires
specified with the same or higher load ratings. INDIAN
MOTORCYCLE-recommended tires provide proper
clearance between fenders, swingarm, drive belts and
other components. See the Specifications section beginning
on page 143.
On models equipped with innertubes, innertubes MUST be
replaced with new innertubes when tires are replaced. Use
only the proper size innertubes.
WARNING! Mismatched tires, rims and air valves may result in
damage to the tire bead during mounting or may allow the tire to slip
off the rim, possibly resulting in tire failure.
Tire Condition
Inspect the tire sidewalls, road contact surface, and tread
base for cuts, punctures, and cracking. Replace damaged
tires immediately. See the INDIAN MOTORCYCLE Service
Manual or an authorized INDIAN MOTORCYCLE dealer.
Tire Tread Depth
Replace any tire with a tread depth of less than 1/16 inch (1.6
mm).
Tread wear indicators are located in at least six places on
the tread circumference and become visible at a tread
depth of approximately 1/16 inch (1.6 mm). The tread wear
indicators appear as a solid band across the tread.
You may also use a depth gauge or an accurate ruler to
measure the depth of the center tire tread on both front and
rear tires.
WARNING
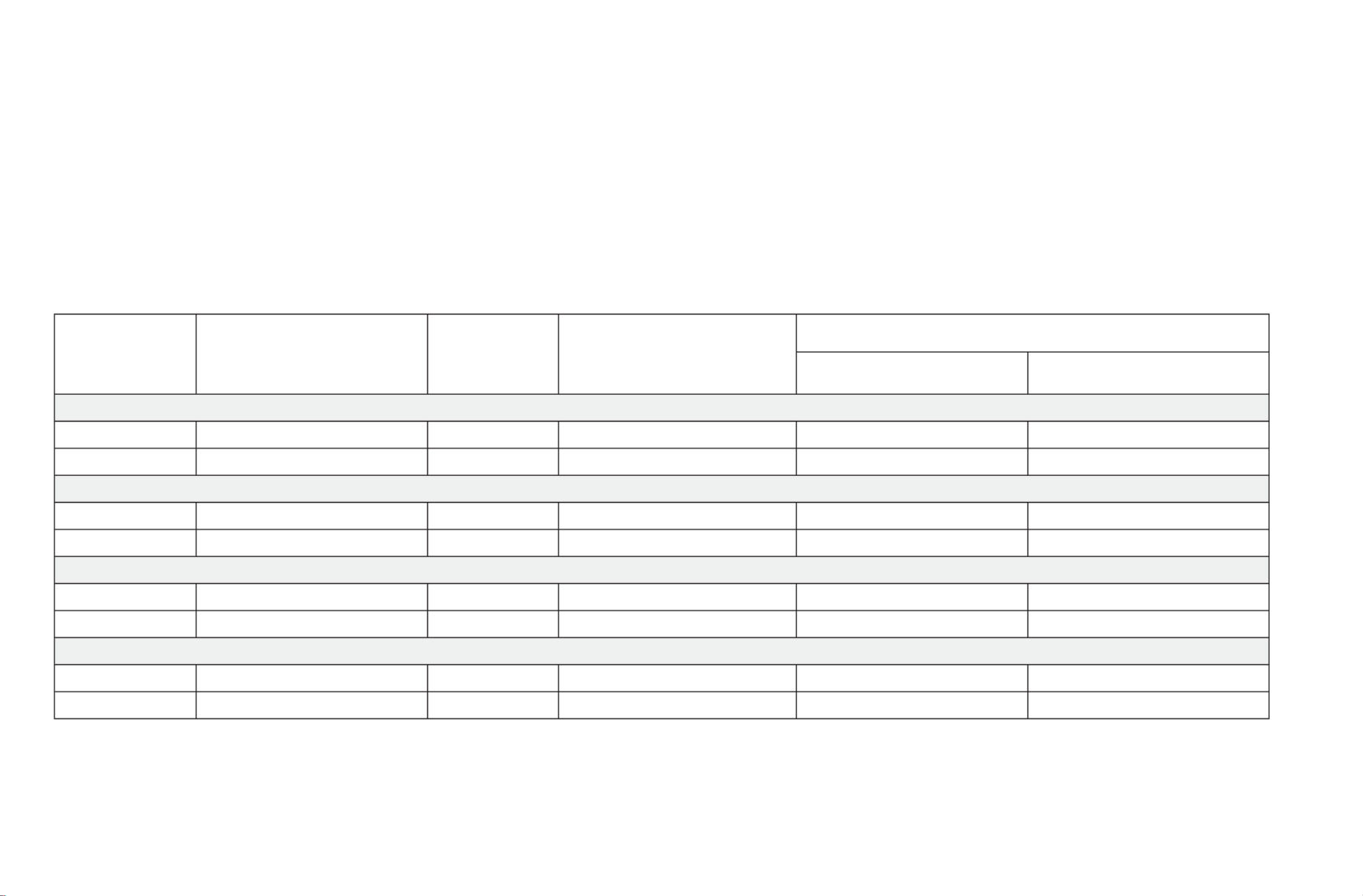
114
Maintenance
Tires
Tire Pressure
Always check and adjust tire pressure when tires are cold. Do not adjust tire pressure immediately after riding. Wait at least 3
hours after riding to check pressure. If pressure checked and adjusted while tires are warm, the pressure will drop as tires
cool and result in underinflation.
Adjust tire pressure as recommended for the total weight of your intended load (see chart below). For more information, refer
to the manufacturing information label located on the front frame downtube. See page 20.
WARNING! Do not exceed the maximum recommended inflation pressure to seat the bead. Tire or rim failure may result.
Location Size Brand Type
Recommended Pressure
Loads up to 200 lbs.
(91 kg)
Loads up to vehicle’s
maximum load capacity
Black Tires - CHIEF Classic/ CHIEF Dark Horse
Front 130/90-B16 73H Dunlop Elite 3 36 psi (248 kPa) 36 psi (248 kPa)
Rear 180/65-B16 81H Dunlop American Elite 40 psi (276 kPa) 40 psi (276 kPa)
White Wall Tires - CHIEF Vintage
Front 130/90-B16 67H Dunlop American Elite 36 psi (248 kPa) 36 psi (248 kPa)
Rear 180/65-B16 81H Dunlop American Elite 40 psi (276 kPa) 40 psi (276 kPa)
Black Tires - SPRINGFIELD
Front 130/90-B16 73H Dunlop Elite 3 36 psi ( kPa)248 36 psi ( kPa)248
Rear 180/60-R16 80H Dunlop Elite 3 41 psi (283 kPa) 41 psi (283 kPa)
Black Tires - CHIEFTAIN Models/ROADMASTER
Front 130/90-B16 73H Dunlop Elite 3 36 psi (248 kPa) 36 psi (248 kPa)
Rear 180/60-R16 80H Dunlop Elite 3 41 psi (283 kPa) 41 psi (283 kPa)
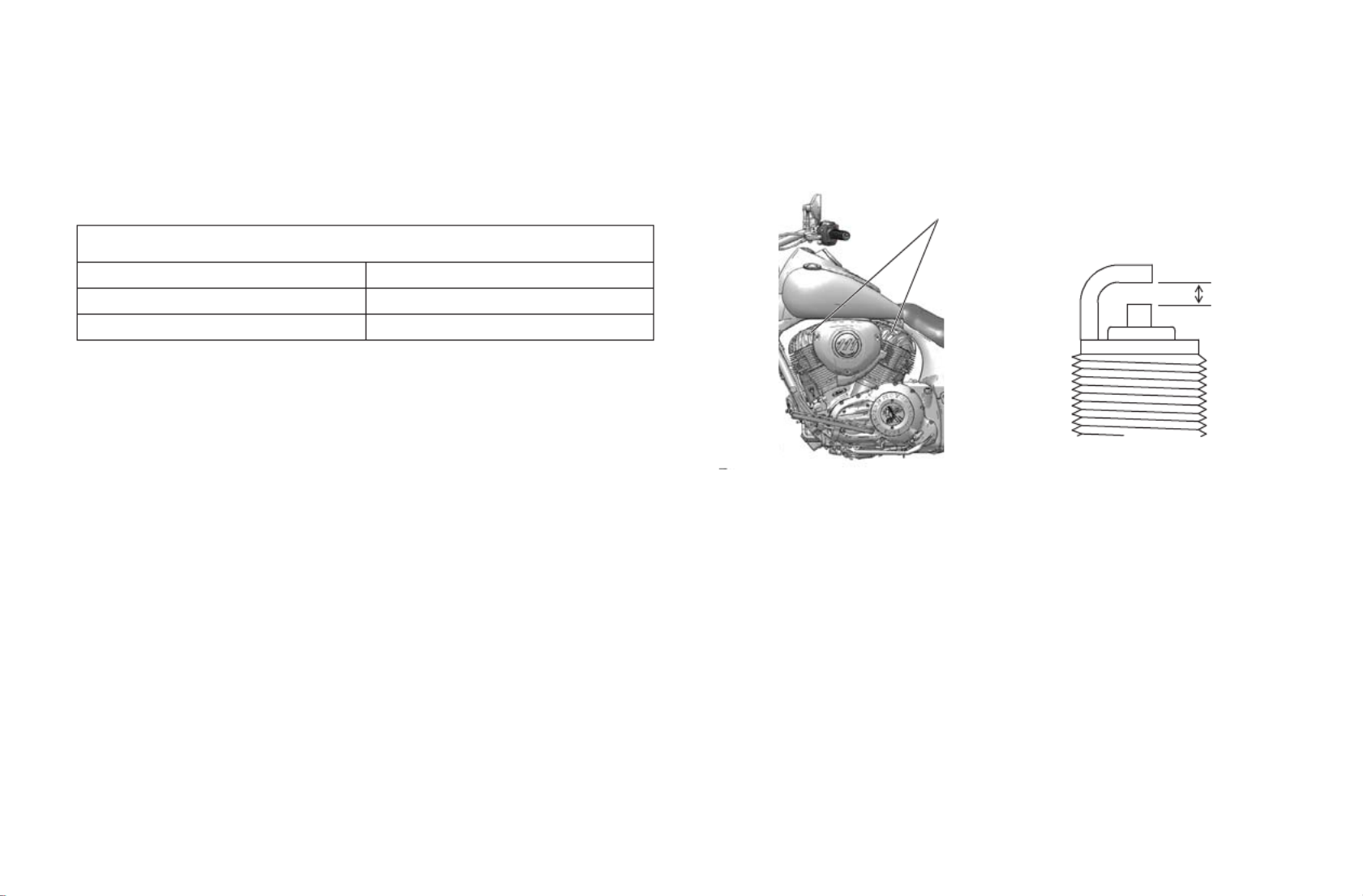
115
Maintenance
Spark Plugs
Inspect spark plugs after the break-in period and every
15,000 miles (24,000 km) thereafter. Replace spark plugs
every 30,000 miles (48,000 km). Always replace spark plugs
in pairs.
1. Make sure the engine has cooled to room temperature.
2. Turn the power switch off.
3. Pull upward on the spark plug boots (not the wires) to
remove the boots.
CAUTION! Wear eye and face protection when using pressurized
air.
4. To prevent debris from entering the spark plug holes,
use compressed air to clean the area around the plugs
before removing them.
Tool: 12 mm plug socket
Tip: Both spark plugs should have the same light or medium tan
color deposits. The electrodes should be square with sharp
edges.
5. Reinstall the spark plugs or install new plugs.
6. Reinstall the spark plug boots.
Spark Plug Specifications
Spark Plug Type NGK DCPR8E
Spark Plug Gap .036 inch (.9 mm)
Spark Plug Torque 12 ft-lbs (16.3 Nm)
Spark Plugs
.036 inch
(0.9 mm)
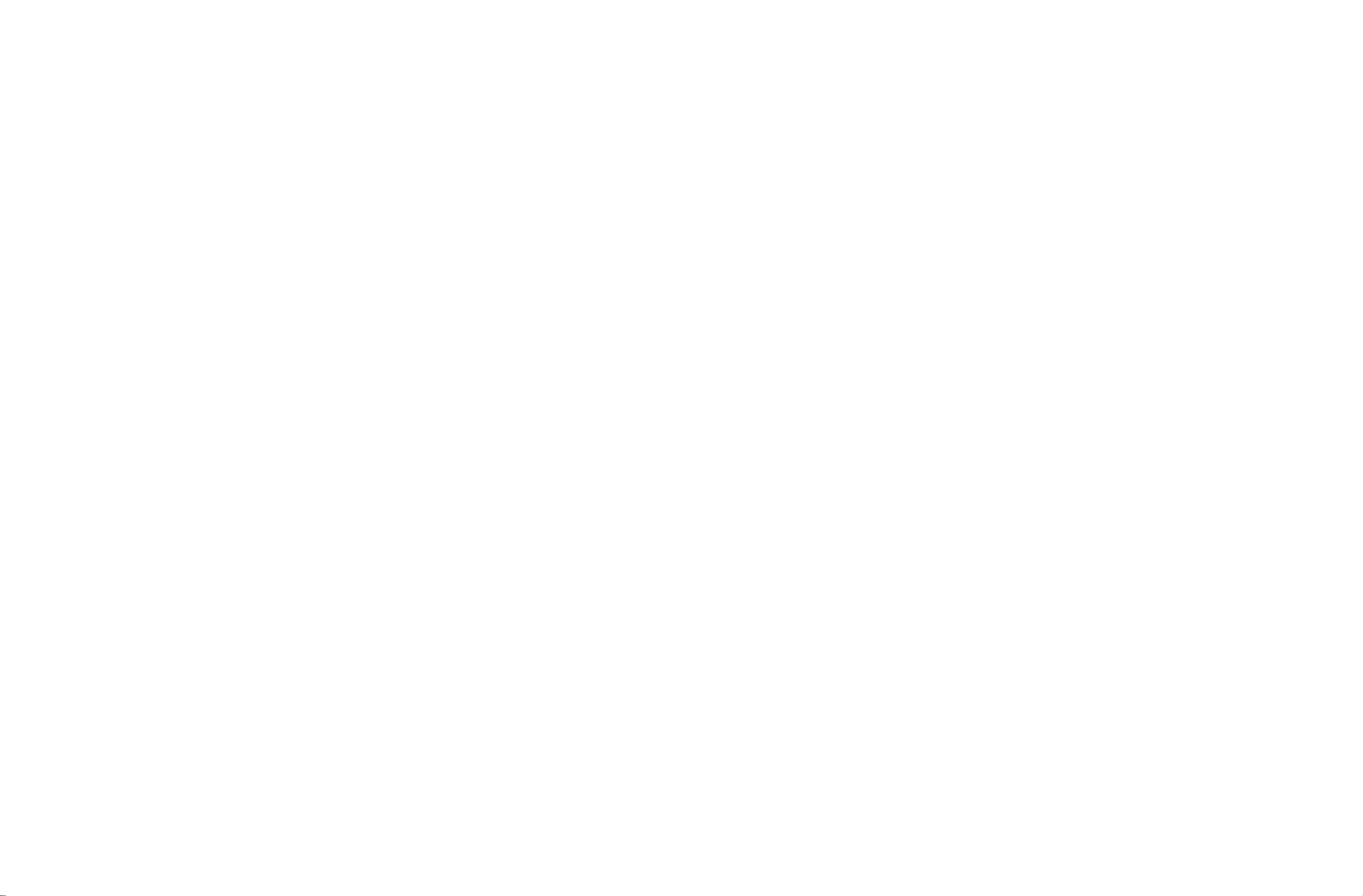
116
Maintenance
Side Covers
Remove the left side cover to access the tool kit, shock air
fitting (if equipped), fuse box and diagnostic connector.
Remove both side covers to access the seat mounting
fasteners and the electrical connections for the saddlebags
(if equipped).
1. Pull outward at each corner of the side cover to
disengage the three darts.
2. Remove the side cover from the motorcycle.
3. To reinstall the side cover, make sure each rubber
grommet is properly positioned. Align each dart with
the appropriate grommet and press inward firmly to
secure each dart.
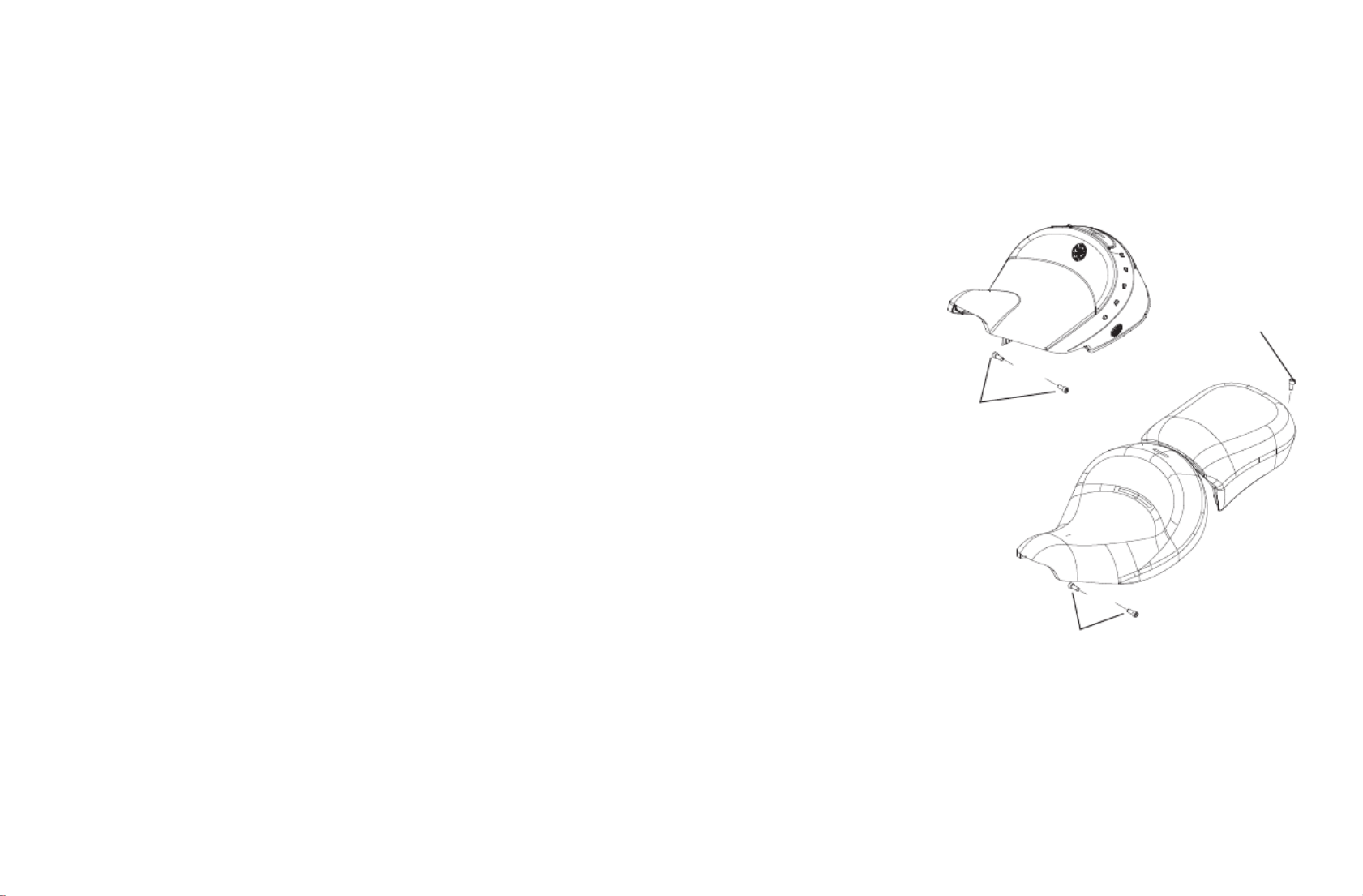
117
Maintenance
Seat Removal
Applies to: CHIEF Models/SPRINGFIELD/CHIEFTAIN Models
Remove the seat to access the battery.
1. Remove the left side cover to access the tool kit.
2. Locate the seat mount brackets under the edge of the driver’s seat. Remove
the seat mount bolt from each side of the seat.
3. Remove the rear bracket bolt, washer and nylon grommet from the passenger
portion of the seat (if equipped).
4. Lift the rear of the seat and pull rearward to disengage the front mounting tab
of the seat from the frame mount. Do not allow the seat mount brackets to
contact the rear fender.
Seat Installation
Applies to: CHIEF Models/SPRINGFIELD/CHIEFTAIN Models
1. Position the seat by inserting the seat mounting tab from rear to front into the
mount on the top of the frame.
2. Rotate the rear of the seat downward and position the side mount seat brackets
onto the frame. Do not allow the seat mount brackets to contact the rear
fender.
3. On each side, thread the seat mount bolt through the seat mount bracket and
into the frame. Torque seat bolts to specification.
Torque: 18 ft-lbs (13.5 Nm)
4. Secure the passenger seat (if equipped). Gently raise the rear bracket and
reinstall the nylon grommet. Thread the rear bracket bolt and washer through
the bracket and nylon grommet. Torque the bolt to specification.
Torque: 96 in-lbs (10.8 Nm)
Seat Mount
Bolts
Rear
Bracket Bolt
(if equipped)
Seat Mount
Bolts
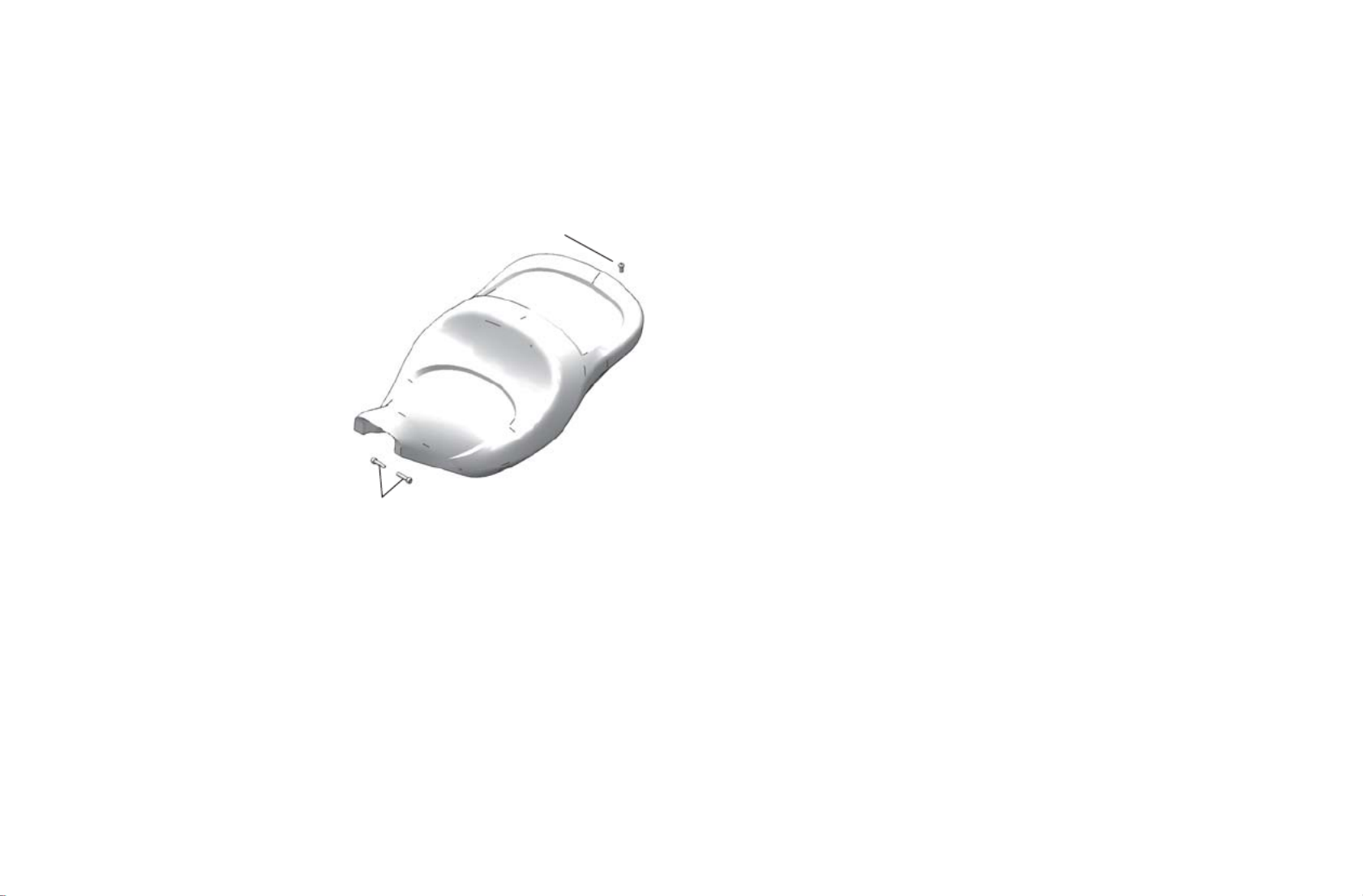
118
Maintenance
Seat Removal (ROADMASTER)
1. Remove the left side cover to access the tool kit.
2. Remove the trunk. See page 56.
3. Disconnect the trunk harness from the main harness.
4. Locate the seat mount
brackets under the
edge of the driver’s
seat. Remove the seat
mount bolt from each
side of the seat.
5. Remove the rear
bracket bolt, washer
and nylon grommet
from the passenger
portion of the seat.
6. Lift the rear of the seat
and unplug the seat
heater.
7. Pull the seat rearward to disengage the front mounting
tab of the seat from the frame mount. Do not allow the
seat mount brackets to contact the rear fender.
Seat Installation (ROADMASTER)
1. Position the seat by inserting the seat mounting tab from
rear to front into the mount on the top of the frame.
2. Reconnect the seat heater.
3. Rotate the rear of the seat downward and position the
side mount seat brackets onto the frame. Do not allow
the seat mount brackets to contact the rear fender.
4. On each side, thread the seat mount bolt through the
seat mount bracket and into the frame. Torque seat bolts
to specification.
Torque: 18 ft-lbs (13.5 Nm)
5. Gently raise the rear bracket and reinstall the nylon
grommet. Thread the rear bracket bolt and washer
through the bracket and nylon grommet. Torque the bolt
to specification.
Torque: 96 in-lbs (10.8 Nm)
6. Reconnect the trunk harness to the main harness.
7. Reinstall the trunk. See page 56.
Seat Mount Bolts
Rear Bracket Bolt
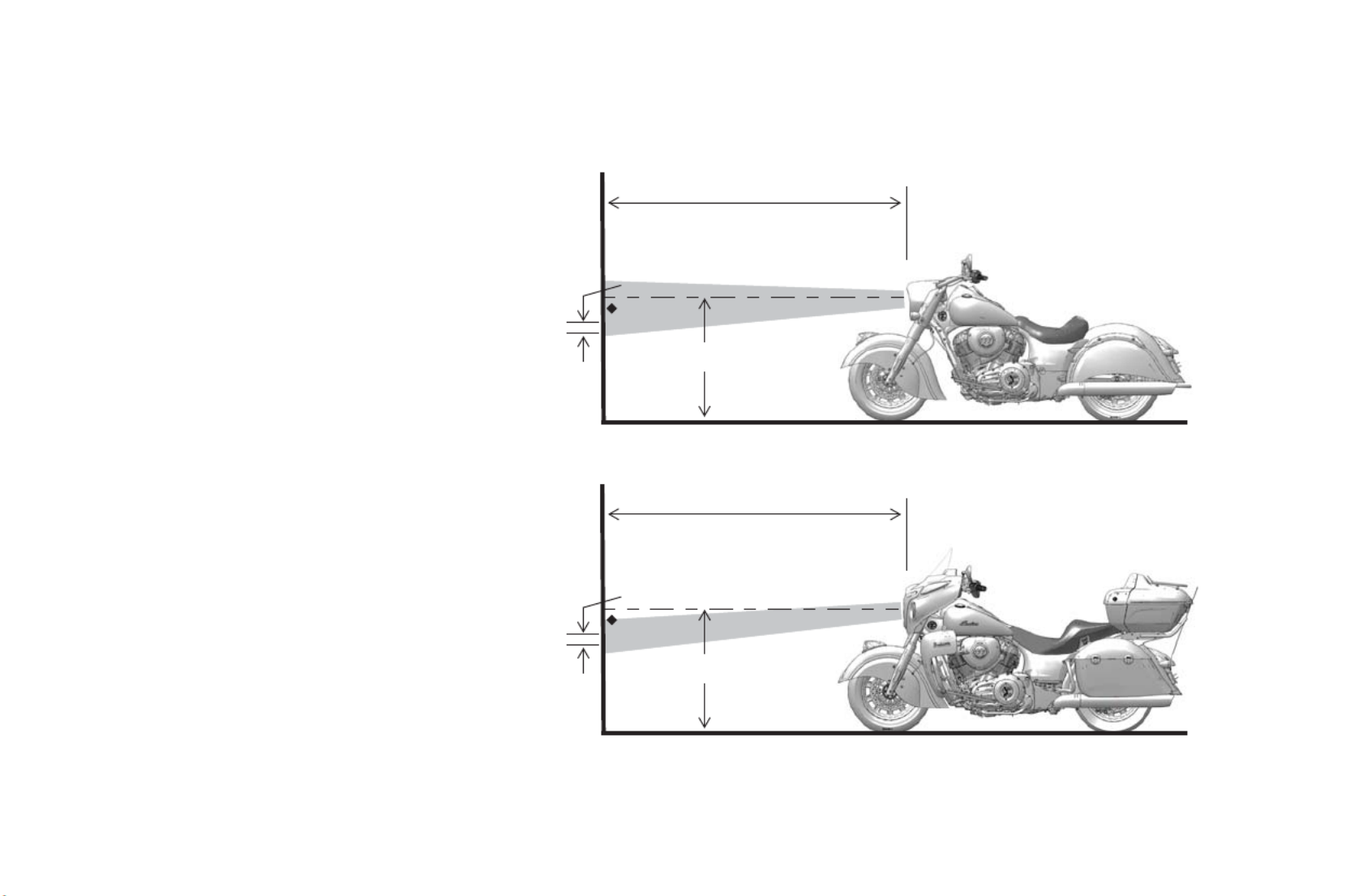
119
Maintenance
Headlight Aim Inspection
CHIEF Models/SPRINGFIELD/CHIEFTAIN
Models: On HIGH beam, the center of highest
intensity (appearing as a diamond shape)
should be 7.5 in. (19 cm) lower than the
headlamp and centered straight ahead at 25
feet (7.6 m).
ROADMASTER: On LOW beam, the top of the
low beam cut-off (appearing as a diamond
shape) should be 3 in. (7.6 cm) lower than the
headlamp center height at 25 feet (7.6 m).
1. Verify that tire pressure is at specification.
See page 114.
2. Verify that rear suspension ride height
(preload) is at specification. See page 98.
3. Position the motorcycle on a level surface
with the headlight 25 feet (7.6 m) from a
wall.
4. With the operator and passenger (if
applicable) on board, bring the
motorcycle to the fully upright position.
5. Start the engine and switch the headlamp
to high beam. Observe the headlight aim
on the wall.
6. Make any necessary adjustments to
headlight aim. See page 120.
25 ft. (7.6 m)
7.5 in. (19 cm)
25 ft. (7.6 m)
Headlamp Center Height
3 in. (7.6 cm)
LOW Beam (ROADMASTER)
Headlamp Center Height
HIGH Beam (CHIEF/CHIEFTAIN/CHIEF DARK HORSE/SPRINGFIELD)
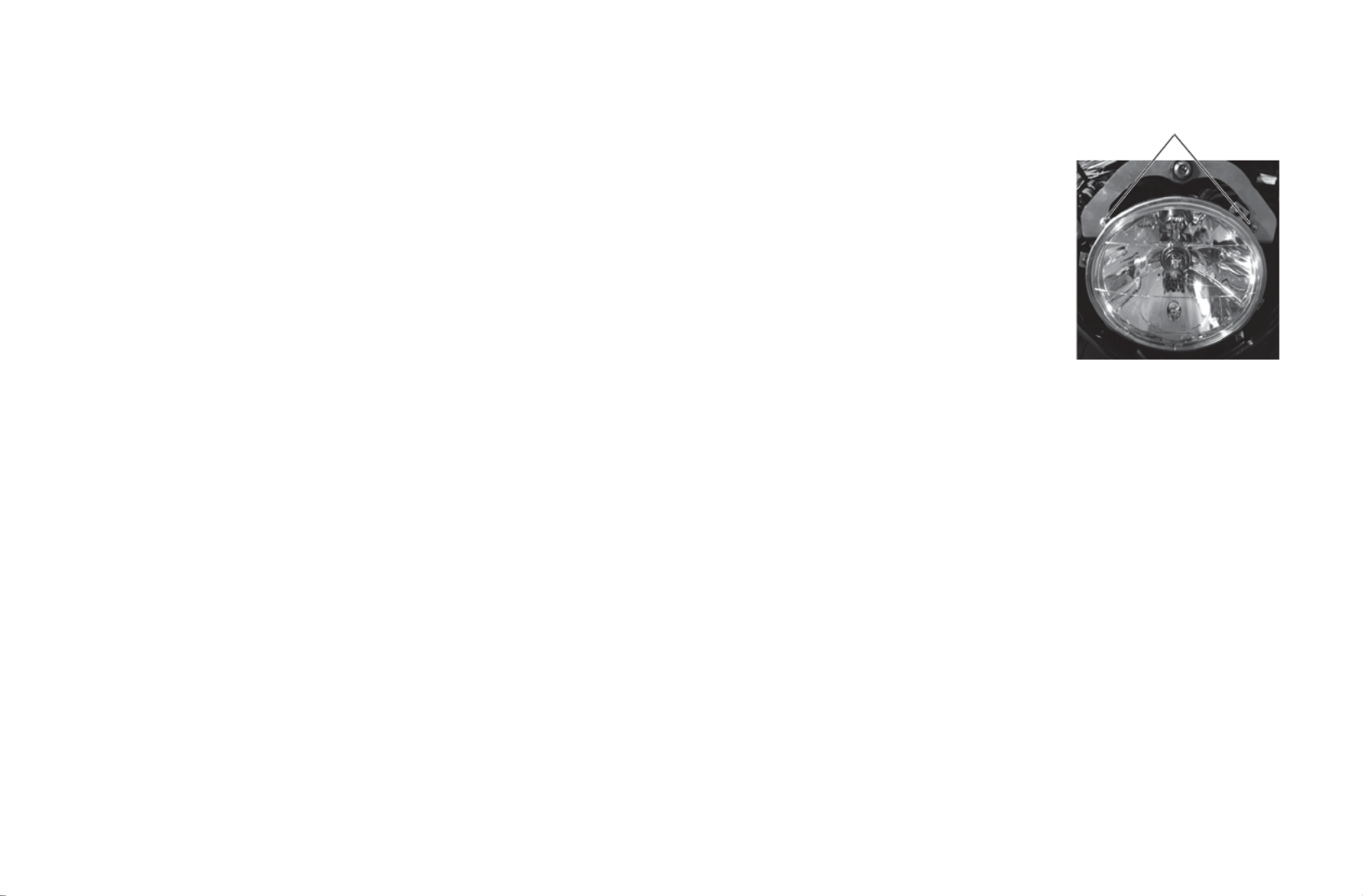
120
Maintenance
Headlight Aim Adjustment
The headlamp adjustment screws are located inside the headlamp housing.
1. Remove the two headlight bezel screws (CHIEFTAIN Models/ROADMASTER only) and
remove the bezel from the fairing. Reinstall the bezel after adjusting the headlamp.
Tool: M4 hex wrench or universal tool
2. To adjust the headlamp vertically, tighten both top adjustment screws equally to adjust the
beam downward. Loosen both screws equally to adjust the beam upward.
Tool: M4 hex wrench or universal tool
3. To adjust the headlamp horizontally, loosen the left side screw to adjust the beam to the
left. Loosen the right side screw to adjust the beam to the right.
Headlight Lamp Replacement
Applies to: CHIEF Models/SPRINGFIELD
1. Remove the six bolts securing the front nacelle headlight shroud. Pull this piece forward to access the headlight.
2. Remove the sealing boot. Press the looped end of the wire bulb retainer clip and swing the end toward the center of the
bulb to release it from the latch tab.
3. With the wire connector attached, pull the bulb out. Disconnect the wire harness.
4. Install the new bulb and secure the retainer.
Tip: Avoid touching a halogen lamp with bare fingers. Oil from your skin leaves a residue, causing a hot spot that will shorten the life of the
lamp. If a lamp is touched, clean it thoroughly with denatured alcohol.
5. Reinstall the sealing boot. Make sure it seals tightly around the bulb base and lens to prevent condensation.
6. Reinstall the front nacelle headlight shroud.
7. Tighten the two (2) top bolts.
Torque: 36 in-lbs (4 Nm)
8. Tighten the four (4) rear bolts.
Torque: 84 in-lbs (9.5 Nm)
Adjustment
Screws
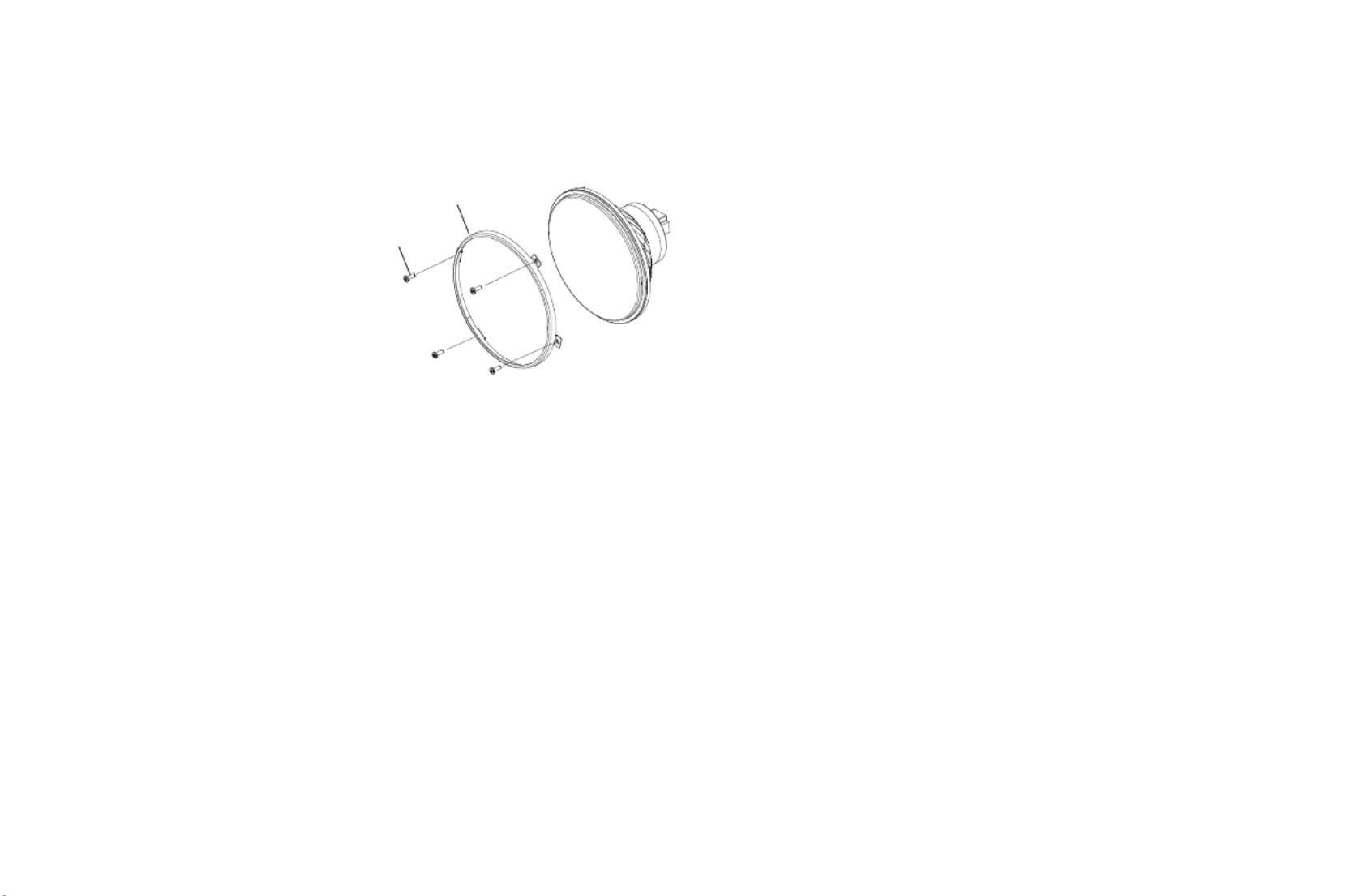
121
Maintenance
Headlight Lamp Replacement
(CHIEFTAIN Models)
1. Remove the two bolts
securing the front trim
bezel to the fairing.
Pull this piece forward
to access the
headlight.
2. Remove the four
screws securing the
headlamp retaining
ring. Remove the
retaining ring.
Tool: Phillips screwdriver or universal tool
3. Remove the headlight assembly from the headlight
carrier.
4. Remove the sealing boot. Press the looped end of the
wire bulb retainer clip and swing the end toward the
center of the bulb to release it from the latch tab.
5. With the wire connector attached, pull the bulb out.
Disconnect the wire harness.
6. Install the new bulb and secure the retainer.
Tip: Avoid touching a halogen lamp with bare fingers. Oil from your
skin leaves a residue, causing a hot spot that will shorten the life
of the lamp. If a lamp is touched, clean it thoroughly with
denatured alcohol.
7. Reinstall the sealing boot. Make sure it seals tightly
around the bulb base and lens to prevent condensation.
8. Reinstall the headlight assembly into the carrier, being
sure to index the assembly properly.
9. Reinstall the retaining ring with the four screws.
Torque: 12 in-lbs (1.4 Nm)
10. Reinstall the front trim bezel and bolts.
Torque: 36 in-lbs (4 Nm)
Headlight Lamp Replacement
(ROADMASTER)
The LED headlight is not serviceable. If the headlight
becomes damaged or inoperable, the entire headlight
assembly must be replaced. See your authorized INDIAN
MOTORCYCLE dealer.
Taillight/Brake Light Replacement
The LED taillight and brake lights are not serviceable. If the
taillight or a brake light becomes damaged or inoperable,
the entire light assembly must be replaced. See your
authorized INDIAN MOTORCYCLE dealer.
Step 2
Retaining
Ring
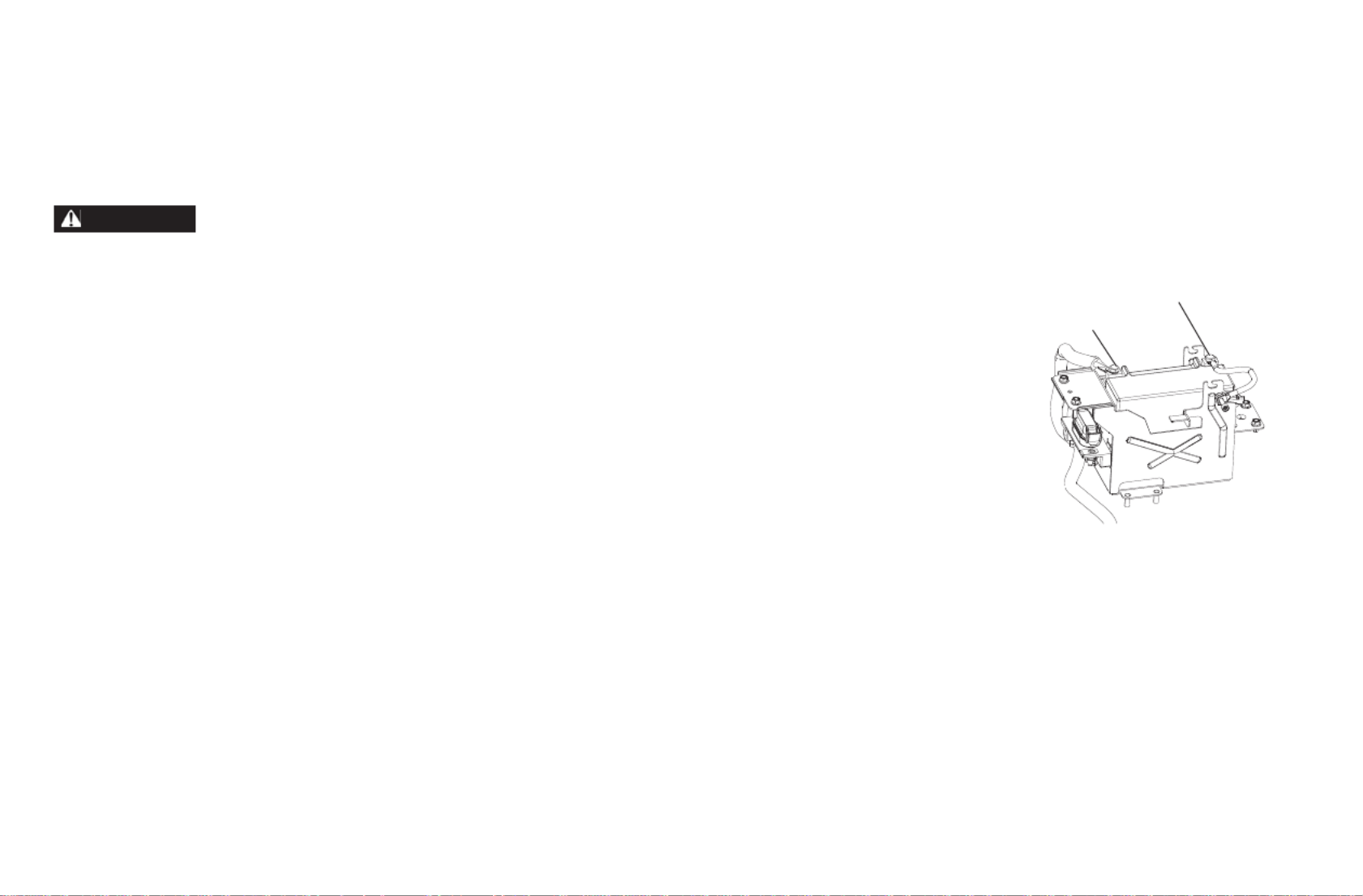
122
Maintenance
Battery
The motorcycle battery is a sealed, maintenance-free
battery. Do not remove the battery cap strip for any reason.
Keep the battery connections clean and tight at all times.
Battery electrolyte is poisonous. It contains sulfuric acid. Serious
burns can result from contact with skin, eyes or clothing.
Antidote:
External: Flush with water.
Internal: Drink large quantities of water or milk. Follow with milk of
magnesia, beaten egg, or vegetable oil. Call physician immediately.
Eyes: Flush with water for 15 minutes and get prompt medical
attention.
Batteries may produce explosive gases.
• Keep sparks, flame, cigarettes, etc. away.
• Ventilate when charging or using in an enclosed space.
• Always shield eyes when working near batteries.
• KEEP OUT OF REACH OF CHILDREN.
Battery Removal
1. Remove the seat. See page 118.
WARNING! Improperly connecting or disconnecting battery
cables can result in an explosion and cause serious injury or death.
When removing the battery, always disconnect the negative (black)
cable first. When reinstalling the battery, always connect the negative
(black) cable last.
2. Remove the fastener
securing the battery cover
to the frame crossmember.
3. Lift the cover, with the
attached electronic module
in place, folding the wires
toward the fuel tank.
Tool: 5 mm hex key wrench
NOTICE: Do not allow the Electronic
Control Unit (ECU) to
touch the battery
terminals or it will damage
the ECU instantly.
4. Remove the negative (-) battery cable from the battery
terminal. Position the cable well clear of the terminal.
Tool: 10 mm wrench
5. Remove the rubber cover from the positive (+) battery
cable and remove the cable from the terminal. Position
the cable well clear of the terminal.
6. Remove the battery.
WARNING
Negative (-)
Positive (+)
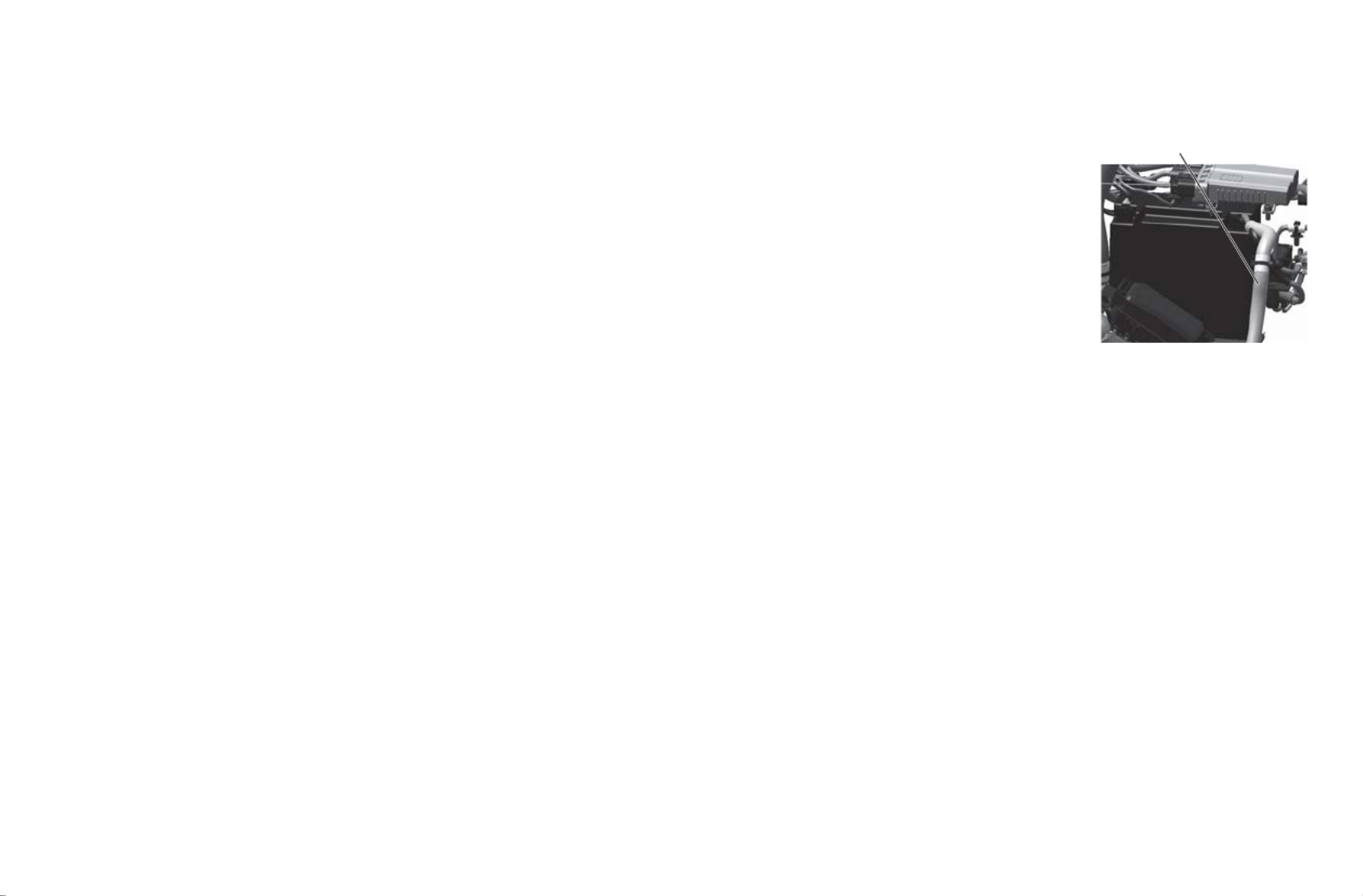
123
Maintenance
Battery Installation
WARNING! Improperly connecting or disconnecting battery
cables can result in an explosion and cause serious injury or death.
When removing the battery, always disconnect the negative (black)
cable first. When reinstalling the battery, always connect the negative
(black) cable last.
NOTICE: Do not remove the battery cables while the engine is
running. Doing so may damage the Electronic Control Unit
(ECU). Take great care not to reverse the battery leads
when installing the battery. Reverse power applied to the
ECU will damage it instantly.
1. Inspect the battery box and cover for damage. Be sure
pads are in good condition and properly located.
2. Make sure cable ends and battery terminals are clean.
Apply a light film of dielectric grease to the terminal
bold threads.
3. Carefully position the battery into the battery box with
the negative (-) terminal toward the front of the
motorcycle.
4. Make sure the positive (+)
cable is routed horizontally
and perpendicular to the long
side of the battery. Connect
the positive (+) cable to the
positive (+) battery terminal.
Torque: 45 in-lbs (5 Nm)
5. Install the negative (-) cable
last. Route the starter ground
cable beneath the frame
ground cable on the negative battery terminal.
Torque: 45 in-lbs (5 Nm)
6. Reinstall the battery cover and fastener.
Torque: 84 in-lbs (9.5 Nm)
7. Reinstall the seat. See page 118.
Positive (+) Cable
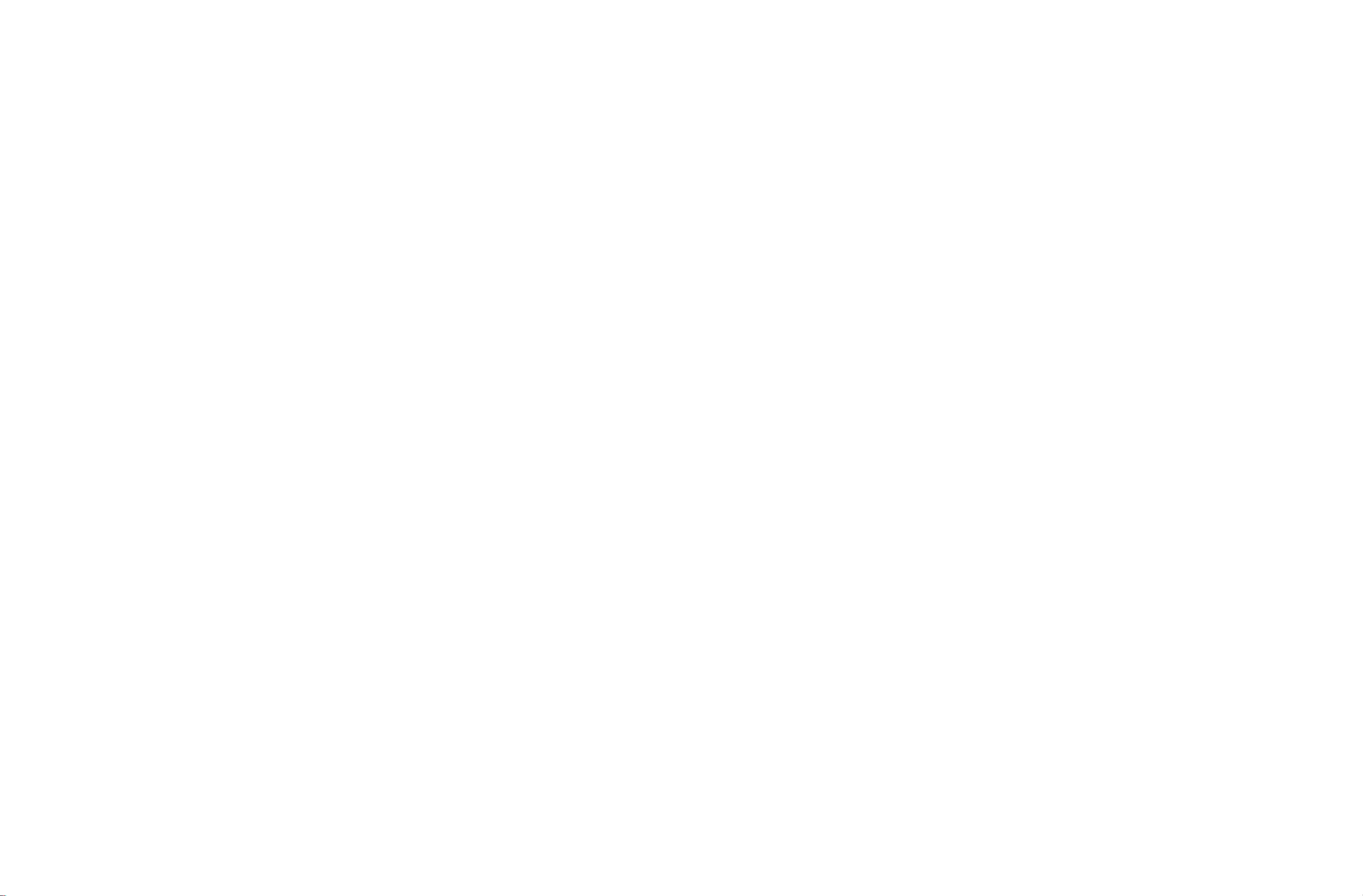
124
Maintenance
Battery Charging
If your motorcycle will not be used for a period of four (4)
weeks or longer, a maintenance charger should be
connected to the battery. A maintenance charger can be
purchased through your authorized INDIAN MOTORCYCLE
dealer.
1. Following the charger manufacturer’s instructions, use a
battery charger designed for use with 12-volt batteries.
The charger should have a maximum charging rate of
1.8 amps. Charge the battery for approximately 10
hours at a rate of 1.8 amps. If you use a taper or trickle
charger, it will take longer to charge the battery.
2. After charging the battery, allow the battery to sit 1-2
hours before checking the state of charge with a DC volt
meter. The charge should be a minimum of 12.5 DC
volts. Repeat the charging cycle if the charge is less than
12.5 DC volts. Replace the battery if it fails to reach 12.5
volts after the second charge.
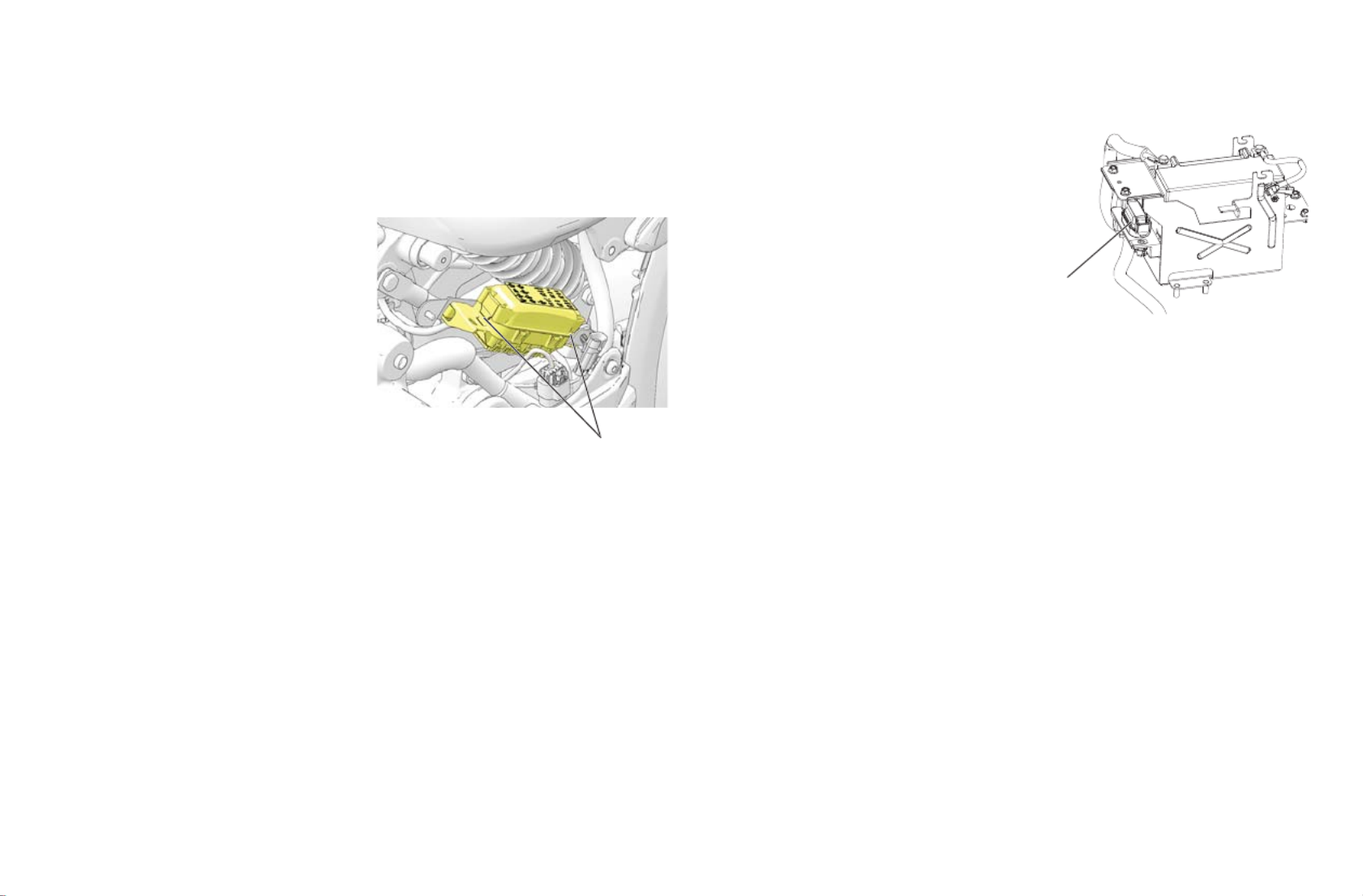
125
Maintenance
Fuse Replacement
NOTICE: Use fuses with the recommended amperage to avoid
damage to the electrical system.
Standard Fuses
The standard fuse box is
located under the left side
cover. This fuse box houses
all standard service fuses
and the automatic circuit
breakers. Fuse application
and size are provided on a
label on the fuse box cover.
Tip: Use the fuse puller
provided in the tool kit to
remove a fuse.
1. Remove the left side
cover. See page 116.
2. Release the locking tabs, then squeeze the upper and
lower cover clips to remove the fuse box cover.
3. After replacing a fuse, reinstall the fuse box cover and
side cover.
High-Current Fuses
The JCASE® fuse box
contains the high-current
fuses for the chassis, vehicle
control module and anti-lock
brake system. This fuse box
is located next to the battery
box.
Fuse application and size are
provided on a label on the
fuse box cover.
Fuse Box
Cover Clips
JCASE®
Fuse Box
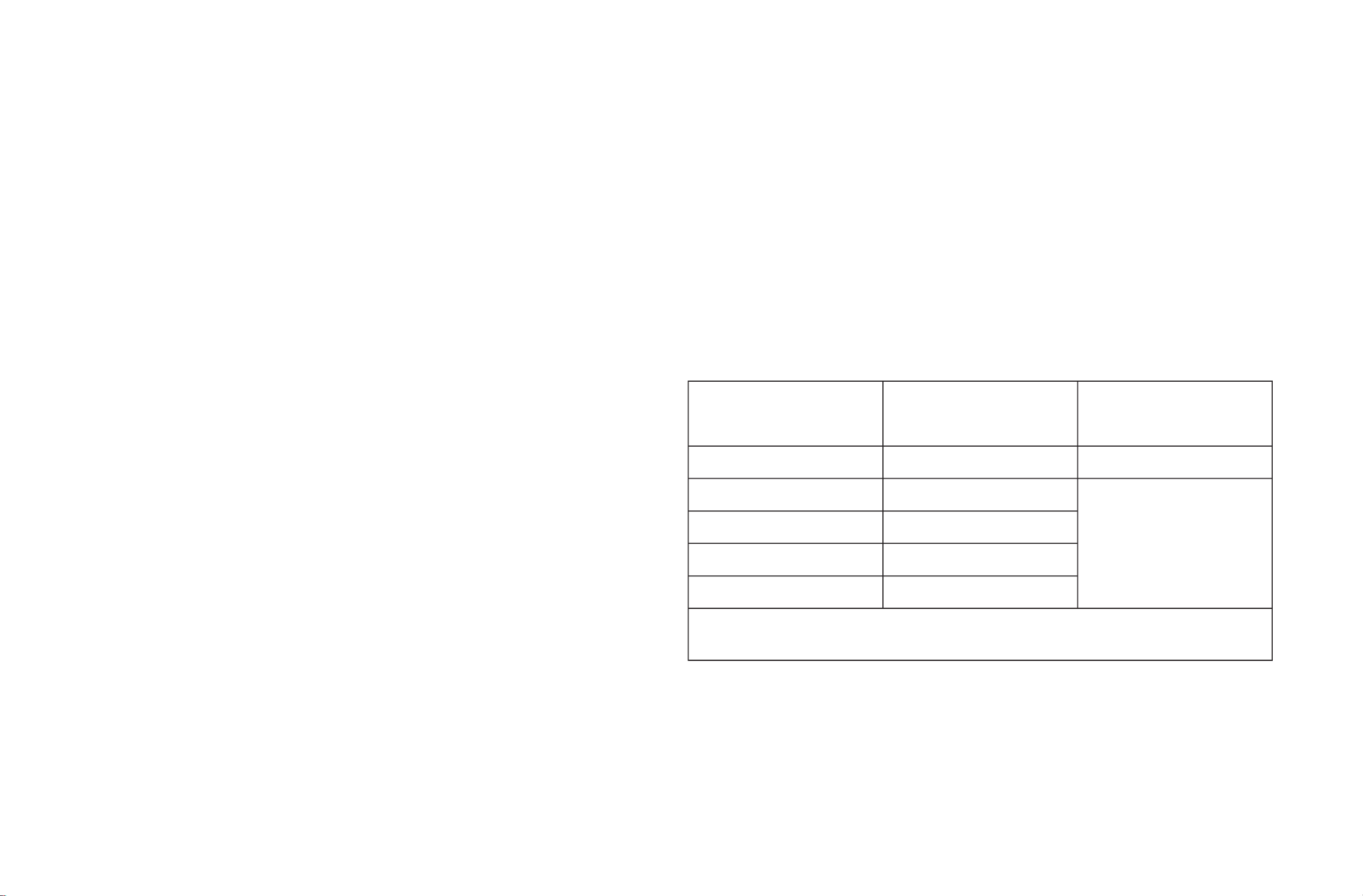
126
Maintenance
Electrical Precautions
Be aware of the following precautions regarding the
electrical system to avoid disruption of electrical signals
and possible system malfunction.
• DO use ONLY genuine INDIAN MOTORCYCLE parts and
accessories designed for your model, and follow the
instructions provided.
• DO use the accessory power connectors located under
the driver’s seat and near the headlight.
• DO NOT splice or cut any wires.
• DO NOT tap in to any power or ground on the motorcycle
unless specifically directed to do so by the INDIAN
MOTORCYCLE instructions that come with the kit.
• DO NOT back-probe electrical connectors on the vehicle
unless directed to do so by the INDIAN MOTORCYCLE
Service Manual.
• DO NOT power any accessories from the diagnostic
connector (under left side cover).
Unlocking the Security System
Your dealer will provide the master personal identification
number (PIN) for the security system. Your dealer may also
change the master PIN to a new rider PIN on your behalf.
Record both PINs on page 5.
Change the dealer-provided PIN to a PIN of your own
choosing as soon as possible after receiving delivery of your
new motorcycle. See page 127.
If a key fob is not available, your rider PIN can be entered
using the turn signal switches to unlock the security system.
Use the following guide to enter your valid rider PIN.
Digit to Enter Turn Signal
Feature Used Procedure
The number “0” CANCEL switch Press and release
First digit (1-9) LEFT turn switch Move and release
once per digit
value. See example
below.
Second digit (1-9) RIGHT turn switch
Third digit (1-9) LEFT turn switch
Fourth digit (1-9) RIGHT turn switch
Example for entering the number 1024:
LEFT - CANCEL - LEFT - LEFT - RIGHT - RIGHT - RIGHT - RIGHT
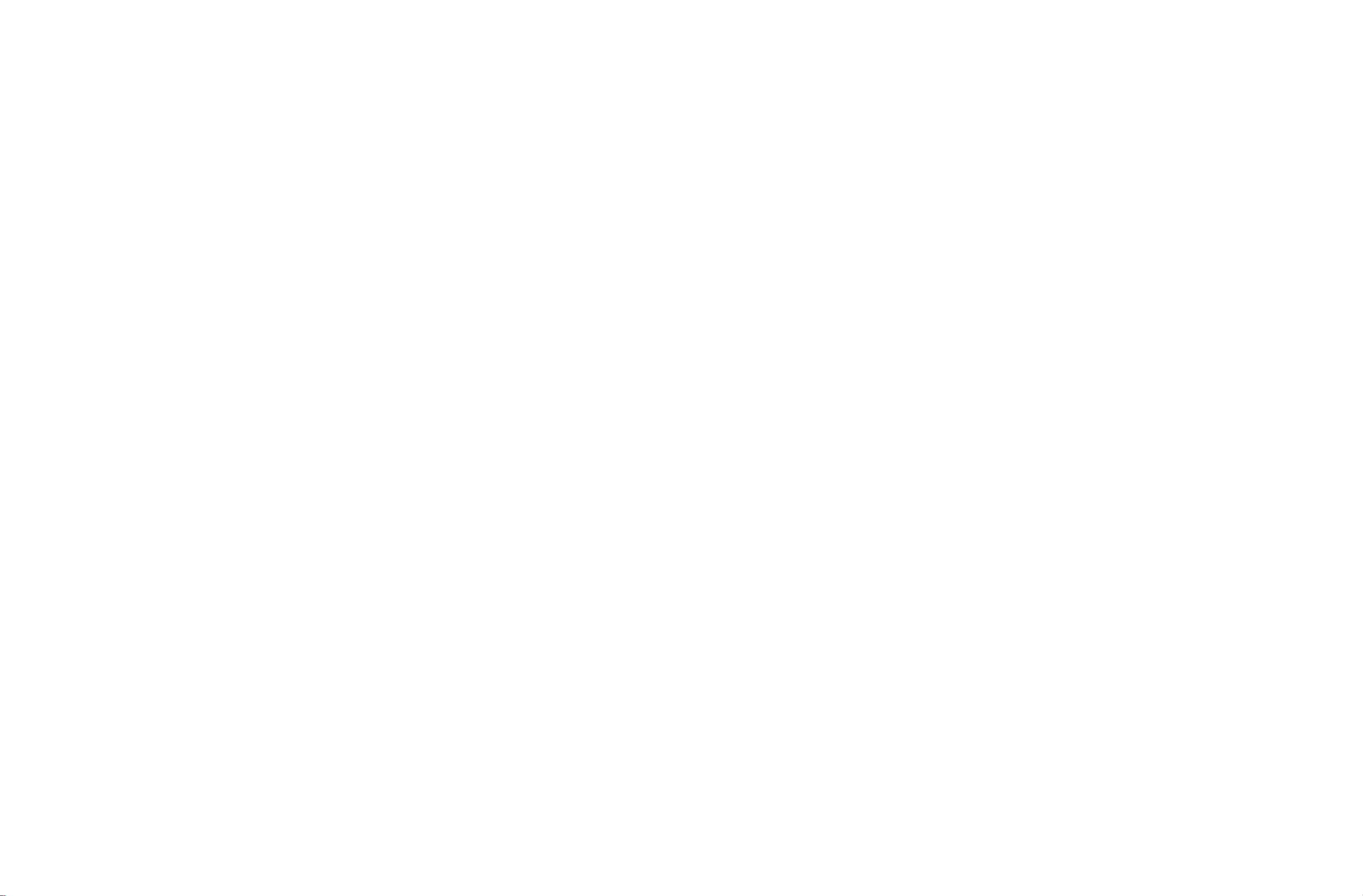
127
Maintenance
Changing Your Security System PIN
To change your PIN, you must have either the key fob or your
existing valid PIN available to gain access to the security
system. If the key fob is not detected or is not available and
you cannot remember your PIN, please see your INDIAN
MOTORCYCLE dealer.
Please read the entire procedure before beginning.
1. Turn the power switch on. Do NOT start the engine. The
security light and/or power switch will turn on briefly
until the key fob is detected or until the valid, current
PIN is entered.
2. Push or hold the turn signal CANCEL switch for 10
seconds until the security light and/or power switch turn
on.
3. Enter either the master PIN or your current 4-digit rider
PIN within 20 seconds. If the PIN is successfully entered,
the security light and/or power switch will remain on
and the horn will sound briefly.
Tip: If the valid PIN is not entered within 20 seconds, the security
light and/or power switch will flash for 10 seconds, then the
system will shut down. Return to step 1 to try again.
Entering Your New Rider PIN
4. Enter a new 4-digit security PIN of your own choosing. If
the PIN is successfully entered, the security light and/or
power switch will remain on and the horn will sound
briefly. Proceed to step 5.
Tip: If the 4-digit PIN is NOT successfully entered within 20 seconds,
the security light and/or power switch will flash for 10 seconds,
then the system exits the procedure. Return to step 1 to try
again.
5. Re-enter the new 4-digit PIN. If this entry matches the
first entry, the security light and/or power switch will
turn off and the horn will sound. The new rider PIN has
been saved. Record your new rider PIN on page 5.
Tip: If the second entry is not entered within 20 seconds or does not
match the first entry, the security light and/or power switch will
flash for 10 seconds, then the system exits the procedure. The
new PIN was NOT saved. Continue to use your former valid PIN.
Return to step 1 to try again.
Key Fob Battery Life
Key fob battery life is approximately 1-2 years depending
on fob type and usage patterns. Battery changes
recommended yearly. Multi-Function (Two Button) Key Fob
battery life will decrease with frequent use of the LOCK /
UNLOCK buttons. Key Fob Replacement Battery Part
Number: 4014675 or CR2032
Low Battery Indicators:
• Decreased fob authentication range
• Horn honks 5 seconds after startup
• Security light stay illuminated for up to 20 seconds
• Both Battery Light and Security Light are illuminated
Key Fob performance can be affected by the following
conditions:
• Close proximity of ferrous materials (e.g. money clip)
• Key Fob stuck to saddlebag speaker magnet
• Key Fob held in ferrous container (e.g. metal cup holder)
• Cold Temp. (Key Fob should be kept above 45° F (7° C)
Specyfikacje produktu
Marka: | Indian |
Kategoria: | Silnik |
Model: | Springfield (2016) |
Potrzebujesz pomocy?
Jeśli potrzebujesz pomocy z Indian Springfield (2016), zadaj pytanie poniżej, a inni użytkownicy Ci odpowiedzą
Instrukcje Silnik Indian

6 Października 2024

29 Września 2024

29 Września 2024

29 Września 2024

29 Września 2024

22 Września 2024

20 Września 2024

20 Września 2024

20 Września 2024

20 Września 2024
Instrukcje Silnik
- Silnik Yamaha
- Silnik Triumph
- Silnik Kawasaki
- Silnik Honda
- Silnik Milwaukee
- Silnik KTM
- Silnik Ducati
- Silnik BMW
- Silnik GasGas
- Silnik Suzuki
- Silnik Husqvarna
- Silnik Aprilia
- Silnik Mercedes-Benz
- Silnik Danfoss
- Silnik Texas
- Silnik ELAC
- Silnik Kettler
- Silnik Mitsubishi
- Silnik Piaggio
- Silnik Reebok
- Silnik Juki
- Silnik Beta
- Silnik Bajaj
- Silnik Royal Enfield
- Silnik Sherco
- Silnik Hyosung
- Silnik Benelli
- Silnik Cagiva
- Silnik Metabo
- Silnik Nautilus
- Silnik Mash
- Silnik Hero
- Silnik Victory
- Silnik Emco
- Silnik Chang Jiang
- Silnik Harley Davidson
- Silnik Moto Guzzi
- Silnik Derbi
- Silnik SMC
- Silnik Ridley
- Silnik Anova
- Silnik Zero
- Silnik MV Agusta
- Silnik BodyCraft
- Silnik Mahindra
- Silnik CRRCpro
Najnowsze instrukcje dla Silnik

1 Marca 2025
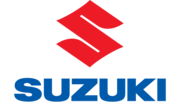
21 Lutego 2025
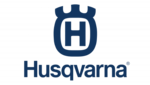
17 Lutego 2025
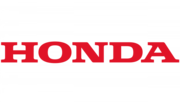
16 Lutego 2025

14 Lutego 2025
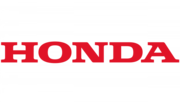
8 Lutego 2025
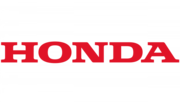
8 Lutego 2025
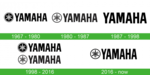
2 Lutego 2025
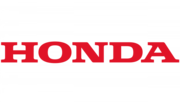
2 Lutego 2025
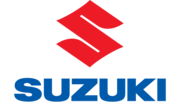
15 Stycznia 2025