Instrukcja obsługi Fibaro Roller Shutter FGRM-222
Fibaro
Niesklasyfikowane
Roller Shutter FGRM-222
Przeczytaj poniżej 📖 instrukcję obsługi w języku polskim dla Fibaro Roller Shutter FGRM-222 (2 stron) w kategorii Niesklasyfikowane. Ta instrukcja była pomocna dla 14 osób i została oceniona przez 2 użytkowników na średnio 4.5 gwiazdek
Strona 1/2
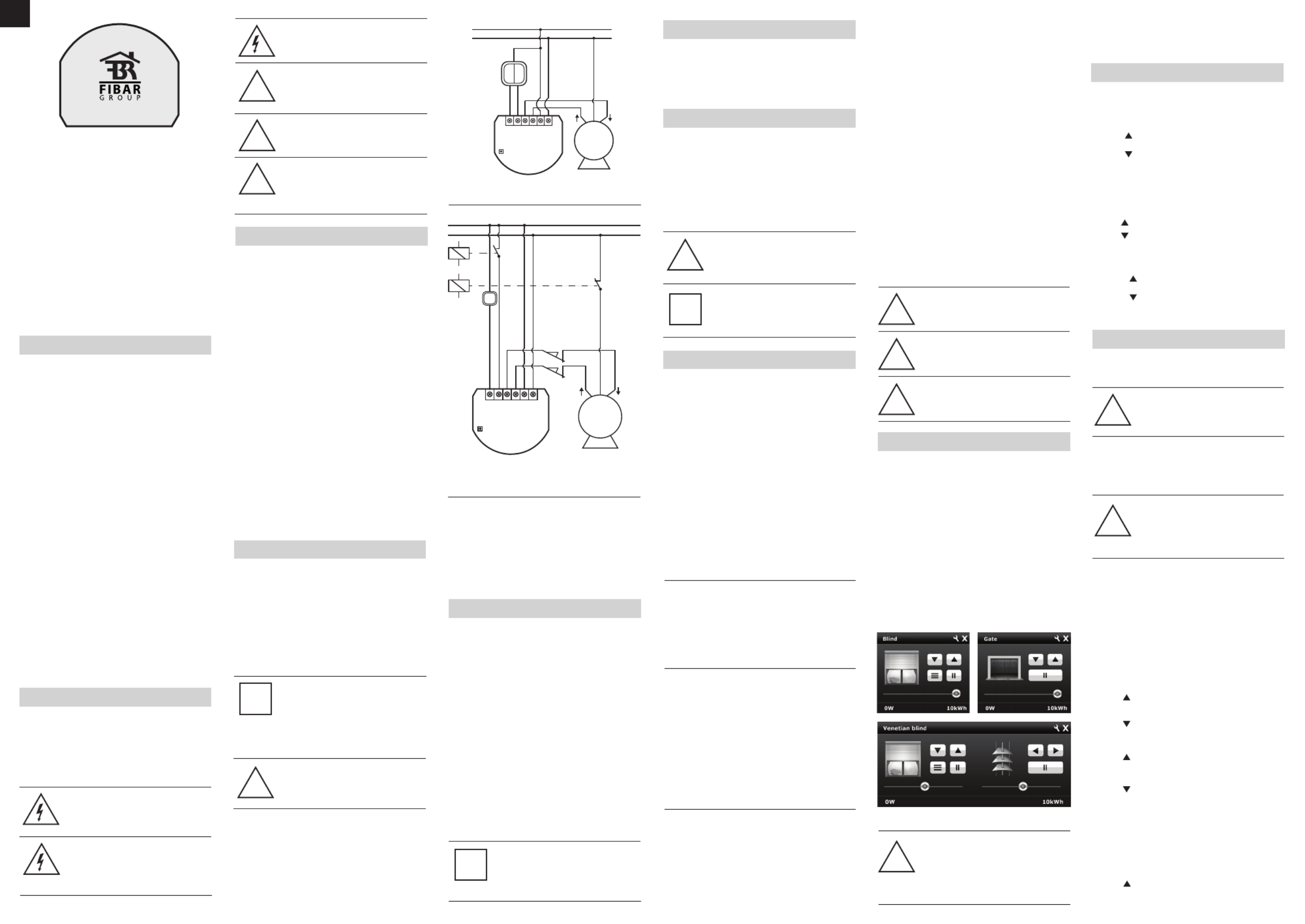
ENG
Fibaro Roller Shutter is a universal, Z-Wave compatible, electric
motor controller. The device allows for controlling motors of roller
blinds, awnings, venetian blinds, gates and others, which are single
phase AC powered. Fibaro Roller Shutter allows for precise
positioning of a roller blind or venetian blind lamellas. Precise
positioning is available for the motors equipped with mechanic and
electronic end switches.
The module may be controlled wirelessly, through the Z-Wave
network main controller, or through the switch keys connected to it.
It’s also possible to combine few devices into groups of devices,
which then can be controlled simultaneously. In addition, Fibaro
Roller Shutter is equipped with Power Metering.
SPECIFICATIONS
Power Supply
Supplied motor type
Supported limit switches type
Power of supplied motor
In accordance
with EU standards
Circuit Temperature limit
Operational Temperature
For installation in boxes
Radio protocol
Radio Frequency
Radio signal power
Range
Dimensions (L x W x H)
Electricity consumption
110 - 230 V ±10% 50/60Hz
Single phase, VAC
Electronic and mechanic
up to 1kW for 230V
up to 500W for 110V
LVD (2006/95/EC)
EMC (2004/10B/EC)
R&TTE(1999/5/EC)
105 °C
0 - 40 °C
Ø ≥ 50mm
Z-Wave
868,4 MHz EU;
908,4 MHz US;
921,4 MHz ANZ;
869,2 MHz RU;
1mW
up to 100m outdoors
up to 30m indoors
(depending on building materials
used)
42 x 37 x 17 mm
< 0,8W
TECHNICAL INFORMATION
• Controlled by Fibaro System devices or any Z-Wave controller
• Microprocessor control
• Executive elements: relays
• The device may be operated by momentary or toggle switches,
and by dedicated roller blind control switches
• Connected motor’s current and historical power consumption
measured
WARNING
Danger of electrocution! Any work on the device
regarding electrical connections may be performed
only after the power supply has been
disconnected.
OPERATING MANUAL
FIBARO ROLLER SHUTTER
FGRM-222-EN-A-v1.00
I. GENERAL INFORMATION ABOUT FIBARO SYSTEM
Fibaro is a wireless system, based on Z-Wave technology. Fibaro
provides many advantages when compared to similar systems. In
general, radio systems create a direct connection between the
receiver and transmitter. However, a radio signal is weakened by
various obstacles located in its path (apartment walls, furniture,
etc.) and in extreme cases it fails to transfer required data. The
advantage of Fibaro System is that its devices, apart from being
transmitters and signal receivers, also duplicate signal. When a
direct connection path between the transmitter and the receiver
cannot be established, the connection may be achieved through
other intermediate devices.
Fibaro is a bi-directional wireless system. This means that the
signal is not only sent to the receivers but also the receivers send
the confirmation of its reception. This operation confirms their
status, which checks whether they are active or not. Safety of the
Fibaro System transmission is comparable to the safety of
transmission in data bus wired systems.
Fibaro operates in the free bandwidth for data transmission. The
frequency depends on radio regulations in individual countries.
Each Fibaro network has its own unique network identification
number (home ID), which is why it is possible to co-operate two or
more independent systems in a single building without any
interference.
Although Z-Wave is quite a new technology, it has already become
recognized and officially a binding standard, similarly to Wi-Fi.
Many manufacturers in various industries offer solutions based on
Z-Wave technology, guaranteeing their compatibility. This means
that the system is open and it may be extended in the future. Find
more information at www.fibaro.com.
Fibaro generates a dynamic network structure. After Fibaro System
is switched on, the location of its individual components is
automatically updated in real-time through status confirmation
signals received from devices operating in a "mesh" network.
II. ROLLER SHUTTER INSTALLATION
1. Before installation make sure the voltage supply is
disconnected.
2. Connect the Roller Shutter in accordance with the wiring
diagram presented on Fig. 1 (roller blinds, venetian blinds) or
Fig. 2 (gates).
3. Place the device in a switch box.
4. Arrange the antenna (tips presented below Fig.2)
5. Turn on the power supply keeping the necessary safety
precautions.
6. Include the module into the Z-Wave network, observing pt. III
description.
7. If necessary, calibrate the module, observing pt. VI descripion.
NOTES FOR THE DIAGRAM:
L - terminal for live lead
N - terminal for neutral lead
S1 - terminal for key no. 1 (has the option of entering the device in
learning mode)
S2 - terminal for key No. 2
O1 - output terminal no. 1 for shutter motor
O2 - output terminal no. 2 for shutter motor
B - service button (used to add or remove a device from the
system)
ROLLER BLIND POSITIONING CALIBRATION
TIPS FOR ARRANGING THE ANTENNA
1. Locate the antenna as far from metal elements as possible
(connection wires, bracket rings, etc.) in order to prevent
interferences.
2. Metal surfaces in direct vicinity of the antenna (e.g. metal switch
boxes, door frames) may impair radio signal reception!
3. Do not cut or shorten the antenna. Its length is perfectly
matched to the band in which the system operates.
NOTE
A push button connected to S1 terminal operates
the O1 output, while the push button connected to
S2 terminal operates the O2 output. It’s recommen-
ded to connect an UP button to S1 terminal and a
wire, responsible of up movement, to O1 output
terminal. Respectively, a DOWN button should be
connected to S2 terminal and a wire, responsible
for down movement, to O2 output terminal.
i
WARNING
Fibaro Roller Shutter is dedicated to operate with
AC powered electric motors. Connecting the device
directly to DC powered motors may result in them
being damaged.
Fig. 3 Roller Shutter icons in Home Center interface
WARNING
Danger of electrocution! Even when the device is
turned off, voltage may be present at it’s terminals.
Any work on the device regarding electrical
connections may be performed only after the
power supply has been disconnected.
WARNING
Any maintenance work on controlled devices may
be performed only after the power supply has been
disconnected.
WARNING
It’s not recommended to operate all of the roller
blinds simultaneously. For safety reasons, at least
one roller blind should be controlled independently,
providing safe escape route in case of emergency.
WARNING
Do not connect the device to loads exceeding
recommended value.
Fig. 1 Roller Shutter wiring diagram
III. Z-WAVE NETWORK INCLUSION
Fibaro Roller Shutter may be included into the Z-Wave network via
the B-button or a push button connected to the S1 terminal. In
addition, the module may be included in auto inclusion mode, by
simply connecting the power supply.
Automatic Z-Wave network inclusion:
1) Make sure the power supply is disconnected and a Roller Shutter
is located within a direct Z-Wave network’s main controller
communication range.
2) Set the main controller into the learn mode (see main controllers
operating manual).
3) Connect the power supply to include the Roller Shutter in auto
inclusion mode.
4) Fibaro Roller Shutter will be automatically detected and included
into the Z-Wave network.
To disable the auto inclusion mode, press the B-button briefly, after
connecting the module to the power supply.
Manual Z-Wave network inclusion:
1) Connect the power supply.
2) Set the main controller into the learn mode (see main controllers
operating manual).
3) Triple click the B-button or a push button connected to the S1
terminal.
4) Fibaro Roller Shutter will be detected and included into the
Z-Wave network.
IV. Z-WAVE NETWORK EXCLUSION
Excluding Fibaro Roller Shutter from the Z-Wave network:
1) Make sure the module is connected to the power supply.
2) Set the main controller into the learn mode (see main controllers
operating manual).
3) Triple click the B-button or a push button connected to the S1
terminal.
V. ROLLER SHUTTER RESET
Reset procedure clears the modules’ EPROM memory, including all
information about the Z-Wave network controller, calibration and
power consumption data.
1) Make sure the module is connected to the power supply.
2) Press and hold the B-button for ca. 14 seconds.
3) LED indicator will glow yellow.
4) Release the B-button and press it again, briefly.
5) The Roller Shutter memory is now empty.
6) The module goes into the auto inclusion mode, until any button
is pushed.
NOTE
Memory reset does not remove the module from
the Z-Wave network main controller’s memory.
Prior to memory reset it’s recommended to exclude
the module from the Z-Wave network.
TIP
After memory reset, the Roller Shutter goes into the
auto inclusion mode and waits to be included into
the Z-Wave network. To exit the auto inclusion
mode press the B-button briefly.
i
Fig. 2 Connecting Roller Shutter to GATE motor
VI. POSITIONING CALIBRATION
Calibration is a process during which a Roller Shutter learns the
position of the limit switches and a motor characteristic. Calibration
is mandatory in order for the Roller Shutter to correctly recognize a
roller blind position. The procedure consists of an automatic, full
movement between the limit switches (up, down, and up again).
There are separate procedures of calibrating roller blind and
lamellas (venetian blind) positioning. Each time the calibration
requires the completion of a full cycle (up and down).
There are 5 procedures of calibrating a Fibaro Roller Shutter to
choose from. Each one gives the same results and the user may
choose which one to execute.
A. Calibration through a Fibaro Home Center 2 interface
1) Make sure the module is connected to the power supply,
according to Fig.1
2) Include the module into the Z-Wave network, according to
section
III of instructions.
3) In Home Center 2 interface choose Fibaro Roller Shutter’s
advanced settings.
4) Click CALIBRATE buttin in the devices advanced settings tab.
5) Roller Shutter performs the calibration process, completing full
cycle - up, down and up again.
6) Using an interface test whether the positioning works correctly.
B. Calibration through the Z-Wave network
1) Make sure the module is connected to the power supply,
according to Fig.1
2) Include the module into the Z-Wave network, according to pt.III
instructions.
3) Set the parameter 29 value to 1.
4) Roller Shutter performs the calibration process, completing full
cycle - up, down and up again.
5) The parameter 29 value will be automatically set to 0.
6) Using an interface test whether the positioning works correctly.
C. Calibration through the switch keys
1) Make sure the module is connected to the power supply,
according to Fig.1, and to the switch keys as well (S1 and S2
inputs).
2) Include the module into the Z-Wave network, according to
section
III of instructions.
3) Press and hold the switch key connected to S1 or S2 input
terminal and release it after at least 3 seconds.
4) Press and hold the same switch key again, and release it after 3
seconds.
5) Now press and hold the same button, for 3 seconds, for the 3rd
time.
6) After pressing and releasing the button for the third time,
automatic calibration sequence will start.
7) Roller Shutter performs the calibration process, completing full
cycle - up, down and up again.
D. Calibration through Menu (B-button)
1) Make sure the module is connected to the power supply,
according to Fig.1
2) Include the module into the Z-Wave network, according to
section
III of instructions.
3) Press and hold the B-button for ca. 6 seconds.
4) LED will glow blue.
5) Release the B-button and press it again, briefly.
6) Roller Shutter performs the calibration process, completing full
cycle - up, down and up again.
CALIBRATING LAMELLAS POSITIONING
IN VENETIAN BLINDS
Apart from calibrating the roller blind position, it’s possible to
calibrate the position of venetian blinds lamellas. After correct
calibration, in case of venetian blinds, it’s possible to set the position
between the limit switches, as well as the lamellas angle. By default,
time of full turn of the lamellas is set to 1,5 seconds. If necessary, it
can be modified following below instructions.
1) Make sure the module is connected to the power supply,
according to Fig.1
2) Include the module into the Z-Wave network, according to section
III of instructions.
3) Calibrate the Roller Shutter, according to the instructions
provided in sections VI.A, VI.B, VI.C, VI.D or VI.E.
4) Set the parameter 10 value to 2 or choose in HC2 interface:
Device Type - Venetian Blind
5) Another device icon, responsible for lamellas operation, will show
up in Home Center 2 interface. In case of any other Z-Wave
network controllers managing the lamellas position is achieved
through pressing and holding a switch key (up or down).
6) By default, time of transition between extreme positions is set to
1 500 ms (1,5 seconds).
7) Turn lamellas between extreme positions. If after full cycle a blind
starts moving up or down, then parameter’s 12 value must be
modified, e.g. to 1 000ms (1 second). Correctly configured
lamellas should not force the blind to move up or down.
NOTE
Roller Shutter needs to be calibrated to work with
any given motor.
NOTE
In Venatian Blind mode, lamellas need to be
calibrated to work with any given motor.
VII. OPERATING THROUGH THE Z-WAVE NETWORK
After including into the Z-Wave network, Fibaro Roller Shutter will
be presented in a Home Center 2 interface as a roller blind icon (see
fig. below). After choosing Venetian Blind device type, a second icon
will show up, responsible for managing lamellas position.
User can choose from the following operating modes:
1. Roller Blind Mode, without positioning
2. Roller Blind Mode, with positioning
3. Venetian Blind Mode
4. Gate Mode, without positioning
5. Gate Mode, with positioning
After choosing one of the above operating modes, device will be
represented in Home Center 2 interface by icons shown in Fig.4. In
addition, each operating mode affects certain parameters settings:
1) Roller blind without positioning (parameter 10 set to 0)
2) Roller blind with positioning (parameter 10 set to 1)
3) Venetian blind (parameter 10 set to 2; parameter 13, set to 2)
4) Gate without positioning (parameter 10 set to 3; parameter 12 set
to 0; parameter 17 set to 0)
5) Gate with positioning (parameter 10 set to 4; parameter 12 set to
0; parameter 17 set to 0)
Opening / Closing a blind is acheved through moving a slider or
pushing a button shown in fig. 3.
In Venetian Blind mode, setting lamellas angle is achieved through
moving a slider or pushing a button shown in fig. 3.
VIII. MANUAL OPERATION
Fibaro Roller Shutter allows for connecting push buttons to S1 and
S2 terminals. These may be momentary or toggle switches,
alternatively. Push buttons are responsible for managing the blind’s
movement.
Using momentary switches:
Clicking button connected to S1 terminal, initiates up
movement.
Clicking button connected to S2 terminal, initiates down
movement.
If the blind is moving, each click, of any button, will stop the
movement. In addition a button click sends a command frame to I-st
association group devices.
In case of venetian blinds, it’s possible to manage the lamellas
angle. Operating Mode - Venetian Blind, or Parameter 10 value set
to 2.
Holding connected to S1 terminal initiates lamellas rotation up.
Holding connected to S2 terminal initiates lamellas rotation
down.
In addition a button hold sends a Fibar Command Class control
frame to II-nd association group devices.
IX. ASSOCIATIONS
Through an association Fibaro Roller Shutter may control another
Z-Wave network device, e.g. another Roller Shutter, Wall Plug,
Dimmer, Relay Switch, RGBW Controller.
NOTE
Association allows for direct communication
between Z-Wave network devices. Main controller
does not take part in such communication.
Fibaro Roller Shutter provides three association groups:
I association group is triggered through a momentary switch click,
or a toggle switch position change.
II association group is triggered through a momentary switch hold
NOTE
II association group is inactive when toggle
switches are used or in Gate Controller mode
(parameter 10). In case of controlling Venetian
Blinds, control commands are sent in Fibar
Command Class standard.
III association group reports the module status. Only one device
may be assigned to this group, main controller by default. It’s not
recommended to modify this group’s settings.
Fibaro Roller Shutter allows for commanding other Roller Shutters,
associated into I or II association group, through clicking or holding
a switch key. For example, this mechanism allows for operating a
Roller Shutter connected to the switch with a button click, and
operating the devices associated in II association group by a button
hold. In addition, when operating Venetian Blinds, it’s possible to
synchronize many devices.
USING ASSOCIATIONS TO OPERATE ANOTHER
ROLLER SHUTTER OR ANY OTHER Z-WAVE
DEVICE.
I ASSOCIATION GROUP:
Clicking button, connected to S1 terminal will initiate up
movement in associated Roller Shutters, or send Turn On command
frame to the devices associated in I-st association group.
Clicking button, connected to S2 terminal will initiate down
movement in associated Roller Shutters, or send Turn Off command
frame to the devices associated in I-st association group.
II ASSOCIATION GROUP:
Holding button , connected to S1 terminal will move the
connected roller blind up, and after 1 second delay initiate up
movement in associated Roller Shutters, or send Turn On command
frame to the devices associated in II-nd association group.
Holding button, connected to S2 terminal will move the
conected rolled blind down, and after 1 second delay initiate down
movement in associated Roller Shutters, or send Turn Off command
frame to the devices associated in II-nd association group.
NOTE
To abort the calibration process press any key
(connected to S1 or S2) or send a STOP control
frame through the Z-Wave network controller. In
Gate Controller mode the calibration process will
be aborted after disconnecting the S2 terminal.
i
Using toggle switches:
Changing switch key position, connected to S1 terminal,
initiates up movement.
Changing switch key position, connected to S2 terminal,
initiates down movement.
Choosing a middle position stops the blind.
!
!
!
!
!
!
!
!
NOTE
Venetian blind lamellas may be only operated by
momentary switches.
!
NOTE
Above operating modes and their default settings
are modified automatically only in Home Center 2
controller. In case of the Z-Wave network
controllers from other manufacturers, these
settings need to be manually adjusted (see section
XV).
!
L NS1 S2
L
N
M
N
O2 O1
safety switch
NC
sensor
NC
Fibaro Roller
Shutter
B
limit
switches
E. Calibration through a Fibar Command Class control frame.
It’s possible to force the calibration process execution through
sending a Fibar Command Class control frame through a Z-Wave
network main controller (see a Fibar Command Class documenta-
tion).
WARNING
It is recomended to monitor regulary operation of
Fibaro Roller shutter in all modes. In case of gate
control mode device, motor limit switches, infrared
barriers and emergency stop should be monitored
and maintained regulary
!
USING ASSOCIATIONS TO OPERATE ROLLER
SHUTTERS CONNECTED TO VENETIAN BLINDS.
Using association mechanism to operating venetian blinds requires
configuring both, I-st and II-nd association groups.
I ASSOCIATION GROUP
Clicking button, connected to S1 terminal will initiate up
movement of the connected venetian blind and other devices
associated in I-st association group.
Fibaro Roller
Shutter
L NS1 S2
L
N
M
N
O2
B
O1

Clicking button, connected to S2 terminal will initiate down
movement of the connected venetian blind and other devices
associated in I-st association group.
II ASSOCIATION GROUP (relevant for momentary switches only)
Holding button, connected to S1 terminal will initiate lamellas
rotation up, of the connected venetian blind as well as the other
devices associated in II-nd association group.
Holding button, connected to S2 terminal will initiate lamellas
rotation down, of the connected venetian blind as well as the other
devices associated in II-nd association group.
NOTE
Once the associated devices are already moving,
they will be stopped if any of the buttons is pressed
and held.
NOTE
In Gate Mode, by default, the S1 terminal is set to
operate with a momentary switch, ignoring the
parameter 14 settings.
Full opening the gate initiates a Roller Shutter COUNTDOWN.
After the COUNTDOWN the gate will start closing. COUNTDOWN
length is set through the parameter 12. In addition, if the IR barrier
is cut (S2 contact opened) at the gate fully open, the gate will start
closing after a time period specified in parameter 17.
NOTE
In both Gate Modes, with and without positioning,
parameters 12 and 17 are automatically set to 0. At
these settings the gate will open, but will not
automatically close. Relevant times need to be set
manually in parameters 12 and 17 (see section
XV).
XI. LED INDICATOR
Fibaro Roller Shutter has a MENU. Each MENU level is signaled
through a LED Indicator colour. To enter MENU press and hold the
B-button for at least 2 seconds.
While the B-button is being held, LED Indicator colours will change
in the following sequence:
XII. Z-WAVE RANGE TESTER
Fibaro Roller Shutter has a built in mechanism, allowing to roughly
estimate the Z-Wave network range.
NOTE
To allow for the Z-Wave network range test, the
Z-Wave network controller needs to support the
functionality and the module needs to be included
in the network. Z-Wave range test puts heavy strain
on the network, so it’s recommended to use the
function only in special cases.
In order to test the Z-Wave network range:
1) Press and hold the B-button for ca. 6 seconds, until the LED
Indicator glows violet.
2) Release the B-button.
3) Click the B-button.
4) LED Indicator will signal the Z-Wave network range (see
description below).
5) Click the B-button to exit the Range Tester.
Network range signaling modes:
Z-Wave network range is signaled by LED illumination colour and
behaviour. Blinking each 1-second means the modules tries to
establish a direct communication with the main controller, while 2
seconds glowing means the test result. The test is performed in a
loop, until being stopped by the user. Z-Wave range test is
performed in three steps, signaled with green, yellow, violet and
red:
1) Blinking in GREEN means the module tries to establish a direct
communication with the main controller. Positive test result is
signaled by a 2 second glowing in GREEN, after which the test is
repeated (step 1). In practice, if the module is able to establish a
direct communication with the main controller, the LED will glow
GREEN, without blinking.
2) If the module is not able to establish a direct connection with the
main controller, it will try to establish a routed connection, through
another, intermediary, Z-Wave network devices. LED indicator will
change the illumination colour to RED. Positive test result is
signaled with glowing in YELLOW. After 2 seconds the module will
retry establishing a direct communication (step 1).
NOTE
The module may modify the main controller
communication from direct to routed and vice
versa, especially if it’s located at the direct
communication range limit.
i
3) If the module is not able to establish a routed connection with the
main controller, LED Indicator colour will change from YELLOW to
VIOLET. After few seconds test will end and the LED Indicator will
glow RED for two seconds. Whole procedure will start again and
the module will try to establish a direct connection with the main
controller (step 1).
XIII. CURRENT AND HISTORICAL
POWER CONSUMPTION MEASURING
Fibaro Roller Shutter allows for the current load and power
consumption monitoring. Data is sent to the main controller, e.g.
Home Center 2.
Measuring is carried out by an independent microprocessor
dedicated exclusively for the purpose, assuring maximum accuracy
and precision. The microprocessor is factory calibrated.
Electric power - power consumed by an electric device in an
instant, in Watts (W).
Electric energy - energy consumed by a device through a time
period. Most commonly measured in kilowatt-hours (kWh). One
kilowatt-hour is equal to one kilowatt of power consumed over a
period of one hour, 1kWh = 1000 Wh.
RESETTING ELECTRICITY CONSUMPTION MEMORY
Fibaro Roller Shutters electricity consumption memory may be
cleared in one of the following ways:
1) Through the module reset (see pt. )
2) Through the main controller menu (see main controllers
operating manual
3) Manually using the following instructions:
a) Make sure the device is connected to voltage supply.
b) Press and hold the B-button for ca. 10 seconds, until LED I
ndicator glows GREEN.
c) Release the B-button.
d) Click the B-button.
e) Energy consumption memory has been erased.
NOTE
1) Please contact your local supplier for the current
rates
2) Fibaro Roller Shutter stores consumed electricity
data on its memory, which means disconnecting
the module from voltage supply does not erase the
data.
XIV. PROTECTION MODE
Fibaro Roller Shutter uses the Protection Command Class v2 to
prevent from unintended motor movement. 22.22 software version
supports the following operation modes (following the Z-Wave
protocol description).
1) Local Protection
Local Protection State:
0 - no protection. Roller Shutter responds to push buttons.
1 - not supported
2 - Local protection active. Roller Shutter does not respond to
push buttons.
Once the Local Protection is activated, the module stops
responding to S1 and S2 push buttons. SCENE ID and association
commands will not be sent as well. The only exception is the
B-button. Menu and Z-Wave network inclusion, after the B-button
or S1 push button triple click, are still active.
NOTE
There’s one more exception in Local Protection. In
Gate Mode, S2 (IR Barrier) is still active. It means if
the obstacle is detected, the gate will stop,
regardless the Local Protection State set.
2) RF Protection (radio protection)
RF Protection State:
0 – No protection. Roller Shutter responds to command frames.
1 - RF Protection active. Roller Shutter does not respond to the
Z-Wave control frames.
2 - not supported.
Once the RF Protection is activated, the module stops responding
to command frames setting the blind position. It’s still possible
however to configure the device (advanced configuration
parameters, protection modes) and checking it’s current state
through polling (position, power, energy).
XV. ADVANCED CONFIGURATION
GENERAL SETTINGS:
3. Reports type
0 – Blind position reports sent to the main controller using Z-Wave
Command Class.
1 - Blind position reports sent to the main controller using Fibar
Command Class.
Parameters value shoud be set to 1 if the module operates in
Venetian Blind mode.
Defauld setting: 0
Parameter size: 1 [byte]
NOTE
To make sure whether Fibar Command Class is
supported by Z-Wave network main controllers
from other manufacturers, please contact the
controllers manufacturer.
10. Roller Shutter operating modes:
0 - Roller Blind Mode, without positioning
1 - Roller Blind Mode, with positioning
2 - Venetian Blind Mode, with positioning
3 - Gate Mode, without positioning
4 - Gate Mode, with positioning
Default settng: 1
Parameter size: [byte]1
12. In Venetian Blind mode (parameter 10 set to 2) the
parameter determines time of full turn of the lamellas.
In Gate Mode (parameter 10 set to 3 or 4) the parameter defines
the COUNTDOWN time, i.e. the time period after which an open
gate starts closing. In any other operating mode the parameter
value is irrelevant.
Value of 0 means the gate will not close automatically.
Available settings: (0 - 655,35s) 0-65535
Default setting: (1,5 s)150
Parameter size: 2 [bytes]
13. Set lamellas back to previous position.
In Venetian Blind Mode (parameter 10 set to 2) the parameter
influences lamellas positioning in various situations. In any other
operating mode the parameter value is irrelevant.
0 - Lamellas return to previously set position only in case of the
main controller operation.
1 - Lamellas return to previously set position in case of the main
controller operation, momentary switch operation, or when the
limit switch is reached.
2 - Lamellas return to previously set position in case of the main
controller operation, momentary switch operation, when the limit
switch is reached or after receiving a “STOP” control frame
(Switch Multilevel Stop).
Default setting: 1
Parameter size: 1 [byte]
14. Switch type.
The parameter settings are relevant for Roller Blind Mode and
Venetian Blind Mode (parameter 10 set to 0, 1, 2).
0 - Momentary switches
1 - Toggle switches
2 - Single, momentary switch. (The switch should be connected to
S1 terminal)
Default setting: 0
Parameter size: 1 [byte]
17. In Roller Blind Mode or Venetian Blind mode (parameter 10
set to 0, 1, 2) the parameter determines when the Roller
Shutter relays are turned off after reaching a limit switch.
In Gate Mode (parameter 10 set to 3 or 4) the parameter
determines a time period after which a gate will start closing after a
S2 contact has been disconnected. In this mode, time to turn off the
Roller Shutter relays after reaching a limit switch is set to 3 seconds
and cannot be modified.
Value of 0 means the gate will note close automatically.
Available settings: (0,1-25,5s).0 - 255
Default setting: (1s).10
Parameter size: 1 [byte]
18. Motor operation detection.
Power threshold to be interpreted as reaching a limit switch.
Available settings: (1-255 W)0 - 255
The value of 0 means reaching a limit switch will not be detected
Default setting: (10W).10
Parameter size: 1 [byte]
22. Motor operation time.
Time period for the motor to continue operation.
Available settings: (0 – 65535s)0 – 65535
The value of 0 means the function is disabled.
Default setting: (240s. – 4 minutes)240
Parameter size: 2 [bytes]
29. Forced Roller Shutter calibration.
By modifying the parameters setting from 0 to 1 a Roller Shutter
enters the calibration mode. The parameter relevant only if a Roller
Shutter is set to work in positioning mode (parameter 10 set to 1, 2
or 4).
1 - Start calibration process
Default setting: 0
Parameter size: 1 [byte]
ALARM SETTINGS:
30. Response to general alarm
0 - No reaction.
1 - Open blind.
2 - Close blind.
Default setting: 2
Parameter size: 1 [byte]
31. Response to flooding alarm
0 - No reaction.
1 - Open blind.
2 - Close blind.
Default setting: 0
Parameter size: 1 [byte]
32. Response to smoke, CO or CO2 alarm
0 - No reaction.
1 - Open blind.
2 - Close blind.
Default setting: 1
Parameter size: 1 [byte]
33. Response to temperature alarm
0 - No reaction.
1 - Open blind.
2 - Close blind.
Default setting: 1
Parameter size: 1 [byte]
35. Managing lamellas in response to alarm.
In Venetian Blind Mode (parameter 10 set to 2), the parameter
determines how the lamellas will react upon alarm detection. In any
other modes, the parameter value is not relevant.
0 - Do not change lamellas position - lamellas return to the last set
position.
1 - Set lamellas to their extreme position.
Default setting: 1
Parameter size: 1 [byte]
POWER AND ENERGY REPORTS SETTINGS:
40. Power reports.
Power level change that will result in new power value report being
sent. The parameter defines a change that needs to occur in order
to trigger the report. The value is a percentage of the previous
report.
Power report threshold available settings: (1-100%). 1-100
Value of 0 means the reports are turned off.
Default setting: (10%).10
Parameter size: 1 [byte]
42. Periodic power or energy reports.
The parameter defines a time period between consecutive reports.
Available settings: (1-65534 seconds)1-65534
Value of means the reports are turned off.0
Default setting: (3600 seconds / 60 minutes).3600
Parameter size: 2 [bytes]
43. Energy reports.
Energy level change which will result in new energy value report
being sent. The parameter defines a change that needs to occur in
order to trigger the report.
Energy threshold available settings: (0,01 - 2,54kWh).1-254
Value of means the reports are turned off.0
Default setting (0,1kWh).10
Parameter size: 1 [byte]
44. Self-measurement.
A Roller Shutter may include power and energy used by itself in
reports sent to the main controller.
0 - Self-measurement inactive.
1 - Self-measurement active.
!
!
!
!
!
!
!
IX. OPERATING GATE MOTORS
Fibaro Roller Shutter allows for operating gate motors. Gate motor
should be connected to O1 and O2 terminals according to Fig.2. In
the Gate Mode, a momentary switch may be connected to S1
terminal. It’s recommended to connect an IR barrier, an emergency
stop button or any alarm mechanism to S2 terminal. Opening a
contact in a device connected to S2 terminal will always result in
stopping a motor in current position (see Fig. 2).
Clicking a push button connected to S1 terminal will initiate opening
the gate. Next click of a button will stop the gate. Yet another click of
a button will close the gate. According to following seaquence:
OPEN → STOP → CLOSE → STOP → OPEN.
1. The Guarantee is provided by FIBAR GROUP Sp. z o.o.
(hereinafter "Manufacturer"), based in Poznan, ul. Lotnicza 1; 60-421
Poznan, entered in the register of the National Court Register kept
by the District Court in Poznań, VIII Economic Department of the
National Court Register, no. 370151, NIP 7811858097, REGON:
301595664.
2. The Manufacturer is responsible for equipment malfunction
resulting from physical defects (manufacturing or material) of the
Device for 12 months from the date of its purchasing.
3. During the Guarantee period, the Manufacturer shall remove any
defects, free of charge, by repairing or replacing (at the sole
discretion of the Manufacturer) any defective components of the
Device with new or regenerated components, that are free of
defects. When the repair impossible, the Manufacturer reserves the
right to replace the device with a new or regenerated one, which shall
be free of any defects and its condition shall not be worse than the
original device owned by the Customer.
4. In special cases, when the device cannot be replaced with the
device of the same type (e.g. the device is no longer available in the
commercial offer), the Manufacturer may replace it with a different
device having technical parameters similar to the faulty one. Such
activity shall be considered as fulfilling the obligations of the
Manufacturer. The Manufacturer shall not refund money paid for the
device.
5. The holder of a valid guarantee shall submit a guarantee claim
through the guarantee service. Remember: before you submit a
guarantee claim, contact our technical support using telephone or
e-mail. More than 50% of operational problems is resolved remotely,
saving time and money spent to initiating guarantee procedure. If
remote support is insufficient, the Customer shall fill the guarantee
claim form (using our website - www.fibargroup.com) in order to
obtain claim authorization.
When the guarantee claim form is submitted correctly, the Customer
shall receive the claim confirmation with an unique number (Return
Merchandise Authorization -RMA).
6. The claim may be also submitted by telephone. In this case, the
call is recorded and the Customer shall be informed about it by a
consultant before submitting the claim. Immediately after submitting
the claim, the consultant shall provide the Customer with the claim
number (RMA-number).
7. When the guarantee claim form is submitted correctly, a
representative of the Authorised Guarantee Service (hereinafter as
"AGS") shall contact the Customer.
8. Defects revealed within the guarantee period shall be removed
not later than 30 days from the date of delivering the Device to AGS.
The guarantee period shall be extended by the time in which the
Device was kept by AGS.
9. The faulty device shall be provided by the Customer with complete
standard equipment and documents proving its purchase.
10. Parts replaced under the guarantee are the property of the
Manufacturer. The guarantee for all parts replaced in the guarantee
process shall be equal to the guarantee period of the original device.
The guarantee period of the replaced part shall not be extended.
11. Costs of delivering the faulty device shall be borne by the
Customer. For unjustified service calls, the Service may charge the
Customer with travel expenses and handling costs related to the
case.
12. AGS shall not accept a complaint claim only when:
• the Device was misused or the manual was not observed,
• the Device was provided by the Customer incomplete, without
accessories or nameplate,
• it was determined that the fault was caused by other reasons than
a material or manufacturing defect of the Device
• the guarantee document is not valid or there is no proof of
purchase,
13. The Manufacturer shall not be liable for damages to property
caused by defective device. The Manufacturer shall not be liable for
indirect, incidental, special, consequential or punitive damages, or
for any damages, including, inter alia, loss of profits, savings, data,
loss of benefits, claims by third parties and any property damage or
personal injuries arising from or related to the use of the Device.
14. The guarantee shall not cover:
• mechanical damages (cracks, fractures, cuts, abrasions, physical
deformations caused by impact, falling or dropping the device or
other object, improper use or not observing the operating manual);
• damages resulting from external causes, e.g.: flood, storm, fire,
lightning, natural disasters, earthquakes, war, civil disturbance, force
majeure, unforeseen accidents, theft, water damage, liquid leakage,
battery spill, weather conditions, sunlight, sand, moisture, high or low
temperature, air pollution;
• damages caused by malfunctioning software, attack of a computer
virus, or by failure to update the software as recommended by the
Manufacturer;
• damages resulting from: surges in the power and/or telecommuni-
cation network, improper connection to the grid in a manner
inconsistent with the operating manual, or from connecting other
devices not recommended by the Manufacturer.
• damages caused by operating or storing the device in extremely
adverse conditions, i.e. high humidity, dust, too low (freezing) or too
high ambient temperature. Detailed permissible conditions for
operating the Device are defined in the operating manual;
• damages caused by using accessories not recommended by the
XIV Guarantee
• damages caused by faulty electrical installation of the Customer,
including the use of incorrect fuses;
• damages caused by Customer's failure to provide maintenance and
servicing activities defined in the operating manual;
• damages resulting from the use of spurious spare parts or
accessories improper for given model, repairing and introducing
alterations by unauthorized persons;
• defects caused by operating faulty Device or accessories.
15. The scope of the guarantee repairs shall not include periodic
maintenance and inspections, in particular cleaning, adjustments,
operational checks, correction of errors or parameter programming
and other activities that should be performed by the user (Buyer).
The guarantee shall not cover natural wear and tear of the Device
and its components listed in the operating manual and in technical
documentation as such elements have a defined operational life.
16. If a defect is not covered by the guarantee, the Manufacturer
reserves the right to remove such defect at its sole discretion,
repairing the damaged or destroyed parts or providing components
necessary for repair or replacement.
17. This guarantee shall not exclude, limit or suspend the Customer
rights when the provided product is inconsistent with the purchase
agreement.
This Device may be used with all devices
certified with Z-Wave certificate and should be
compatible with such devices produced by
other manufacturers.
Any device compatible with Z-Wave may be added
to Fibaro system.
i
FIBARGROUP
FIBARO
In case of any technical questions contact customer service centre
in your country.
www.fibargroup.com
Fig. 4 Roller Shutter icon in Home Center interface
NOTE
Parameters 12 and 17 settings are automatically
modified only in Home Center 2 controller, when
choosing one of Gate Modes. In case of controllers
from other manufacturers these parameters need
to be set manually (see section XV).
!
NOTE
Installation of the gate driver may be performed
only by certified professionals. The motor must be
equipped with the appropriate limit switches (see
Fig 2). It’s recommended to connect a NC
(normally closed) contact of an IR barrier to S2
terminal. Opening the contact will stop the gate. In
addition, it’s recommened to connect an
emergency stop button to the motors neutral (N)
wire. In emergency, pushing the emergency stop
button will cut the power and stop the gate. It is
recomended to monitor regulary operation of
Fibaro Roller shutter in all modes. Also it is
recomended to regulary verificate and maintenan-
ce connectors.
!
NOTE
S1 and S2 terminals react to mains voltage only.
Using IR barriers with NC contacts operating on
lower voltages require using an additional relay
(see Fig. 2)
!
Default setting: 0
Parameter size: 1 [byte]
SCENES AND ASSOCIATIONS SETTINGS:
50. Scenes / Associations activation.
Parameter determines whether scenes or associations are
activated by the switch keys.
0 - Associations activation
1 - Scenes activation
Default setting: 0
Parameter size: 1 [byte]
BLUE - Roller Shutter calibration procedure (see pt. )
VIOLET - initiate the Z-Wave network range tester
GREEN - reset energy consumption data memory (see pt. )
YELLOW - Roller Shutter reset (see pt. )
Release the B-button to choose the desired function and confirm
your choice with the B-button click.
WARNING!
In Protection Mode it will not be possible to control
Fibaro Roller Shutter from buttons. It is not
recomended to control all Fibaro Roller Shutters in
this mode.
Specyfikacje produktu
Marka: | Fibaro |
Kategoria: | Niesklasyfikowane |
Model: | Roller Shutter FGRM-222 |
Potrzebujesz pomocy?
Jeśli potrzebujesz pomocy z Fibaro Roller Shutter FGRM-222, zadaj pytanie poniżej, a inni użytkownicy Ci odpowiedzą
Instrukcje Niesklasyfikowane Fibaro

30 Grudnia 2025

18 Września 2024

16 Września 2024

15 Września 2024

14 Września 2024

14 Września 2024

13 Września 2024

13 Września 2024

12 Września 2024

11 Września 2024
Instrukcje Niesklasyfikowane
- Niesklasyfikowane Sony
- Niesklasyfikowane Bauknecht
- Niesklasyfikowane Yamaha
- Niesklasyfikowane Ikea
- Niesklasyfikowane Hoshizaki
- Niesklasyfikowane Samsung
- Niesklasyfikowane Tesy
- Niesklasyfikowane Kindercraft
- Niesklasyfikowane PeakTech
- Niesklasyfikowane Bertazzoni
- Niesklasyfikowane Electrolux
- Niesklasyfikowane Gamdias
- Niesklasyfikowane Tenda
- Niesklasyfikowane AEG
- Niesklasyfikowane Fellowes
- Niesklasyfikowane Balay
- Niesklasyfikowane Leica
- Niesklasyfikowane Beko
- Niesklasyfikowane Teka
- Niesklasyfikowane Sven
- Niesklasyfikowane ChamSys
- Niesklasyfikowane LG
- Niesklasyfikowane Worx
- Niesklasyfikowane Küppersbusch
- Niesklasyfikowane Smeg
- Niesklasyfikowane Motorola
- Niesklasyfikowane Götze & Jensen
- Niesklasyfikowane Dreame
- Niesklasyfikowane Beurer
- Niesklasyfikowane Peugeot
- Niesklasyfikowane Stabo
- Niesklasyfikowane Logitech
- Niesklasyfikowane Gram
- Niesklasyfikowane Sanitas
- Niesklasyfikowane Spektrum
- Niesklasyfikowane Caso
- Niesklasyfikowane Amica
- Niesklasyfikowane Xiaomi
- Niesklasyfikowane Gorenje
- Niesklasyfikowane Etna
- Niesklasyfikowane Joy-It
- Niesklasyfikowane LERAN
- Niesklasyfikowane Lego
- Niesklasyfikowane SHX
- Niesklasyfikowane President
- Niesklasyfikowane MyPhone
- Niesklasyfikowane Sharp
- Niesklasyfikowane BeamZ
- Niesklasyfikowane Huawei
- Niesklasyfikowane Supermicro
- Niesklasyfikowane TCL
- Niesklasyfikowane Braun
- Niesklasyfikowane Russell Hobbs
- Niesklasyfikowane Pioneer
- Niesklasyfikowane Statron
- Niesklasyfikowane Lenovo
- Niesklasyfikowane Tefal
- Niesklasyfikowane Honda
- Niesklasyfikowane TP-Link
- Niesklasyfikowane Voltcraft
- Niesklasyfikowane Milwaukee
- Niesklasyfikowane Philips
- Niesklasyfikowane Livoo
- Niesklasyfikowane Plantronics
- Niesklasyfikowane SilverCrest
- Niesklasyfikowane Endress
- Niesklasyfikowane Dometic
- Niesklasyfikowane Gigabyte
- Niesklasyfikowane Acer
- Niesklasyfikowane Realme
- Niesklasyfikowane Ultimate Speed
- Niesklasyfikowane Technics
- Niesklasyfikowane Stihl
- Niesklasyfikowane Bosch
- Niesklasyfikowane Yato
- Niesklasyfikowane Xblitz
- Niesklasyfikowane Dash
- Niesklasyfikowane Epson
- Niesklasyfikowane JBL
- Niesklasyfikowane Parkside
- Niesklasyfikowane Hikvision
- Niesklasyfikowane Candy
- Niesklasyfikowane GW Instek
- Niesklasyfikowane Maxi-Cosi
- Niesklasyfikowane Onkyo
- Niesklasyfikowane Volkswagen
- Niesklasyfikowane Whirlpool
- Niesklasyfikowane Grillmeister
- Niesklasyfikowane IPGARD
- Niesklasyfikowane Lionelo
- Niesklasyfikowane Fujitsu
- Niesklasyfikowane Ferroli
- Niesklasyfikowane Edision
- Niesklasyfikowane Global
- Niesklasyfikowane Thule
- Niesklasyfikowane Roland
- Niesklasyfikowane Cramer
- Niesklasyfikowane Miele
- Niesklasyfikowane HyperX
- Niesklasyfikowane Stiga
- Niesklasyfikowane Easy Home
- Niesklasyfikowane Hacienda
- Niesklasyfikowane LC-Power
- Niesklasyfikowane Waterco
- Niesklasyfikowane Geemarc
- Niesklasyfikowane Nokia
- Niesklasyfikowane Scott
- Niesklasyfikowane Brentwood
- Niesklasyfikowane Nobo
- Niesklasyfikowane Midea
- Niesklasyfikowane Toolcraft
- Niesklasyfikowane Axkid
- Niesklasyfikowane KEF
- Niesklasyfikowane Festool
- Niesklasyfikowane Kärcher
- Niesklasyfikowane Bose
- Niesklasyfikowane Severin
- Niesklasyfikowane Hisense
- Niesklasyfikowane Berg
- Niesklasyfikowane Infiniton
- Niesklasyfikowane EZVIZ
- Niesklasyfikowane Conceptronic
- Niesklasyfikowane Singer
- Niesklasyfikowane Panasonic
- Niesklasyfikowane StarTech.com
- Niesklasyfikowane Promethean
- Niesklasyfikowane Bavaria By Einhell
- Niesklasyfikowane Theben
- Niesklasyfikowane Klipsch
- Niesklasyfikowane Muse
- Niesklasyfikowane Liebherr
- Niesklasyfikowane Canon
- Niesklasyfikowane Mio
- Niesklasyfikowane Crestron
- Niesklasyfikowane Withings
- Niesklasyfikowane Bestway
- Niesklasyfikowane Viewsonic
- Niesklasyfikowane Behringer
- Niesklasyfikowane Asus
- Niesklasyfikowane Nedis
- Niesklasyfikowane Stanley
- Niesklasyfikowane Nexa
- Niesklasyfikowane Jura
- Niesklasyfikowane AG Neovo
- Niesklasyfikowane Be Cool
- Niesklasyfikowane Allen & Heath
- Niesklasyfikowane Enphase
- Niesklasyfikowane Rossmax
- Niesklasyfikowane IK Multimedia
- Niesklasyfikowane Reolink
- Niesklasyfikowane American DJ
- Niesklasyfikowane Medion
- Niesklasyfikowane Boss
- Niesklasyfikowane Black & Decker
- Niesklasyfikowane OK
- Niesklasyfikowane Lenco
- Niesklasyfikowane TRENDnet
- Niesklasyfikowane Audioline
- Niesklasyfikowane Polar
- Niesklasyfikowane Max Pro
- Niesklasyfikowane Scheppach
- Niesklasyfikowane Fujifilm
- Niesklasyfikowane Proxxon
- Niesklasyfikowane Adler
- Niesklasyfikowane Bluetti
- Niesklasyfikowane BaByliss
- Niesklasyfikowane Marquant
- Niesklasyfikowane Subaru
- Niesklasyfikowane MSI
- Niesklasyfikowane Ford
- Niesklasyfikowane Hoover
- Niesklasyfikowane Toshiba
- Niesklasyfikowane Tesla
- Niesklasyfikowane Deditec
- Niesklasyfikowane Westinghouse
- Niesklasyfikowane D-Link
- Niesklasyfikowane Rinnai
- Niesklasyfikowane Majestic
- Niesklasyfikowane Hendi
- Niesklasyfikowane Quigg
- Niesklasyfikowane Jensen
- Niesklasyfikowane August
- Niesklasyfikowane Niceboy
- Niesklasyfikowane Maytag
- Niesklasyfikowane Hazet
- Niesklasyfikowane Bluebird
- Niesklasyfikowane Vertiv
- Niesklasyfikowane Yealink
- Niesklasyfikowane Domo
- Niesklasyfikowane Conair
- Niesklasyfikowane GE
- Niesklasyfikowane ILive
- Niesklasyfikowane Ardes
- Niesklasyfikowane Taurus
- Niesklasyfikowane VitalMaxx
- Niesklasyfikowane RIKON
- Niesklasyfikowane Ring
- Niesklasyfikowane Orbegozo
- Niesklasyfikowane Native Instruments
- Niesklasyfikowane Garmin
- Niesklasyfikowane Blaupunkt
- Niesklasyfikowane Profoon
- Niesklasyfikowane Brandt
- Niesklasyfikowane Vivax
- Niesklasyfikowane ATen
- Niesklasyfikowane IOptron
- Niesklasyfikowane Grizzly
- Niesklasyfikowane Siemens
- Niesklasyfikowane Teac
- Niesklasyfikowane Speed-Link
- Niesklasyfikowane Gardena
- Niesklasyfikowane Casio
- Niesklasyfikowane Iiyama
- Niesklasyfikowane Lincoln Electric
- Niesklasyfikowane BRITA
- Niesklasyfikowane Metra
- Niesklasyfikowane Thrustmaster
- Niesklasyfikowane Volvo
- Niesklasyfikowane Evolveo
- Niesklasyfikowane Stadler Form
- Niesklasyfikowane Ambiano
- Niesklasyfikowane DeWalt
- Niesklasyfikowane Bbf
- Niesklasyfikowane Danby
- Niesklasyfikowane Martin Logan
- Niesklasyfikowane Dual
- Niesklasyfikowane Einhell
- Niesklasyfikowane Grundig
- Niesklasyfikowane APC
- Niesklasyfikowane Hegel
- Niesklasyfikowane Alcatel
- Niesklasyfikowane Kiloview
- Niesklasyfikowane Suzuki
- Niesklasyfikowane Haier
- Niesklasyfikowane Sigma
- Niesklasyfikowane Homedics
- Niesklasyfikowane Remington
- Niesklasyfikowane Eberle
- Niesklasyfikowane HP
- Niesklasyfikowane KKT Kolbe
- Niesklasyfikowane Cylinda
- Niesklasyfikowane Teltonika
- Niesklasyfikowane S.M.S.L
- Niesklasyfikowane Genesis
- Niesklasyfikowane Jocel
- Niesklasyfikowane Soundmaster
- Niesklasyfikowane Prixton
- Niesklasyfikowane Hyundai
- Niesklasyfikowane Silverline
- Niesklasyfikowane Blomberg
- Niesklasyfikowane Bimar
- Niesklasyfikowane Line 6
- Niesklasyfikowane Rowenta
- Niesklasyfikowane Brother
- Niesklasyfikowane Mesko
- Niesklasyfikowane Master
- Niesklasyfikowane Husqvarna
- Niesklasyfikowane Honeywell
- Niesklasyfikowane DAP-Audio
- Niesklasyfikowane Creative
- Niesklasyfikowane Concept
- Niesklasyfikowane Joie
- Niesklasyfikowane Manhattan
- Niesklasyfikowane Chauvet
- Niesklasyfikowane Strong
- Niesklasyfikowane Cybex
- Niesklasyfikowane Microchip
- Niesklasyfikowane Honor
- Niesklasyfikowane Heritage Audio
- Niesklasyfikowane Fisher & Paykel
- Niesklasyfikowane Cotek
- Niesklasyfikowane Tripp Lite
- Niesklasyfikowane Shure
- Niesklasyfikowane EWON
- Niesklasyfikowane ECG
- Niesklasyfikowane IRobot
- Niesklasyfikowane Indesit
- Niesklasyfikowane Amazfit
- Niesklasyfikowane Steinel
- Niesklasyfikowane Makita
- Niesklasyfikowane Ilve
- Niesklasyfikowane Mikrotik
- Niesklasyfikowane Hecht
- Niesklasyfikowane Denon
- Niesklasyfikowane Akasa
- Niesklasyfikowane Unold
- Niesklasyfikowane Swann
- Niesklasyfikowane Krontaler
- Niesklasyfikowane Truma
- Niesklasyfikowane Kwikset
- Niesklasyfikowane Mercury
- Niesklasyfikowane Empress Effects
- Niesklasyfikowane Carel
- Niesklasyfikowane Petzl
- Niesklasyfikowane Nikon
- Niesklasyfikowane Shimano
- Niesklasyfikowane Viking
- Niesklasyfikowane Antari
- Niesklasyfikowane Medela
- Niesklasyfikowane Block
- Niesklasyfikowane Rapid
- Niesklasyfikowane Ozito
- Niesklasyfikowane Primus
- Niesklasyfikowane Kodak
- Niesklasyfikowane Phoenix Gold
- Niesklasyfikowane Nodor
- Niesklasyfikowane Forza
- Niesklasyfikowane CATA
- Niesklasyfikowane Testo
- Niesklasyfikowane HeiTech
- Niesklasyfikowane Audac
- Niesklasyfikowane Cisco
- Niesklasyfikowane Baby Brezza
- Niesklasyfikowane Primera
- Niesklasyfikowane SBS
- Niesklasyfikowane Draper
- Niesklasyfikowane Cambridge
- Niesklasyfikowane Aim TTi
- Niesklasyfikowane Fuxtec
- Niesklasyfikowane Smart
- Niesklasyfikowane ORNO
- Niesklasyfikowane Fiap
- Niesklasyfikowane Cooler Master
- Niesklasyfikowane Sanus
- Niesklasyfikowane TFA
- Niesklasyfikowane Dyson
- Niesklasyfikowane Chauvin Arnoux
- Niesklasyfikowane Broan
- Niesklasyfikowane Hotpoint
- Niesklasyfikowane Kenwood
- Niesklasyfikowane Scosche
- Niesklasyfikowane Icy Box
- Niesklasyfikowane Sungrow
- Niesklasyfikowane NuPrime
- Niesklasyfikowane Polk
- Niesklasyfikowane Hasbro
- Niesklasyfikowane V-Zug
- Niesklasyfikowane Moxa
- Niesklasyfikowane Deye
- Niesklasyfikowane Trisa
- Niesklasyfikowane DJI
- Niesklasyfikowane RYOBI
- Niesklasyfikowane Synology
- Niesklasyfikowane Godex
- Niesklasyfikowane Kugoo
- Niesklasyfikowane Alpine
- Niesklasyfikowane Wolf Garten
- Niesklasyfikowane Natec
- Niesklasyfikowane Knog
- Niesklasyfikowane Zenit
- Niesklasyfikowane Gembird
- Niesklasyfikowane Scala
- Niesklasyfikowane ZTE
- Niesklasyfikowane Godox
- Niesklasyfikowane Uni-T
- Niesklasyfikowane Røde
- Niesklasyfikowane Ariston Thermo
- Niesklasyfikowane Zelmer
- Niesklasyfikowane Vango
- Niesklasyfikowane Hammersmith
- Niesklasyfikowane Chicco
- Niesklasyfikowane Mestic
- Niesklasyfikowane My Wall
- Niesklasyfikowane Chamberlain
- Niesklasyfikowane Dynaudio
- Niesklasyfikowane Paradigm
- Niesklasyfikowane Paladin
- Niesklasyfikowane Spin Master
- Niesklasyfikowane Lindy
- Niesklasyfikowane Olivetti
- Niesklasyfikowane PKM
- Niesklasyfikowane Ninja
- Niesklasyfikowane Medisana
- Niesklasyfikowane MaxCom
- Niesklasyfikowane Minox
- Niesklasyfikowane Cuisinart
- Niesklasyfikowane Zebra
- Niesklasyfikowane Bang & Olufsen
- Niesklasyfikowane Wilfa
- Niesklasyfikowane DSC
- Niesklasyfikowane Deltaco
- Niesklasyfikowane Cobra
- Niesklasyfikowane Flex
- Niesklasyfikowane JVC
- Niesklasyfikowane ZyXEL
- Niesklasyfikowane Auriol
- Niesklasyfikowane Konig & Meyer
- Niesklasyfikowane Trust
- Niesklasyfikowane V7
- Niesklasyfikowane Thor
- Niesklasyfikowane LogiLink
- Niesklasyfikowane Amana
- Niesklasyfikowane Stokke
- Niesklasyfikowane Memphis Audio
- Niesklasyfikowane Intergas
- Niesklasyfikowane Sandisk
- Niesklasyfikowane Grohe
- Niesklasyfikowane Dell
- Niesklasyfikowane Dacor
- Niesklasyfikowane Polaris
- Niesklasyfikowane Fitbit
- Niesklasyfikowane Axor
- Niesklasyfikowane GLORIA
- Niesklasyfikowane Yard Force
- Niesklasyfikowane IFM
- Niesklasyfikowane Spelsberg
- Niesklasyfikowane Hotpoint Ariston
- Niesklasyfikowane Ctek
- Niesklasyfikowane Krups
- Niesklasyfikowane Datapath
- Niesklasyfikowane Furrion
- Niesklasyfikowane Bialetti
- Niesklasyfikowane Silk'n
- Niesklasyfikowane Bomann
- Niesklasyfikowane U-Line
- Niesklasyfikowane Linksys
- Niesklasyfikowane Clean Air Optima
- Niesklasyfikowane Moulinex
- Niesklasyfikowane Teesa
- Niesklasyfikowane Cleanmaxx
- Niesklasyfikowane Ursus Trotter
- Niesklasyfikowane Ultimate
- Niesklasyfikowane Aprilia
- Niesklasyfikowane PS Audio
- Niesklasyfikowane PowerXL
- Niesklasyfikowane Jamo
- Niesklasyfikowane DEDRA
- Niesklasyfikowane Corsair
- Niesklasyfikowane Emerio
- Niesklasyfikowane Owon
- Niesklasyfikowane Focusrite
- Niesklasyfikowane Wood's
- Niesklasyfikowane Baumr-AG
- Niesklasyfikowane Nuna
- Niesklasyfikowane Google
- Niesklasyfikowane Create
- Niesklasyfikowane Rega
- Niesklasyfikowane Intex
- Niesklasyfikowane Biltema
- Niesklasyfikowane Oricom
- Niesklasyfikowane B.E.G.
- Niesklasyfikowane Crane
- Niesklasyfikowane H.Koenig
- Niesklasyfikowane InAlto
- Niesklasyfikowane CMI
- Niesklasyfikowane Hilti
- Niesklasyfikowane Eastron
- Niesklasyfikowane Meireles
- Niesklasyfikowane Revitive
- Niesklasyfikowane Digitus
- Niesklasyfikowane Salewa
- Niesklasyfikowane Fimi
- Niesklasyfikowane Oppo
- Niesklasyfikowane Cateye
- Niesklasyfikowane Thinkware
- Niesklasyfikowane Alesis
- Niesklasyfikowane Lowrance
- Niesklasyfikowane Tanita
- Niesklasyfikowane Anybus
- Niesklasyfikowane Melissa
- Niesklasyfikowane TechniSat
- Niesklasyfikowane Auna
- Niesklasyfikowane Vimar
- Niesklasyfikowane Nubert
- Niesklasyfikowane V-TAC
- Niesklasyfikowane Dahua Technology
- Niesklasyfikowane Schneider
- Niesklasyfikowane Deutz
- Niesklasyfikowane SABO
- Niesklasyfikowane Ledlenser
- Niesklasyfikowane Beper
- Niesklasyfikowane Infomir
- Niesklasyfikowane Eurolite
- Niesklasyfikowane Kyocera
- Niesklasyfikowane LD Systems
- Niesklasyfikowane Techno Line
- Niesklasyfikowane SuperTooth
- Niesklasyfikowane Foppapedretti
- Niesklasyfikowane Foreo
- Niesklasyfikowane Daikin
- Niesklasyfikowane Kospel
- Niesklasyfikowane EVOline
- Niesklasyfikowane Kubota
- Niesklasyfikowane Thetford
- Niesklasyfikowane TrueLife
- Niesklasyfikowane Eufy
- Niesklasyfikowane Stirling
- Niesklasyfikowane Ricoh
- Niesklasyfikowane Krüger&Matz
- Niesklasyfikowane TOGU
- Niesklasyfikowane SMART Technologies
- Niesklasyfikowane Mad Dog
- Niesklasyfikowane NZXT
- Niesklasyfikowane Audioengine
- Niesklasyfikowane Hozelock
- Niesklasyfikowane Playmobil
- Niesklasyfikowane MPM
- Niesklasyfikowane OneConcept
- Niesklasyfikowane Recaro
- Niesklasyfikowane Hori
- Niesklasyfikowane CDA
- Niesklasyfikowane Emos
- Niesklasyfikowane Sabrent
- Niesklasyfikowane AVMATRIX
- Niesklasyfikowane IMC Toys
- Niesklasyfikowane Philco
- Niesklasyfikowane Neff
- Niesklasyfikowane Seiko
- Niesklasyfikowane Renkforce
- Niesklasyfikowane Rollei
- Niesklasyfikowane Corbero
- Niesklasyfikowane Morphy Richards
- Niesklasyfikowane Zanussi
- Niesklasyfikowane Sekonic
- Niesklasyfikowane Hensel
- Niesklasyfikowane Sonel
- Niesklasyfikowane Pure
- Niesklasyfikowane NightStick
- Niesklasyfikowane Ravanson
- Niesklasyfikowane Crivit
- Niesklasyfikowane Marshall
- Niesklasyfikowane Zenec
- Niesklasyfikowane Audiotec Fischer
- Niesklasyfikowane Osram
- Niesklasyfikowane BaseTech
- Niesklasyfikowane Thermex
- Niesklasyfikowane AXA
- Niesklasyfikowane Traxxas
- Niesklasyfikowane Viessmann
- Niesklasyfikowane Perel
- Niesklasyfikowane Janitza
- Niesklasyfikowane Wagner
- Niesklasyfikowane Salta
- Niesklasyfikowane Fagor
- Niesklasyfikowane Redmond
- Niesklasyfikowane Sena
- Niesklasyfikowane Koenic
- Niesklasyfikowane Graco
- Niesklasyfikowane Trotec
- Niesklasyfikowane Autel
- Niesklasyfikowane Somfy
- Niesklasyfikowane Everdure
- Niesklasyfikowane Uniden
- Niesklasyfikowane Adder
- Niesklasyfikowane Ansmann
- Niesklasyfikowane Clarion
- Niesklasyfikowane Wacom
- Niesklasyfikowane Omron
- Niesklasyfikowane Netgear
- Niesklasyfikowane Cellular Line
- Niesklasyfikowane Thomson
- Niesklasyfikowane DiO
- Niesklasyfikowane Pro-Ject
- Niesklasyfikowane Dremel
- Niesklasyfikowane Texas Instruments
- Niesklasyfikowane Lastolite
- Niesklasyfikowane AVM
- Niesklasyfikowane La Crosse Technology
- Niesklasyfikowane Growatt
- Niesklasyfikowane Velux
- Niesklasyfikowane Izzy
- Niesklasyfikowane Fresh 'n Rebel
- Niesklasyfikowane Little Tikes
- Niesklasyfikowane Chipolino
- Niesklasyfikowane Velleman
- Niesklasyfikowane Ferguson
- Niesklasyfikowane BT
- Niesklasyfikowane Meec Tools
- Niesklasyfikowane Fusion
- Niesklasyfikowane BOYA
- Niesklasyfikowane WMF
- Niesklasyfikowane Korg
- Niesklasyfikowane ProfiCook
- Niesklasyfikowane Homematic IP
- Niesklasyfikowane Neumann
- Niesklasyfikowane DataVideo
- Niesklasyfikowane AL-KO
- Niesklasyfikowane One For All
- Niesklasyfikowane Klarstein
- Niesklasyfikowane BEEM
- Niesklasyfikowane Wharfedale
- Niesklasyfikowane Safety 1st
- Niesklasyfikowane Polti
- Niesklasyfikowane Totolink
- Niesklasyfikowane Victor Technology
- Niesklasyfikowane Danfoss
- Niesklasyfikowane JYSK
- Niesklasyfikowane Coyote
- Niesklasyfikowane Intertechno
- Niesklasyfikowane Magnat
- Niesklasyfikowane Black Box
- Niesklasyfikowane Lowepro
- Niesklasyfikowane Güde
- Niesklasyfikowane Arendo
- Niesklasyfikowane Revamp
- Niesklasyfikowane DreamGEAR
- Niesklasyfikowane Witt
- Niesklasyfikowane Victron Energy
- Niesklasyfikowane Delta Dore
- Niesklasyfikowane E-ast
- Niesklasyfikowane Hobby
- Niesklasyfikowane Manta
- Niesklasyfikowane Pyle
- Niesklasyfikowane CTA Digital
- Niesklasyfikowane Segway
- Niesklasyfikowane Gem Toys
- Niesklasyfikowane Texas
- Niesklasyfikowane Apple
- Niesklasyfikowane ELAC
- Niesklasyfikowane Lancom
- Niesklasyfikowane Adviti
- Niesklasyfikowane Crimson
- Niesklasyfikowane Dymo
- Niesklasyfikowane ATIKA
- Niesklasyfikowane Hauck
- Niesklasyfikowane Bikemate
- Niesklasyfikowane Zoom
- Niesklasyfikowane Iogear
- Niesklasyfikowane Cardo
- Niesklasyfikowane Panduit
- Niesklasyfikowane Intellinet
- Niesklasyfikowane Datalogic
- Niesklasyfikowane NGS
- Niesklasyfikowane CRUX
- Niesklasyfikowane Vaillant
- Niesklasyfikowane Beautifly
- Niesklasyfikowane Newline
- Niesklasyfikowane Bavaria
- Niesklasyfikowane Devolo
- Niesklasyfikowane Juwel
- Niesklasyfikowane Biostar
- Niesklasyfikowane Cecotec
- Niesklasyfikowane Artusi
- Niesklasyfikowane Vileda
- Niesklasyfikowane Dirt Devil
- Niesklasyfikowane Midland
- Niesklasyfikowane Marantz
- Niesklasyfikowane KitchenAid
- Niesklasyfikowane MARTOR
- Niesklasyfikowane AFK
- Niesklasyfikowane Waeco
- Niesklasyfikowane AOC
- Niesklasyfikowane Cougar
- Niesklasyfikowane Monster
- Niesklasyfikowane Sennheiser
- Niesklasyfikowane JANDY
- Niesklasyfikowane Esoteric
- Niesklasyfikowane Roidmi
- Niesklasyfikowane Jabra
- Niesklasyfikowane Chord
- Niesklasyfikowane Zipper
- Niesklasyfikowane Vivotek
- Niesklasyfikowane Eta
- Niesklasyfikowane Mount-It!
- Niesklasyfikowane Kingston
- Niesklasyfikowane Camry
- Niesklasyfikowane Vtech
- Niesklasyfikowane Steba
- Niesklasyfikowane Werma
- Niesklasyfikowane Perixx
- Niesklasyfikowane Peerless-AV
- Niesklasyfikowane Speco Technologies
- Niesklasyfikowane Medeli
- Niesklasyfikowane Suunto
- Niesklasyfikowane Showtec
- Niesklasyfikowane Weber
- Niesklasyfikowane Heckler Design
- Niesklasyfikowane Lenoxx
- Niesklasyfikowane Keurig
- Niesklasyfikowane Grundfos
- Niesklasyfikowane Bowers & Wilkins
- Niesklasyfikowane Samson
- Niesklasyfikowane EtiamPro
- Niesklasyfikowane EA Elektro Automatik
- Niesklasyfikowane Tineco
- Niesklasyfikowane Imperial
- Niesklasyfikowane Emporia
- Niesklasyfikowane Helios
- Niesklasyfikowane Scarlett
- Niesklasyfikowane SodaStream
- Niesklasyfikowane Microlife
- Niesklasyfikowane PreSonus
- Niesklasyfikowane Mercusys
- Niesklasyfikowane Koss
- Niesklasyfikowane Monitor Audio
- Niesklasyfikowane Audio Pro
- Niesklasyfikowane I-TEC
- Niesklasyfikowane Weston
- Niesklasyfikowane ARRI
- Niesklasyfikowane ResMed
- Niesklasyfikowane Blackstar
- Niesklasyfikowane NACON
- Niesklasyfikowane Gossen Metrawatt
- Niesklasyfikowane Sôlt
- Niesklasyfikowane Mafell
- Niesklasyfikowane Eden
- Niesklasyfikowane Fosi Audio
- Niesklasyfikowane TC Electronic
- Niesklasyfikowane GUTFELS
- Niesklasyfikowane Shelly
- Niesklasyfikowane Revox
- Niesklasyfikowane Fluke
- Niesklasyfikowane Nevir
- Niesklasyfikowane Kindermann
- Niesklasyfikowane Megger
- Niesklasyfikowane Ewent
- Niesklasyfikowane HyperIce
- Niesklasyfikowane Olympus
- Niesklasyfikowane Navitel
- Niesklasyfikowane Greisinger
- Niesklasyfikowane Draytek
- Niesklasyfikowane TriStar
- Niesklasyfikowane Ibiza Sound
- Niesklasyfikowane MTD
- Niesklasyfikowane Oliveri
- Niesklasyfikowane Vonyx
- Niesklasyfikowane Musical Fidelity
- Niesklasyfikowane Master Lock
- Niesklasyfikowane Numatic
- Niesklasyfikowane Bogen
- Niesklasyfikowane Landmann
- Niesklasyfikowane Pulsar
- Niesklasyfikowane PATLITE
- Niesklasyfikowane Exquisit
- Niesklasyfikowane Bartscher
- Niesklasyfikowane Phanteks
- Niesklasyfikowane First Austria
- Niesklasyfikowane Alto
- Niesklasyfikowane Hestan
- Niesklasyfikowane Fiskars
- Niesklasyfikowane Gastroback
- Niesklasyfikowane GYS
- Niesklasyfikowane Mitsubishi
- Niesklasyfikowane Privileg
- Niesklasyfikowane Avaya
- Niesklasyfikowane Edimax
- Niesklasyfikowane Naim
- Niesklasyfikowane Razer
- Niesklasyfikowane Grothe
- Niesklasyfikowane Dimplex
- Niesklasyfikowane Falmec
- Niesklasyfikowane National Geographic
- Niesklasyfikowane Florabest
- Niesklasyfikowane Harvia
- Niesklasyfikowane Baxi
- Niesklasyfikowane BeSafe
- Niesklasyfikowane ADATA
- Niesklasyfikowane Kidde
- Niesklasyfikowane Chief
- Niesklasyfikowane 4ms
- Niesklasyfikowane Peavey
- Niesklasyfikowane IVT
- Niesklasyfikowane GoClever
- Niesklasyfikowane Sunding
- Niesklasyfikowane Baby Lock
- Niesklasyfikowane Dehner
- Niesklasyfikowane Bryton
- Niesklasyfikowane Weidmüller
- Niesklasyfikowane BENNING
- Niesklasyfikowane ION
- Niesklasyfikowane Camille Bauer
- Niesklasyfikowane Huion
- Niesklasyfikowane Arçelik
- Niesklasyfikowane ART
- Niesklasyfikowane First Alert
- Niesklasyfikowane Hanseatic
- Niesklasyfikowane Assa Abloy
- Niesklasyfikowane NAD
- Niesklasyfikowane Solo
- Niesklasyfikowane Continental Edison
- Niesklasyfikowane RCF
- Niesklasyfikowane Topmove
- Niesklasyfikowane Delta
- Niesklasyfikowane Kerbl
- Niesklasyfikowane Bifinett
- Niesklasyfikowane SEH
- Niesklasyfikowane Zhiyun
- Niesklasyfikowane Gree
- Niesklasyfikowane Fluval
- Niesklasyfikowane Bissell
- Niesklasyfikowane AirLive
- Niesklasyfikowane Harman Kardon
- Niesklasyfikowane Rolls
- Niesklasyfikowane Audio-Technica
- Niesklasyfikowane Maginon
- Niesklasyfikowane EnGenius
- Niesklasyfikowane SPC
- Niesklasyfikowane Atag
- Niesklasyfikowane Babymoov
- Niesklasyfikowane Rosieres
- Niesklasyfikowane Franke
- Niesklasyfikowane Planet
- Niesklasyfikowane Intermec
- Niesklasyfikowane Dahle
- Niesklasyfikowane XGIMI
- Niesklasyfikowane Adidas
- Niesklasyfikowane GoGen
- Niesklasyfikowane Intenso
- Niesklasyfikowane DCG
- Niesklasyfikowane Accu-Chek
- Niesklasyfikowane Genie
- Niesklasyfikowane TC Helicon
- Niesklasyfikowane RCBS
- Niesklasyfikowane Peg Perego
- Niesklasyfikowane NEC
- Niesklasyfikowane Rexel
- Niesklasyfikowane Brandson
- Niesklasyfikowane Soundcraft
- Niesklasyfikowane Beautiful
- Niesklasyfikowane Metrix
- Niesklasyfikowane Parrot
- Niesklasyfikowane Antec
- Niesklasyfikowane Vornado
- Niesklasyfikowane Polaroid
- Niesklasyfikowane Rocktrail
- Niesklasyfikowane Prestigio
- Niesklasyfikowane Blustream
- Niesklasyfikowane Aiwa
- Niesklasyfikowane G3 Ferrari
- Niesklasyfikowane Ooni
- Niesklasyfikowane JL Audio
- Niesklasyfikowane LevelOne
- Niesklasyfikowane Omega Altise
- Niesklasyfikowane Konica Minolta
- Niesklasyfikowane Bugaboo
- Niesklasyfikowane AKAI
- Niesklasyfikowane Tunturi
- Niesklasyfikowane Razor
- Niesklasyfikowane Digi
- Niesklasyfikowane JLab
- Niesklasyfikowane OSEE
- Niesklasyfikowane Maglite
- Niesklasyfikowane Mobicool
- Niesklasyfikowane Axis
- Niesklasyfikowane Sanyo
- Niesklasyfikowane ICOM
- Niesklasyfikowane Vivolink
- Niesklasyfikowane Life Fitness
- Niesklasyfikowane Red Digital Cinema
- Niesklasyfikowane Westfalia
- Niesklasyfikowane Hamilton Beach
- Niesklasyfikowane Majority
- Niesklasyfikowane Elvid
- Niesklasyfikowane Hayward
- Niesklasyfikowane Neumärker
- Niesklasyfikowane REL Acoustics
- Niesklasyfikowane Flaem
- Niesklasyfikowane Gourmetmaxx
- Niesklasyfikowane Rigol
- Niesklasyfikowane Bixolon
- Niesklasyfikowane Ergotools Pattfield
- Niesklasyfikowane Hoymiles
- Niesklasyfikowane Teufel
- Niesklasyfikowane Novy
- Niesklasyfikowane Suevia
- Niesklasyfikowane Remko
- Niesklasyfikowane Hartke
- Niesklasyfikowane Clatronic
- Niesklasyfikowane BabyBjörn
- Niesklasyfikowane Healthy Choice
- Niesklasyfikowane Tronic
- Niesklasyfikowane Klark Teknik
- Niesklasyfikowane Dali
- Niesklasyfikowane Vision
- Niesklasyfikowane Telefunken
- Niesklasyfikowane NEO Tools
- Niesklasyfikowane Oregon Scientific
- Niesklasyfikowane Lorex
- Niesklasyfikowane Eventide
- Niesklasyfikowane Optoma
- Niesklasyfikowane Melitta
- Niesklasyfikowane Rommer
- Niesklasyfikowane Proel
- Niesklasyfikowane Calor
- Niesklasyfikowane Inventum
- Niesklasyfikowane SVAN
- Niesklasyfikowane Ariete
- Niesklasyfikowane Flame
- Niesklasyfikowane Hifonics
- Niesklasyfikowane Vogel's
- Niesklasyfikowane Heidemann
- Niesklasyfikowane Fuzzix
- Niesklasyfikowane Focal
- Niesklasyfikowane OnePlus
- Niesklasyfikowane Tepro
- Niesklasyfikowane Bernina
- Niesklasyfikowane Asrock
- Niesklasyfikowane LiftMaster
- Niesklasyfikowane Taga Harmony
- Niesklasyfikowane Graef
- Niesklasyfikowane Viper
- Niesklasyfikowane Napoleon
- Niesklasyfikowane Audix
- Niesklasyfikowane Milesight
- Niesklasyfikowane DBX
- Niesklasyfikowane Princess
- Niesklasyfikowane Baby Jogger
- Niesklasyfikowane Kicker
- Niesklasyfikowane Amazon
- Niesklasyfikowane Carson
- Niesklasyfikowane Doepfer
- Niesklasyfikowane TDE Instruments
- Niesklasyfikowane Innoliving
- Niesklasyfikowane Aluratek
- Niesklasyfikowane Abus
- Niesklasyfikowane Thorens
- Niesklasyfikowane Bresser
- Niesklasyfikowane Sunbeam
- Niesklasyfikowane Rocstor
- Niesklasyfikowane Reebok
- Niesklasyfikowane Omnitronic
- Niesklasyfikowane Livarno Lux
- Niesklasyfikowane Solac
- Niesklasyfikowane Valco Baby
- Niesklasyfikowane Elro
- Niesklasyfikowane Olympia
- Niesklasyfikowane Jay-Tech
- Niesklasyfikowane Novis
- Niesklasyfikowane Hama
- Niesklasyfikowane Mackie
- Niesklasyfikowane Juki
- Niesklasyfikowane Shokz
- Niesklasyfikowane Microsoft
- Niesklasyfikowane Marmitek
- Niesklasyfikowane Busch + Müller
- Niesklasyfikowane Eltako
- Niesklasyfikowane Heller
- Niesklasyfikowane Palmer
- Niesklasyfikowane Sanitaire
- Niesklasyfikowane FiiO
- Niesklasyfikowane SkyRC
- Niesklasyfikowane Waring Commercial
- Niesklasyfikowane Corel
- Niesklasyfikowane SE Electronics
- Niesklasyfikowane Ubiquiti Networks
- Niesklasyfikowane Western Digital
- Niesklasyfikowane Princeton Tec
- Niesklasyfikowane Lindell Audio
- Niesklasyfikowane Verbatim
- Niesklasyfikowane Baby Annabell
- Niesklasyfikowane Caple
- Niesklasyfikowane Taylor
- Niesklasyfikowane Duronic
- Niesklasyfikowane ModeCom
- Niesklasyfikowane Nivona
- Niesklasyfikowane Smoby
- Niesklasyfikowane Smart-AVI
- Niesklasyfikowane Maximum
- Niesklasyfikowane Omega
- Niesklasyfikowane Axagon
- Niesklasyfikowane MXL
- Niesklasyfikowane Cameo
- Niesklasyfikowane Christopeit
- Niesklasyfikowane Comfee
- Niesklasyfikowane Medel
- Niesklasyfikowane Fein
- Niesklasyfikowane Mattel
- Niesklasyfikowane Jumbo
- Niesklasyfikowane Barco
- Niesklasyfikowane Goobay
- Niesklasyfikowane Sagemcom
- Niesklasyfikowane Optex
- Niesklasyfikowane GoPro
- Niesklasyfikowane Bush
- Niesklasyfikowane Siméo
- Niesklasyfikowane ThinkFun
- Niesklasyfikowane Schwaiger
- Niesklasyfikowane New Pol
- Niesklasyfikowane Promise Technology
- Niesklasyfikowane Sharkoon
- Niesklasyfikowane Eheim
- Niesklasyfikowane Watson
- Niesklasyfikowane Saramonic
- Niesklasyfikowane Oase
- Niesklasyfikowane Pro-User
- Niesklasyfikowane Mean Well
- Niesklasyfikowane Gravity
- Niesklasyfikowane Kenmore
- Niesklasyfikowane Kaiser
- Niesklasyfikowane Equip
- Niesklasyfikowane Loewe
- Niesklasyfikowane DeepCool
- Niesklasyfikowane Bluesound
- Niesklasyfikowane Zephyr
- Niesklasyfikowane Michelin
- Niesklasyfikowane Boso
- Niesklasyfikowane Kemo
- Niesklasyfikowane Breville
- Niesklasyfikowane Swift
- Niesklasyfikowane Terraillon
- Niesklasyfikowane Sera
- Niesklasyfikowane Allibert
- Niesklasyfikowane Aerotec
- Niesklasyfikowane GA.MA
- Niesklasyfikowane Juniper
- Niesklasyfikowane Deaf Bonce
- Niesklasyfikowane Sangean
- Niesklasyfikowane BORA
- Niesklasyfikowane Cudy
- Niesklasyfikowane VOX
- Niesklasyfikowane QNAP
- Niesklasyfikowane Ferm
- Niesklasyfikowane COLBOR
- Niesklasyfikowane Insignia
- Niesklasyfikowane AVer
- Niesklasyfikowane AYA
- Niesklasyfikowane Pelgrim
- Niesklasyfikowane Walrus Audio
- Niesklasyfikowane Ambient Weather
- Niesklasyfikowane Veripart
- Niesklasyfikowane Apricorn
- Niesklasyfikowane Esperanza
- Niesklasyfikowane Playtive
- Niesklasyfikowane Arris
- Niesklasyfikowane SVS
- Niesklasyfikowane Navman
- Niesklasyfikowane Chenbro Micom
- Niesklasyfikowane HTC
- Niesklasyfikowane Gabor
- Niesklasyfikowane ZKTeco
- Niesklasyfikowane Netis
- Niesklasyfikowane Frilec
- Niesklasyfikowane Akuvox
- Niesklasyfikowane Benavent
- Niesklasyfikowane Jane
- Niesklasyfikowane Hager
- Niesklasyfikowane Extech
- Niesklasyfikowane NANO Modules
- Niesklasyfikowane Elation
- Niesklasyfikowane GVM
- Niesklasyfikowane Ravensburger
- Niesklasyfikowane TomTom
- Niesklasyfikowane Shark
- Niesklasyfikowane TSC
- Niesklasyfikowane True
- Niesklasyfikowane 3M
- Niesklasyfikowane ECS
- Niesklasyfikowane Franklin
- Niesklasyfikowane Magivaac
- Niesklasyfikowane Victrola
- Niesklasyfikowane Nilfisk
- Niesklasyfikowane Tower
- Niesklasyfikowane XPG
- Niesklasyfikowane Elta
- Niesklasyfikowane Orima
- Niesklasyfikowane Yukon
- Niesklasyfikowane Mac Audio
- Niesklasyfikowane Vakoss
- Niesklasyfikowane Infinity
- Niesklasyfikowane Pentair
- Niesklasyfikowane McIntosh
- Niesklasyfikowane Advance Acoustic
- Niesklasyfikowane Solis
- Niesklasyfikowane Revel
- Niesklasyfikowane Junkers
- Niesklasyfikowane Denver
- Niesklasyfikowane Harley Benton
- Niesklasyfikowane Anker
- Niesklasyfikowane Testboy
- Niesklasyfikowane Pentax
- Niesklasyfikowane Bushnell
- Niesklasyfikowane Horizon Fitness
- Niesklasyfikowane Berger & Schröter
- Niesklasyfikowane Allnet
- Niesklasyfikowane Kernau
- Niesklasyfikowane Veritas
- Niesklasyfikowane Dynacord
- Niesklasyfikowane Aspes
- Niesklasyfikowane Albrecht
- Niesklasyfikowane Marshall Electronics
- Niesklasyfikowane Orion
- Niesklasyfikowane Ashly
- Niesklasyfikowane DCS
- Niesklasyfikowane Hitachi
- Niesklasyfikowane Postium
- Niesklasyfikowane Weller
- Niesklasyfikowane Herkules
- Niesklasyfikowane Blumfeldt
- Niesklasyfikowane Futurelight
- Niesklasyfikowane Yale
- Niesklasyfikowane JIMMY
- Niesklasyfikowane FED
- Niesklasyfikowane InfaSecure
- Niesklasyfikowane Fender
- Niesklasyfikowane Winix
- Niesklasyfikowane Hertz
- Niesklasyfikowane Em-Trak
- Niesklasyfikowane Nitecore
- Niesklasyfikowane InLine
- Niesklasyfikowane Inter-M
- Niesklasyfikowane Kali Audio
- Niesklasyfikowane Rapoo
- Niesklasyfikowane Tracer
- Niesklasyfikowane Salton
- Niesklasyfikowane Ventura
- Niesklasyfikowane Polisport
- Niesklasyfikowane Stabila
- Niesklasyfikowane IStarUSA
- Niesklasyfikowane Joby
- Niesklasyfikowane Technika
- Niesklasyfikowane Emerson
- Niesklasyfikowane Enhance
- Niesklasyfikowane Seiki
- Niesklasyfikowane SereneLife
- Niesklasyfikowane JennAir
- Niesklasyfikowane Kyoritsu
- Niesklasyfikowane Pfaff
- Niesklasyfikowane Craftsman
- Niesklasyfikowane Silverstone
- Niesklasyfikowane Mooer
- Niesklasyfikowane Ernitec
- Niesklasyfikowane AKG
- Niesklasyfikowane Vemer
- Niesklasyfikowane Frigidaire
- Niesklasyfikowane CyberPower
- Niesklasyfikowane Azden
- Niesklasyfikowane Galanz
- Niesklasyfikowane FeiyuTech
- Niesklasyfikowane AVerMedia
- Niesklasyfikowane Roccat
- Niesklasyfikowane Olight
- Niesklasyfikowane Barazza
- Niesklasyfikowane Busch-Jaeger
- Niesklasyfikowane Magnus
- Niesklasyfikowane EcoFlow
- Niesklasyfikowane RCA
- Niesklasyfikowane Klein Tools
- Niesklasyfikowane OWC
- Niesklasyfikowane MEE Audio
- Niesklasyfikowane Black Diamond
- Niesklasyfikowane AJA
- Niesklasyfikowane Electro Harmonix
- Niesklasyfikowane KRK
- Niesklasyfikowane MBM
- Niesklasyfikowane Scotsman
- Niesklasyfikowane Genius
- Niesklasyfikowane Marvel
- Niesklasyfikowane Media-Tech
- Niesklasyfikowane Levenhuk
- Niesklasyfikowane Atlas Sound
- Niesklasyfikowane IOTAVX
- Niesklasyfikowane Fieldmann
- Niesklasyfikowane Summit
- Niesklasyfikowane Homelite
- Niesklasyfikowane Gemini
- Niesklasyfikowane BenQ
- Niesklasyfikowane Trevi
- Niesklasyfikowane Technaxx
- Niesklasyfikowane Atlona
- Niesklasyfikowane Elektrobock
- Niesklasyfikowane Thermaltake
- Niesklasyfikowane Amer
- Niesklasyfikowane Hunter
- Niesklasyfikowane FSR
- Niesklasyfikowane Sirius
- Niesklasyfikowane Simrad
- Niesklasyfikowane Salus
- Niesklasyfikowane ENTES
- Niesklasyfikowane Tams Elektronik
- Niesklasyfikowane Nintendo
- Niesklasyfikowane Lexibook
- Niesklasyfikowane Soundskins
- Niesklasyfikowane Ridgid
- Niesklasyfikowane Foster
- Niesklasyfikowane Hammond
- Niesklasyfikowane Minn Kota
- Niesklasyfikowane Shindaiwa
- Niesklasyfikowane GPX
- Niesklasyfikowane Gefen
- Niesklasyfikowane Hansgrohe
- Niesklasyfikowane Lanaform
- Niesklasyfikowane Gardenline
- Niesklasyfikowane Martin
- Niesklasyfikowane Hanwha
- Niesklasyfikowane Rommelsbacher
- Niesklasyfikowane American International
- Niesklasyfikowane Ixxat
- Niesklasyfikowane Overmax
- Niesklasyfikowane SEADA
- Niesklasyfikowane Vivanco
- Niesklasyfikowane EQ-3
- Niesklasyfikowane Inkbird
- Niesklasyfikowane Fishman
- Niesklasyfikowane Leifheit
- Niesklasyfikowane Eurochron
- Niesklasyfikowane Radial Engineering
- Niesklasyfikowane PowerPlus
- Niesklasyfikowane Fulgor Milano
- Niesklasyfikowane Quantum
- Niesklasyfikowane MDT
- Niesklasyfikowane Kelvinator
- Niesklasyfikowane Bebe Confort
- Niesklasyfikowane Grandstream
- Niesklasyfikowane Alpha Tools
- Niesklasyfikowane Arturia
- Niesklasyfikowane Lectrosonics
- Niesklasyfikowane Gaggenau
- Niesklasyfikowane Asaklitt
- Niesklasyfikowane Sencor
- Niesklasyfikowane Emko
- Niesklasyfikowane BDI
- Niesklasyfikowane Definitive Technology
- Niesklasyfikowane Ground Zero
- Niesklasyfikowane Noxon
- Niesklasyfikowane Polsen
- Niesklasyfikowane Vonroc
- Niesklasyfikowane Mistral
- Niesklasyfikowane Elica
- Niesklasyfikowane Eversolo
- Niesklasyfikowane Tamron
- Niesklasyfikowane Spear & Jackson
- Niesklasyfikowane Raymarine
- Niesklasyfikowane Powerfix
- Niesklasyfikowane HiKOKI
- Niesklasyfikowane Workzone
- Niesklasyfikowane Insta360
- Niesklasyfikowane Evenflo
- Niesklasyfikowane McCulloch
- Niesklasyfikowane Tempo
- Niesklasyfikowane Nabo
- Niesklasyfikowane EasyMaxx
- Niesklasyfikowane Stinger
- Niesklasyfikowane Dreadbox
- Niesklasyfikowane PowerBass
- Niesklasyfikowane Elo
- Niesklasyfikowane Avanti
- Niesklasyfikowane BABY Born
- Niesklasyfikowane Seaward
- Niesklasyfikowane Revlon
- Niesklasyfikowane Power Dynamics
- Niesklasyfikowane Blackmagic Design
- Niesklasyfikowane AEA
- Niesklasyfikowane Asko
- Niesklasyfikowane Kanto
- Niesklasyfikowane Ikan
- Niesklasyfikowane Alecto
- Niesklasyfikowane Vacmaster
- Niesklasyfikowane Kathrein
- Niesklasyfikowane Kalorik
- Niesklasyfikowane Avidsen
- Niesklasyfikowane Binatone
- Niesklasyfikowane Rockford Fosgate
- Niesklasyfikowane Domyos
- Niesklasyfikowane DOD
- Niesklasyfikowane Suntec
- Niesklasyfikowane Steinberg
- Niesklasyfikowane Impact
- Niesklasyfikowane Be Quiet!
- Niesklasyfikowane Microboards
- Niesklasyfikowane JUNG
- Niesklasyfikowane Xtorm
- Niesklasyfikowane Eaton
- Niesklasyfikowane Carrier
- Niesklasyfikowane Burg Wächter
- Niesklasyfikowane Hammer
- Niesklasyfikowane Nextbase
- Niesklasyfikowane Lund
- Niesklasyfikowane Honey-Can-Do
- Niesklasyfikowane Foscam
- Niesklasyfikowane Lumens
- Niesklasyfikowane Eizo
- Niesklasyfikowane Senal
- Niesklasyfikowane TOA
- Niesklasyfikowane Newland
- Niesklasyfikowane Byron
- Niesklasyfikowane Monacor
- Niesklasyfikowane Esatto
- Niesklasyfikowane Aputure
- Niesklasyfikowane HQ Power
- Niesklasyfikowane Signature
- Niesklasyfikowane Ferplast
- Niesklasyfikowane Daewoo
- Niesklasyfikowane ADE
- Niesklasyfikowane Hotone
- Niesklasyfikowane Cosori
- Niesklasyfikowane X-Sense
- Niesklasyfikowane Neutrik
- Niesklasyfikowane Tannoy
- Niesklasyfikowane Livington
- Niesklasyfikowane Electro-Voice
- Niesklasyfikowane Anthem
- Niesklasyfikowane Dörr
- Niesklasyfikowane Consul
- Niesklasyfikowane Tascam
- Niesklasyfikowane Etekcity
- Niesklasyfikowane RME
- Niesklasyfikowane Metz
- Niesklasyfikowane Laser
- Niesklasyfikowane Wiha
- Niesklasyfikowane M-e
- Niesklasyfikowane Lervia
- Niesklasyfikowane WAGAN
- Niesklasyfikowane Kunft
- Niesklasyfikowane Robinhood
- Niesklasyfikowane Tetra
- Niesklasyfikowane Grunkel
- Niesklasyfikowane SLV
- Niesklasyfikowane H-Tronic
- Niesklasyfikowane Sonnet
- Niesklasyfikowane Novation
- Niesklasyfikowane Silver Cross
- Niesklasyfikowane Vicoustic
- Niesklasyfikowane Zibro
- Niesklasyfikowane Alphatronics
- Niesklasyfikowane Havis
- Niesklasyfikowane Becken
- Niesklasyfikowane JAYS
- Niesklasyfikowane AudioControl
- Niesklasyfikowane Karma
- Niesklasyfikowane Scandomestic
- Niesklasyfikowane NOCO
- Niesklasyfikowane EVE
- Niesklasyfikowane OKAY
- Niesklasyfikowane API Audio
- Niesklasyfikowane Bahr
- Niesklasyfikowane Socket Mobile
- Niesklasyfikowane Smartwares
- Niesklasyfikowane Elgato
- Niesklasyfikowane Traeger
- Niesklasyfikowane Magmatic
- Niesklasyfikowane Porter-Cable
- Niesklasyfikowane Noctua
- Niesklasyfikowane Masport
- Niesklasyfikowane Metabo
- Niesklasyfikowane GVision
- Niesklasyfikowane ProfiCare
- Niesklasyfikowane Audiolab
- Niesklasyfikowane Bretford
- Niesklasyfikowane Galcon
- Niesklasyfikowane Guzzanti
- Niesklasyfikowane Vocopro
- Niesklasyfikowane Technical Pro
- Niesklasyfikowane Adj
- Niesklasyfikowane CM Storm
- Niesklasyfikowane Mauser
- Niesklasyfikowane MEPROLIGHT
- Niesklasyfikowane Lagrange
- Niesklasyfikowane Lamax
- Niesklasyfikowane Absco
- Niesklasyfikowane Bestgreen
- Niesklasyfikowane WiiM
- Niesklasyfikowane AkYtec
- Niesklasyfikowane Wachendorff
- Niesklasyfikowane SPL
- Niesklasyfikowane SureFire
- Niesklasyfikowane ISi
- Niesklasyfikowane Cyrus
- Niesklasyfikowane Gold Note
- Niesklasyfikowane SolaX Power
- Niesklasyfikowane Ketron
- Niesklasyfikowane ETC
- Niesklasyfikowane EZ Dupe
- Niesklasyfikowane IBEAM
- Niesklasyfikowane Terratec
- Niesklasyfikowane Gastronoma
- Niesklasyfikowane Pinolino
- Niesklasyfikowane Transcend
- Niesklasyfikowane Edilkamin
- Niesklasyfikowane Axxess
- Niesklasyfikowane Dualit
- Niesklasyfikowane Kern
- Niesklasyfikowane Crunch
- Niesklasyfikowane Wilson
- Niesklasyfikowane Goki
- Niesklasyfikowane Zoofari
- Niesklasyfikowane EGO
- Niesklasyfikowane WilTec
- Niesklasyfikowane Toro
- Niesklasyfikowane AstralPool
- Niesklasyfikowane ABC Design
- Niesklasyfikowane Müller
- Niesklasyfikowane Cotech
- Niesklasyfikowane Gre
- Niesklasyfikowane Britax
- Niesklasyfikowane Humminbird
- Niesklasyfikowane Dataflex
- Niesklasyfikowane Dormakaba
- Niesklasyfikowane Stairville
- Niesklasyfikowane Snom
- Niesklasyfikowane Elmo
- Niesklasyfikowane Vitek
- Niesklasyfikowane Skil
- Niesklasyfikowane Xvive
- Niesklasyfikowane Geneva
- Niesklasyfikowane Miomare
- Niesklasyfikowane Alfatron
- Niesklasyfikowane Anton/Bauer
- Niesklasyfikowane Sound Devices
- Niesklasyfikowane Eurom
- Niesklasyfikowane Beha-Amprobe
- Niesklasyfikowane Sebo
- Niesklasyfikowane Enermax
- Niesklasyfikowane Clas Ohlson
- Niesklasyfikowane Savio
- Niesklasyfikowane TechBite
- Niesklasyfikowane RADEMACHER
- Niesklasyfikowane Blackburn
- Niesklasyfikowane Salicru
- Niesklasyfikowane Laserliner
- Niesklasyfikowane Zotac
- Niesklasyfikowane Cocraft
- Niesklasyfikowane Lupine
- Niesklasyfikowane Reflexion
- Niesklasyfikowane Megasat
- Niesklasyfikowane Kopp
- Niesklasyfikowane Hikmicro
- Niesklasyfikowane Maytronics
- Niesklasyfikowane Crosley
- Niesklasyfikowane TensCare
- Niesklasyfikowane Varta
- Niesklasyfikowane Nutrichef
- Niesklasyfikowane Constructa
- Niesklasyfikowane Proline
- Niesklasyfikowane Atomos
- Niesklasyfikowane Adventuridge
- Niesklasyfikowane Casa Deco
- Niesklasyfikowane EXIT
- Niesklasyfikowane HK Audio
- Niesklasyfikowane Euromaid
- Niesklasyfikowane Reloop
- Niesklasyfikowane Primewire
- Niesklasyfikowane Swissvoice
- Niesklasyfikowane Lorelli
- Niesklasyfikowane Cherry
- Niesklasyfikowane Greenworks
- Niesklasyfikowane Rittal
- Niesklasyfikowane BSS Audio
- Niesklasyfikowane Newstar
- Niesklasyfikowane Oreck
- Niesklasyfikowane Timbersled
- Niesklasyfikowane I.safe Mobile
- Niesklasyfikowane Artsound
- Niesklasyfikowane Chandler
- Niesklasyfikowane Flama
- Niesklasyfikowane Sevenoak
- Niesklasyfikowane Vivitar
- Niesklasyfikowane Areca
- Niesklasyfikowane Belkin
- Niesklasyfikowane SWIT
- Niesklasyfikowane Zeiss
- Niesklasyfikowane Bebob
- Niesklasyfikowane Morley
- Niesklasyfikowane Generac
- Niesklasyfikowane Kramer
- Niesklasyfikowane Gen Energy
- Niesklasyfikowane Lian Li
- Niesklasyfikowane Kahayan
- Niesklasyfikowane Profoto
- Niesklasyfikowane Wimberley
- Niesklasyfikowane Kopul
- Niesklasyfikowane Analog Way
- Niesklasyfikowane BZBGear
- Niesklasyfikowane K&M
- Niesklasyfikowane RGBlink
- Niesklasyfikowane Glide Gear
- Niesklasyfikowane Hosa
- Niesklasyfikowane Vortex
- Niesklasyfikowane Cranborne Audio
- Niesklasyfikowane SmallRig
- Niesklasyfikowane ToughTested
- Niesklasyfikowane Arkon
- Niesklasyfikowane Trijicon
- Niesklasyfikowane Xcellon
- Niesklasyfikowane Murideo
- Niesklasyfikowane Intellijel
- Niesklasyfikowane CEDAR
- Niesklasyfikowane Rupert Neve Designs
- Niesklasyfikowane Pawa
- Niesklasyfikowane Erica Synths
- Niesklasyfikowane Key Digital
- Niesklasyfikowane Robus
- Niesklasyfikowane Ideal
- Niesklasyfikowane Apantac
- Niesklasyfikowane AMX
- Niesklasyfikowane Rosco
- Niesklasyfikowane Scancool
- Niesklasyfikowane JILONG
- Niesklasyfikowane OBH Nordica
- Niesklasyfikowane AENO
- Niesklasyfikowane ABB
- Niesklasyfikowane SRS
- Niesklasyfikowane Thermador
- Niesklasyfikowane Wolfcraft
- Niesklasyfikowane Budda
- Niesklasyfikowane Soler & Palau
- Niesklasyfikowane Goodis
- Niesklasyfikowane Bestron
- Niesklasyfikowane Eura
- Niesklasyfikowane Optimum
- Niesklasyfikowane Atosa
- Niesklasyfikowane HiLook
- Niesklasyfikowane Rotel
- Niesklasyfikowane Lexmark
- Niesklasyfikowane Atlas
- Niesklasyfikowane Profile
- Niesklasyfikowane Sensiplast
- Niesklasyfikowane Swan
- Niesklasyfikowane Brondi
- Niesklasyfikowane Fysic
- Niesklasyfikowane Wiko
- Niesklasyfikowane A.O. Smith
- Niesklasyfikowane Dangerous Music
- Niesklasyfikowane Lumantek
- Niesklasyfikowane Kluge
- Niesklasyfikowane Aduro
- Niesklasyfikowane Alpina
- Niesklasyfikowane Airlux
- Niesklasyfikowane Aligator
- Niesklasyfikowane Ambrogio
- Niesklasyfikowane Allied Telesis
- Niesklasyfikowane Alienware
- Niesklasyfikowane Amfra
- Niesklasyfikowane Alcon
- Niesklasyfikowane A4tech
- Niesklasyfikowane Ampeg
- Niesklasyfikowane Amplicom
- Niesklasyfikowane Amprobe
- Niesklasyfikowane Archos
- Niesklasyfikowane Argon
- Niesklasyfikowane American Audio
- Niesklasyfikowane Aquapur
- Niesklasyfikowane Devialet
- Niesklasyfikowane KDK
- Niesklasyfikowane IFi Audio
- Niesklasyfikowane Crosscall
- Niesklasyfikowane Cabasse
- Niesklasyfikowane Amiko
- Niesklasyfikowane Aeris
- Niesklasyfikowane Ascom
- Niesklasyfikowane Alpen Kreuzer
- Niesklasyfikowane ACME
- Niesklasyfikowane Reflecta
- Niesklasyfikowane Argus
- Niesklasyfikowane ATN
- Niesklasyfikowane Ziggo
- Niesklasyfikowane Intermatic
- Niesklasyfikowane Flamingo
- Niesklasyfikowane Toolland
- Niesklasyfikowane Brennenstuhl
- Niesklasyfikowane MJX
- Niesklasyfikowane Hirschmann
- Niesklasyfikowane Kruidvat
- Niesklasyfikowane Audison
- Niesklasyfikowane Proteca
- Niesklasyfikowane Toorx
- Niesklasyfikowane Body Solid
- Niesklasyfikowane Tryton
- Niesklasyfikowane Oceanic
- Niesklasyfikowane Korona
- Niesklasyfikowane Saturn
- Niesklasyfikowane Tiger
- Niesklasyfikowane Progress
- Niesklasyfikowane Meradiso
- Niesklasyfikowane BH Fitness
- Niesklasyfikowane Tevion
- Niesklasyfikowane GPO
- Niesklasyfikowane Lucide
- Niesklasyfikowane Parisot
- Niesklasyfikowane Caliber
- Niesklasyfikowane Bellini
- Niesklasyfikowane Eminent
- Niesklasyfikowane Pressalit
- Niesklasyfikowane Oster
- Niesklasyfikowane Kichler
- Niesklasyfikowane VAX
- Niesklasyfikowane Vestel
- Niesklasyfikowane Sinbo
- Niesklasyfikowane Jata
- Niesklasyfikowane VirtuFit
- Niesklasyfikowane Fritel
- Niesklasyfikowane Ordex
- Niesklasyfikowane Itho
- Niesklasyfikowane Targus
- Niesklasyfikowane Q-CONNECT
- Niesklasyfikowane Sicce
- Niesklasyfikowane Outwell
- Niesklasyfikowane Sitecom
- Niesklasyfikowane United Office
- Niesklasyfikowane Monogram
- Niesklasyfikowane Maxdata
- Niesklasyfikowane Hard Head
- Niesklasyfikowane Exibel
- Niesklasyfikowane Logik
- Niesklasyfikowane Easy Camp
- Niesklasyfikowane Energy Sistem
- Niesklasyfikowane Orbit
- Niesklasyfikowane Auto Joe
- Niesklasyfikowane Fortinet
- Niesklasyfikowane Youin
- Niesklasyfikowane Telestar
- Niesklasyfikowane Valore
- Niesklasyfikowane Accucold
- Niesklasyfikowane Sun Joe
- Niesklasyfikowane Perfecta
- Niesklasyfikowane Doro
- Niesklasyfikowane Sagem
- Niesklasyfikowane Cricut
- Niesklasyfikowane Hähnel
- Niesklasyfikowane EWT
- Niesklasyfikowane Enduro
- Niesklasyfikowane Aukey
- Niesklasyfikowane Ernesto
- Niesklasyfikowane KlikaanKlikuit
- Niesklasyfikowane Easypix
- Niesklasyfikowane Ei Electronics
- Niesklasyfikowane Simplified MFG
- Niesklasyfikowane Mellerware
- Niesklasyfikowane Silva
- Niesklasyfikowane Tacklife
- Niesklasyfikowane Energenie
- Niesklasyfikowane Heinner
- Niesklasyfikowane Termozeta
- Niesklasyfikowane Bella
- Niesklasyfikowane Palson
- Niesklasyfikowane Eldom
- Niesklasyfikowane Valeton
- Niesklasyfikowane Jocca
- Niesklasyfikowane Nilox
- Niesklasyfikowane Tiptop Audio
- Niesklasyfikowane Sonos
- Niesklasyfikowane Summit Audio
- Niesklasyfikowane SKS
- Niesklasyfikowane Musway
- Niesklasyfikowane Kensington
- Niesklasyfikowane Nautilus
- Niesklasyfikowane Cresta
- Niesklasyfikowane Maxxmee
- Niesklasyfikowane Brigmton
- Niesklasyfikowane Sunstech
- Niesklasyfikowane Smith & Wesson
- Niesklasyfikowane Reich
- Niesklasyfikowane Defy
- Niesklasyfikowane Stiebel Eltron
- Niesklasyfikowane DeLock
- Niesklasyfikowane Avalon
- Niesklasyfikowane Plant Craft
- Niesklasyfikowane Dubatti
- Niesklasyfikowane Bionaire
- Niesklasyfikowane Sylvania
- Niesklasyfikowane Campomatic
- Niesklasyfikowane Patton
- Niesklasyfikowane Igloo
- Niesklasyfikowane Senco
- Niesklasyfikowane Tork
- Niesklasyfikowane Techly
- Niesklasyfikowane Vaude
- Niesklasyfikowane GlobalTronics
- Niesklasyfikowane Sunny
- Niesklasyfikowane Inglesina
- Niesklasyfikowane BBB
- Niesklasyfikowane BlueBuilt
- Niesklasyfikowane Gazelle
- Niesklasyfikowane Nibe
- Niesklasyfikowane Damixa
- Niesklasyfikowane Da-Lite
- Niesklasyfikowane Trebs
- Niesklasyfikowane Ednet
- Niesklasyfikowane Luxor
- Niesklasyfikowane Bowflex
- Niesklasyfikowane Visage
- Niesklasyfikowane Celestron
- Niesklasyfikowane CaterCool
- Niesklasyfikowane Matrox
- Niesklasyfikowane Rangemaster
- Niesklasyfikowane Maktec
- Niesklasyfikowane Connect IT
- Niesklasyfikowane Steren
- Niesklasyfikowane Eico
- Niesklasyfikowane Hansa
- Niesklasyfikowane Nero
- Niesklasyfikowane Kubo
- Niesklasyfikowane Exagerate
- Niesklasyfikowane Air King
- Niesklasyfikowane Tanaka
- Niesklasyfikowane Gossen
- Niesklasyfikowane Elba
- Niesklasyfikowane Flir
- Niesklasyfikowane Paidi
- Niesklasyfikowane KiddyGuard
- Niesklasyfikowane Livarno
- Niesklasyfikowane Soehnle
- Niesklasyfikowane Barkan
- Niesklasyfikowane Coby
- Niesklasyfikowane Royal Sovereign
- Niesklasyfikowane King
- Niesklasyfikowane Maxwell
- Niesklasyfikowane AcuRite
- Niesklasyfikowane Envivo
- Niesklasyfikowane Gustavsberg
- Niesklasyfikowane Galaxy Audio
- Niesklasyfikowane ESYLUX
- Niesklasyfikowane Ventus
- Niesklasyfikowane Melinera
- Niesklasyfikowane TOTO
- Niesklasyfikowane Fisher Price
- Niesklasyfikowane Technoline
- Niesklasyfikowane Osann
- Niesklasyfikowane Lindam
- Niesklasyfikowane Goliath
- Niesklasyfikowane Yamato
- Niesklasyfikowane Vivo
- Niesklasyfikowane Dorma
- Niesklasyfikowane Belgacom
- Niesklasyfikowane SEB
- Niesklasyfikowane Pelican
- Niesklasyfikowane Malmbergs
- Niesklasyfikowane Phoenix
- Niesklasyfikowane AV:link
- Niesklasyfikowane Power Craft
- Niesklasyfikowane Otolift
- Niesklasyfikowane GBC
- Niesklasyfikowane Prenatal
- Niesklasyfikowane Champion
- Niesklasyfikowane Tvilum
- Niesklasyfikowane Heylo
- Niesklasyfikowane TacTic
- Niesklasyfikowane Nolte
- Niesklasyfikowane G3
- Niesklasyfikowane Peach
- Niesklasyfikowane Trixie
- Niesklasyfikowane Finnlo
- Niesklasyfikowane Lescha
- Niesklasyfikowane Capital Sports
- Niesklasyfikowane Buffalo
- Niesklasyfikowane Vello
- Niesklasyfikowane Jenn-Air
- Niesklasyfikowane R-Vent
- Niesklasyfikowane Woood
- Niesklasyfikowane Audiovox
- Niesklasyfikowane Carpigiani
- Niesklasyfikowane Renegade
- Niesklasyfikowane Davis
- Niesklasyfikowane ICU
- Niesklasyfikowane Daitsu
- Niesklasyfikowane Edesa
- Niesklasyfikowane Farberware
- Niesklasyfikowane Ufesa
- Niesklasyfikowane CasaFan
- Niesklasyfikowane Milectric
- Niesklasyfikowane Vicks
- Niesklasyfikowane Yaesu
- Niesklasyfikowane Walkstool
- Niesklasyfikowane Macally
- Niesklasyfikowane Apogee
- Niesklasyfikowane Arlo
- Niesklasyfikowane Nest
- Niesklasyfikowane Kwantum
- Niesklasyfikowane Olimpia Splendid
- Niesklasyfikowane Safescan
- Niesklasyfikowane Pyle Pro
- Niesklasyfikowane Wehkamp
- Niesklasyfikowane Svedbergs
- Niesklasyfikowane Osprey
- Niesklasyfikowane Bunn
- Niesklasyfikowane Ninebot
- Niesklasyfikowane Siedle
- Niesklasyfikowane Cilio
- Niesklasyfikowane LaCie
- Niesklasyfikowane Itho-Daalderop
- Niesklasyfikowane Maul
- Niesklasyfikowane BabyOno
- Niesklasyfikowane Karibu
- Niesklasyfikowane Pericles
- Niesklasyfikowane Troy-Bilt
- Niesklasyfikowane Laica
- Niesklasyfikowane Rusta
- Niesklasyfikowane Samac
- Niesklasyfikowane Brevi
- Niesklasyfikowane SMA
- Niesklasyfikowane Autotek
- Niesklasyfikowane Hive
- Niesklasyfikowane Brabantia
- Niesklasyfikowane AS - Schwabe
- Niesklasyfikowane Fissler
- Niesklasyfikowane Kayoba
- Niesklasyfikowane Wamsler
- Niesklasyfikowane MB Quart
- Niesklasyfikowane Valcom
- Niesklasyfikowane Switel
- Niesklasyfikowane Bopita
- Niesklasyfikowane FireAngel
- Niesklasyfikowane Duux
- Niesklasyfikowane Chacon
- Niesklasyfikowane Astro
- Niesklasyfikowane Imetec
- Niesklasyfikowane InFocus
- Niesklasyfikowane Bigben
- Niesklasyfikowane Topcraft
- Niesklasyfikowane Kraftwerk
- Niesklasyfikowane Naish
- Niesklasyfikowane Festo
- Niesklasyfikowane Massive
- Niesklasyfikowane Barska
- Niesklasyfikowane Weihrauch Sport
- Niesklasyfikowane Blaze
- Niesklasyfikowane Hombli
- Niesklasyfikowane Martha Stewart
- Niesklasyfikowane Milan
- Niesklasyfikowane Lümme
- Niesklasyfikowane Springfree
- Niesklasyfikowane Ansco
- Niesklasyfikowane Glem Gas
- Niesklasyfikowane Goodram
- Niesklasyfikowane MADE
- Niesklasyfikowane Noma
- Niesklasyfikowane IDance
- Niesklasyfikowane Habitat
- Niesklasyfikowane Body Sculpture
- Niesklasyfikowane Maxview
- Niesklasyfikowane Yongnuo
- Niesklasyfikowane Gamma
- Niesklasyfikowane Proctor Silex
- Niesklasyfikowane Elite
- Niesklasyfikowane Zodiac
- Niesklasyfikowane BOHLT
- Niesklasyfikowane Handicare
- Niesklasyfikowane Simplecom
- Niesklasyfikowane Primo
- Niesklasyfikowane Rocketfish
- Niesklasyfikowane Alba
- Niesklasyfikowane Baninni
- Niesklasyfikowane Naxa
- Niesklasyfikowane Nemef
- Niesklasyfikowane Atlantic
- Niesklasyfikowane RugGear
- Niesklasyfikowane Umidigi
- Niesklasyfikowane Saro
- Niesklasyfikowane Millenium
- Niesklasyfikowane Vogue
- Niesklasyfikowane Grixx
- Niesklasyfikowane Topeak
- Niesklasyfikowane SuperFish
- Niesklasyfikowane Luvion
- Niesklasyfikowane Aqua Joe
- Niesklasyfikowane Innovaphone
- Niesklasyfikowane Intel
- Niesklasyfikowane Mamiya
- Niesklasyfikowane Zuiver
- Niesklasyfikowane Fantec
- Niesklasyfikowane Konig
- Niesklasyfikowane Valueline
- Niesklasyfikowane Active Era
- Niesklasyfikowane Trigano
- Niesklasyfikowane Sweex
- Niesklasyfikowane Busch And Müller
- Niesklasyfikowane Ices
- Niesklasyfikowane Vizio
- Niesklasyfikowane Schuberth
- Niesklasyfikowane Cello
- Niesklasyfikowane RDL
- Niesklasyfikowane Austrian Audio
- Niesklasyfikowane Eberspacher
- Niesklasyfikowane Kress
- Niesklasyfikowane Zehnder
- Niesklasyfikowane Laurastar
- Niesklasyfikowane Mx Onda
- Niesklasyfikowane Wacker Neuson
- Niesklasyfikowane Nûby
- Niesklasyfikowane Xterra
- Niesklasyfikowane Fredenstein
- Niesklasyfikowane Dolmar
- Niesklasyfikowane Invacare
- Niesklasyfikowane Nanni
- Niesklasyfikowane Fuji
- Niesklasyfikowane Swissonic
- Niesklasyfikowane Schütte
- Niesklasyfikowane BRIO
- Niesklasyfikowane Aruba
- Niesklasyfikowane RGV
- Niesklasyfikowane Elkay
- Niesklasyfikowane IHealth
- Niesklasyfikowane Hapro
- Niesklasyfikowane Tamiya
- Niesklasyfikowane Logicom
- Niesklasyfikowane Alfen
- Niesklasyfikowane Sound Machines
- Niesklasyfikowane Team
- Niesklasyfikowane Nikkei
- Niesklasyfikowane Petsafe
- Niesklasyfikowane Nelson
- Niesklasyfikowane TranzX
- Niesklasyfikowane Aviom
- Niesklasyfikowane UPM
- Niesklasyfikowane Happy Plugs
- Niesklasyfikowane Duro
- Niesklasyfikowane T'nB
- Niesklasyfikowane Ematic
- Niesklasyfikowane Finder
- Niesklasyfikowane Levoit
- Niesklasyfikowane Palm
- Niesklasyfikowane QSC
- Niesklasyfikowane Phonak
- Niesklasyfikowane Faber
- Niesklasyfikowane Cardiostrong
- Niesklasyfikowane Hartan
- Niesklasyfikowane Hamax
- Niesklasyfikowane Xavax
- Niesklasyfikowane Emmaljunga
- Niesklasyfikowane Fantini Cosmi
- Niesklasyfikowane X4-Tech
- Niesklasyfikowane ZAZU
- Niesklasyfikowane Countryman
- Niesklasyfikowane Minolta
- Niesklasyfikowane Aerial
- Niesklasyfikowane Victor
- Niesklasyfikowane Zagg
- Niesklasyfikowane ESI
- Niesklasyfikowane Edgestar
- Niesklasyfikowane Orbis
- Niesklasyfikowane ACE
- Niesklasyfikowane Maxicool
- Niesklasyfikowane For_Q
- Niesklasyfikowane Avocor
- Niesklasyfikowane Lanzar
- Niesklasyfikowane DoorBird
- Niesklasyfikowane FoodSaver
- Niesklasyfikowane Vroomshoop
- Niesklasyfikowane McGregor
- Niesklasyfikowane Rain Bird
- Niesklasyfikowane Leitz
- Niesklasyfikowane Nvidia
- Niesklasyfikowane Irritrol
- Niesklasyfikowane Boneco
- Niesklasyfikowane Basbau
- Niesklasyfikowane CaterChef
- Niesklasyfikowane Echowell
- Niesklasyfikowane Kasda
- Niesklasyfikowane Patching Panda
- Niesklasyfikowane NEP
- Niesklasyfikowane Veho
- Niesklasyfikowane Kambrook
- Niesklasyfikowane Nevadent
- Niesklasyfikowane Plum
- Niesklasyfikowane Grasslin
- Niesklasyfikowane Puky
- Niesklasyfikowane GFI System
- Niesklasyfikowane Roadstar
- Niesklasyfikowane Humax
- Niesklasyfikowane Vaddio
- Niesklasyfikowane Berner
- Niesklasyfikowane Swarovski Optik
- Niesklasyfikowane Gira
- Niesklasyfikowane Sachtler
- Niesklasyfikowane Seagate
- Niesklasyfikowane Golden Age Project
- Niesklasyfikowane Britax-Romer
- Niesklasyfikowane Technicolor
- Niesklasyfikowane Bravilor Bonamat
- Niesklasyfikowane Blue
- Niesklasyfikowane Efbe-schott
- Niesklasyfikowane Brinsea
- Niesklasyfikowane Genexis
- Niesklasyfikowane Genelec
- Niesklasyfikowane Maxxter
- Niesklasyfikowane Inspire
- Niesklasyfikowane Apart
- Niesklasyfikowane Venta
- Niesklasyfikowane Anchor Audio
- Niesklasyfikowane 4moms
- Niesklasyfikowane Wolf
- Niesklasyfikowane Dantherm
- Niesklasyfikowane Interlogix
- Niesklasyfikowane Projecta
- Niesklasyfikowane Dnt
- Niesklasyfikowane Lyman
- Niesklasyfikowane Genaray
- Niesklasyfikowane Balance
- Niesklasyfikowane Qualcast
- Niesklasyfikowane Cablexpert
- Niesklasyfikowane Iomega
- Niesklasyfikowane Phil And Teds
- Niesklasyfikowane Tornado
- Niesklasyfikowane Stelton
- Niesklasyfikowane Mr Handsfree
- Niesklasyfikowane Pattfield
- Niesklasyfikowane Joovy
- Niesklasyfikowane Bodum
- Niesklasyfikowane Saitek
- Niesklasyfikowane DAS Audio
- Niesklasyfikowane Vestfrost
- Niesklasyfikowane Leen Bakker
- Niesklasyfikowane OSO
- Niesklasyfikowane Roxio
- Niesklasyfikowane Fito
- Niesklasyfikowane Jotul
- Niesklasyfikowane Shoprider
- Niesklasyfikowane WHALE
- Niesklasyfikowane Shuttle
- Niesklasyfikowane Furuno
- Niesklasyfikowane HQ
- Niesklasyfikowane Max
- Niesklasyfikowane Clage
- Niesklasyfikowane Vorago
- Niesklasyfikowane GMB Gaming
- Niesklasyfikowane Cre8audio
- Niesklasyfikowane Nanlite
- Niesklasyfikowane Kupper
- Niesklasyfikowane Ledger
- Niesklasyfikowane Koenig
- Niesklasyfikowane Contour
- Niesklasyfikowane BakkerElkhuizen
- Niesklasyfikowane Lupilu
- Niesklasyfikowane Outdoorchef
- Niesklasyfikowane Boyo
- Niesklasyfikowane IKRA
- Niesklasyfikowane Turmix
- Niesklasyfikowane Fakir
- Niesklasyfikowane IOttie
- Niesklasyfikowane Verizon
- Niesklasyfikowane Trio Lighting
- Niesklasyfikowane Integra
- Niesklasyfikowane Upo
- Niesklasyfikowane Vitamix
- Niesklasyfikowane Cadel
- Niesklasyfikowane Ipevo
- Niesklasyfikowane Miggo
- Niesklasyfikowane Urrea
- Niesklasyfikowane Iget
- Niesklasyfikowane Emtec
- Niesklasyfikowane Ranex
- Niesklasyfikowane Russound
- Niesklasyfikowane Truper
- Niesklasyfikowane ISDT
- Niesklasyfikowane Debel
- Niesklasyfikowane Abac
- Niesklasyfikowane Stannah
- Niesklasyfikowane Comelit
- Niesklasyfikowane Slik
- Niesklasyfikowane Celly
- Niesklasyfikowane Skan Holz
- Niesklasyfikowane Comica
- Niesklasyfikowane Tommee Tippee
- Niesklasyfikowane Globo
- Niesklasyfikowane EverFocus
- Niesklasyfikowane Audient
- Niesklasyfikowane Adesso
- Niesklasyfikowane Infantino
- Niesklasyfikowane C3
- Niesklasyfikowane EMSA
- Niesklasyfikowane Eurospec
- Niesklasyfikowane Waldbeck
- Niesklasyfikowane Natuzzi
- Niesklasyfikowane Satel
- Niesklasyfikowane Bazooka
- Niesklasyfikowane K&K Sound
- Niesklasyfikowane Dutchbone
- Niesklasyfikowane Fanvil
- Niesklasyfikowane Noise Engineering
- Niesklasyfikowane PAC
- Niesklasyfikowane Beretta
- Niesklasyfikowane Wentronic
- Niesklasyfikowane Peerless
- Niesklasyfikowane Xtreme
- Niesklasyfikowane RAVPower
- Niesklasyfikowane Hooker
- Niesklasyfikowane IHome
- Niesklasyfikowane Luxman
- Niesklasyfikowane Gitzo
- Niesklasyfikowane M-Audio
- Niesklasyfikowane SeaLife
- Niesklasyfikowane Nesco
- Niesklasyfikowane Wago
- Niesklasyfikowane AIC
- Niesklasyfikowane Concept2
- Niesklasyfikowane Brydge
- Niesklasyfikowane Selec
- Niesklasyfikowane Aiphone
- Niesklasyfikowane Tivoli Audio
- Niesklasyfikowane JETI
- Niesklasyfikowane Waves
- Niesklasyfikowane EQ3
- Niesklasyfikowane Karlik
- Niesklasyfikowane Comark
- Niesklasyfikowane Coline
- Niesklasyfikowane N8WERK
- Niesklasyfikowane Petri
- Niesklasyfikowane Calex
- Niesklasyfikowane REV
- Niesklasyfikowane Skullcandy
- Niesklasyfikowane Dymond
- Niesklasyfikowane 4smarts
- Niesklasyfikowane Learning Resources
- Niesklasyfikowane Xaoc
- Niesklasyfikowane SVAT
- Niesklasyfikowane Qute
- Niesklasyfikowane BabyGO
- Niesklasyfikowane Schwinn
- Niesklasyfikowane Friedland
- Niesklasyfikowane Proaim
- Niesklasyfikowane Megableu
- Niesklasyfikowane Nexxt
- Niesklasyfikowane Coleman
- Niesklasyfikowane Magic Care
- Niesklasyfikowane Raclet
- Niesklasyfikowane Weishaupt
- Niesklasyfikowane Glock
- Niesklasyfikowane Linn
- Niesklasyfikowane Iluv
- Niesklasyfikowane Monoprice
- Niesklasyfikowane Echo
- Niesklasyfikowane Croozer
- Niesklasyfikowane TELEX
- Niesklasyfikowane Dynamic
- Niesklasyfikowane Sauter
- Niesklasyfikowane Eve Audio
- Niesklasyfikowane Café
- Niesklasyfikowane Adam Hall
- Niesklasyfikowane Murr Elektronik
- Niesklasyfikowane Baja Mobility
- Niesklasyfikowane Yorkville
- Niesklasyfikowane Neewer
- Niesklasyfikowane Meross
- Niesklasyfikowane Könner & Söhnen
- Niesklasyfikowane Klavis
- Niesklasyfikowane Manitowoc
- Niesklasyfikowane Aconatic
- Niesklasyfikowane Advance
- Niesklasyfikowane Artecta
- Niesklasyfikowane NordicTrack
- Niesklasyfikowane Eliminator Lighting
- Niesklasyfikowane Buzz Rack
- Niesklasyfikowane CAME-TV
- Niesklasyfikowane ColorKey
- Niesklasyfikowane ChyTV
- Niesklasyfikowane Holosun
- Niesklasyfikowane Panamax
- Niesklasyfikowane Sonifex
- Niesklasyfikowane TV One
- Niesklasyfikowane Vertex
- Niesklasyfikowane Home Easy
- Niesklasyfikowane Basil
- Niesklasyfikowane Munchkin
- Niesklasyfikowane Nxg
- Niesklasyfikowane AGM
- Niesklasyfikowane Ambient Recording
- Niesklasyfikowane Bruder Mannesmann
- Niesklasyfikowane Autodesk
- Niesklasyfikowane Diana
- Niesklasyfikowane Tandberg Data
- Niesklasyfikowane Fostex
- Niesklasyfikowane Viridian
- Niesklasyfikowane Plustek
- Niesklasyfikowane Prowise
- Niesklasyfikowane Mousetrapper
- Niesklasyfikowane SKROSS
- Niesklasyfikowane Sikkens
- Niesklasyfikowane DEXP
- Niesklasyfikowane Burris
- Niesklasyfikowane GolfBuddy
- Niesklasyfikowane Lynx
- Niesklasyfikowane Vantec
- Niesklasyfikowane FBT
- Niesklasyfikowane Tiptel
- Niesklasyfikowane Thermor
- Niesklasyfikowane NodOn
- Niesklasyfikowane Edge
- Niesklasyfikowane Endorphin.es
- Niesklasyfikowane Crofton
- Niesklasyfikowane MIPRO
- Niesklasyfikowane Bravilor
- Niesklasyfikowane Bracketron
- Niesklasyfikowane Solid State Logic
- Niesklasyfikowane Pointer
- Niesklasyfikowane XYZprinting
- Niesklasyfikowane Computherm
- Niesklasyfikowane ICE Watch
- Niesklasyfikowane Carmen
- Niesklasyfikowane MTM
- Niesklasyfikowane De Buyer
- Niesklasyfikowane Metapace
- Niesklasyfikowane Exo-Terra
- Niesklasyfikowane Neets
- Niesklasyfikowane OutNowTech
- Niesklasyfikowane NAV-TV
- Niesklasyfikowane Wooden Camera
- Niesklasyfikowane Maclaren
- Niesklasyfikowane AdHoc
- Niesklasyfikowane AudioQuest
- Niesklasyfikowane Powerblade
- Niesklasyfikowane HiFi ROSE
- Niesklasyfikowane Hayter
- Niesklasyfikowane Gianni Ferrari
- Niesklasyfikowane OSD Audio
- Niesklasyfikowane WMD
- Niesklasyfikowane Simpark
- Niesklasyfikowane Beafon
- Niesklasyfikowane Maruyama
- Niesklasyfikowane 3B
- Niesklasyfikowane Ergotron
- Niesklasyfikowane Zepter
- Niesklasyfikowane Giordani
- Niesklasyfikowane Black Lion Audio
- Niesklasyfikowane Cowon
- Niesklasyfikowane Soundstream
- Niesklasyfikowane Cruz
- Niesklasyfikowane Khind
- Niesklasyfikowane Crayola
- Niesklasyfikowane Fischer
- Niesklasyfikowane Xoro
- Niesklasyfikowane Maze
- Niesklasyfikowane CTOUCH
- Niesklasyfikowane Adastra
- Niesklasyfikowane Meister Craft
- Niesklasyfikowane Meade
- Niesklasyfikowane Unify
- Niesklasyfikowane Yeastar
- Niesklasyfikowane Laserworld
- Niesklasyfikowane Billow
- Niesklasyfikowane Chuango
- Niesklasyfikowane Kelty
- Niesklasyfikowane West Elm
- Niesklasyfikowane Keter
- Niesklasyfikowane Ozone
- Niesklasyfikowane Clearblue
- Niesklasyfikowane Garden Lights
- Niesklasyfikowane ETiger
- Niesklasyfikowane Bison
- Niesklasyfikowane Jabsco
- Niesklasyfikowane Foxconn
- Niesklasyfikowane Icy Dock
- Niesklasyfikowane Wasco
- Niesklasyfikowane Make Noise
- Niesklasyfikowane Telstra
- Niesklasyfikowane TeachLogic
- Niesklasyfikowane Sole Fitness
- Niesklasyfikowane Lumag
- Niesklasyfikowane Charge Amps
- Niesklasyfikowane Berker
- Niesklasyfikowane Eufab
- Niesklasyfikowane Manfrotto
- Niesklasyfikowane Crucial
- Niesklasyfikowane Premier
- Niesklasyfikowane Aeon Labs
- Niesklasyfikowane Ibm
- Niesklasyfikowane Unilux
- Niesklasyfikowane Citronic
- Niesklasyfikowane Pontec
- Niesklasyfikowane TEF
- Niesklasyfikowane Maxell
- Niesklasyfikowane Cosatto
- Niesklasyfikowane Weasy
- Niesklasyfikowane Datacard
- Niesklasyfikowane Nordea
- Niesklasyfikowane Life Gear
- Niesklasyfikowane ZYCOO
- Niesklasyfikowane Macrom
- Niesklasyfikowane Kontakt Chemie
- Niesklasyfikowane Purell
- Niesklasyfikowane Riccar
- Niesklasyfikowane BabyHome
- Niesklasyfikowane Contax
- Niesklasyfikowane OpenVox
- Niesklasyfikowane Atdec
- Niesklasyfikowane Batavia
- Niesklasyfikowane Klarfit
- Niesklasyfikowane Marklin
- Niesklasyfikowane Bruynzeel
- Niesklasyfikowane MSpa
- Niesklasyfikowane View Quest
- Niesklasyfikowane Drayton
- Niesklasyfikowane Titanwolf
- Niesklasyfikowane Uplink
- Niesklasyfikowane Mybeo
- Niesklasyfikowane CSL
- Niesklasyfikowane Bearware
- Niesklasyfikowane Perfect Christmas
- Niesklasyfikowane Core SWX
- Niesklasyfikowane Formuler
- Niesklasyfikowane Oertli
- Niesklasyfikowane UX
- Niesklasyfikowane Moog
- Niesklasyfikowane Nerf
- Niesklasyfikowane KidKraft
- Niesklasyfikowane Metrel
- Niesklasyfikowane Multimetrix
- Niesklasyfikowane Solid
- Niesklasyfikowane Morris
- Niesklasyfikowane 8BitDo
- Niesklasyfikowane Ruger
- Niesklasyfikowane Hubelino
- Niesklasyfikowane Gerni
- Niesklasyfikowane Jupio
- Niesklasyfikowane PCE
- Niesklasyfikowane MedFolio
- Niesklasyfikowane Warm Audio
- Niesklasyfikowane Blaser
- Niesklasyfikowane Heatit
- Niesklasyfikowane ProForm
- Niesklasyfikowane UTEPO
- Niesklasyfikowane Purpleline
- Niesklasyfikowane Think Tank
- Niesklasyfikowane Portech
- Niesklasyfikowane Lec
- Niesklasyfikowane Geomag
- Niesklasyfikowane LTC
- Niesklasyfikowane Koala
- Niesklasyfikowane Drawmer
- Niesklasyfikowane Audeze
- Niesklasyfikowane Blue Sky
- Niesklasyfikowane Dunlop
- Niesklasyfikowane Valeo
- Niesklasyfikowane Velbus
- Niesklasyfikowane Babyzen
- Niesklasyfikowane Woonexpress
- Niesklasyfikowane IQAir
- Niesklasyfikowane Sanus Systems
- Niesklasyfikowane BabyDan
- Niesklasyfikowane Tormatic
- Niesklasyfikowane After Later Audio
- Niesklasyfikowane Aqara
- Niesklasyfikowane 2hp
- Niesklasyfikowane Energizer
- Niesklasyfikowane IXS
- Niesklasyfikowane Samlex
- Niesklasyfikowane Navionics
- Niesklasyfikowane Zalman
- Niesklasyfikowane Turbo Air
- Niesklasyfikowane Zega
- Niesklasyfikowane Leatherman
- Niesklasyfikowane CreativeWorKs
- Niesklasyfikowane Horizon
- Niesklasyfikowane Ultimate Support
- Niesklasyfikowane Rösle
- Niesklasyfikowane Interphone
- Niesklasyfikowane Prince
- Niesklasyfikowane AXI
- Niesklasyfikowane Inter-Tech
- Niesklasyfikowane Thomann
- Niesklasyfikowane Holzmann
- Niesklasyfikowane EMG
- Niesklasyfikowane James
- Niesklasyfikowane Bicker Elektronik
- Niesklasyfikowane Iadea
- Niesklasyfikowane Blizzard
- Niesklasyfikowane Nimble
- Niesklasyfikowane SIIG
- Niesklasyfikowane Reginox
- Niesklasyfikowane BIOS Medical
- Niesklasyfikowane Advantech
- Niesklasyfikowane PSSO
- Niesklasyfikowane Wise
- Niesklasyfikowane SIG Sauer
- Niesklasyfikowane Merkel
- Niesklasyfikowane Biohort
- Niesklasyfikowane Crest Audio
- Niesklasyfikowane Globe
- Niesklasyfikowane Rossi
- Niesklasyfikowane Hercules
- Niesklasyfikowane Grace Design
- Niesklasyfikowane Contour Design
- Niesklasyfikowane Propellerhead
- Niesklasyfikowane Nanuk
- Niesklasyfikowane Digital Watchdog
- Niesklasyfikowane Riviera And Bar
- Niesklasyfikowane Apelson
- Niesklasyfikowane Kreiling
- Niesklasyfikowane Xantech
- Niesklasyfikowane Scanstrut
- Niesklasyfikowane Marker
- Niesklasyfikowane Kohler
- Niesklasyfikowane Safco
- Niesklasyfikowane Xunzel
- Niesklasyfikowane Oklahoma Sound
- Niesklasyfikowane Thames & Kosmos
- Niesklasyfikowane Betso
- Niesklasyfikowane Fortia
- Niesklasyfikowane Moen
- Niesklasyfikowane Babysense
- Niesklasyfikowane Namco Bandai Games
- Niesklasyfikowane Sealy
- Niesklasyfikowane Wet Sounds
- Niesklasyfikowane CRU
- Niesklasyfikowane Avantone Pro
- Niesklasyfikowane Umarex
- Niesklasyfikowane Televés
- Niesklasyfikowane AbleNet
- Niesklasyfikowane Exalux
- Niesklasyfikowane IBasso
- Niesklasyfikowane Gtech
- Niesklasyfikowane Leap Frog
- Niesklasyfikowane Sightmark
- Niesklasyfikowane Eissound
- Niesklasyfikowane Ganz
- Niesklasyfikowane Hughes & Kettner
- Niesklasyfikowane Manley
- Niesklasyfikowane Micro Matic
- Niesklasyfikowane Thermomate
- Niesklasyfikowane Steiner
- Niesklasyfikowane Graphite
- Niesklasyfikowane Gosund
- Niesklasyfikowane HMS Premium
- Niesklasyfikowane TVLogic
- Niesklasyfikowane Gamber-Johnson
- Niesklasyfikowane Acard
- Niesklasyfikowane Burigotto
- Niesklasyfikowane T.I.P.
- Niesklasyfikowane Gra-Vue
- Niesklasyfikowane BASSBOSS
- Niesklasyfikowane Doffler
- Niesklasyfikowane On-Stage
- Niesklasyfikowane SurgeX
- Niesklasyfikowane MuxLab
- Niesklasyfikowane Sencys
- Niesklasyfikowane Norton Clipper
- Niesklasyfikowane Extron
- Niesklasyfikowane Avocent
- Niesklasyfikowane Geze
- Niesklasyfikowane RTS
- Niesklasyfikowane Ontech
- Niesklasyfikowane HyperJuice
- Niesklasyfikowane Swingline
- Niesklasyfikowane RaySafe
- Niesklasyfikowane Di4
- Niesklasyfikowane Hohner
- Niesklasyfikowane Ocean Matrix
- Niesklasyfikowane MAK
- Niesklasyfikowane Dobot
- Niesklasyfikowane Ocean Way Audio
- Niesklasyfikowane Nearity
- Niesklasyfikowane Comprehensive
- Niesklasyfikowane Sanli
- Niesklasyfikowane Husky
- Niesklasyfikowane Philos
- Niesklasyfikowane Legamaster
- Niesklasyfikowane Siemon
- Niesklasyfikowane Block & Block
- Niesklasyfikowane Brondell
- Niesklasyfikowane NutriBullet
- Niesklasyfikowane Four Hands
- Niesklasyfikowane Oben
- Niesklasyfikowane ASA
- Niesklasyfikowane Thronmax
- Niesklasyfikowane Botex
- Niesklasyfikowane Maxsa
- Niesklasyfikowane Tripp
- Niesklasyfikowane TRIUS
- Niesklasyfikowane Ankarsrum
- Niesklasyfikowane Etymotic
- Niesklasyfikowane Fine Dine
- Niesklasyfikowane ClearOne
- Niesklasyfikowane Superrollo
- Niesklasyfikowane Goldtouch
- Niesklasyfikowane Gamewright
- Niesklasyfikowane Braun Phototechnik
- Niesklasyfikowane Black Decker
- Niesklasyfikowane SXT
- Niesklasyfikowane Essenza
- Niesklasyfikowane Seecode
- Niesklasyfikowane Thomas
- Niesklasyfikowane Rugged Geek
- Niesklasyfikowane Dave Smith
- Niesklasyfikowane Skymaster
- Niesklasyfikowane Gardol
- Niesklasyfikowane Helix
- Niesklasyfikowane TFA Dostmann
- Niesklasyfikowane Durable
- Niesklasyfikowane Zenza Bronica
- Niesklasyfikowane Spypoint
- Niesklasyfikowane Suprema
- Niesklasyfikowane Ziehl
- Niesklasyfikowane VAIS
- Niesklasyfikowane Perma
- Niesklasyfikowane Scandes
- Niesklasyfikowane Testec
- Niesklasyfikowane Quadro
- Niesklasyfikowane Enovate
- Niesklasyfikowane Lofrans
- Niesklasyfikowane Winegard
- Niesklasyfikowane Pigtronix
- Niesklasyfikowane ProTeam
- Niesklasyfikowane Wagner SprayTech
- Niesklasyfikowane Libec
- Niesklasyfikowane Pardini
- Niesklasyfikowane KWC
- Niesklasyfikowane Soul
- Niesklasyfikowane Laney
- Niesklasyfikowane Compex
- Niesklasyfikowane Theragun
- Niesklasyfikowane Weil
- Niesklasyfikowane Plantiflor
- Niesklasyfikowane LAS
- Niesklasyfikowane Rosseto
- Niesklasyfikowane Redrock Micro
- Niesklasyfikowane Motu
- Niesklasyfikowane Kata
- Niesklasyfikowane Minix
- Niesklasyfikowane Lazer
- Niesklasyfikowane EarthQuaker Devices
- Niesklasyfikowane The Grainfather
- Niesklasyfikowane Kessler
- Niesklasyfikowane Emga
- Niesklasyfikowane Briggs & Stratton
- Niesklasyfikowane USAopoly
- Niesklasyfikowane Gami
- Niesklasyfikowane Igloohome
- Niesklasyfikowane Rothenberger
- Niesklasyfikowane Creamsource
- Niesklasyfikowane Kenko
- Niesklasyfikowane Zennio
- Niesklasyfikowane Vixen
- Niesklasyfikowane B-tech
- Niesklasyfikowane Praktica
- Niesklasyfikowane Elinchrom
- Niesklasyfikowane Boori
- Niesklasyfikowane CamRanger
- Niesklasyfikowane Hasselblad
- Niesklasyfikowane Madrix
- Niesklasyfikowane Q Acoustics
- Niesklasyfikowane Spacedec
- Niesklasyfikowane Auray
- Niesklasyfikowane Bontempi
- Niesklasyfikowane Furman
- Niesklasyfikowane Summer Infant
- Niesklasyfikowane Cooper & Quint
- Niesklasyfikowane Deltex
- Niesklasyfikowane Adax
- Niesklasyfikowane Xplora
- Niesklasyfikowane Eonon
- Niesklasyfikowane Calligaris .com
- Niesklasyfikowane SMC
- Niesklasyfikowane Ibico
- Niesklasyfikowane OXO Good Grips
- Niesklasyfikowane Exit Toys
- Niesklasyfikowane Triton
- Niesklasyfikowane Profizelt24
- Niesklasyfikowane Helios Preisser
- Niesklasyfikowane YSI
- Niesklasyfikowane Yeyian
- Niesklasyfikowane Paulmann
- Niesklasyfikowane Nitek
- Niesklasyfikowane Snoes
- Niesklasyfikowane Alpatronix
- Niesklasyfikowane Labelmate
- Niesklasyfikowane Martin Audio
- Niesklasyfikowane Schertler
- Niesklasyfikowane Teradek
- Niesklasyfikowane Sissel
- Niesklasyfikowane Kunath
- Niesklasyfikowane Penclic
- Niesklasyfikowane SolarEdge
- Niesklasyfikowane GOgroove
- Niesklasyfikowane ViewCast
- Niesklasyfikowane Crown
- Niesklasyfikowane Kogan
- Niesklasyfikowane Tennsco
- Niesklasyfikowane FireKing
- Niesklasyfikowane RAM Mounts
- Niesklasyfikowane Novus
- Niesklasyfikowane Getac
- Niesklasyfikowane Arebos
- Niesklasyfikowane Kreg
- Niesklasyfikowane Bentley
- Niesklasyfikowane Morningstar
- Niesklasyfikowane DMax
- Niesklasyfikowane Backyard Discovery
- Niesklasyfikowane Minuteman
- Niesklasyfikowane Ortofon
- Niesklasyfikowane RéVive
- Niesklasyfikowane Mega
- Niesklasyfikowane Star Micronics
- Niesklasyfikowane Woodland Scenics
- Niesklasyfikowane Chapin
- Niesklasyfikowane Morel
- Niesklasyfikowane J. Rockett Audio Designs
- Niesklasyfikowane Pancontrol
- Niesklasyfikowane Satisfyer
- Niesklasyfikowane Hämmerli
- Niesklasyfikowane Verto
- Niesklasyfikowane Soma
- Niesklasyfikowane Posiflex
- Niesklasyfikowane Little Giant
- Niesklasyfikowane Point 65
- Niesklasyfikowane ReTrak
- Niesklasyfikowane Avantree
- Niesklasyfikowane LYYT
- Niesklasyfikowane Old Blood Noise
- Niesklasyfikowane Vulcan
- Niesklasyfikowane CradlePoint
- Niesklasyfikowane GAO
- Niesklasyfikowane Rovo Kids
- Niesklasyfikowane Catalyst
- Niesklasyfikowane Dension
- Niesklasyfikowane Antelope Audio
- Niesklasyfikowane Brinno
- Niesklasyfikowane Venom
- Niesklasyfikowane CE Labs
- Niesklasyfikowane Legrand
- Niesklasyfikowane Z CAM
- Niesklasyfikowane Digium
- Niesklasyfikowane Giardino
- Niesklasyfikowane Mulex
- Niesklasyfikowane Socomec
- Niesklasyfikowane System Sensor
- Niesklasyfikowane San Jamar
- Niesklasyfikowane IPort
- Niesklasyfikowane X-Rite
- Niesklasyfikowane Wetelux
- Niesklasyfikowane Talkaphone
- Niesklasyfikowane Merax
- Niesklasyfikowane GermGuardian
- Niesklasyfikowane R-Go Tools
- Niesklasyfikowane Urbanista
- Niesklasyfikowane Sagitter
- Niesklasyfikowane Rainbow
- Niesklasyfikowane Duracell
- Niesklasyfikowane Riello
- Niesklasyfikowane Gagato
- Niesklasyfikowane General
- Niesklasyfikowane ECTIVE
- Niesklasyfikowane Gymform
- Niesklasyfikowane Ebro
- Niesklasyfikowane Tzumi
- Niesklasyfikowane BERTSCHAT
- Niesklasyfikowane Schumacher
- Niesklasyfikowane Michael Todd Beauty
- Niesklasyfikowane Cygnett
- Niesklasyfikowane Germania
- Niesklasyfikowane Victorio
- Niesklasyfikowane Platinum
- Niesklasyfikowane Trimble
- Niesklasyfikowane Sensei
- Niesklasyfikowane Playtive Junior
- Niesklasyfikowane Parklands
- Niesklasyfikowane Avid
- Niesklasyfikowane Vipack
- Niesklasyfikowane EKO
- Niesklasyfikowane BIG
- Niesklasyfikowane Emeril Lagasse
- Niesklasyfikowane POGS
- Niesklasyfikowane Graflex
- Niesklasyfikowane Coolaroo
- Niesklasyfikowane Wurth
- Niesklasyfikowane Mebus
- Niesklasyfikowane Gioteck
- Niesklasyfikowane Kenton
- Niesklasyfikowane Cypress
- Niesklasyfikowane Foliatec
- Niesklasyfikowane Silhouette
- Niesklasyfikowane South Shore
- Niesklasyfikowane Discovery
- Niesklasyfikowane T4E
- Niesklasyfikowane Speck
- Niesklasyfikowane Generation
- Niesklasyfikowane Iseki
- Niesklasyfikowane MOZA
- Niesklasyfikowane Ecler
- Niesklasyfikowane Turbosound
- Niesklasyfikowane Phase One
- Niesklasyfikowane Röhm
- Niesklasyfikowane ADDAC System
- Niesklasyfikowane Roadinger
- Niesklasyfikowane Ulanzi
- Niesklasyfikowane Anova
- Niesklasyfikowane Viscount
- Niesklasyfikowane Hurricane
- Niesklasyfikowane DAB
- Niesklasyfikowane Anex
- Niesklasyfikowane Majella
- Niesklasyfikowane GMB Audio
- Niesklasyfikowane Ashdown Engineering
- Niesklasyfikowane Century
- Niesklasyfikowane Unger
- Niesklasyfikowane Anthro
- Niesklasyfikowane Inverto
- Niesklasyfikowane Special-T
- Niesklasyfikowane Ygnis
- Niesklasyfikowane Esotec
- Niesklasyfikowane True & Tidy
- Niesklasyfikowane NovaStar
- Niesklasyfikowane Petkit
- Niesklasyfikowane Icon
- Niesklasyfikowane Kitchen Brains
- Niesklasyfikowane Challenge Xtreme
- Niesklasyfikowane Best
- Niesklasyfikowane Flycam
- Niesklasyfikowane NetAlly
- Niesklasyfikowane Triax
- Niesklasyfikowane XS Power
- Niesklasyfikowane Peltor
- Niesklasyfikowane JAR Systems
- Niesklasyfikowane Moleskine
- Niesklasyfikowane Bytecc
- Niesklasyfikowane Strex
- Niesklasyfikowane Xlyne
- Niesklasyfikowane Premier Mounts
- Niesklasyfikowane One Stop Systems
- Niesklasyfikowane Cool Maker
- Niesklasyfikowane Neo
- Niesklasyfikowane Mtx Audio
- Niesklasyfikowane DoughXpress
- Niesklasyfikowane Aquatic AV
- Niesklasyfikowane Parasound
- Niesklasyfikowane MSR
- Niesklasyfikowane Cabstone
- Niesklasyfikowane SPT
- Niesklasyfikowane DB Technologies
- Niesklasyfikowane Promate
- Niesklasyfikowane Tru Components
- Niesklasyfikowane Step2
- Niesklasyfikowane Crystal Quest
- Niesklasyfikowane Pit Boss
- Niesklasyfikowane Needit
- Niesklasyfikowane MiPow
- Niesklasyfikowane GoldenEar Technology
- Niesklasyfikowane Colt
- Niesklasyfikowane Elite Screens
- Niesklasyfikowane Ultron
- Niesklasyfikowane Choice
- Niesklasyfikowane Roswell
- Niesklasyfikowane King Craft
- Niesklasyfikowane FOX ESS
- Niesklasyfikowane Airman
- Niesklasyfikowane Cascade Audio Engineering
- Niesklasyfikowane B-Speech
- Niesklasyfikowane Vanish
- Niesklasyfikowane Nostalgia
- Niesklasyfikowane Grosfillex
- Niesklasyfikowane Solplanet
- Niesklasyfikowane Beemoo
- Niesklasyfikowane Hollyland
- Niesklasyfikowane Platinet
- Niesklasyfikowane Santos
- Niesklasyfikowane Evoc
- Niesklasyfikowane Versare
- Niesklasyfikowane Alutruss
- Niesklasyfikowane Tractive
- Niesklasyfikowane SpeakerCraft
- Niesklasyfikowane Celexon
- Niesklasyfikowane Epcom
- Niesklasyfikowane ZeeVee
- Niesklasyfikowane Siku
- Niesklasyfikowane Viatek
- Niesklasyfikowane Simplicity
- Niesklasyfikowane Doomoo
- Niesklasyfikowane MBZ
- Niesklasyfikowane Davey
- Niesklasyfikowane Mettler
- Niesklasyfikowane Metalux
- Niesklasyfikowane Potenza
- Niesklasyfikowane LOQED
- Niesklasyfikowane Hatco
- Niesklasyfikowane KONFTEL
- Niesklasyfikowane Canicom
- Niesklasyfikowane Mitsai
- Niesklasyfikowane Selfsat
- Niesklasyfikowane Leef
- Niesklasyfikowane Tusa
- Niesklasyfikowane Hovicon
- Niesklasyfikowane Starlyf
- Niesklasyfikowane Point Source Audio
- Niesklasyfikowane American BioTech Supply
- Niesklasyfikowane Noris
- Niesklasyfikowane Schmidt & Bender
- Niesklasyfikowane Mesa Boogie
- Niesklasyfikowane Improv
- Niesklasyfikowane LandRoller
- Niesklasyfikowane Wegman
- Niesklasyfikowane Lockncharge
- Niesklasyfikowane Merlin
- Niesklasyfikowane Standard Horizon
- Niesklasyfikowane Goal Zero
- Niesklasyfikowane HealthPostures
- Niesklasyfikowane CYP
- Niesklasyfikowane Heaven Fresh
- Niesklasyfikowane Lutec
- Niesklasyfikowane Champion Sports
- Niesklasyfikowane Molotow
- Niesklasyfikowane Herlag
- Niesklasyfikowane Dux
- Niesklasyfikowane JMAZ Lighting
- Niesklasyfikowane Hortus
- Niesklasyfikowane FALLER
- Niesklasyfikowane Miditech
- Niesklasyfikowane TTM
- Niesklasyfikowane Paw Patrol
- Niesklasyfikowane LELO
- Niesklasyfikowane Mermade
- Niesklasyfikowane MXR
- Niesklasyfikowane SKLZ
- Niesklasyfikowane Herma
- Niesklasyfikowane BWT
- Niesklasyfikowane Syrp
- Niesklasyfikowane Ugolini
- Niesklasyfikowane Cosina
- Niesklasyfikowane Heckler & Koch
- Niesklasyfikowane Whistler
- Niesklasyfikowane Twisper
- Niesklasyfikowane J5create
- Niesklasyfikowane Hushmat
- Niesklasyfikowane Xigmatek
- Niesklasyfikowane Tema
- Niesklasyfikowane ALM
- Niesklasyfikowane Topaz
- Niesklasyfikowane Toddy
- Niesklasyfikowane Aicon
- Niesklasyfikowane Astell&Kern
- Niesklasyfikowane Fun Generation
- Niesklasyfikowane Berkel
- Niesklasyfikowane Glorious
- Niesklasyfikowane Ciarra
- Niesklasyfikowane Bellari
- Niesklasyfikowane Beghelli
- Niesklasyfikowane Hugo Muller
- Niesklasyfikowane Vinci
- Niesklasyfikowane Jordan
- Niesklasyfikowane Duromax
- Niesklasyfikowane DataComm
- Niesklasyfikowane Powercube
- Niesklasyfikowane Kasp
- Niesklasyfikowane Dimavery
- Niesklasyfikowane WestBend
- Niesklasyfikowane Mr Coffee
- Niesklasyfikowane Sherlock
- Niesklasyfikowane SEA-PRO
- Niesklasyfikowane Omiindustriies
- Niesklasyfikowane Weltevree
- Niesklasyfikowane Phoenix Contact
- Niesklasyfikowane AMS Neve
- Niesklasyfikowane LVSUN
- Niesklasyfikowane Aston Microphones
- Niesklasyfikowane Netsys
- Niesklasyfikowane Alfi
- Niesklasyfikowane Polarlite
- Niesklasyfikowane Companion
- Niesklasyfikowane Mr. Beams
- Niesklasyfikowane Morphor
- Niesklasyfikowane Lapp
- Niesklasyfikowane XO
- Niesklasyfikowane PcDuino
- Niesklasyfikowane LECO
- Niesklasyfikowane Maretron
- Niesklasyfikowane Razorri
- Niesklasyfikowane Fetch
- Niesklasyfikowane Zoetis
- Niesklasyfikowane Prem-i-air
- Niesklasyfikowane NWS
- Niesklasyfikowane GAM
- Niesklasyfikowane EXO
- Niesklasyfikowane Altman
- Niesklasyfikowane FoxFury
- Niesklasyfikowane Eller
- Niesklasyfikowane Grimm Audio
- Niesklasyfikowane A-NeuVideo
- Niesklasyfikowane Best Service
- Niesklasyfikowane Arylic
- Niesklasyfikowane Aguilar
- Niesklasyfikowane Alogic
- Niesklasyfikowane Scale Computing
- Niesklasyfikowane Broil King
- Niesklasyfikowane Naturn Living
- Niesklasyfikowane Aeotec
- Niesklasyfikowane Catlink
- Niesklasyfikowane FitterFirst
- Niesklasyfikowane Raveland
- Niesklasyfikowane Mr. Heater
- Niesklasyfikowane Welltech
- Niesklasyfikowane Trumeter
- Niesklasyfikowane Seidio
- Niesklasyfikowane Sincreative
- Niesklasyfikowane JDC
- Niesklasyfikowane Hidrate
- Niesklasyfikowane Sonicware
- Niesklasyfikowane Nexibo
- Niesklasyfikowane Jolin
- Niesklasyfikowane MoTip
- Niesklasyfikowane Stenda
- Niesklasyfikowane Pro-Lift
- Niesklasyfikowane HIOAZO
- Niesklasyfikowane Malstrom
- Niesklasyfikowane Laserluchs
- Niesklasyfikowane Powersoft
- Niesklasyfikowane Casetastic
- Niesklasyfikowane UClear
- Niesklasyfikowane BikeLogger
- Niesklasyfikowane Tor Rey
- Niesklasyfikowane Momo Design
- Niesklasyfikowane Esdec
- Niesklasyfikowane Ruark Audio
- Niesklasyfikowane AJH Synth
- Niesklasyfikowane LifeStraw
- Niesklasyfikowane Magnavox
- Niesklasyfikowane Toolit
- Niesklasyfikowane Egnater
- Niesklasyfikowane DutchOne
- Niesklasyfikowane Feitian
- Niesklasyfikowane Ergie
- Niesklasyfikowane Reltech
- Niesklasyfikowane Armcross
- Niesklasyfikowane Focus Electrics
- Niesklasyfikowane Huntleigh
- Niesklasyfikowane Beeletix
- Niesklasyfikowane Claypaky
- Niesklasyfikowane EOTech
- Niesklasyfikowane Gehmann
- Niesklasyfikowane Batronix
- Niesklasyfikowane Franzis
- Niesklasyfikowane Gridbyt
- Niesklasyfikowane LONQ
- Niesklasyfikowane Wonky Monkey
- Niesklasyfikowane Dresden Elektronik
- Niesklasyfikowane Atmel
- Niesklasyfikowane Flavour Blaster
- Niesklasyfikowane SmartAVI
- Niesklasyfikowane EPH Elektronik
- Niesklasyfikowane InfiRay
- Niesklasyfikowane Markbass
- Niesklasyfikowane IMG Stage Line
- Niesklasyfikowane IMAC
- Niesklasyfikowane Metz Connect
- Niesklasyfikowane MGL Avionics
- Niesklasyfikowane Eikon
- Niesklasyfikowane Casablanca
- Niesklasyfikowane Nemco
- Niesklasyfikowane Wireless Solution
- Niesklasyfikowane Beverage-Air
- Niesklasyfikowane Sparco
- Niesklasyfikowane Barber Tech
- Niesklasyfikowane Estella
- Niesklasyfikowane EarFun
- Niesklasyfikowane Minkels
- Niesklasyfikowane Kipor
- Niesklasyfikowane Lenmar
- Niesklasyfikowane Arduino
- Niesklasyfikowane Ave Six
- Niesklasyfikowane Bestar
- Niesklasyfikowane Pelco
- Niesklasyfikowane Gardigo
- Niesklasyfikowane Highpoint
- Niesklasyfikowane Puls Dimension
- Niesklasyfikowane Studiologic
- Niesklasyfikowane Fischer Amps
- Niesklasyfikowane CHINT
- Niesklasyfikowane Sirus
- Niesklasyfikowane Digitech
- Niesklasyfikowane Leviton
- Niesklasyfikowane Gretsch
- Niesklasyfikowane Pentacon
- Niesklasyfikowane Winia
- Niesklasyfikowane Bolsey
- Niesklasyfikowane Louis Tellier
- Niesklasyfikowane Baracuda
- Niesklasyfikowane Kstar
- Niesklasyfikowane Air Guard
- Niesklasyfikowane MediaMatrix
- Niesklasyfikowane ESX
- Niesklasyfikowane Tuur
- Niesklasyfikowane ONE Smart Control
- Niesklasyfikowane OBSBOT
- Niesklasyfikowane InSinkErator
- Niesklasyfikowane AREXX
- Niesklasyfikowane Elite Force
- Niesklasyfikowane DEHN
- Niesklasyfikowane Piko
- Niesklasyfikowane Lifan
- Niesklasyfikowane Jomox
- Niesklasyfikowane Pentatech
- Niesklasyfikowane Burley
- Niesklasyfikowane Lexicon
- Niesklasyfikowane Icarus Blue
- Niesklasyfikowane Command
- Niesklasyfikowane IRIS
- Niesklasyfikowane Neno
- Niesklasyfikowane Starburst
- Niesklasyfikowane Fluance
- Niesklasyfikowane PCE Instruments
- Niesklasyfikowane Garden Place
- Niesklasyfikowane Moldex
- Niesklasyfikowane MaximaVida
- Niesklasyfikowane Firefriend
- Niesklasyfikowane LightZone
- Niesklasyfikowane Bliss Outdoors
- Niesklasyfikowane Fontiso
- Niesklasyfikowane Varytec
- Niesklasyfikowane Altra
- Niesklasyfikowane Omnilux
- Niesklasyfikowane Quartet
- Niesklasyfikowane Shadow
- Niesklasyfikowane IP-COM
- Niesklasyfikowane Comtek
- Niesklasyfikowane Digital Juice
- Niesklasyfikowane Eschenbach
- Niesklasyfikowane ASM
- Niesklasyfikowane Elektron
- Niesklasyfikowane Ltech
- Niesklasyfikowane RetroSound
- Niesklasyfikowane Caroline
- Niesklasyfikowane Zomo
- Niesklasyfikowane VAIS Technology
- Niesklasyfikowane Buchla & TipTop Audio
- Niesklasyfikowane Pyramid
- Niesklasyfikowane Maico
- Niesklasyfikowane On-Q
- Niesklasyfikowane SetonixSynth
- Niesklasyfikowane Horex
- Niesklasyfikowane Inno-Hit
- Niesklasyfikowane Sime
- Niesklasyfikowane AvaValley
- Niesklasyfikowane INTIMINA
- Niesklasyfikowane FCC BBQ
- Niesklasyfikowane Auto XS
- Niesklasyfikowane Toomax
- Niesklasyfikowane Aqua Marina
- Niesklasyfikowane Hameg
- Niesklasyfikowane Greemotion
- Niesklasyfikowane Winter Modular
- Niesklasyfikowane Synamodec
- Niesklasyfikowane Grotime
- Niesklasyfikowane Pico Macom
- Niesklasyfikowane RadonTec
- Niesklasyfikowane Katrin
- Niesklasyfikowane Kendau
- Niesklasyfikowane NUX
- Niesklasyfikowane Coxreels
- Niesklasyfikowane Overade
- Niesklasyfikowane Liemke
- Niesklasyfikowane Copco
- Niesklasyfikowane Vanson
- Niesklasyfikowane Canyon
- Niesklasyfikowane Carcomm
- Niesklasyfikowane Style Me Up
- Niesklasyfikowane Swedish Posture
- Niesklasyfikowane Melnor
- Niesklasyfikowane CDVI
- Niesklasyfikowane Excalibur
- Niesklasyfikowane Holman
- Niesklasyfikowane HomePilot
- Niesklasyfikowane Leaptel
- Niesklasyfikowane Lifenaxx
- Niesklasyfikowane Powertec
- Niesklasyfikowane Waterbird
- Niesklasyfikowane Dreambaby
- Niesklasyfikowane AOpen
- Niesklasyfikowane Angler
- Niesklasyfikowane GP
- Niesklasyfikowane Akrobat
- Niesklasyfikowane Selleys
- Niesklasyfikowane WindFall
- Niesklasyfikowane Ameristep
- Niesklasyfikowane KM-fit
- Niesklasyfikowane X Rocker
- Niesklasyfikowane Mircom
- Niesklasyfikowane ESUN
- Niesklasyfikowane Durex
- Niesklasyfikowane ZWO
- Niesklasyfikowane AeroCool
- Niesklasyfikowane Vantage Point
- Niesklasyfikowane Jokari
- Niesklasyfikowane Engel
- Niesklasyfikowane BeeSecure
- Niesklasyfikowane MantelMount
- Niesklasyfikowane Unicol
- Niesklasyfikowane Fisher Paykel
- Niesklasyfikowane Lasita Maja
- Niesklasyfikowane Meccano
- Niesklasyfikowane Parallels
- Niesklasyfikowane Oatey
- Niesklasyfikowane QUIO
- Niesklasyfikowane Fisher
- Niesklasyfikowane Gretsch Guitars
- Niesklasyfikowane Banoch
- Niesklasyfikowane XP-PEN
- Niesklasyfikowane Atmotube
- Niesklasyfikowane Sun Pumps
- Niesklasyfikowane Electrify
- Niesklasyfikowane Leatt
- Niesklasyfikowane Bleep Labs
- Niesklasyfikowane FontaFit
- Niesklasyfikowane Gossmann
- Niesklasyfikowane Comatec
- Niesklasyfikowane Jonard Tools
- Niesklasyfikowane WEG
- Niesklasyfikowane Atech Flash Technology
- Niesklasyfikowane AutoParkTime
- Niesklasyfikowane Hudora
- Niesklasyfikowane Facal
- Niesklasyfikowane Planet Audio
- Niesklasyfikowane Datacolor
- Niesklasyfikowane Silicon Power
- Niesklasyfikowane JAXY
- Niesklasyfikowane WARN
- Niesklasyfikowane Aarke
- Niesklasyfikowane TikkTokk
- Niesklasyfikowane Roco
- Niesklasyfikowane Flexson
- Niesklasyfikowane Camec
- Niesklasyfikowane Wibrain
- Niesklasyfikowane Rolly Toys
- Niesklasyfikowane CAD Audio
- Niesklasyfikowane Altrad
- Niesklasyfikowane Black Hydra
- Niesklasyfikowane Level Mount
- Niesklasyfikowane Teenage Engineering
- Niesklasyfikowane Elipson
- Niesklasyfikowane STANDIVARIUS
- Niesklasyfikowane CommScope
- Niesklasyfikowane Orange
- Niesklasyfikowane Extralife Instruments
- Niesklasyfikowane Genki Instruments
- Niesklasyfikowane Industrial Music Electronics
- Niesklasyfikowane Mauser Sitzkultur
- Niesklasyfikowane Accezz
- Niesklasyfikowane A4 Tech
- Niesklasyfikowane Full Boar
- Niesklasyfikowane Zedar
- Niesklasyfikowane Yli Electronic
- Niesklasyfikowane Dals
- Niesklasyfikowane Bulman
- Niesklasyfikowane TOOLMATE
- Niesklasyfikowane SleepPro
- Niesklasyfikowane Muama
- Niesklasyfikowane Lepu Medical
- Niesklasyfikowane Michigan
- Niesklasyfikowane Beringer
- Niesklasyfikowane Phonic
- Niesklasyfikowane ZCover
- Niesklasyfikowane Vasagle
- Niesklasyfikowane Aquatica
- Niesklasyfikowane Girmi
- Niesklasyfikowane Goaliath
- Niesklasyfikowane 909 Outdoor
- Niesklasyfikowane Viomi
- Niesklasyfikowane Better Life
- Niesklasyfikowane Dayclocks
- Niesklasyfikowane Phidgets
- Niesklasyfikowane TK Audio
- Niesklasyfikowane Hawk-Woods
- Niesklasyfikowane Novo
- Niesklasyfikowane Commercial Chef
- Niesklasyfikowane Dexibell
- Niesklasyfikowane IsoAcoustics
- Niesklasyfikowane Memphis
- Niesklasyfikowane Clifford
- Niesklasyfikowane Cambo
- Niesklasyfikowane Hedbox
- Niesklasyfikowane Lansinoh
- Niesklasyfikowane Maclean
- Niesklasyfikowane 9.solutions
- Niesklasyfikowane WEN
- Niesklasyfikowane Trace Elliot
- Niesklasyfikowane Lockwood
- Niesklasyfikowane Nexera
- Niesklasyfikowane Goodway
- Niesklasyfikowane BlueDri
- Niesklasyfikowane Seenergy
- Niesklasyfikowane Meinl
- Niesklasyfikowane Analogis
- Niesklasyfikowane BBQ Premium
- Niesklasyfikowane Stäubli
- Niesklasyfikowane RAB
- Niesklasyfikowane Schabus
- Niesklasyfikowane Eoslift
- Niesklasyfikowane Bron-Coucke
- Niesklasyfikowane Steelton
- Niesklasyfikowane FeinTech
- Niesklasyfikowane Masterbuilt
- Niesklasyfikowane T-Rex
- Niesklasyfikowane Koolatron
- Niesklasyfikowane Euro Cuisine
- Niesklasyfikowane GFM
- Niesklasyfikowane Tot Tutors
- Niesklasyfikowane X4 Life
- Niesklasyfikowane Tonar
- Niesklasyfikowane Peterson
- Niesklasyfikowane CFH
- Niesklasyfikowane Emeril Everyday
- Niesklasyfikowane Rockboard
- Niesklasyfikowane Nivian
- Niesklasyfikowane L.R.Baggs
- Niesklasyfikowane Millennia
- Niesklasyfikowane Vermona Modular
- Niesklasyfikowane Adventure Kings
- Niesklasyfikowane Drive Medical
- Niesklasyfikowane Hitron
- Niesklasyfikowane Bliss Hammocks
- Niesklasyfikowane Singular Sound
- Niesklasyfikowane Maneco Labs
- Niesklasyfikowane BISWIND
- Niesklasyfikowane ABE Arnhold
- Niesklasyfikowane Mermade Hair
- Niesklasyfikowane Hover-1
- Niesklasyfikowane VCM
- Niesklasyfikowane BodyCraft
- Niesklasyfikowane Auer Signal
- Niesklasyfikowane BrightSign
- Niesklasyfikowane Mamas & Papas
- Niesklasyfikowane Manduca
- Niesklasyfikowane HELGI
- Niesklasyfikowane Forge Adour
- Niesklasyfikowane Darkglass
- Niesklasyfikowane Paasche
- Niesklasyfikowane Vistus
- Niesklasyfikowane GMW
- Niesklasyfikowane AER
- Niesklasyfikowane Dynavox
- Niesklasyfikowane Columbus
- Niesklasyfikowane IWH
- Niesklasyfikowane Code Mercenaries
- Niesklasyfikowane Diamex
- Niesklasyfikowane Sunset
- Niesklasyfikowane Avital
- Niesklasyfikowane Ondis24
- Niesklasyfikowane D'Addario
- Niesklasyfikowane BBE
- Niesklasyfikowane Warwick
- Niesklasyfikowane MyAVR
- Niesklasyfikowane EBS
- Niesklasyfikowane WEICON
- Niesklasyfikowane Rotronic
- Niesklasyfikowane Edsyn
- Niesklasyfikowane Urban Glide
- Niesklasyfikowane EISL
- Niesklasyfikowane RCS
- Niesklasyfikowane Nicai Systems
- Niesklasyfikowane IDENTsmart
- Niesklasyfikowane Sharper Image
- Niesklasyfikowane Revier Manager
- Niesklasyfikowane Homak
- Niesklasyfikowane Tycon Systems
- Niesklasyfikowane Selve
- Niesklasyfikowane Lumel
- Niesklasyfikowane Digigram
- Niesklasyfikowane Paingone
- Niesklasyfikowane Plugwise
- Niesklasyfikowane Martens
- Niesklasyfikowane Palmako
- Niesklasyfikowane Desview
- Niesklasyfikowane ActiveJet
- Niesklasyfikowane Global Water
- Niesklasyfikowane Allsee
- Niesklasyfikowane Softing
- Niesklasyfikowane Pulse ShowerSpas
- Niesklasyfikowane GFB
- Niesklasyfikowane Sonicsmith
- Niesklasyfikowane Toraiz
- Niesklasyfikowane Ergodyne
- Niesklasyfikowane Maturmeat
- Niesklasyfikowane D-Jix
- Niesklasyfikowane Orbsmart
- Niesklasyfikowane Eowave
- Niesklasyfikowane Imperia
- Niesklasyfikowane Nature2
- Niesklasyfikowane Baby Trend
- Niesklasyfikowane AMERRY
- Niesklasyfikowane Walther
- Niesklasyfikowane ShelterLogic
- Niesklasyfikowane Varad
- Niesklasyfikowane Dr. Browns
- Niesklasyfikowane KMA Machines
- Niesklasyfikowane Elcom
- Niesklasyfikowane Source Audio
- Niesklasyfikowane AtomoSynth
- Niesklasyfikowane Innr
- Niesklasyfikowane Benidub
- Niesklasyfikowane Protector
- Niesklasyfikowane Winston
- Niesklasyfikowane Solidsteel
- Niesklasyfikowane Dracast
- Niesklasyfikowane Dream
- Niesklasyfikowane Malouf
- Niesklasyfikowane Roba
- Niesklasyfikowane Ravelli
- Niesklasyfikowane Piet Boon
- Niesklasyfikowane PureTools
- Niesklasyfikowane JML
- Niesklasyfikowane Reber
- Niesklasyfikowane SiriusXM
- Niesklasyfikowane Earthwise
- Niesklasyfikowane DoubleSight
- Niesklasyfikowane Raya
- Niesklasyfikowane Artex
- Niesklasyfikowane Bobrick
- Niesklasyfikowane Verbos Electronics
- Niesklasyfikowane Ark
- Niesklasyfikowane DLO
- Niesklasyfikowane ENS
- Niesklasyfikowane Listen
- Niesklasyfikowane Oscium
- Niesklasyfikowane Benchmark USA
- Niesklasyfikowane Python
- Niesklasyfikowane Littelfuse
- Niesklasyfikowane Game Factor
- Niesklasyfikowane NComputing
- Niesklasyfikowane Mode Machines
- Niesklasyfikowane Legends
- Niesklasyfikowane AS Synthesizers
- Niesklasyfikowane Itechworld
- Niesklasyfikowane Nexcom
- Niesklasyfikowane SatKing
- Niesklasyfikowane Fulltone
- Niesklasyfikowane Advantix
- Niesklasyfikowane Wampler
- Niesklasyfikowane VAEMI
- Niesklasyfikowane Narva
- Niesklasyfikowane DOK
- Niesklasyfikowane OzCharge
- Niesklasyfikowane MIYO
- Niesklasyfikowane Cioks
- Niesklasyfikowane Neopower
- Niesklasyfikowane AvMap
- Niesklasyfikowane Arlec
- Niesklasyfikowane Sanwa
- Niesklasyfikowane REDARC
- Niesklasyfikowane Guardian
- Niesklasyfikowane Radio Flyer
- Niesklasyfikowane Gaslock
- Niesklasyfikowane Gaffgun
- Niesklasyfikowane AquaMAX
- Niesklasyfikowane DigitSole
- Niesklasyfikowane Portsmith
- Niesklasyfikowane Rome
- Niesklasyfikowane DW
- Niesklasyfikowane BEA
- Niesklasyfikowane Disty
- Niesklasyfikowane OXI Instruments
- Niesklasyfikowane AvaTime
- Niesklasyfikowane Xhose
- Niesklasyfikowane MYVU
- Niesklasyfikowane Kopykake
- Niesklasyfikowane Konstant Lab
- Niesklasyfikowane Turbo Scrub
- Niesklasyfikowane Tenderfoot Electronics
- Niesklasyfikowane Kask
- Niesklasyfikowane Callpod
- Niesklasyfikowane Dorman
- Niesklasyfikowane 2box
- Niesklasyfikowane Enlight
- Niesklasyfikowane Franken
- Niesklasyfikowane RUBI
- Niesklasyfikowane Europa Leisure
- Niesklasyfikowane GAMO
- Niesklasyfikowane Musser
- Niesklasyfikowane Edge Products
- Niesklasyfikowane IClever
- Niesklasyfikowane HN-Power
- Niesklasyfikowane BIONIK
- Niesklasyfikowane King Canopy
- Niesklasyfikowane HeadRush
- Niesklasyfikowane Flover
- Niesklasyfikowane Milestone Systems
- Niesklasyfikowane Micsig
- Niesklasyfikowane Dodow
- Niesklasyfikowane Spring
- Niesklasyfikowane Red Panda
- Niesklasyfikowane OJ ELECTRONICS
- Niesklasyfikowane Aquasure
- Niesklasyfikowane Banana Pi
- Niesklasyfikowane Ilford
- Niesklasyfikowane Crazy Tube Circuits
- Niesklasyfikowane J.P. Instruments
- Niesklasyfikowane Proclip
- Niesklasyfikowane SainSmart
- Niesklasyfikowane Kaona
- Niesklasyfikowane DPW Design
- Niesklasyfikowane SinuPulse
- Niesklasyfikowane The T.bone
- Niesklasyfikowane DIEZEL
- Niesklasyfikowane VMB
- Niesklasyfikowane Z.Vex
- Niesklasyfikowane Seymour Duncan
- Niesklasyfikowane BluGuitar
- Niesklasyfikowane Lehle
- Niesklasyfikowane Bricasti Design
- Niesklasyfikowane T.akustik
- Niesklasyfikowane Dwarf Connection
- Niesklasyfikowane JL Cooper
- Niesklasyfikowane StrikeMaster
- Niesklasyfikowane ProUser
- Niesklasyfikowane Bēm Wireless
- Niesklasyfikowane Aqua-Vu
- Niesklasyfikowane Millecroquettes
- Niesklasyfikowane GR Bass
- Niesklasyfikowane Sure-Fi
- Niesklasyfikowane Copernicus
- Niesklasyfikowane Gumdrop
- Niesklasyfikowane Tellur
- Niesklasyfikowane Woox
- Niesklasyfikowane Gallien-Krueger
- Niesklasyfikowane Jetway
- Niesklasyfikowane Texsport
- Niesklasyfikowane SSV Works
- Niesklasyfikowane Terre
- Niesklasyfikowane Sanitec
- Niesklasyfikowane Pangea Audio
- Niesklasyfikowane Hogue
- Niesklasyfikowane ATP
- Niesklasyfikowane Pfannenberg
- Niesklasyfikowane Scytek
- Niesklasyfikowane MotorScrubber
- Niesklasyfikowane Krone
- Niesklasyfikowane Kraftmax
- Niesklasyfikowane Steelplay
- Niesklasyfikowane PCTV Systems
- Niesklasyfikowane Cooper Lighting
- Niesklasyfikowane Code Corporation
- Niesklasyfikowane Now TV
- Niesklasyfikowane Best Fitness
- Niesklasyfikowane Voodoo Lab
- Niesklasyfikowane Strymon
- Niesklasyfikowane Insect Lore
- Niesklasyfikowane Faytech
- Niesklasyfikowane Chrome-Q
- Niesklasyfikowane Tektronix
- Niesklasyfikowane Kitronik
- Niesklasyfikowane Trasman
- Niesklasyfikowane Hamlet
- Niesklasyfikowane SumUp
- Niesklasyfikowane Microlab
- Niesklasyfikowane Rotolight
- Niesklasyfikowane Mr Gardener
- Niesklasyfikowane Lumu
- Niesklasyfikowane WAYDOO
- Niesklasyfikowane Fimer
- Niesklasyfikowane ASIWO
- Niesklasyfikowane Lexar
- Niesklasyfikowane Vent-Axia
- Niesklasyfikowane Firefield
- Niesklasyfikowane E-Power
- Niesklasyfikowane RectorSeal
- Niesklasyfikowane Kaiser Nienhaus
- Niesklasyfikowane Freeplay
- Niesklasyfikowane Roller Grill
- Niesklasyfikowane Zaor
- Niesklasyfikowane Cleco
- Niesklasyfikowane AVTech
- Niesklasyfikowane Bugera
- Niesklasyfikowane Handy Lux
- Niesklasyfikowane Rossum Electro-Music
- Niesklasyfikowane Panta
- Niesklasyfikowane Pentel
- Niesklasyfikowane Wallas
- Niesklasyfikowane Gima
- Niesklasyfikowane MagnaPool
- Niesklasyfikowane Aquadon
- Niesklasyfikowane Raidsonic
- Niesklasyfikowane Approx
- Niesklasyfikowane Gamesir
- Niesklasyfikowane Neunaber
- Niesklasyfikowane DPM
- Niesklasyfikowane VOREL
- Niesklasyfikowane DayStar Filters
- Niesklasyfikowane Flexispot
- Niesklasyfikowane OP/TECH
- Niesklasyfikowane Cinderella
- Niesklasyfikowane Bauhn
- Niesklasyfikowane Aspen
- Niesklasyfikowane Cottons
- Niesklasyfikowane Frequency Central
- Niesklasyfikowane Sacrament
- Niesklasyfikowane The Box
- Niesklasyfikowane AudioThing
- Niesklasyfikowane Cambium Networks
- Niesklasyfikowane Trident
- Niesklasyfikowane Schoeps
- Niesklasyfikowane HPI Racing
- Niesklasyfikowane Favini
- Niesklasyfikowane Dnipro
- Niesklasyfikowane IFootage
- Niesklasyfikowane Sonuus
- Niesklasyfikowane Jonsered
- Niesklasyfikowane Saint Algue
- Niesklasyfikowane Cactus
- Niesklasyfikowane Oecolux
- Niesklasyfikowane SoundLAB
- Niesklasyfikowane ACL
- Niesklasyfikowane Mars Gaming
- Niesklasyfikowane Radiant
- Niesklasyfikowane G.Skill
- Niesklasyfikowane Edbak
- Niesklasyfikowane DMT
- Niesklasyfikowane Integral LED
- Niesklasyfikowane Integral
- Niesklasyfikowane Roline
- Niesklasyfikowane Virax
- Niesklasyfikowane MSW
- Niesklasyfikowane Gill
- Niesklasyfikowane AMC
- Niesklasyfikowane Triangle
- Niesklasyfikowane Tumbleweed
- Niesklasyfikowane Sunpentown
- Niesklasyfikowane Hamstra
- Niesklasyfikowane PVI
- Niesklasyfikowane Avenview
- Niesklasyfikowane Grendel
- Niesklasyfikowane Coravin
- Niesklasyfikowane O&O Software
- Niesklasyfikowane Wasp
- Niesklasyfikowane Chef's Choice
- Niesklasyfikowane Warmup
- Niesklasyfikowane Brastemp
- Niesklasyfikowane Wavtech
- Niesklasyfikowane Satco
- Niesklasyfikowane AMT
- Niesklasyfikowane Royal Catering
- Niesklasyfikowane Artrom
- Niesklasyfikowane Lowell
- Niesklasyfikowane Adonit
- Niesklasyfikowane ANDYCINE
- Niesklasyfikowane AmpliVox
- Niesklasyfikowane Pippi
- Niesklasyfikowane Casalux
- Niesklasyfikowane CyberData Systems
- Niesklasyfikowane Omnitron Systems
- Niesklasyfikowane Stewart Systems
- Niesklasyfikowane SwitchBot
- Niesklasyfikowane Qubino
- Niesklasyfikowane Eurosound
- Niesklasyfikowane Williams Sound
- Niesklasyfikowane ICC
- Niesklasyfikowane Magewell
- Niesklasyfikowane Globalo
- Niesklasyfikowane SoundTube
- Niesklasyfikowane Therabody
- Niesklasyfikowane Infortrend
- Niesklasyfikowane STI
- Niesklasyfikowane Rug Doctor
- Niesklasyfikowane Raspberry Pi
- Niesklasyfikowane Bals
- Niesklasyfikowane Balt
- Niesklasyfikowane AJ.BA
- Niesklasyfikowane ESKA
- Niesklasyfikowane Lascar Electronics
- Niesklasyfikowane Sport-Tronic
- Niesklasyfikowane Alga
- Niesklasyfikowane WesAudio
- Niesklasyfikowane Hamron
- Niesklasyfikowane Robust
- Niesklasyfikowane Quik Lok
- Niesklasyfikowane Tsakalis AudioWorks
- Niesklasyfikowane MagTek
- Niesklasyfikowane Jupiter
- Niesklasyfikowane Sony Optiarc
- Niesklasyfikowane Colortone
- Niesklasyfikowane Super Rod
- Niesklasyfikowane Carnielli
- Niesklasyfikowane Luminex
- Niesklasyfikowane Epiphan
- Niesklasyfikowane Deltaco Gaming
- Niesklasyfikowane P3 International
- Niesklasyfikowane Idec
- Niesklasyfikowane Beckmann & Egle
- Niesklasyfikowane Seek Thermal
- Niesklasyfikowane VintageView
- Niesklasyfikowane Alfresco
- Niesklasyfikowane Bintec-elmeg
- Niesklasyfikowane Crane Song
- Niesklasyfikowane W'eau
- Niesklasyfikowane Belena
- Niesklasyfikowane Fanox
- Niesklasyfikowane Crouzet
- Niesklasyfikowane Megarevo
- Niesklasyfikowane Tech 21
- Niesklasyfikowane Petmate
- Niesklasyfikowane BlendMount
- Niesklasyfikowane Perlick
- Niesklasyfikowane Sedona
- Niesklasyfikowane Tecnoinox
- Niesklasyfikowane CaterRacks
- Niesklasyfikowane Besco
- Niesklasyfikowane Prologue
- Niesklasyfikowane Nanoleaf
- Niesklasyfikowane Mach Power
- Niesklasyfikowane Soltection
- Niesklasyfikowane Kool-It
- Niesklasyfikowane Cool Head
- Niesklasyfikowane KeepOut
- Niesklasyfikowane LawnMaster
- Niesklasyfikowane Deltronic
- Niesklasyfikowane Eligent
- Niesklasyfikowane Meris
- Niesklasyfikowane Procare
- Niesklasyfikowane AmerBox
- Niesklasyfikowane Qu-Bit
- Niesklasyfikowane Blue Lantern
- Niesklasyfikowane DivKid
- Niesklasyfikowane Uniross
- Niesklasyfikowane FaseLunare
- Niesklasyfikowane (Recovery)
- Niesklasyfikowane Twinkly
- Niesklasyfikowane Squarp Instruments
- Niesklasyfikowane EtherWAN
- Niesklasyfikowane Econ Connect
- Niesklasyfikowane META
- Niesklasyfikowane Shimbol
- Niesklasyfikowane GC Audio
- Niesklasyfikowane Einhell Bavaria
- Niesklasyfikowane Motrona
- Niesklasyfikowane Thalheimer
- Niesklasyfikowane FeiYu-Tech
- Niesklasyfikowane Aida
- Niesklasyfikowane VisionTek
- Niesklasyfikowane Accsoon
- Niesklasyfikowane Losi
- Niesklasyfikowane Bessey
- Niesklasyfikowane A3
- Niesklasyfikowane Serge
- Niesklasyfikowane Gladiator
- Niesklasyfikowane Mobli
- Niesklasyfikowane G-Technology
- Niesklasyfikowane Caroma
- Niesklasyfikowane Sungale
- Niesklasyfikowane Befaco
- Niesklasyfikowane Waltec
- Niesklasyfikowane Eartec
- Niesklasyfikowane Portkeys
- Niesklasyfikowane Westcott
- Niesklasyfikowane EXSYS
- Niesklasyfikowane Digiquest
- Niesklasyfikowane Gewiss
- Niesklasyfikowane Hagor
- Niesklasyfikowane Glyph
- Niesklasyfikowane Seco-Larm
- Niesklasyfikowane Massoth
- Niesklasyfikowane Envitec
- Niesklasyfikowane Mimo Monitors
- Niesklasyfikowane Alula
- Niesklasyfikowane Blebox
- Niesklasyfikowane VS Sassoon
- Niesklasyfikowane Redsbaby
- Niesklasyfikowane Bright Spark
- Niesklasyfikowane Algo
- Niesklasyfikowane Peloton
- Niesklasyfikowane Gentrax
- Niesklasyfikowane Brocade
- Niesklasyfikowane Insteon
- Niesklasyfikowane Altronix
- Niesklasyfikowane Warner Bros
- Niesklasyfikowane Vinotemp
- Niesklasyfikowane Silent Knight
- Niesklasyfikowane Mosconi
- Niesklasyfikowane CGV
- Niesklasyfikowane My Arcade
- Niesklasyfikowane Tescoma
- Niesklasyfikowane RF Elements
- Niesklasyfikowane ALC
- Niesklasyfikowane Holland Electronics
- Niesklasyfikowane Arista
- Niesklasyfikowane Triumph Sports
- Niesklasyfikowane Gasmate
- Niesklasyfikowane Crelando
- Niesklasyfikowane Novo Nordisk
- Niesklasyfikowane Seville Classics
- Niesklasyfikowane TechLogix Networx
- Niesklasyfikowane Thermalright
- Niesklasyfikowane Bxterra
- Niesklasyfikowane Bea-fon
- Niesklasyfikowane Babylonia
- Niesklasyfikowane HeartSine
- Niesklasyfikowane Bullet
- Niesklasyfikowane Morrison
- Niesklasyfikowane Ordo
- Niesklasyfikowane Alphacool
- Niesklasyfikowane Asetek
- Niesklasyfikowane AZZA
- Niesklasyfikowane Audibax
- Niesklasyfikowane TechN
- Niesklasyfikowane Davita
- Niesklasyfikowane Giga Copper
- Niesklasyfikowane Elsner
- Niesklasyfikowane Séura
- Niesklasyfikowane Cube Controls
- Niesklasyfikowane Meridian
- Niesklasyfikowane Donexon
- Niesklasyfikowane Linq
- Niesklasyfikowane Wortmann AG
- Niesklasyfikowane DiGiGrid
- Niesklasyfikowane Sanofi
- Niesklasyfikowane Mitzu
- Niesklasyfikowane Avteq
- Niesklasyfikowane Fizzics
- Niesklasyfikowane XFX
- Niesklasyfikowane Leynew
- Niesklasyfikowane Lauten Audio
- Niesklasyfikowane Cropico
- Niesklasyfikowane Sunwoda
- Niesklasyfikowane Schleich
- Niesklasyfikowane Unitech
- Niesklasyfikowane FXLab
- Niesklasyfikowane Middle Atlantic
- Niesklasyfikowane Kincrome
- Niesklasyfikowane Brockhaus HEUER
- Niesklasyfikowane Reishunger
- Niesklasyfikowane Ergotec
- Niesklasyfikowane Dupla
- Niesklasyfikowane APSystems
- Niesklasyfikowane IODD
- Niesklasyfikowane BYD
- Niesklasyfikowane Aqua Medic
- Niesklasyfikowane Pylontech
- Niesklasyfikowane Fire Sense
- Niesklasyfikowane Grüniq
- Niesklasyfikowane Goodwe
- Niesklasyfikowane Moki
- Niesklasyfikowane Enertex
- Niesklasyfikowane Ovation
- Niesklasyfikowane Enviroswim
- Niesklasyfikowane Dobar
- Niesklasyfikowane Vevor
- Niesklasyfikowane Ovente
- Niesklasyfikowane PowerColor
- Niesklasyfikowane ISpring
- Niesklasyfikowane WeFix
- Niesklasyfikowane BCA
- Niesklasyfikowane Saki
- Niesklasyfikowane Smart365
- Niesklasyfikowane ChargeHub
- Niesklasyfikowane Eldat
- Niesklasyfikowane SoundSwitch
- Niesklasyfikowane Dostmann Electronic
- Niesklasyfikowane JBC
- Niesklasyfikowane DV Mark
- Niesklasyfikowane MOON
- Niesklasyfikowane Cuggl
- Niesklasyfikowane HABAU
- Niesklasyfikowane CVW
- Niesklasyfikowane Earbreeze
- Niesklasyfikowane Möhlenhoff
- Niesklasyfikowane Taqua
- Niesklasyfikowane Brainstorm
- Niesklasyfikowane Colonial Elegance
- Niesklasyfikowane Overtone Labs
- Niesklasyfikowane Bühnen
- Niesklasyfikowane Blukac
- Niesklasyfikowane BendixKing
- Niesklasyfikowane Tube-Tech
- Niesklasyfikowane TCW Technologies
- Niesklasyfikowane UNITEK
- Niesklasyfikowane CoolerMaster
- Niesklasyfikowane Rexing
- Niesklasyfikowane The T.mix
- Niesklasyfikowane Regula-Werk King
- Niesklasyfikowane MIDI Solutions
- Niesklasyfikowane Positive Grid
- Niesklasyfikowane Amgrow
- Niesklasyfikowane Xaphoon
- Niesklasyfikowane Winchester
- Niesklasyfikowane Lampa
- Niesklasyfikowane Sinus Live
- Niesklasyfikowane Sureguard
- Niesklasyfikowane QuickCool
- Niesklasyfikowane Smit Visual
- Niesklasyfikowane NZR
- Niesklasyfikowane Toparc
- Niesklasyfikowane Oro-Med
- Niesklasyfikowane Hex
- Niesklasyfikowane Baby Cakes
- Niesklasyfikowane Deflecto
- Niesklasyfikowane ELMEKO
- Niesklasyfikowane Tesseract Modular
- Niesklasyfikowane Sport Dog
- Niesklasyfikowane Nowsonic
- Niesklasyfikowane On Air
- Niesklasyfikowane Acoustic Solutions
- Niesklasyfikowane Hubble Connected
- Niesklasyfikowane ELTA Music
- Niesklasyfikowane Dragonshock
- Niesklasyfikowane We-Vibe
- Niesklasyfikowane Electronics International
- Niesklasyfikowane Lamar
- Niesklasyfikowane Atlantis Land
- Niesklasyfikowane White Lightning
- Niesklasyfikowane GEV
- Niesklasyfikowane Frient
- Niesklasyfikowane Kaiser Fototechnik
- Niesklasyfikowane Vishay
- Niesklasyfikowane Rooboost
- Niesklasyfikowane Bitspower
- Niesklasyfikowane Comar
- Niesklasyfikowane Freedor
- Niesklasyfikowane Start International
- Niesklasyfikowane AXITEC
- Niesklasyfikowane Lingg & Janke
- Niesklasyfikowane Auralex
- Niesklasyfikowane Pieps
- Niesklasyfikowane Innovative
- Niesklasyfikowane Lynx Technik
- Niesklasyfikowane Yuede
- Niesklasyfikowane ClimeMET
- Niesklasyfikowane Pliant Technologies
- Niesklasyfikowane Prompter People
- Niesklasyfikowane Astropet
- Niesklasyfikowane Canopia
- Niesklasyfikowane Wabeco
- Niesklasyfikowane Swingline GBC
- Niesklasyfikowane Staudte-Hirsch
- Niesklasyfikowane Universal Remote Control
- Niesklasyfikowane Lantronix
- Niesklasyfikowane Kino Flo
- Niesklasyfikowane Aqua Computer
- Niesklasyfikowane HEDD
- Niesklasyfikowane Vinpower Digital
- Niesklasyfikowane Lindemann
- Niesklasyfikowane Silent Angel
- Niesklasyfikowane Club 3D
- Niesklasyfikowane Sprolink
- Niesklasyfikowane Thermionic Culture
- Niesklasyfikowane Watercool
- Niesklasyfikowane Moultrie
- Niesklasyfikowane Skaarhoj
- Niesklasyfikowane Whitestone
- Niesklasyfikowane BMB
- Niesklasyfikowane Cloud
- Niesklasyfikowane Sandia Aerospace
- Niesklasyfikowane EK Water Blocks
- Niesklasyfikowane Lamptron
- Niesklasyfikowane Gudsen
- Niesklasyfikowane Zendure
- Niesklasyfikowane Envertech
- Niesklasyfikowane Prism Sound
- Niesklasyfikowane MoFi
- Niesklasyfikowane ID-Tech
- Niesklasyfikowane FSP/Fortron
- Niesklasyfikowane IDIS
- Niesklasyfikowane Fixpoint
- Niesklasyfikowane Enerdrive
- Niesklasyfikowane Respironics
- Niesklasyfikowane TESLA Electronics
- Niesklasyfikowane Intesis
- Niesklasyfikowane Nethix
- Niesklasyfikowane Pluto
- Niesklasyfikowane Laine
- Niesklasyfikowane 3Doodler
- Niesklasyfikowane Middle Atlantic Products
- Niesklasyfikowane Doepke
- Niesklasyfikowane Loctite
- Niesklasyfikowane Antelope
- Niesklasyfikowane Astera
- Niesklasyfikowane Polyend
- Niesklasyfikowane Sabco
- Niesklasyfikowane Sensative
- Niesklasyfikowane Plasma Cloud
- Niesklasyfikowane Flo
- Niesklasyfikowane Sheeran Looper
- Niesklasyfikowane Applico
- Niesklasyfikowane Jungle Gym
- Niesklasyfikowane Smart Media
- Niesklasyfikowane Code
- Niesklasyfikowane Mivar
- Niesklasyfikowane The Joy Factory
- Niesklasyfikowane Veber
- Niesklasyfikowane Edwards
- Niesklasyfikowane Grand Effects
- Niesklasyfikowane SunPower
- Niesklasyfikowane Westland
- Niesklasyfikowane Black Line
- Niesklasyfikowane Enbrighten
- Niesklasyfikowane Albert Heijn
- Niesklasyfikowane Yphix
- Niesklasyfikowane TAURUS Titanium
- Niesklasyfikowane Magliner
- Niesklasyfikowane Comfortisse
- Niesklasyfikowane Cayin
- Niesklasyfikowane Videotel Digital
- Niesklasyfikowane Zylight
- Niesklasyfikowane Smith-Victor
- Niesklasyfikowane HuddleCamHD
- Niesklasyfikowane MooreCo
- Niesklasyfikowane BIOS Living
- Niesklasyfikowane Connection
- Niesklasyfikowane Blind Spot
- Niesklasyfikowane Badiona
- Niesklasyfikowane VMV
- Niesklasyfikowane Telmax
- Niesklasyfikowane Exelpet
- Niesklasyfikowane Aplic
- Niesklasyfikowane Imarflex
- Niesklasyfikowane Tempmate
- Niesklasyfikowane Stalco
- Niesklasyfikowane Carlsbro
- Niesklasyfikowane Ventev
- Niesklasyfikowane Mobotix
- Niesklasyfikowane Steelbody
- Niesklasyfikowane PureLink
- Niesklasyfikowane UNYKAch
- Niesklasyfikowane VAVA
- Niesklasyfikowane Mammut
- Niesklasyfikowane Modbap Modular
- Niesklasyfikowane Bluestork
- Niesklasyfikowane INOGENI
- Niesklasyfikowane Carry-on
- Niesklasyfikowane AddLiving
- Niesklasyfikowane IOIO
- Niesklasyfikowane Nimbus
- Niesklasyfikowane Coca-Cola
- Niesklasyfikowane City Theatrical
- Niesklasyfikowane Acros
- Niesklasyfikowane Redback Technologies
- Niesklasyfikowane Vent-A-Hood
- Niesklasyfikowane GoXtreme
- Niesklasyfikowane Bome
- Niesklasyfikowane One Control
- Niesklasyfikowane EQ Acoustics
- Niesklasyfikowane AV Tool
- Niesklasyfikowane Aquael
- Niesklasyfikowane NEXTO DI
- Niesklasyfikowane Thermarest
- Niesklasyfikowane Fortinge
- Niesklasyfikowane RF-Links
- Niesklasyfikowane LiveU
- Niesklasyfikowane Austral
- Niesklasyfikowane Luxul
- Niesklasyfikowane Cherub
- Niesklasyfikowane ProLights
- Niesklasyfikowane Xinfrared
- Niesklasyfikowane Brizo
- Niesklasyfikowane Europalms
- Niesklasyfikowane DuroStar
- Niesklasyfikowane Waterstone
- Niesklasyfikowane Huslog
- Niesklasyfikowane Mr Steam
- Niesklasyfikowane DVDO
- Niesklasyfikowane A-Designs
- Niesklasyfikowane Henry Engineering
- Niesklasyfikowane Primacoustic
- Niesklasyfikowane HomeCraft
- Niesklasyfikowane Heusinkveld
- Niesklasyfikowane EnOcean
- Niesklasyfikowane Storcube
- Niesklasyfikowane Varia
- Niesklasyfikowane Gurari
- Niesklasyfikowane Fezz
- Niesklasyfikowane ASI
- Niesklasyfikowane Lexivon
- Niesklasyfikowane Swiss Eye
- Niesklasyfikowane Cane Creek
- Niesklasyfikowane EPEVER
- Niesklasyfikowane KED
- Niesklasyfikowane Caberg
- Niesklasyfikowane Exped
- Niesklasyfikowane Lawn Star
- Niesklasyfikowane Edouard Rousseau
- Niesklasyfikowane GameDay
- Niesklasyfikowane Sparkle
- Niesklasyfikowane Söll
- Niesklasyfikowane X-Lite
- Niesklasyfikowane AXESS
- Niesklasyfikowane Glemm
- Niesklasyfikowane Ridem
- Niesklasyfikowane StarIink
- Niesklasyfikowane Noyafa
- Niesklasyfikowane Envertec
- Niesklasyfikowane Nordic Winter
- Niesklasyfikowane Volcano
- Niesklasyfikowane Wire Technologies
- Niesklasyfikowane Taco Tuesday
- Niesklasyfikowane CEEM
- Niesklasyfikowane IMM Photonics
- Niesklasyfikowane Field Optics
- Niesklasyfikowane Robern
- Niesklasyfikowane Signature Hardware
- Niesklasyfikowane GRAUGEAR
- Niesklasyfikowane Sure Petcare
- Niesklasyfikowane Sortimo
- Niesklasyfikowane Livall
- Niesklasyfikowane Beaphar
- Niesklasyfikowane Catit
- Niesklasyfikowane WarmlyYours
- Niesklasyfikowane Mebby
- Niesklasyfikowane TONI&GUY
- Niesklasyfikowane Balam Rush
- Niesklasyfikowane Roesle
- Niesklasyfikowane Oreg
- Niesklasyfikowane Karran
- Niesklasyfikowane OOONO
- Niesklasyfikowane CaviLock
- Niesklasyfikowane Origin Storage
- Niesklasyfikowane Kostal
- Niesklasyfikowane Stamos
- Niesklasyfikowane Ulsonix
- Niesklasyfikowane Stamony
- Niesklasyfikowane Uniprodo
- Niesklasyfikowane Triplett
- Niesklasyfikowane RC Allen
- Niesklasyfikowane Bulgin
- Niesklasyfikowane Pure 100
- Niesklasyfikowane STANDARD
- Niesklasyfikowane BigBlue
- Niesklasyfikowane Plastkon
- Niesklasyfikowane Tele Vue
- Niesklasyfikowane Wiesenfield
- Niesklasyfikowane Ferrofish
- Niesklasyfikowane Luxli
- Niesklasyfikowane Blonder Tongue
- Niesklasyfikowane Crystal Video
- Niesklasyfikowane HPRC
- Niesklasyfikowane Platypus
- Niesklasyfikowane Petite Chérie
- Niesklasyfikowane Njoy
- Niesklasyfikowane Studio Titan
- Niesklasyfikowane AstrHori
- Niesklasyfikowane Icron
- Niesklasyfikowane Pyrex
- Niesklasyfikowane ProFlo
- Niesklasyfikowane Trezor
- Niesklasyfikowane Yamazen
- Niesklasyfikowane Really Right Stuff
- Niesklasyfikowane Decimator
- Niesklasyfikowane Chimera
- Niesklasyfikowane ButtKicker
- Niesklasyfikowane Tilta
- Niesklasyfikowane PAG
- Niesklasyfikowane NeoMounts
- Niesklasyfikowane Western Co.
- Niesklasyfikowane Ruggard
- Niesklasyfikowane DiversiTech
- Niesklasyfikowane Violectric
- Niesklasyfikowane Aalberg Audio
- Niesklasyfikowane OM SYSTEM
- Niesklasyfikowane PoLabs
- Niesklasyfikowane Bolin Technology
- Niesklasyfikowane Taiji
- Niesklasyfikowane Total Chef
- Niesklasyfikowane Evooch
- Niesklasyfikowane Total
- Niesklasyfikowane Kolcraft
- Niesklasyfikowane Fellow
- Niesklasyfikowane Digi-Pas
- Niesklasyfikowane Klauke
- Niesklasyfikowane Axler
- Niesklasyfikowane Pfister
- Niesklasyfikowane Symmons
- Niesklasyfikowane Gerber
- Niesklasyfikowane Royale
- Niesklasyfikowane Venicci
- Niesklasyfikowane Das Keyboard
- Niesklasyfikowane Schaffner
- Niesklasyfikowane Vitec
- Niesklasyfikowane Nicols
- Niesklasyfikowane Matterport
- Niesklasyfikowane Physa
- Niesklasyfikowane ARNOLD Lichttechnik
- Niesklasyfikowane Moomin
- Niesklasyfikowane Belulu
- Niesklasyfikowane Jedo
- Niesklasyfikowane Bayco
- Niesklasyfikowane Dinstar
- Niesklasyfikowane Noordi
- Niesklasyfikowane Corona
- Niesklasyfikowane Coors Light
- Niesklasyfikowane Arco
- Niesklasyfikowane KoolScapes
- Niesklasyfikowane Netter Vibration
- Niesklasyfikowane Califone
- Niesklasyfikowane Dynon Avionics
- Niesklasyfikowane Uvex
- Niesklasyfikowane UAvionix
- Niesklasyfikowane LARQ
- Niesklasyfikowane ORCA
- Niesklasyfikowane YA-MAN
- Niesklasyfikowane CRAFT + MAIN
- Niesklasyfikowane V-Tone
- Niesklasyfikowane Hellberg
- Niesklasyfikowane Stelzner
- Niesklasyfikowane LightKeeper Pro
- Niesklasyfikowane Cressi
- Niesklasyfikowane Singercon
- Niesklasyfikowane BMAX
- Niesklasyfikowane Pivo
- Niesklasyfikowane Sharkbite
- Niesklasyfikowane CatSynth
- Niesklasyfikowane Lantus
- Niesklasyfikowane Pitsos
- Niesklasyfikowane Lively
- Niesklasyfikowane Ember
- Niesklasyfikowane ACOPower
- Niesklasyfikowane Sifflus
- Niesklasyfikowane GeoBox
- Niesklasyfikowane Cosi Home
- Niesklasyfikowane Clean Paper
- Niesklasyfikowane URC
- Niesklasyfikowane Advanced Network Devices
- Niesklasyfikowane Telycam
- Niesklasyfikowane SafeMi
- Niesklasyfikowane XTRARM
- Niesklasyfikowane Rock N Roller
Najnowsze instrukcje dla Niesklasyfikowane

29 Stycznia 2025

29 Stycznia 2025

29 Stycznia 2025

29 Stycznia 2025

29 Stycznia 2025

29 Stycznia 2025

29 Stycznia 2025

29 Stycznia 2025

29 Stycznia 2025

29 Stycznia 2025