Instrukcja obsługi Microchip MCP111
Microchip
Niesklasyfikowane
MCP111
Przeczytaj poniżej 📖 instrukcję obsługi w języku polskim dla Microchip MCP111 (8 stron) w kategorii Niesklasyfikowane. Ta instrukcja była pomocna dla 10 osób i została oceniona przez 2 użytkowników na średnio 4.5 gwiazdek
Strona 1/8
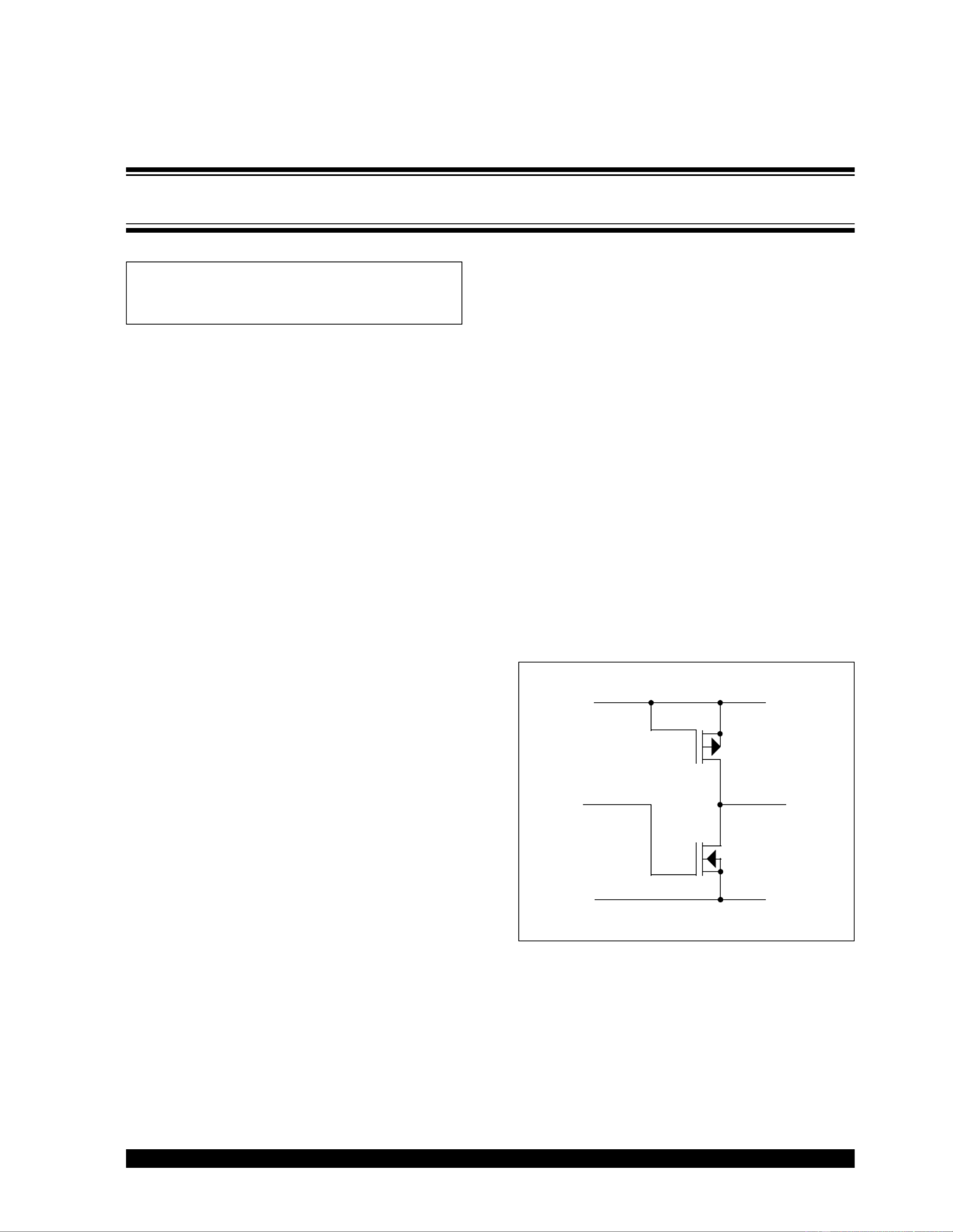
2002 Microchip Technology Inc. DS00820A-page 1
MAN820
INTRODUCTION
Semiconductor manufacturers have designed several
types of circuit supervisors with varying types of func-
tionality over the past few years. Some supervisors
incorporate watchdog features as well as complex func-
tions, such as programmable threshold levels. As it
turns out, most system supervisor data sheets address
typical supervisor functions related to Power-on Reset,
power-down, and brown-out conditions. In order to
serve a wide customer base, semiconductor manufac-
turers should also address system supervisors
designed into systems where microcontrollers (MCUs)
and programmable logic devices (PLDs) are pro-
grammed in-circuit. Programming PICmicro® micro-
controllers in this fashion is known as In-Circuit Serial
ProgrammingTM (ICSPTM), which can be implemented
for a variety of reasons, including field upgrades.
System supervisors are available with several types of
output stages. Some have active low output stages,
some active high, and there are others similar to the
MCP100, with output stages that drive RESET lines
both high and low. Supervisor output stages are
extremely important to understand for ICSP circuitry,
since programming equipment actually drives the out-
put stages when the MCU or PLD is being pro-
grammed. While there is a wide variety of supervisor
types available on the market, this Application Note pri-
marily focuses on the MCP120, which has an open
drain, active low, output stage. Even though the
MCP120 was chosen for this ICSP example, the design
techniques included below are intended to guide
designers with supervisors of all kinds for ICSP
circuitry.
CIRCUITRY BACKGROUND
MCP120 Output Stage
A simplified schematic for the MCP120 output stage is
shown in Figure 1. Nominally, the output stage of the
MCP120 can handle sinking less than 1 mA of current
in a high impedance state. That is, when the output is
not driving low and when a voltage is applied to the out-
put that is higher than the power supply level, the out-
put can handle sinking less than 1 mA. Other pertinent
electrical specifications for the device are shown in the
data sheet, which includes test conditions for the chip.
The MCP120 has an open drain output, though it is not
a true open drain. Specifically, the PMOS transistor on
the high side of the output stage is diode-connected, as
shown in Figure 1. When the voltage applied to the out-
put of the supervisor exceeds the power supply for the
chip, the PMOS transistor acts like a forward biased
diode. Lastly, since the output stage is open drain, a
pull-up resistor is required between the supervisor out-
put and VDD.
FIGURE 1: MCP120 output stage simplified.
Author: Ken Dietz
Microchip Technology Inc.
VDD
OutIn
GND
System Supervisors in ICSPTM Architectures
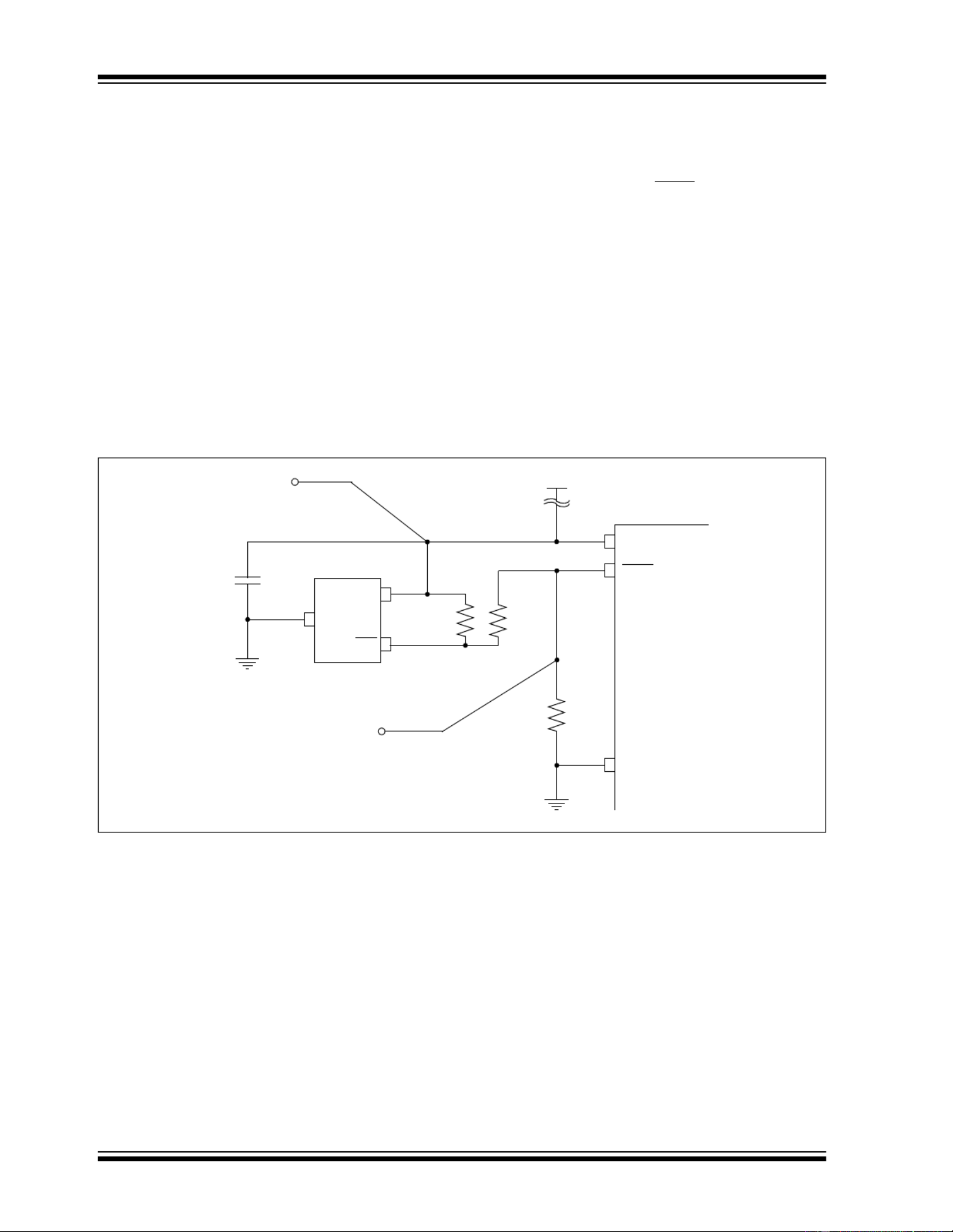
AN820
DS00820A-page 2 2002 Microchip Technology Inc.
ICSP Circuit Configuration
A schematic showing ICSP circuitry with the MCP120 is
shown in Figure 2. A current limiting resistor, RCL, limits
the current driven into the output stage of the supervisor
when the programming voltage is applied to the MCU.
A pull-up resistor, RPU, is placed between the supervi-
sor output and VDD, since the MCP120 output is open
drain and active low. Calculations for the resistors are
explained in the Design Methodology section.
The pull-down resistor, RPD, shown in Figure 2 is useful
during power-up and power-down sequences. Supervi-
sor functionality is not specified at power supply volt-
ages typically lower than 1 Volt, so the output stage of
the supervisor could be in a high impedance state. If
the supervisor output is high impedance and voltage is
applied to the MCU from an external source, the pro-
cessor could potentially run its program until the super-
visor takes over and resets the MCU again. This is
especially important in systems where multiple printed
circuit boards are interfaced together and a secondary
board might end up driving the MCU I/O pins before
power is applied to the primary board.
Since the voltage on the MCLR pin on a PICmicro®
MCU is very close to the power supply level, RPD can
be fairly large to minimize current consumption when
the circuit is normally operating. Furthermore, during
program and verify sequences, up to 13.25 Volts are
applied to the pull-down resistor. Because of this, R
PD
should also be large enough to minimize current con-
sumption for the programming voltage supply. A value
of 100 kΩ (+/-5%) results in a maximum of 140 µA
when VPP is applied to the microcontroller, or 134 µA if
1% resistors are used, which is a small load for most
programmers. For battery powered applications, sub-
stantially larger valued resistors may be desirable for
this purpose.
FIGURE 2: Active low open drain ICSP circuit.
Key Programmer Specifications
The PRO MATE® II and the ICSP Socket Module, part
number AC004004, were used to test the circuit shown
in Figure 2. Current drive for the programming voltage
signal and current drive for the power supply signals are
critical specifications for the ICSP socket module. For
the VPP signal, the output of the ICSP module can pro-
vide as much as 100 mA, and for the power supply sig-
nal, the ICSP socket module can drive as much as
400 mA. Furthermore, the PRO MATE II programs
MCUs only at 5 Volts. However, it does have the capa-
bility to verify the memory contents of microcontrollers
at power supply levels ranging from 2.5 Volts to
5.5 Volts.
Another important aspect to consider for In-Circuit
Serial Programming includes the cable length for the
interface. Not only are sufficient current drive capabili-
ties required, but if a lengthy cable is used, reflections
and oscillations may cause programming errors.
Because of this phenomenon, manufacturers imple-
menting ICSP architectures should keep their cables
as short as possible. The circuits tested for the purpose
of this article implemented the ICSP cable that is nor-
mally shipped with the ICSP module, which is about 6
feet long. Lastly, the end of the cable connected to the
printed circuit board was modified to interface to a
modular connector.
VDD
(Programmer Supplied)
Bypass
Capacitor MCP120
VSS
VDD
RST
RPU RCL
3.3 Volts
Isolation
Microcontroller
VDD
MCLR
VSS
RPD
VPP
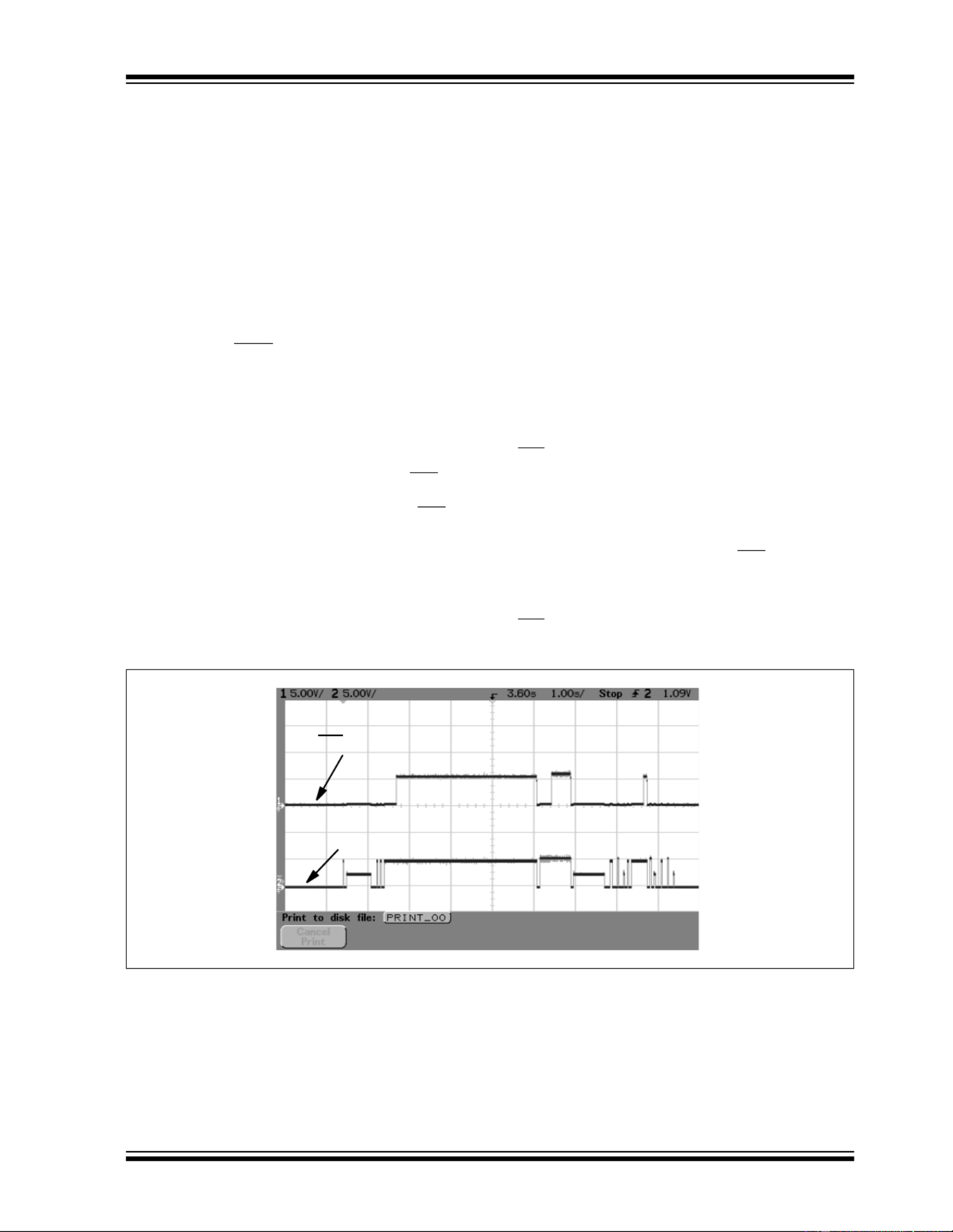
2002 Microchip Technology Inc. DS00820A-page 3
AN820
DESIGN METHODOLOGY
Absolute Maximum Clarifications
A critical question about designing this type of circuit
revolves around the worst case voltages and currents
applied to the circuit. Additionally, a circuit designer
needs to determine whether or not the absolute maxi-
mum ratings for any of the components on the board
are being exceeded. Knowing the largest voltage drops
across the circuit enables a designer to calculate the
resistor sizes so that absolute maximum ratings for all
components are not exceeded. From the PIC16LF872
data sheet (DS30221), the maximum voltage that can
be applied to the MCLR pin of the microcontroller can-
not exceed 13.25 Volts. Additionally, the maximum volt-
age that can be applied to any pin on the MCP120, with
respect to VSS, is from -0.6 Volts to (VDD + 1.0) Volts.
Calculations
Since the lowest voltage applied to V
DD is 0 Volts dur-
ing programming, the voltage applied to the RST pin
should not exceed 1.0 Volt. Knowing this, the circuit
can be designed to limit the voltage applied to RST to
a nominal 700 mV. This means that RCL has to drop at
most 12.55 Volts. If the assumption is made that all of
the current flowing through RCL is also flowing through
RPU when the supervisor output is high impedance,
then RPU needs to be 700 and RΩCL should be at least
12.55kΩ. For standard 1% tolerance resistors, 715Ω
and 12.7kΩ would be the correct selections for R
PU
and RCL, respectively. If standard 5% resistors are
being used in the circuit, then 750Ω and 13 kΩ are the
correct solutions.
In order to determine if this combination of resistors will
work in the design, all of the permutations for power
supply levels and output drive levels for the supervisor
must include calculations for minimum and maximum
currents and voltages in the circuit. While the microcon-
troller is being programmed, power supply levels can
be as high as 5.5 Volts for the PIC16LF872 during ver-
ify operations. This can be further clarified by reviewing
Figure 3. With this in mind, minimum and maximum cir-
cuit calculations show that this selection of resistors will
work within tolerance.
Results
Figure 3 shows a successful programming waveform
for two key nodes in an ICSP circuit. Channel 1 mea-
sured the voltage levels on the supervisor output pin,
RST, and Channel 2 measured the voltage applied to
the node between the power supply pins of the micro-
controller and the supervisor. The circuit schematic for
this system was shown in Figure 2. Notice that
Channel 2 in Figure 3 shows the verification voltage
levels at 5.5 Volts and 2.5 Volts. Notice also that Chan-
nel 1 shows the voltage on the RST pin at about
700 mV when the supervisor output is driving low.
Lastly, when the supervisor output is high impedance,
Channel 1 shows a voltage level of 5.7 Volts applied to
RST, which is about 700 mV above the power supply.
FIGURE 3: Successful programming waveform.
RST Node
VDD Node
Specyfikacje produktu
Marka: | Microchip |
Kategoria: | Niesklasyfikowane |
Model: | MCP111 |
Potrzebujesz pomocy?
Jeśli potrzebujesz pomocy z Microchip MCP111, zadaj pytanie poniżej, a inni użytkownicy Ci odpowiedzą
Instrukcje Niesklasyfikowane Microchip

15 Stycznia 2025

15 Stycznia 2025

15 Stycznia 2025

15 Stycznia 2025

15 Stycznia 2025

15 Stycznia 2025

15 Stycznia 2025

15 Stycznia 2025

15 Stycznia 2025

15 Stycznia 2025
Instrukcje Niesklasyfikowane
- Niesklasyfikowane Sony
- Niesklasyfikowane Bauknecht
- Niesklasyfikowane Yamaha
- Niesklasyfikowane Ikea
- Niesklasyfikowane Hoshizaki
- Niesklasyfikowane Samsung
- Niesklasyfikowane Tesy
- Niesklasyfikowane Kindercraft
- Niesklasyfikowane PeakTech
- Niesklasyfikowane Bertazzoni
- Niesklasyfikowane Electrolux
- Niesklasyfikowane Gamdias
- Niesklasyfikowane Tenda
- Niesklasyfikowane AEG
- Niesklasyfikowane Fellowes
- Niesklasyfikowane Balay
- Niesklasyfikowane Leica
- Niesklasyfikowane Beko
- Niesklasyfikowane Teka
- Niesklasyfikowane Sven
- Niesklasyfikowane ChamSys
- Niesklasyfikowane LG
- Niesklasyfikowane Worx
- Niesklasyfikowane Küppersbusch
- Niesklasyfikowane Smeg
- Niesklasyfikowane Motorola
- Niesklasyfikowane Götze & Jensen
- Niesklasyfikowane Dreame
- Niesklasyfikowane Beurer
- Niesklasyfikowane Peugeot
- Niesklasyfikowane Stabo
- Niesklasyfikowane Logitech
- Niesklasyfikowane Gram
- Niesklasyfikowane Sanitas
- Niesklasyfikowane Spektrum
- Niesklasyfikowane Caso
- Niesklasyfikowane Amica
- Niesklasyfikowane Xiaomi
- Niesklasyfikowane Gorenje
- Niesklasyfikowane Etna
- Niesklasyfikowane Joy-It
- Niesklasyfikowane LERAN
- Niesklasyfikowane Lego
- Niesklasyfikowane SHX
- Niesklasyfikowane President
- Niesklasyfikowane MyPhone
- Niesklasyfikowane Sharp
- Niesklasyfikowane BeamZ
- Niesklasyfikowane Huawei
- Niesklasyfikowane Supermicro
- Niesklasyfikowane TCL
- Niesklasyfikowane Braun
- Niesklasyfikowane Russell Hobbs
- Niesklasyfikowane Pioneer
- Niesklasyfikowane Statron
- Niesklasyfikowane Lenovo
- Niesklasyfikowane Tefal
- Niesklasyfikowane Honda
- Niesklasyfikowane TP-Link
- Niesklasyfikowane Voltcraft
- Niesklasyfikowane Milwaukee
- Niesklasyfikowane Philips
- Niesklasyfikowane Livoo
- Niesklasyfikowane Plantronics
- Niesklasyfikowane SilverCrest
- Niesklasyfikowane Endress
- Niesklasyfikowane Dometic
- Niesklasyfikowane Gigabyte
- Niesklasyfikowane Acer
- Niesklasyfikowane Realme
- Niesklasyfikowane Ultimate Speed
- Niesklasyfikowane Technics
- Niesklasyfikowane Stihl
- Niesklasyfikowane Bosch
- Niesklasyfikowane Yato
- Niesklasyfikowane Xblitz
- Niesklasyfikowane Dash
- Niesklasyfikowane Epson
- Niesklasyfikowane JBL
- Niesklasyfikowane Parkside
- Niesklasyfikowane Hikvision
- Niesklasyfikowane Candy
- Niesklasyfikowane GW Instek
- Niesklasyfikowane Maxi-Cosi
- Niesklasyfikowane Onkyo
- Niesklasyfikowane Volkswagen
- Niesklasyfikowane Whirlpool
- Niesklasyfikowane Grillmeister
- Niesklasyfikowane IPGARD
- Niesklasyfikowane Lionelo
- Niesklasyfikowane Fujitsu
- Niesklasyfikowane Ferroli
- Niesklasyfikowane Edision
- Niesklasyfikowane Global
- Niesklasyfikowane Thule
- Niesklasyfikowane Roland
- Niesklasyfikowane Cramer
- Niesklasyfikowane Miele
- Niesklasyfikowane HyperX
- Niesklasyfikowane Stiga
- Niesklasyfikowane Easy Home
- Niesklasyfikowane Hacienda
- Niesklasyfikowane LC-Power
- Niesklasyfikowane Waterco
- Niesklasyfikowane Geemarc
- Niesklasyfikowane Nokia
- Niesklasyfikowane Scott
- Niesklasyfikowane Brentwood
- Niesklasyfikowane Nobo
- Niesklasyfikowane Midea
- Niesklasyfikowane Toolcraft
- Niesklasyfikowane Axkid
- Niesklasyfikowane KEF
- Niesklasyfikowane Festool
- Niesklasyfikowane Kärcher
- Niesklasyfikowane Bose
- Niesklasyfikowane Severin
- Niesklasyfikowane Hisense
- Niesklasyfikowane Berg
- Niesklasyfikowane Infiniton
- Niesklasyfikowane EZVIZ
- Niesklasyfikowane Conceptronic
- Niesklasyfikowane Singer
- Niesklasyfikowane Panasonic
- Niesklasyfikowane StarTech.com
- Niesklasyfikowane Promethean
- Niesklasyfikowane Bavaria By Einhell
- Niesklasyfikowane Theben
- Niesklasyfikowane Klipsch
- Niesklasyfikowane Muse
- Niesklasyfikowane Liebherr
- Niesklasyfikowane Canon
- Niesklasyfikowane Mio
- Niesklasyfikowane Crestron
- Niesklasyfikowane Withings
- Niesklasyfikowane Bestway
- Niesklasyfikowane Viewsonic
- Niesklasyfikowane Behringer
- Niesklasyfikowane Asus
- Niesklasyfikowane Nedis
- Niesklasyfikowane Stanley
- Niesklasyfikowane Nexa
- Niesklasyfikowane Jura
- Niesklasyfikowane AG Neovo
- Niesklasyfikowane Be Cool
- Niesklasyfikowane Allen & Heath
- Niesklasyfikowane Enphase
- Niesklasyfikowane Rossmax
- Niesklasyfikowane IK Multimedia
- Niesklasyfikowane Reolink
- Niesklasyfikowane American DJ
- Niesklasyfikowane Medion
- Niesklasyfikowane Boss
- Niesklasyfikowane Black & Decker
- Niesklasyfikowane OK
- Niesklasyfikowane Lenco
- Niesklasyfikowane TRENDnet
- Niesklasyfikowane Audioline
- Niesklasyfikowane Polar
- Niesklasyfikowane Max Pro
- Niesklasyfikowane Scheppach
- Niesklasyfikowane Fujifilm
- Niesklasyfikowane Proxxon
- Niesklasyfikowane Adler
- Niesklasyfikowane Bluetti
- Niesklasyfikowane BaByliss
- Niesklasyfikowane Marquant
- Niesklasyfikowane Subaru
- Niesklasyfikowane MSI
- Niesklasyfikowane Ford
- Niesklasyfikowane Hoover
- Niesklasyfikowane Toshiba
- Niesklasyfikowane Tesla
- Niesklasyfikowane Deditec
- Niesklasyfikowane Westinghouse
- Niesklasyfikowane D-Link
- Niesklasyfikowane Rinnai
- Niesklasyfikowane Majestic
- Niesklasyfikowane Hendi
- Niesklasyfikowane Quigg
- Niesklasyfikowane Jensen
- Niesklasyfikowane August
- Niesklasyfikowane Niceboy
- Niesklasyfikowane Maytag
- Niesklasyfikowane Hazet
- Niesklasyfikowane Bluebird
- Niesklasyfikowane Vertiv
- Niesklasyfikowane Yealink
- Niesklasyfikowane Domo
- Niesklasyfikowane Conair
- Niesklasyfikowane GE
- Niesklasyfikowane ILive
- Niesklasyfikowane Ardes
- Niesklasyfikowane Taurus
- Niesklasyfikowane VitalMaxx
- Niesklasyfikowane RIKON
- Niesklasyfikowane Ring
- Niesklasyfikowane Orbegozo
- Niesklasyfikowane Native Instruments
- Niesklasyfikowane Garmin
- Niesklasyfikowane Blaupunkt
- Niesklasyfikowane Profoon
- Niesklasyfikowane Brandt
- Niesklasyfikowane Vivax
- Niesklasyfikowane ATen
- Niesklasyfikowane IOptron
- Niesklasyfikowane Grizzly
- Niesklasyfikowane Siemens
- Niesklasyfikowane Teac
- Niesklasyfikowane Speed-Link
- Niesklasyfikowane Gardena
- Niesklasyfikowane Casio
- Niesklasyfikowane Iiyama
- Niesklasyfikowane Lincoln Electric
- Niesklasyfikowane BRITA
- Niesklasyfikowane Metra
- Niesklasyfikowane Thrustmaster
- Niesklasyfikowane Volvo
- Niesklasyfikowane Evolveo
- Niesklasyfikowane Stadler Form
- Niesklasyfikowane Ambiano
- Niesklasyfikowane DeWalt
- Niesklasyfikowane Bbf
- Niesklasyfikowane Danby
- Niesklasyfikowane Martin Logan
- Niesklasyfikowane Dual
- Niesklasyfikowane Einhell
- Niesklasyfikowane Grundig
- Niesklasyfikowane APC
- Niesklasyfikowane Hegel
- Niesklasyfikowane Alcatel
- Niesklasyfikowane Kiloview
- Niesklasyfikowane Suzuki
- Niesklasyfikowane Haier
- Niesklasyfikowane Sigma
- Niesklasyfikowane Homedics
- Niesklasyfikowane Remington
- Niesklasyfikowane Eberle
- Niesklasyfikowane HP
- Niesklasyfikowane KKT Kolbe
- Niesklasyfikowane Cylinda
- Niesklasyfikowane Teltonika
- Niesklasyfikowane S.M.S.L
- Niesklasyfikowane Genesis
- Niesklasyfikowane Jocel
- Niesklasyfikowane Soundmaster
- Niesklasyfikowane Prixton
- Niesklasyfikowane Hyundai
- Niesklasyfikowane Silverline
- Niesklasyfikowane Blomberg
- Niesklasyfikowane Bimar
- Niesklasyfikowane Line 6
- Niesklasyfikowane Rowenta
- Niesklasyfikowane Brother
- Niesklasyfikowane Mesko
- Niesklasyfikowane Master
- Niesklasyfikowane Husqvarna
- Niesklasyfikowane Honeywell
- Niesklasyfikowane DAP-Audio
- Niesklasyfikowane Creative
- Niesklasyfikowane Concept
- Niesklasyfikowane Joie
- Niesklasyfikowane Manhattan
- Niesklasyfikowane Chauvet
- Niesklasyfikowane Strong
- Niesklasyfikowane Cybex
- Niesklasyfikowane Honor
- Niesklasyfikowane Heritage Audio
- Niesklasyfikowane Fisher & Paykel
- Niesklasyfikowane Cotek
- Niesklasyfikowane Tripp Lite
- Niesklasyfikowane Shure
- Niesklasyfikowane EWON
- Niesklasyfikowane ECG
- Niesklasyfikowane IRobot
- Niesklasyfikowane Indesit
- Niesklasyfikowane Amazfit
- Niesklasyfikowane Steinel
- Niesklasyfikowane Makita
- Niesklasyfikowane Ilve
- Niesklasyfikowane Mikrotik
- Niesklasyfikowane Hecht
- Niesklasyfikowane Denon
- Niesklasyfikowane Akasa
- Niesklasyfikowane Unold
- Niesklasyfikowane Swann
- Niesklasyfikowane Krontaler
- Niesklasyfikowane Truma
- Niesklasyfikowane Kwikset
- Niesklasyfikowane Mercury
- Niesklasyfikowane Empress Effects
- Niesklasyfikowane Carel
- Niesklasyfikowane Petzl
- Niesklasyfikowane Nikon
- Niesklasyfikowane Shimano
- Niesklasyfikowane Viking
- Niesklasyfikowane Antari
- Niesklasyfikowane Medela
- Niesklasyfikowane Block
- Niesklasyfikowane Rapid
- Niesklasyfikowane Ozito
- Niesklasyfikowane Primus
- Niesklasyfikowane Kodak
- Niesklasyfikowane Phoenix Gold
- Niesklasyfikowane Nodor
- Niesklasyfikowane Forza
- Niesklasyfikowane CATA
- Niesklasyfikowane Testo
- Niesklasyfikowane HeiTech
- Niesklasyfikowane Audac
- Niesklasyfikowane Cisco
- Niesklasyfikowane Baby Brezza
- Niesklasyfikowane Primera
- Niesklasyfikowane SBS
- Niesklasyfikowane Draper
- Niesklasyfikowane Cambridge
- Niesklasyfikowane Fuxtec
- Niesklasyfikowane Smart
- Niesklasyfikowane ORNO
- Niesklasyfikowane Fiap
- Niesklasyfikowane Cooler Master
- Niesklasyfikowane Sanus
- Niesklasyfikowane TFA
- Niesklasyfikowane Dyson
- Niesklasyfikowane Chauvin Arnoux
- Niesklasyfikowane Broan
- Niesklasyfikowane Hotpoint
- Niesklasyfikowane Kenwood
- Niesklasyfikowane Scosche
- Niesklasyfikowane Icy Box
- Niesklasyfikowane Sungrow
- Niesklasyfikowane NuPrime
- Niesklasyfikowane Polk
- Niesklasyfikowane Hasbro
- Niesklasyfikowane V-Zug
- Niesklasyfikowane Moxa
- Niesklasyfikowane Deye
- Niesklasyfikowane Trisa
- Niesklasyfikowane DJI
- Niesklasyfikowane RYOBI
- Niesklasyfikowane Synology
- Niesklasyfikowane Godex
- Niesklasyfikowane Kugoo
- Niesklasyfikowane Alpine
- Niesklasyfikowane Wolf Garten
- Niesklasyfikowane Natec
- Niesklasyfikowane Knog
- Niesklasyfikowane Zenit
- Niesklasyfikowane Gembird
- Niesklasyfikowane Scala
- Niesklasyfikowane ZTE
- Niesklasyfikowane Godox
- Niesklasyfikowane Uni-T
- Niesklasyfikowane Røde
- Niesklasyfikowane Ariston Thermo
- Niesklasyfikowane Zelmer
- Niesklasyfikowane Vango
- Niesklasyfikowane Hammersmith
- Niesklasyfikowane Chicco
- Niesklasyfikowane Mestic
- Niesklasyfikowane My Wall
- Niesklasyfikowane Chamberlain
- Niesklasyfikowane Dynaudio
- Niesklasyfikowane Paradigm
- Niesklasyfikowane Paladin
- Niesklasyfikowane Spin Master
- Niesklasyfikowane Lindy
- Niesklasyfikowane Olivetti
- Niesklasyfikowane PKM
- Niesklasyfikowane Ninja
- Niesklasyfikowane Medisana
- Niesklasyfikowane MaxCom
- Niesklasyfikowane Minox
- Niesklasyfikowane Cuisinart
- Niesklasyfikowane Zebra
- Niesklasyfikowane Bang & Olufsen
- Niesklasyfikowane Wilfa
- Niesklasyfikowane DSC
- Niesklasyfikowane Deltaco
- Niesklasyfikowane Cobra
- Niesklasyfikowane Flex
- Niesklasyfikowane JVC
- Niesklasyfikowane ZyXEL
- Niesklasyfikowane Auriol
- Niesklasyfikowane Konig & Meyer
- Niesklasyfikowane Trust
- Niesklasyfikowane V7
- Niesklasyfikowane Thor
- Niesklasyfikowane LogiLink
- Niesklasyfikowane Amana
- Niesklasyfikowane Stokke
- Niesklasyfikowane Memphis Audio
- Niesklasyfikowane Intergas
- Niesklasyfikowane Sandisk
- Niesklasyfikowane Grohe
- Niesklasyfikowane Dell
- Niesklasyfikowane Dacor
- Niesklasyfikowane Polaris
- Niesklasyfikowane Fitbit
- Niesklasyfikowane Axor
- Niesklasyfikowane GLORIA
- Niesklasyfikowane Yard Force
- Niesklasyfikowane IFM
- Niesklasyfikowane Spelsberg
- Niesklasyfikowane Hotpoint Ariston
- Niesklasyfikowane Ctek
- Niesklasyfikowane Krups
- Niesklasyfikowane Datapath
- Niesklasyfikowane Furrion
- Niesklasyfikowane Bialetti
- Niesklasyfikowane Silk'n
- Niesklasyfikowane Bomann
- Niesklasyfikowane U-Line
- Niesklasyfikowane Linksys
- Niesklasyfikowane Clean Air Optima
- Niesklasyfikowane Moulinex
- Niesklasyfikowane Teesa
- Niesklasyfikowane Cleanmaxx
- Niesklasyfikowane Ursus Trotter
- Niesklasyfikowane Ultimate
- Niesklasyfikowane Aprilia
- Niesklasyfikowane PS Audio
- Niesklasyfikowane PowerXL
- Niesklasyfikowane Jamo
- Niesklasyfikowane DEDRA
- Niesklasyfikowane Corsair
- Niesklasyfikowane Emerio
- Niesklasyfikowane Owon
- Niesklasyfikowane Focusrite
- Niesklasyfikowane Wood's
- Niesklasyfikowane Baumr-AG
- Niesklasyfikowane Nuna
- Niesklasyfikowane Google
- Niesklasyfikowane Create
- Niesklasyfikowane Rega
- Niesklasyfikowane Intex
- Niesklasyfikowane Biltema
- Niesklasyfikowane Oricom
- Niesklasyfikowane B.E.G.
- Niesklasyfikowane Crane
- Niesklasyfikowane H.Koenig
- Niesklasyfikowane InAlto
- Niesklasyfikowane CMI
- Niesklasyfikowane Hilti
- Niesklasyfikowane Eastron
- Niesklasyfikowane Meireles
- Niesklasyfikowane Revitive
- Niesklasyfikowane Digitus
- Niesklasyfikowane Salewa
- Niesklasyfikowane Fimi
- Niesklasyfikowane Oppo
- Niesklasyfikowane Cateye
- Niesklasyfikowane Thinkware
- Niesklasyfikowane Alesis
- Niesklasyfikowane Lowrance
- Niesklasyfikowane Tanita
- Niesklasyfikowane Anybus
- Niesklasyfikowane Melissa
- Niesklasyfikowane TechniSat
- Niesklasyfikowane Auna
- Niesklasyfikowane Vimar
- Niesklasyfikowane V-TAC
- Niesklasyfikowane Dahua Technology
- Niesklasyfikowane Schneider
- Niesklasyfikowane Deutz
- Niesklasyfikowane SABO
- Niesklasyfikowane Ledlenser
- Niesklasyfikowane Beper
- Niesklasyfikowane Infomir
- Niesklasyfikowane Eurolite
- Niesklasyfikowane Kyocera
- Niesklasyfikowane LD Systems
- Niesklasyfikowane Techno Line
- Niesklasyfikowane SuperTooth
- Niesklasyfikowane Foppapedretti
- Niesklasyfikowane Foreo
- Niesklasyfikowane Daikin
- Niesklasyfikowane Kospel
- Niesklasyfikowane EVOline
- Niesklasyfikowane Kubota
- Niesklasyfikowane Thetford
- Niesklasyfikowane TrueLife
- Niesklasyfikowane Eufy
- Niesklasyfikowane Stirling
- Niesklasyfikowane Ricoh
- Niesklasyfikowane Krüger&Matz
- Niesklasyfikowane TOGU
- Niesklasyfikowane SMART Technologies
- Niesklasyfikowane Mad Dog
- Niesklasyfikowane NZXT
- Niesklasyfikowane Audioengine
- Niesklasyfikowane Hozelock
- Niesklasyfikowane Playmobil
- Niesklasyfikowane MPM
- Niesklasyfikowane OneConcept
- Niesklasyfikowane Recaro
- Niesklasyfikowane Hori
- Niesklasyfikowane CDA
- Niesklasyfikowane Emos
- Niesklasyfikowane Sabrent
- Niesklasyfikowane AVMATRIX
- Niesklasyfikowane IMC Toys
- Niesklasyfikowane Philco
- Niesklasyfikowane Neff
- Niesklasyfikowane Seiko
- Niesklasyfikowane Renkforce
- Niesklasyfikowane Rollei
- Niesklasyfikowane Corbero
- Niesklasyfikowane Morphy Richards
- Niesklasyfikowane Zanussi
- Niesklasyfikowane Sekonic
- Niesklasyfikowane Hensel
- Niesklasyfikowane Sonel
- Niesklasyfikowane Pure
- Niesklasyfikowane NightStick
- Niesklasyfikowane Ravanson
- Niesklasyfikowane Crivit
- Niesklasyfikowane Marshall
- Niesklasyfikowane Zenec
- Niesklasyfikowane Audiotec Fischer
- Niesklasyfikowane Osram
- Niesklasyfikowane BaseTech
- Niesklasyfikowane Thermex
- Niesklasyfikowane AXA
- Niesklasyfikowane Traxxas
- Niesklasyfikowane Viessmann
- Niesklasyfikowane Perel
- Niesklasyfikowane Janitza
- Niesklasyfikowane Wagner
- Niesklasyfikowane Salta
- Niesklasyfikowane Fagor
- Niesklasyfikowane Redmond
- Niesklasyfikowane Sena
- Niesklasyfikowane Koenic
- Niesklasyfikowane Graco
- Niesklasyfikowane Trotec
- Niesklasyfikowane Autel
- Niesklasyfikowane Somfy
- Niesklasyfikowane Everdure
- Niesklasyfikowane Uniden
- Niesklasyfikowane Adder
- Niesklasyfikowane Ansmann
- Niesklasyfikowane Clarion
- Niesklasyfikowane Wacom
- Niesklasyfikowane Omron
- Niesklasyfikowane Netgear
- Niesklasyfikowane Cellular Line
- Niesklasyfikowane Thomson
- Niesklasyfikowane DiO
- Niesklasyfikowane Pro-Ject
- Niesklasyfikowane Dremel
- Niesklasyfikowane Texas Instruments
- Niesklasyfikowane Lastolite
- Niesklasyfikowane AVM
- Niesklasyfikowane La Crosse Technology
- Niesklasyfikowane Growatt
- Niesklasyfikowane Velux
- Niesklasyfikowane Izzy
- Niesklasyfikowane Fresh 'n Rebel
- Niesklasyfikowane Little Tikes
- Niesklasyfikowane Chipolino
- Niesklasyfikowane Velleman
- Niesklasyfikowane Ferguson
- Niesklasyfikowane BT
- Niesklasyfikowane Meec Tools
- Niesklasyfikowane Fusion
- Niesklasyfikowane BOYA
- Niesklasyfikowane WMF
- Niesklasyfikowane Korg
- Niesklasyfikowane ProfiCook
- Niesklasyfikowane Homematic IP
- Niesklasyfikowane Neumann
- Niesklasyfikowane DataVideo
- Niesklasyfikowane AL-KO
- Niesklasyfikowane One For All
- Niesklasyfikowane Klarstein
- Niesklasyfikowane BEEM
- Niesklasyfikowane Wharfedale
- Niesklasyfikowane Safety 1st
- Niesklasyfikowane Polti
- Niesklasyfikowane Totolink
- Niesklasyfikowane Victor Technology
- Niesklasyfikowane Danfoss
- Niesklasyfikowane JYSK
- Niesklasyfikowane Coyote
- Niesklasyfikowane Intertechno
- Niesklasyfikowane Magnat
- Niesklasyfikowane Black Box
- Niesklasyfikowane Lowepro
- Niesklasyfikowane Güde
- Niesklasyfikowane Arendo
- Niesklasyfikowane Revamp
- Niesklasyfikowane DreamGEAR
- Niesklasyfikowane Witt
- Niesklasyfikowane Victron Energy
- Niesklasyfikowane Delta Dore
- Niesklasyfikowane E-ast
- Niesklasyfikowane Hobby
- Niesklasyfikowane Manta
- Niesklasyfikowane Pyle
- Niesklasyfikowane CTA Digital
- Niesklasyfikowane Segway
- Niesklasyfikowane Gem Toys
- Niesklasyfikowane Texas
- Niesklasyfikowane Apple
- Niesklasyfikowane ELAC
- Niesklasyfikowane Lancom
- Niesklasyfikowane Adviti
- Niesklasyfikowane Crimson
- Niesklasyfikowane Dymo
- Niesklasyfikowane ATIKA
- Niesklasyfikowane Hauck
- Niesklasyfikowane Bikemate
- Niesklasyfikowane Zoom
- Niesklasyfikowane Iogear
- Niesklasyfikowane Cardo
- Niesklasyfikowane Panduit
- Niesklasyfikowane Intellinet
- Niesklasyfikowane Datalogic
- Niesklasyfikowane NGS
- Niesklasyfikowane CRUX
- Niesklasyfikowane Vaillant
- Niesklasyfikowane Beautifly
- Niesklasyfikowane Newline
- Niesklasyfikowane Bavaria
- Niesklasyfikowane Devolo
- Niesklasyfikowane Juwel
- Niesklasyfikowane Biostar
- Niesklasyfikowane Cecotec
- Niesklasyfikowane Artusi
- Niesklasyfikowane Vileda
- Niesklasyfikowane Dirt Devil
- Niesklasyfikowane Midland
- Niesklasyfikowane Marantz
- Niesklasyfikowane KitchenAid
- Niesklasyfikowane MARTOR
- Niesklasyfikowane AFK
- Niesklasyfikowane Waeco
- Niesklasyfikowane AOC
- Niesklasyfikowane Cougar
- Niesklasyfikowane Monster
- Niesklasyfikowane Sennheiser
- Niesklasyfikowane JANDY
- Niesklasyfikowane Esoteric
- Niesklasyfikowane Roidmi
- Niesklasyfikowane Jabra
- Niesklasyfikowane Chord
- Niesklasyfikowane Zipper
- Niesklasyfikowane Vivotek
- Niesklasyfikowane Eta
- Niesklasyfikowane Mount-It!
- Niesklasyfikowane Kingston
- Niesklasyfikowane Camry
- Niesklasyfikowane Vtech
- Niesklasyfikowane Steba
- Niesklasyfikowane Werma
- Niesklasyfikowane Perixx
- Niesklasyfikowane Peerless-AV
- Niesklasyfikowane Speco Technologies
- Niesklasyfikowane Medeli
- Niesklasyfikowane Suunto
- Niesklasyfikowane Showtec
- Niesklasyfikowane Weber
- Niesklasyfikowane Heckler Design
- Niesklasyfikowane Lenoxx
- Niesklasyfikowane Keurig
- Niesklasyfikowane Grundfos
- Niesklasyfikowane Bowers & Wilkins
- Niesklasyfikowane Samson
- Niesklasyfikowane EtiamPro
- Niesklasyfikowane EA Elektro Automatik
- Niesklasyfikowane Tineco
- Niesklasyfikowane Imperial
- Niesklasyfikowane Emporia
- Niesklasyfikowane Helios
- Niesklasyfikowane Scarlett
- Niesklasyfikowane SodaStream
- Niesklasyfikowane Microlife
- Niesklasyfikowane PreSonus
- Niesklasyfikowane Mercusys
- Niesklasyfikowane Koss
- Niesklasyfikowane Monitor Audio
- Niesklasyfikowane Audio Pro
- Niesklasyfikowane I-TEC
- Niesklasyfikowane Weston
- Niesklasyfikowane ARRI
- Niesklasyfikowane ResMed
- Niesklasyfikowane Blackstar
- Niesklasyfikowane NACON
- Niesklasyfikowane Gossen Metrawatt
- Niesklasyfikowane Sôlt
- Niesklasyfikowane Mafell
- Niesklasyfikowane Eden
- Niesklasyfikowane Fosi Audio
- Niesklasyfikowane TC Electronic
- Niesklasyfikowane GUTFELS
- Niesklasyfikowane Shelly
- Niesklasyfikowane Revox
- Niesklasyfikowane Fluke
- Niesklasyfikowane Nevir
- Niesklasyfikowane Kindermann
- Niesklasyfikowane Megger
- Niesklasyfikowane Ewent
- Niesklasyfikowane HyperIce
- Niesklasyfikowane Olympus
- Niesklasyfikowane Navitel
- Niesklasyfikowane Greisinger
- Niesklasyfikowane Draytek
- Niesklasyfikowane TriStar
- Niesklasyfikowane Ibiza Sound
- Niesklasyfikowane MTD
- Niesklasyfikowane Oliveri
- Niesklasyfikowane Vonyx
- Niesklasyfikowane Musical Fidelity
- Niesklasyfikowane Master Lock
- Niesklasyfikowane Numatic
- Niesklasyfikowane Bogen
- Niesklasyfikowane Landmann
- Niesklasyfikowane Pulsar
- Niesklasyfikowane PATLITE
- Niesklasyfikowane Exquisit
- Niesklasyfikowane Bartscher
- Niesklasyfikowane Phanteks
- Niesklasyfikowane First Austria
- Niesklasyfikowane Alto
- Niesklasyfikowane Hestan
- Niesklasyfikowane Fiskars
- Niesklasyfikowane Gastroback
- Niesklasyfikowane GYS
- Niesklasyfikowane Mitsubishi
- Niesklasyfikowane Privileg
- Niesklasyfikowane Avaya
- Niesklasyfikowane Edimax
- Niesklasyfikowane Naim
- Niesklasyfikowane Razer
- Niesklasyfikowane Grothe
- Niesklasyfikowane Dimplex
- Niesklasyfikowane Falmec
- Niesklasyfikowane National Geographic
- Niesklasyfikowane Florabest
- Niesklasyfikowane Harvia
- Niesklasyfikowane Baxi
- Niesklasyfikowane BeSafe
- Niesklasyfikowane ADATA
- Niesklasyfikowane Kidde
- Niesklasyfikowane Chief
- Niesklasyfikowane 4ms
- Niesklasyfikowane Peavey
- Niesklasyfikowane IVT
- Niesklasyfikowane GoClever
- Niesklasyfikowane Sunding
- Niesklasyfikowane Baby Lock
- Niesklasyfikowane Dehner
- Niesklasyfikowane Bryton
- Niesklasyfikowane Weidmüller
- Niesklasyfikowane BENNING
- Niesklasyfikowane ION
- Niesklasyfikowane Camille Bauer
- Niesklasyfikowane Huion
- Niesklasyfikowane Arçelik
- Niesklasyfikowane ART
- Niesklasyfikowane First Alert
- Niesklasyfikowane Hanseatic
- Niesklasyfikowane Assa Abloy
- Niesklasyfikowane NAD
- Niesklasyfikowane Solo
- Niesklasyfikowane Continental Edison
- Niesklasyfikowane RCF
- Niesklasyfikowane Topmove
- Niesklasyfikowane Delta
- Niesklasyfikowane Kerbl
- Niesklasyfikowane Bifinett
- Niesklasyfikowane SEH
- Niesklasyfikowane Zhiyun
- Niesklasyfikowane Gree
- Niesklasyfikowane Fluval
- Niesklasyfikowane Bissell
- Niesklasyfikowane AirLive
- Niesklasyfikowane Harman Kardon
- Niesklasyfikowane Rolls
- Niesklasyfikowane Audio-Technica
- Niesklasyfikowane Maginon
- Niesklasyfikowane EnGenius
- Niesklasyfikowane SPC
- Niesklasyfikowane Atag
- Niesklasyfikowane Babymoov
- Niesklasyfikowane Rosieres
- Niesklasyfikowane Franke
- Niesklasyfikowane Planet
- Niesklasyfikowane Intermec
- Niesklasyfikowane Dahle
- Niesklasyfikowane XGIMI
- Niesklasyfikowane Adidas
- Niesklasyfikowane GoGen
- Niesklasyfikowane Intenso
- Niesklasyfikowane DCG
- Niesklasyfikowane Accu-Chek
- Niesklasyfikowane Genie
- Niesklasyfikowane TC Helicon
- Niesklasyfikowane RCBS
- Niesklasyfikowane Peg Perego
- Niesklasyfikowane NEC
- Niesklasyfikowane Rexel
- Niesklasyfikowane Brandson
- Niesklasyfikowane Soundcraft
- Niesklasyfikowane Beautiful
- Niesklasyfikowane Metrix
- Niesklasyfikowane Parrot
- Niesklasyfikowane Antec
- Niesklasyfikowane Vornado
- Niesklasyfikowane Polaroid
- Niesklasyfikowane Rocktrail
- Niesklasyfikowane Prestigio
- Niesklasyfikowane Blustream
- Niesklasyfikowane Aiwa
- Niesklasyfikowane G3 Ferrari
- Niesklasyfikowane Ooni
- Niesklasyfikowane JL Audio
- Niesklasyfikowane LevelOne
- Niesklasyfikowane Omega Altise
- Niesklasyfikowane Konica Minolta
- Niesklasyfikowane Bugaboo
- Niesklasyfikowane AKAI
- Niesklasyfikowane Tunturi
- Niesklasyfikowane Razor
- Niesklasyfikowane Digi
- Niesklasyfikowane JLab
- Niesklasyfikowane Maglite
- Niesklasyfikowane Mobicool
- Niesklasyfikowane Axis
- Niesklasyfikowane Sanyo
- Niesklasyfikowane ICOM
- Niesklasyfikowane Vivolink
- Niesklasyfikowane Life Fitness
- Niesklasyfikowane Red Digital Cinema
- Niesklasyfikowane Westfalia
- Niesklasyfikowane Hamilton Beach
- Niesklasyfikowane Majority
- Niesklasyfikowane Elvid
- Niesklasyfikowane Hayward
- Niesklasyfikowane Neumärker
- Niesklasyfikowane REL Acoustics
- Niesklasyfikowane Flaem
- Niesklasyfikowane Gourmetmaxx
- Niesklasyfikowane Rigol
- Niesklasyfikowane Bixolon
- Niesklasyfikowane Ergotools Pattfield
- Niesklasyfikowane Hoymiles
- Niesklasyfikowane Teufel
- Niesklasyfikowane Novy
- Niesklasyfikowane Suevia
- Niesklasyfikowane Remko
- Niesklasyfikowane Hartke
- Niesklasyfikowane Clatronic
- Niesklasyfikowane BabyBjörn
- Niesklasyfikowane Healthy Choice
- Niesklasyfikowane Tronic
- Niesklasyfikowane Klark Teknik
- Niesklasyfikowane Dali
- Niesklasyfikowane Vision
- Niesklasyfikowane Telefunken
- Niesklasyfikowane NEO Tools
- Niesklasyfikowane Oregon Scientific
- Niesklasyfikowane Lorex
- Niesklasyfikowane Eventide
- Niesklasyfikowane Optoma
- Niesklasyfikowane Melitta
- Niesklasyfikowane Rommer
- Niesklasyfikowane Proel
- Niesklasyfikowane Calor
- Niesklasyfikowane Inventum
- Niesklasyfikowane SVAN
- Niesklasyfikowane Ariete
- Niesklasyfikowane Flame
- Niesklasyfikowane Hifonics
- Niesklasyfikowane Vogel's
- Niesklasyfikowane Heidemann
- Niesklasyfikowane Fuzzix
- Niesklasyfikowane Focal
- Niesklasyfikowane OnePlus
- Niesklasyfikowane Tepro
- Niesklasyfikowane Bernina
- Niesklasyfikowane Asrock
- Niesklasyfikowane LiftMaster
- Niesklasyfikowane Taga Harmony
- Niesklasyfikowane Graef
- Niesklasyfikowane Viper
- Niesklasyfikowane Napoleon
- Niesklasyfikowane Audix
- Niesklasyfikowane Milesight
- Niesklasyfikowane DBX
- Niesklasyfikowane Princess
- Niesklasyfikowane Baby Jogger
- Niesklasyfikowane Kicker
- Niesklasyfikowane Amazon
- Niesklasyfikowane Carson
- Niesklasyfikowane Doepfer
- Niesklasyfikowane TDE Instruments
- Niesklasyfikowane Innoliving
- Niesklasyfikowane Aluratek
- Niesklasyfikowane Abus
- Niesklasyfikowane Thorens
- Niesklasyfikowane Bresser
- Niesklasyfikowane Sunbeam
- Niesklasyfikowane Rocstor
- Niesklasyfikowane Reebok
- Niesklasyfikowane Omnitronic
- Niesklasyfikowane Livarno Lux
- Niesklasyfikowane Solac
- Niesklasyfikowane Valco Baby
- Niesklasyfikowane Elro
- Niesklasyfikowane Olympia
- Niesklasyfikowane Jay-Tech
- Niesklasyfikowane Novis
- Niesklasyfikowane Hama
- Niesklasyfikowane Mackie
- Niesklasyfikowane Juki
- Niesklasyfikowane Shokz
- Niesklasyfikowane Microsoft
- Niesklasyfikowane Marmitek
- Niesklasyfikowane Busch + Müller
- Niesklasyfikowane Eltako
- Niesklasyfikowane Heller
- Niesklasyfikowane Palmer
- Niesklasyfikowane Sanitaire
- Niesklasyfikowane FiiO
- Niesklasyfikowane SkyRC
- Niesklasyfikowane Waring Commercial
- Niesklasyfikowane Corel
- Niesklasyfikowane SE Electronics
- Niesklasyfikowane Ubiquiti Networks
- Niesklasyfikowane Western Digital
- Niesklasyfikowane Princeton Tec
- Niesklasyfikowane Lindell Audio
- Niesklasyfikowane Verbatim
- Niesklasyfikowane Baby Annabell
- Niesklasyfikowane Caple
- Niesklasyfikowane Taylor
- Niesklasyfikowane Duronic
- Niesklasyfikowane ModeCom
- Niesklasyfikowane Nivona
- Niesklasyfikowane Smoby
- Niesklasyfikowane Smart-AVI
- Niesklasyfikowane Maximum
- Niesklasyfikowane Omega
- Niesklasyfikowane Axagon
- Niesklasyfikowane MXL
- Niesklasyfikowane Cameo
- Niesklasyfikowane Christopeit
- Niesklasyfikowane Comfee
- Niesklasyfikowane Medel
- Niesklasyfikowane Fein
- Niesklasyfikowane Mattel
- Niesklasyfikowane Jumbo
- Niesklasyfikowane Barco
- Niesklasyfikowane Goobay
- Niesklasyfikowane Sagemcom
- Niesklasyfikowane Optex
- Niesklasyfikowane GoPro
- Niesklasyfikowane Bush
- Niesklasyfikowane Siméo
- Niesklasyfikowane ThinkFun
- Niesklasyfikowane Schwaiger
- Niesklasyfikowane New Pol
- Niesklasyfikowane Promise Technology
- Niesklasyfikowane Sharkoon
- Niesklasyfikowane Eheim
- Niesklasyfikowane Watson
- Niesklasyfikowane Saramonic
- Niesklasyfikowane Oase
- Niesklasyfikowane Pro-User
- Niesklasyfikowane Mean Well
- Niesklasyfikowane Gravity
- Niesklasyfikowane Kenmore
- Niesklasyfikowane Kaiser
- Niesklasyfikowane Equip
- Niesklasyfikowane Loewe
- Niesklasyfikowane DeepCool
- Niesklasyfikowane Bluesound
- Niesklasyfikowane Zephyr
- Niesklasyfikowane Michelin
- Niesklasyfikowane Boso
- Niesklasyfikowane Kemo
- Niesklasyfikowane Breville
- Niesklasyfikowane Swift
- Niesklasyfikowane Terraillon
- Niesklasyfikowane Sera
- Niesklasyfikowane Allibert
- Niesklasyfikowane Aerotec
- Niesklasyfikowane GA.MA
- Niesklasyfikowane Juniper
- Niesklasyfikowane Deaf Bonce
- Niesklasyfikowane Sangean
- Niesklasyfikowane BORA
- Niesklasyfikowane Cudy
- Niesklasyfikowane VOX
- Niesklasyfikowane QNAP
- Niesklasyfikowane Ferm
- Niesklasyfikowane COLBOR
- Niesklasyfikowane Insignia
- Niesklasyfikowane AVer
- Niesklasyfikowane AYA
- Niesklasyfikowane Pelgrim
- Niesklasyfikowane Walrus Audio
- Niesklasyfikowane Ambient Weather
- Niesklasyfikowane Veripart
- Niesklasyfikowane Apricorn
- Niesklasyfikowane Esperanza
- Niesklasyfikowane Playtive
- Niesklasyfikowane Arris
- Niesklasyfikowane SVS
- Niesklasyfikowane Navman
- Niesklasyfikowane Chenbro Micom
- Niesklasyfikowane HTC
- Niesklasyfikowane Gabor
- Niesklasyfikowane ZKTeco
- Niesklasyfikowane Netis
- Niesklasyfikowane Frilec
- Niesklasyfikowane Akuvox
- Niesklasyfikowane Benavent
- Niesklasyfikowane Jane
- Niesklasyfikowane Hager
- Niesklasyfikowane Extech
- Niesklasyfikowane NANO Modules
- Niesklasyfikowane Elation
- Niesklasyfikowane GVM
- Niesklasyfikowane Ravensburger
- Niesklasyfikowane TomTom
- Niesklasyfikowane Shark
- Niesklasyfikowane TSC
- Niesklasyfikowane True
- Niesklasyfikowane 3M
- Niesklasyfikowane ECS
- Niesklasyfikowane Franklin
- Niesklasyfikowane Magivaac
- Niesklasyfikowane Victrola
- Niesklasyfikowane Nilfisk
- Niesklasyfikowane Tower
- Niesklasyfikowane XPG
- Niesklasyfikowane Elta
- Niesklasyfikowane Orima
- Niesklasyfikowane Yukon
- Niesklasyfikowane Mac Audio
- Niesklasyfikowane Vakoss
- Niesklasyfikowane Infinity
- Niesklasyfikowane Pentair
- Niesklasyfikowane McIntosh
- Niesklasyfikowane Advance Acoustic
- Niesklasyfikowane Solis
- Niesklasyfikowane Revel
- Niesklasyfikowane Junkers
- Niesklasyfikowane Denver
- Niesklasyfikowane Harley Benton
- Niesklasyfikowane Anker
- Niesklasyfikowane Testboy
- Niesklasyfikowane Pentax
- Niesklasyfikowane Bushnell
- Niesklasyfikowane Horizon Fitness
- Niesklasyfikowane Berger & Schröter
- Niesklasyfikowane Allnet
- Niesklasyfikowane Kernau
- Niesklasyfikowane Veritas
- Niesklasyfikowane Dynacord
- Niesklasyfikowane Aspes
- Niesklasyfikowane Albrecht
- Niesklasyfikowane Marshall Electronics
- Niesklasyfikowane Orion
- Niesklasyfikowane Ashly
- Niesklasyfikowane DCS
- Niesklasyfikowane Hitachi
- Niesklasyfikowane Postium
- Niesklasyfikowane Weller
- Niesklasyfikowane Herkules
- Niesklasyfikowane Blumfeldt
- Niesklasyfikowane Futurelight
- Niesklasyfikowane Yale
- Niesklasyfikowane JIMMY
- Niesklasyfikowane FED
- Niesklasyfikowane InfaSecure
- Niesklasyfikowane Fender
- Niesklasyfikowane Winix
- Niesklasyfikowane Hertz
- Niesklasyfikowane Em-Trak
- Niesklasyfikowane Nitecore
- Niesklasyfikowane InLine
- Niesklasyfikowane Inter-M
- Niesklasyfikowane Kali Audio
- Niesklasyfikowane Rapoo
- Niesklasyfikowane Tracer
- Niesklasyfikowane Salton
- Niesklasyfikowane Ventura
- Niesklasyfikowane Polisport
- Niesklasyfikowane Stabila
- Niesklasyfikowane IStarUSA
- Niesklasyfikowane Joby
- Niesklasyfikowane Technika
- Niesklasyfikowane Emerson
- Niesklasyfikowane Seiki
- Niesklasyfikowane SereneLife
- Niesklasyfikowane JennAir
- Niesklasyfikowane Kyoritsu
- Niesklasyfikowane Pfaff
- Niesklasyfikowane Craftsman
- Niesklasyfikowane Silverstone
- Niesklasyfikowane Mooer
- Niesklasyfikowane Ernitec
- Niesklasyfikowane AKG
- Niesklasyfikowane Vemer
- Niesklasyfikowane Frigidaire
- Niesklasyfikowane CyberPower
- Niesklasyfikowane Azden
- Niesklasyfikowane Galanz
- Niesklasyfikowane FeiyuTech
- Niesklasyfikowane AVerMedia
- Niesklasyfikowane Roccat
- Niesklasyfikowane Olight
- Niesklasyfikowane Barazza
- Niesklasyfikowane Busch-Jaeger
- Niesklasyfikowane Magnus
- Niesklasyfikowane EcoFlow
- Niesklasyfikowane RCA
- Niesklasyfikowane Klein Tools
- Niesklasyfikowane OWC
- Niesklasyfikowane MEE Audio
- Niesklasyfikowane Black Diamond
- Niesklasyfikowane AJA
- Niesklasyfikowane Electro Harmonix
- Niesklasyfikowane KRK
- Niesklasyfikowane MBM
- Niesklasyfikowane Scotsman
- Niesklasyfikowane Genius
- Niesklasyfikowane Marvel
- Niesklasyfikowane Media-Tech
- Niesklasyfikowane Levenhuk
- Niesklasyfikowane Atlas Sound
- Niesklasyfikowane IOTAVX
- Niesklasyfikowane Fieldmann
- Niesklasyfikowane Summit
- Niesklasyfikowane Homelite
- Niesklasyfikowane Gemini
- Niesklasyfikowane BenQ
- Niesklasyfikowane Trevi
- Niesklasyfikowane Technaxx
- Niesklasyfikowane Atlona
- Niesklasyfikowane Elektrobock
- Niesklasyfikowane Thermaltake
- Niesklasyfikowane Amer
- Niesklasyfikowane Hunter
- Niesklasyfikowane Fibaro
- Niesklasyfikowane Sirius
- Niesklasyfikowane Simrad
- Niesklasyfikowane Salus
- Niesklasyfikowane ENTES
- Niesklasyfikowane Tams Elektronik
- Niesklasyfikowane Nintendo
- Niesklasyfikowane Lexibook
- Niesklasyfikowane Soundskins
- Niesklasyfikowane Ridgid
- Niesklasyfikowane Foster
- Niesklasyfikowane Hammond
- Niesklasyfikowane Minn Kota
- Niesklasyfikowane Shindaiwa
- Niesklasyfikowane GPX
- Niesklasyfikowane Gefen
- Niesklasyfikowane Hansgrohe
- Niesklasyfikowane Lanaform
- Niesklasyfikowane Gardenline
- Niesklasyfikowane Martin
- Niesklasyfikowane Hanwha
- Niesklasyfikowane Rommelsbacher
- Niesklasyfikowane American International
- Niesklasyfikowane Ixxat
- Niesklasyfikowane Overmax
- Niesklasyfikowane SEADA
- Niesklasyfikowane Vivanco
- Niesklasyfikowane EQ-3
- Niesklasyfikowane Inkbird
- Niesklasyfikowane Fishman
- Niesklasyfikowane Leifheit
- Niesklasyfikowane Eurochron
- Niesklasyfikowane Radial Engineering
- Niesklasyfikowane PowerPlus
- Niesklasyfikowane Fulgor Milano
- Niesklasyfikowane Quantum
- Niesklasyfikowane MDT
- Niesklasyfikowane Kelvinator
- Niesklasyfikowane Bebe Confort
- Niesklasyfikowane Grandstream
- Niesklasyfikowane Alpha Tools
- Niesklasyfikowane Arturia
- Niesklasyfikowane Lectrosonics
- Niesklasyfikowane Gaggenau
- Niesklasyfikowane Asaklitt
- Niesklasyfikowane Sencor
- Niesklasyfikowane Emko
- Niesklasyfikowane BDI
- Niesklasyfikowane Definitive Technology
- Niesklasyfikowane Ground Zero
- Niesklasyfikowane Noxon
- Niesklasyfikowane Polsen
- Niesklasyfikowane Vonroc
- Niesklasyfikowane Mistral
- Niesklasyfikowane Elica
- Niesklasyfikowane Eversolo
- Niesklasyfikowane Tamron
- Niesklasyfikowane Spear & Jackson
- Niesklasyfikowane Raymarine
- Niesklasyfikowane Powerfix
- Niesklasyfikowane HiKOKI
- Niesklasyfikowane Workzone
- Niesklasyfikowane Insta360
- Niesklasyfikowane Evenflo
- Niesklasyfikowane McCulloch
- Niesklasyfikowane Tempo
- Niesklasyfikowane Nabo
- Niesklasyfikowane EasyMaxx
- Niesklasyfikowane Stinger
- Niesklasyfikowane Dreadbox
- Niesklasyfikowane PowerBass
- Niesklasyfikowane Elo
- Niesklasyfikowane Avanti
- Niesklasyfikowane BABY Born
- Niesklasyfikowane Seaward
- Niesklasyfikowane Revlon
- Niesklasyfikowane Power Dynamics
- Niesklasyfikowane Blackmagic Design
- Niesklasyfikowane AEA
- Niesklasyfikowane Asko
- Niesklasyfikowane Kanto
- Niesklasyfikowane Ikan
- Niesklasyfikowane Alecto
- Niesklasyfikowane Vacmaster
- Niesklasyfikowane Kathrein
- Niesklasyfikowane Kalorik
- Niesklasyfikowane Avidsen
- Niesklasyfikowane Binatone
- Niesklasyfikowane Rockford Fosgate
- Niesklasyfikowane Domyos
- Niesklasyfikowane DOD
- Niesklasyfikowane Suntec
- Niesklasyfikowane Steinberg
- Niesklasyfikowane Impact
- Niesklasyfikowane Be Quiet!
- Niesklasyfikowane Microboards
- Niesklasyfikowane JUNG
- Niesklasyfikowane Xtorm
- Niesklasyfikowane Eaton
- Niesklasyfikowane Carrier
- Niesklasyfikowane Burg Wächter
- Niesklasyfikowane Hammer
- Niesklasyfikowane Nextbase
- Niesklasyfikowane Lund
- Niesklasyfikowane Honey-Can-Do
- Niesklasyfikowane Foscam
- Niesklasyfikowane Lumens
- Niesklasyfikowane Eizo
- Niesklasyfikowane Senal
- Niesklasyfikowane TOA
- Niesklasyfikowane Newland
- Niesklasyfikowane Byron
- Niesklasyfikowane Monacor
- Niesklasyfikowane Esatto
- Niesklasyfikowane Aputure
- Niesklasyfikowane HQ Power
- Niesklasyfikowane Signature
- Niesklasyfikowane Ferplast
- Niesklasyfikowane Daewoo
- Niesklasyfikowane ADE
- Niesklasyfikowane Hotone
- Niesklasyfikowane Cosori
- Niesklasyfikowane X-Sense
- Niesklasyfikowane Neutrik
- Niesklasyfikowane Tannoy
- Niesklasyfikowane Livington
- Niesklasyfikowane Electro-Voice
- Niesklasyfikowane Anthem
- Niesklasyfikowane Dörr
- Niesklasyfikowane Consul
- Niesklasyfikowane Tascam
- Niesklasyfikowane Etekcity
- Niesklasyfikowane RME
- Niesklasyfikowane Metz
- Niesklasyfikowane Laser
- Niesklasyfikowane Wiha
- Niesklasyfikowane M-e
- Niesklasyfikowane Lervia
- Niesklasyfikowane WAGAN
- Niesklasyfikowane Kunft
- Niesklasyfikowane Robinhood
- Niesklasyfikowane Tetra
- Niesklasyfikowane Grunkel
- Niesklasyfikowane SLV
- Niesklasyfikowane H-Tronic
- Niesklasyfikowane Sonnet
- Niesklasyfikowane Novation
- Niesklasyfikowane Silver Cross
- Niesklasyfikowane Vicoustic
- Niesklasyfikowane Zibro
- Niesklasyfikowane Alphatronics
- Niesklasyfikowane Havis
- Niesklasyfikowane Becken
- Niesklasyfikowane JAYS
- Niesklasyfikowane AudioControl
- Niesklasyfikowane Karma
- Niesklasyfikowane Scandomestic
- Niesklasyfikowane NOCO
- Niesklasyfikowane EVE
- Niesklasyfikowane OKAY
- Niesklasyfikowane API Audio
- Niesklasyfikowane Bahr
- Niesklasyfikowane Socket Mobile
- Niesklasyfikowane Smartwares
- Niesklasyfikowane Elgato
- Niesklasyfikowane Traeger
- Niesklasyfikowane Magmatic
- Niesklasyfikowane Porter-Cable
- Niesklasyfikowane Noctua
- Niesklasyfikowane Masport
- Niesklasyfikowane Metabo
- Niesklasyfikowane GVision
- Niesklasyfikowane ProfiCare
- Niesklasyfikowane Audiolab
- Niesklasyfikowane Bretford
- Niesklasyfikowane Galcon
- Niesklasyfikowane Guzzanti
- Niesklasyfikowane Vocopro
- Niesklasyfikowane Technical Pro
- Niesklasyfikowane Adj
- Niesklasyfikowane CM Storm
- Niesklasyfikowane Mauser
- Niesklasyfikowane MEPROLIGHT
- Niesklasyfikowane Lagrange
- Niesklasyfikowane Lamax
- Niesklasyfikowane Absco
- Niesklasyfikowane Bestgreen
- Niesklasyfikowane WiiM
- Niesklasyfikowane AkYtec
- Niesklasyfikowane Wachendorff
- Niesklasyfikowane SPL
- Niesklasyfikowane SureFire
- Niesklasyfikowane ISi
- Niesklasyfikowane Cyrus
- Niesklasyfikowane Gold Note
- Niesklasyfikowane SolaX Power
- Niesklasyfikowane Ketron
- Niesklasyfikowane ETC
- Niesklasyfikowane EZ Dupe
- Niesklasyfikowane IBEAM
- Niesklasyfikowane Terratec
- Niesklasyfikowane Gastronoma
- Niesklasyfikowane Pinolino
- Niesklasyfikowane Transcend
- Niesklasyfikowane Edilkamin
- Niesklasyfikowane Axxess
- Niesklasyfikowane Dualit
- Niesklasyfikowane Kern
- Niesklasyfikowane Crunch
- Niesklasyfikowane Wilson
- Niesklasyfikowane Goki
- Niesklasyfikowane Zoofari
- Niesklasyfikowane EGO
- Niesklasyfikowane WilTec
- Niesklasyfikowane Toro
- Niesklasyfikowane AstralPool
- Niesklasyfikowane ABC Design
- Niesklasyfikowane Müller
- Niesklasyfikowane Cotech
- Niesklasyfikowane Gre
- Niesklasyfikowane Britax
- Niesklasyfikowane Humminbird
- Niesklasyfikowane Dataflex
- Niesklasyfikowane Dormakaba
- Niesklasyfikowane Stairville
- Niesklasyfikowane Snom
- Niesklasyfikowane Elmo
- Niesklasyfikowane Vitek
- Niesklasyfikowane Skil
- Niesklasyfikowane Xvive
- Niesklasyfikowane Geneva
- Niesklasyfikowane Miomare
- Niesklasyfikowane Alfatron
- Niesklasyfikowane Anton/Bauer
- Niesklasyfikowane Sound Devices
- Niesklasyfikowane Eurom
- Niesklasyfikowane Beha-Amprobe
- Niesklasyfikowane Sebo
- Niesklasyfikowane Enermax
- Niesklasyfikowane Clas Ohlson
- Niesklasyfikowane Savio
- Niesklasyfikowane TechBite
- Niesklasyfikowane RADEMACHER
- Niesklasyfikowane Blackburn
- Niesklasyfikowane Salicru
- Niesklasyfikowane Laserliner
- Niesklasyfikowane Zotac
- Niesklasyfikowane Cocraft
- Niesklasyfikowane Lupine
- Niesklasyfikowane Reflexion
- Niesklasyfikowane Megasat
- Niesklasyfikowane Kopp
- Niesklasyfikowane Hikmicro
- Niesklasyfikowane Maytronics
- Niesklasyfikowane Crosley
- Niesklasyfikowane TensCare
- Niesklasyfikowane Varta
- Niesklasyfikowane Nutrichef
- Niesklasyfikowane Constructa
- Niesklasyfikowane Proline
- Niesklasyfikowane Atomos
- Niesklasyfikowane Adventuridge
- Niesklasyfikowane Casa Deco
- Niesklasyfikowane EXIT
- Niesklasyfikowane HK Audio
- Niesklasyfikowane Euromaid
- Niesklasyfikowane Reloop
- Niesklasyfikowane Primewire
- Niesklasyfikowane Lorelli
- Niesklasyfikowane Cherry
- Niesklasyfikowane Greenworks
- Niesklasyfikowane Rittal
- Niesklasyfikowane BSS Audio
- Niesklasyfikowane Newstar
- Niesklasyfikowane Oreck
- Niesklasyfikowane Timbersled
- Niesklasyfikowane I.safe Mobile
- Niesklasyfikowane Artsound
- Niesklasyfikowane Chandler
- Niesklasyfikowane Flama
- Niesklasyfikowane Sevenoak
- Niesklasyfikowane Vivitar
- Niesklasyfikowane Areca
- Niesklasyfikowane Belkin
- Niesklasyfikowane SWIT
- Niesklasyfikowane Zeiss
- Niesklasyfikowane Bebob
- Niesklasyfikowane Morley
- Niesklasyfikowane Generac
- Niesklasyfikowane Kramer
- Niesklasyfikowane Gen Energy
- Niesklasyfikowane Lian Li
- Niesklasyfikowane Kahayan
- Niesklasyfikowane Profoto
- Niesklasyfikowane Wimberley
- Niesklasyfikowane Kopul
- Niesklasyfikowane Analog Way
- Niesklasyfikowane BZBGear
- Niesklasyfikowane K&M
- Niesklasyfikowane RGBlink
- Niesklasyfikowane Glide Gear
- Niesklasyfikowane Hosa
- Niesklasyfikowane Vortex
- Niesklasyfikowane Cranborne Audio
- Niesklasyfikowane SmallRig
- Niesklasyfikowane ToughTested
- Niesklasyfikowane Arkon
- Niesklasyfikowane Trijicon
- Niesklasyfikowane Xcellon
- Niesklasyfikowane Murideo
- Niesklasyfikowane Intellijel
- Niesklasyfikowane CEDAR
- Niesklasyfikowane Rupert Neve Designs
- Niesklasyfikowane Pawa
- Niesklasyfikowane Erica Synths
- Niesklasyfikowane Key Digital
- Niesklasyfikowane Robus
- Niesklasyfikowane Ideal
- Niesklasyfikowane Apantac
- Niesklasyfikowane AMX
- Niesklasyfikowane Rosco
- Niesklasyfikowane Scancool
- Niesklasyfikowane JILONG
- Niesklasyfikowane OBH Nordica
- Niesklasyfikowane AENO
- Niesklasyfikowane ABB
- Niesklasyfikowane SRS
- Niesklasyfikowane Thermador
- Niesklasyfikowane Wolfcraft
- Niesklasyfikowane Budda
- Niesklasyfikowane Soler & Palau
- Niesklasyfikowane Goodis
- Niesklasyfikowane Bestron
- Niesklasyfikowane Eura
- Niesklasyfikowane Optimum
- Niesklasyfikowane Atosa
- Niesklasyfikowane HiLook
- Niesklasyfikowane Rotel
- Niesklasyfikowane Lexmark
- Niesklasyfikowane Atlas
- Niesklasyfikowane Profile
- Niesklasyfikowane Sensiplast
- Niesklasyfikowane Swan
- Niesklasyfikowane Brondi
- Niesklasyfikowane Fysic
- Niesklasyfikowane Wiko
- Niesklasyfikowane A.O. Smith
- Niesklasyfikowane Dangerous Music
- Niesklasyfikowane Lumantek
- Niesklasyfikowane Kluge
- Niesklasyfikowane Aduro
- Niesklasyfikowane Alpina
- Niesklasyfikowane Airlux
- Niesklasyfikowane Aligator
- Niesklasyfikowane Ambrogio
- Niesklasyfikowane Allied Telesis
- Niesklasyfikowane Alienware
- Niesklasyfikowane Amfra
- Niesklasyfikowane Alcon
- Niesklasyfikowane A4tech
- Niesklasyfikowane Ampeg
- Niesklasyfikowane Amplicom
- Niesklasyfikowane Amprobe
- Niesklasyfikowane Archos
- Niesklasyfikowane Argon
- Niesklasyfikowane American Audio
- Niesklasyfikowane Aquapur
- Niesklasyfikowane Devialet
- Niesklasyfikowane KDK
- Niesklasyfikowane IFi Audio
- Niesklasyfikowane Crosscall
- Niesklasyfikowane Cabasse
- Niesklasyfikowane Amiko
- Niesklasyfikowane Aeris
- Niesklasyfikowane Ascom
- Niesklasyfikowane Alpen Kreuzer
- Niesklasyfikowane ACME
- Niesklasyfikowane Reflecta
- Niesklasyfikowane Argus
- Niesklasyfikowane ATN
- Niesklasyfikowane Ziggo
- Niesklasyfikowane Intermatic
- Niesklasyfikowane Flamingo
- Niesklasyfikowane Toolland
- Niesklasyfikowane Brennenstuhl
- Niesklasyfikowane MJX
- Niesklasyfikowane Hirschmann
- Niesklasyfikowane Kruidvat
- Niesklasyfikowane Audison
- Niesklasyfikowane Proteca
- Niesklasyfikowane Toorx
- Niesklasyfikowane Body Solid
- Niesklasyfikowane Tryton
- Niesklasyfikowane Oceanic
- Niesklasyfikowane Korona
- Niesklasyfikowane Saturn
- Niesklasyfikowane Tiger
- Niesklasyfikowane Progress
- Niesklasyfikowane Meradiso
- Niesklasyfikowane BH Fitness
- Niesklasyfikowane Tevion
- Niesklasyfikowane GPO
- Niesklasyfikowane Lucide
- Niesklasyfikowane Parisot
- Niesklasyfikowane Caliber
- Niesklasyfikowane Bellini
- Niesklasyfikowane Eminent
- Niesklasyfikowane Pressalit
- Niesklasyfikowane Oster
- Niesklasyfikowane Kichler
- Niesklasyfikowane VAX
- Niesklasyfikowane Vestel
- Niesklasyfikowane Sinbo
- Niesklasyfikowane Jata
- Niesklasyfikowane VirtuFit
- Niesklasyfikowane Fritel
- Niesklasyfikowane Ordex
- Niesklasyfikowane Itho
- Niesklasyfikowane Targus
- Niesklasyfikowane Q-CONNECT
- Niesklasyfikowane Sicce
- Niesklasyfikowane Outwell
- Niesklasyfikowane Sitecom
- Niesklasyfikowane United Office
- Niesklasyfikowane Monogram
- Niesklasyfikowane Maxdata
- Niesklasyfikowane Hard Head
- Niesklasyfikowane Exibel
- Niesklasyfikowane Logik
- Niesklasyfikowane Easy Camp
- Niesklasyfikowane Energy Sistem
- Niesklasyfikowane Orbit
- Niesklasyfikowane Auto Joe
- Niesklasyfikowane Fortinet
- Niesklasyfikowane Youin
- Niesklasyfikowane Telestar
- Niesklasyfikowane Valore
- Niesklasyfikowane Accucold
- Niesklasyfikowane Sun Joe
- Niesklasyfikowane Perfecta
- Niesklasyfikowane Doro
- Niesklasyfikowane Sagem
- Niesklasyfikowane Cricut
- Niesklasyfikowane Hähnel
- Niesklasyfikowane EWT
- Niesklasyfikowane Enduro
- Niesklasyfikowane Aukey
- Niesklasyfikowane Ernesto
- Niesklasyfikowane KlikaanKlikuit
- Niesklasyfikowane Easypix
- Niesklasyfikowane Ei Electronics
- Niesklasyfikowane Simplified MFG
- Niesklasyfikowane Mellerware
- Niesklasyfikowane Silva
- Niesklasyfikowane Tacklife
- Niesklasyfikowane Energenie
- Niesklasyfikowane Heinner
- Niesklasyfikowane Termozeta
- Niesklasyfikowane Bella
- Niesklasyfikowane Palson
- Niesklasyfikowane Eldom
- Niesklasyfikowane Valeton
- Niesklasyfikowane Jocca
- Niesklasyfikowane Nilox
- Niesklasyfikowane Tiptop Audio
- Niesklasyfikowane Sonos
- Niesklasyfikowane Summit Audio
- Niesklasyfikowane SKS
- Niesklasyfikowane Musway
- Niesklasyfikowane Kensington
- Niesklasyfikowane Nautilus
- Niesklasyfikowane Cresta
- Niesklasyfikowane Maxxmee
- Niesklasyfikowane Brigmton
- Niesklasyfikowane Sunstech
- Niesklasyfikowane Smith & Wesson
- Niesklasyfikowane Reich
- Niesklasyfikowane Defy
- Niesklasyfikowane Stiebel Eltron
- Niesklasyfikowane DeLock
- Niesklasyfikowane Avalon
- Niesklasyfikowane Plant Craft
- Niesklasyfikowane Dubatti
- Niesklasyfikowane Bionaire
- Niesklasyfikowane Sylvania
- Niesklasyfikowane Campomatic
- Niesklasyfikowane Patton
- Niesklasyfikowane Igloo
- Niesklasyfikowane Senco
- Niesklasyfikowane Tork
- Niesklasyfikowane Techly
- Niesklasyfikowane Vaude
- Niesklasyfikowane GlobalTronics
- Niesklasyfikowane Sunny
- Niesklasyfikowane Inglesina
- Niesklasyfikowane BBB
- Niesklasyfikowane BlueBuilt
- Niesklasyfikowane Gazelle
- Niesklasyfikowane Nibe
- Niesklasyfikowane Damixa
- Niesklasyfikowane Da-Lite
- Niesklasyfikowane Trebs
- Niesklasyfikowane Ednet
- Niesklasyfikowane Luxor
- Niesklasyfikowane Bowflex
- Niesklasyfikowane Visage
- Niesklasyfikowane Celestron
- Niesklasyfikowane CaterCool
- Niesklasyfikowane Matrox
- Niesklasyfikowane Rangemaster
- Niesklasyfikowane Maktec
- Niesklasyfikowane Connect IT
- Niesklasyfikowane Steren
- Niesklasyfikowane Eico
- Niesklasyfikowane Hansa
- Niesklasyfikowane Nero
- Niesklasyfikowane Kubo
- Niesklasyfikowane Exagerate
- Niesklasyfikowane Air King
- Niesklasyfikowane Tanaka
- Niesklasyfikowane Gossen
- Niesklasyfikowane Elba
- Niesklasyfikowane Flir
- Niesklasyfikowane Paidi
- Niesklasyfikowane KiddyGuard
- Niesklasyfikowane Livarno
- Niesklasyfikowane Soehnle
- Niesklasyfikowane Barkan
- Niesklasyfikowane Coby
- Niesklasyfikowane Royal Sovereign
- Niesklasyfikowane King
- Niesklasyfikowane Maxwell
- Niesklasyfikowane AcuRite
- Niesklasyfikowane Envivo
- Niesklasyfikowane Gustavsberg
- Niesklasyfikowane Galaxy Audio
- Niesklasyfikowane ESYLUX
- Niesklasyfikowane Ventus
- Niesklasyfikowane Melinera
- Niesklasyfikowane TOTO
- Niesklasyfikowane Fisher Price
- Niesklasyfikowane Technoline
- Niesklasyfikowane Osann
- Niesklasyfikowane Lindam
- Niesklasyfikowane Goliath
- Niesklasyfikowane Yamato
- Niesklasyfikowane Vivo
- Niesklasyfikowane Dorma
- Niesklasyfikowane Belgacom
- Niesklasyfikowane SEB
- Niesklasyfikowane Malmbergs
- Niesklasyfikowane Phoenix
- Niesklasyfikowane AV:link
- Niesklasyfikowane Power Craft
- Niesklasyfikowane Otolift
- Niesklasyfikowane GBC
- Niesklasyfikowane Prenatal
- Niesklasyfikowane Champion
- Niesklasyfikowane Tvilum
- Niesklasyfikowane Heylo
- Niesklasyfikowane TacTic
- Niesklasyfikowane Nolte
- Niesklasyfikowane G3
- Niesklasyfikowane Peach
- Niesklasyfikowane Trixie
- Niesklasyfikowane Finnlo
- Niesklasyfikowane Lescha
- Niesklasyfikowane Capital Sports
- Niesklasyfikowane Buffalo
- Niesklasyfikowane Vello
- Niesklasyfikowane Jenn-Air
- Niesklasyfikowane R-Vent
- Niesklasyfikowane Woood
- Niesklasyfikowane Audiovox
- Niesklasyfikowane Carpigiani
- Niesklasyfikowane Renegade
- Niesklasyfikowane Davis
- Niesklasyfikowane ICU
- Niesklasyfikowane Daitsu
- Niesklasyfikowane Edesa
- Niesklasyfikowane Farberware
- Niesklasyfikowane Ufesa
- Niesklasyfikowane CasaFan
- Niesklasyfikowane Milectric
- Niesklasyfikowane Vicks
- Niesklasyfikowane Yaesu
- Niesklasyfikowane Walkstool
- Niesklasyfikowane Macally
- Niesklasyfikowane Apogee
- Niesklasyfikowane Arlo
- Niesklasyfikowane Nest
- Niesklasyfikowane Kwantum
- Niesklasyfikowane Olimpia Splendid
- Niesklasyfikowane Safescan
- Niesklasyfikowane Pyle Pro
- Niesklasyfikowane Wehkamp
- Niesklasyfikowane Svedbergs
- Niesklasyfikowane Osprey
- Niesklasyfikowane Bunn
- Niesklasyfikowane Ninebot
- Niesklasyfikowane Siedle
- Niesklasyfikowane Cilio
- Niesklasyfikowane LaCie
- Niesklasyfikowane Itho-Daalderop
- Niesklasyfikowane Maul
- Niesklasyfikowane BabyOno
- Niesklasyfikowane Karibu
- Niesklasyfikowane Pericles
- Niesklasyfikowane Troy-Bilt
- Niesklasyfikowane Laica
- Niesklasyfikowane Rusta
- Niesklasyfikowane Samac
- Niesklasyfikowane Brevi
- Niesklasyfikowane SMA
- Niesklasyfikowane Autotek
- Niesklasyfikowane Hive
- Niesklasyfikowane Brabantia
- Niesklasyfikowane AS - Schwabe
- Niesklasyfikowane Fissler
- Niesklasyfikowane Kayoba
- Niesklasyfikowane Wamsler
- Niesklasyfikowane MB Quart
- Niesklasyfikowane Valcom
- Niesklasyfikowane Switel
- Niesklasyfikowane Bopita
- Niesklasyfikowane FireAngel
- Niesklasyfikowane Duux
- Niesklasyfikowane Chacon
- Niesklasyfikowane Astro
- Niesklasyfikowane Imetec
- Niesklasyfikowane InFocus
- Niesklasyfikowane Bigben
- Niesklasyfikowane Topcraft
- Niesklasyfikowane Kraftwerk
- Niesklasyfikowane Naish
- Niesklasyfikowane Festo
- Niesklasyfikowane Massive
- Niesklasyfikowane Barska
- Niesklasyfikowane Weihrauch Sport
- Niesklasyfikowane Blaze
- Niesklasyfikowane Hombli
- Niesklasyfikowane Martha Stewart
- Niesklasyfikowane Milan
- Niesklasyfikowane Lümme
- Niesklasyfikowane Springfree
- Niesklasyfikowane Ansco
- Niesklasyfikowane Glem Gas
- Niesklasyfikowane Goodram
- Niesklasyfikowane MADE
- Niesklasyfikowane Noma
- Niesklasyfikowane IDance
- Niesklasyfikowane Habitat
- Niesklasyfikowane Body Sculpture
- Niesklasyfikowane Maxview
- Niesklasyfikowane Yongnuo
- Niesklasyfikowane Gamma
- Niesklasyfikowane Proctor Silex
- Niesklasyfikowane Elite
- Niesklasyfikowane Zodiac
- Niesklasyfikowane BOHLT
- Niesklasyfikowane Handicare
- Niesklasyfikowane Simplecom
- Niesklasyfikowane Primo
- Niesklasyfikowane Rocketfish
- Niesklasyfikowane Alba
- Niesklasyfikowane Baninni
- Niesklasyfikowane Naxa
- Niesklasyfikowane Nemef
- Niesklasyfikowane Atlantic
- Niesklasyfikowane RugGear
- Niesklasyfikowane Umidigi
- Niesklasyfikowane Saro
- Niesklasyfikowane Millenium
- Niesklasyfikowane Vogue
- Niesklasyfikowane Grixx
- Niesklasyfikowane Topeak
- Niesklasyfikowane SuperFish
- Niesklasyfikowane Luvion
- Niesklasyfikowane Aqua Joe
- Niesklasyfikowane Innovaphone
- Niesklasyfikowane Intel
- Niesklasyfikowane Mamiya
- Niesklasyfikowane Zuiver
- Niesklasyfikowane Fantec
- Niesklasyfikowane Konig
- Niesklasyfikowane Valueline
- Niesklasyfikowane Active Era
- Niesklasyfikowane Trigano
- Niesklasyfikowane Sweex
- Niesklasyfikowane Busch And Müller
- Niesklasyfikowane Ices
- Niesklasyfikowane Vizio
- Niesklasyfikowane Schuberth
- Niesklasyfikowane Cello
- Niesklasyfikowane RDL
- Niesklasyfikowane Austrian Audio
- Niesklasyfikowane Eberspacher
- Niesklasyfikowane Kress
- Niesklasyfikowane Zehnder
- Niesklasyfikowane Laurastar
- Niesklasyfikowane Mx Onda
- Niesklasyfikowane Wacker Neuson
- Niesklasyfikowane Nûby
- Niesklasyfikowane Xterra
- Niesklasyfikowane Fredenstein
- Niesklasyfikowane Dolmar
- Niesklasyfikowane Invacare
- Niesklasyfikowane Nanni
- Niesklasyfikowane Fuji
- Niesklasyfikowane Swissonic
- Niesklasyfikowane Schütte
- Niesklasyfikowane BRIO
- Niesklasyfikowane Aruba
- Niesklasyfikowane RGV
- Niesklasyfikowane Elkay
- Niesklasyfikowane IHealth
- Niesklasyfikowane Hapro
- Niesklasyfikowane Tamiya
- Niesklasyfikowane Logicom
- Niesklasyfikowane Alfen
- Niesklasyfikowane Sound Machines
- Niesklasyfikowane Team
- Niesklasyfikowane Nikkei
- Niesklasyfikowane Petsafe
- Niesklasyfikowane Nelson
- Niesklasyfikowane TranzX
- Niesklasyfikowane Aviom
- Niesklasyfikowane UPM
- Niesklasyfikowane Happy Plugs
- Niesklasyfikowane Duro
- Niesklasyfikowane T'nB
- Niesklasyfikowane Ematic
- Niesklasyfikowane Finder
- Niesklasyfikowane Levoit
- Niesklasyfikowane Palm
- Niesklasyfikowane QSC
- Niesklasyfikowane Phonak
- Niesklasyfikowane Faber
- Niesklasyfikowane Cardiostrong
- Niesklasyfikowane Hartan
- Niesklasyfikowane Hamax
- Niesklasyfikowane Xavax
- Niesklasyfikowane Emmaljunga
- Niesklasyfikowane Fantini Cosmi
- Niesklasyfikowane X4-Tech
- Niesklasyfikowane ZAZU
- Niesklasyfikowane Countryman
- Niesklasyfikowane Minolta
- Niesklasyfikowane Aerial
- Niesklasyfikowane Victor
- Niesklasyfikowane Zagg
- Niesklasyfikowane ESI
- Niesklasyfikowane Edgestar
- Niesklasyfikowane Orbis
- Niesklasyfikowane ACE
- Niesklasyfikowane Maxicool
- Niesklasyfikowane For_Q
- Niesklasyfikowane Avocor
- Niesklasyfikowane Lanzar
- Niesklasyfikowane DoorBird
- Niesklasyfikowane FoodSaver
- Niesklasyfikowane Vroomshoop
- Niesklasyfikowane McGregor
- Niesklasyfikowane Rain Bird
- Niesklasyfikowane Leitz
- Niesklasyfikowane Nvidia
- Niesklasyfikowane Irritrol
- Niesklasyfikowane Boneco
- Niesklasyfikowane Basbau
- Niesklasyfikowane CaterChef
- Niesklasyfikowane Echowell
- Niesklasyfikowane Kasda
- Niesklasyfikowane Patching Panda
- Niesklasyfikowane NEP
- Niesklasyfikowane Veho
- Niesklasyfikowane Kambrook
- Niesklasyfikowane Nevadent
- Niesklasyfikowane Plum
- Niesklasyfikowane Grasslin
- Niesklasyfikowane Puky
- Niesklasyfikowane GFI System
- Niesklasyfikowane Roadstar
- Niesklasyfikowane Humax
- Niesklasyfikowane Vaddio
- Niesklasyfikowane Berner
- Niesklasyfikowane Swarovski Optik
- Niesklasyfikowane Gira
- Niesklasyfikowane Sachtler
- Niesklasyfikowane Seagate
- Niesklasyfikowane Golden Age Project
- Niesklasyfikowane Britax-Romer
- Niesklasyfikowane Technicolor
- Niesklasyfikowane Bravilor Bonamat
- Niesklasyfikowane Blue
- Niesklasyfikowane Efbe-schott
- Niesklasyfikowane Brinsea
- Niesklasyfikowane Genexis
- Niesklasyfikowane Genelec
- Niesklasyfikowane Maxxter
- Niesklasyfikowane Inspire
- Niesklasyfikowane Apart
- Niesklasyfikowane Venta
- Niesklasyfikowane Anchor Audio
- Niesklasyfikowane 4moms
- Niesklasyfikowane Wolf
- Niesklasyfikowane Dantherm
- Niesklasyfikowane Interlogix
- Niesklasyfikowane Projecta
- Niesklasyfikowane Dnt
- Niesklasyfikowane Lyman
- Niesklasyfikowane Genaray
- Niesklasyfikowane Balance
- Niesklasyfikowane Qualcast
- Niesklasyfikowane Cablexpert
- Niesklasyfikowane Iomega
- Niesklasyfikowane Phil And Teds
- Niesklasyfikowane Tornado
- Niesklasyfikowane Stelton
- Niesklasyfikowane Mr Handsfree
- Niesklasyfikowane Pattfield
- Niesklasyfikowane Joovy
- Niesklasyfikowane Bodum
- Niesklasyfikowane Saitek
- Niesklasyfikowane DAS Audio
- Niesklasyfikowane Vestfrost
- Niesklasyfikowane Leen Bakker
- Niesklasyfikowane OSO
- Niesklasyfikowane Roxio
- Niesklasyfikowane Fito
- Niesklasyfikowane Jotul
- Niesklasyfikowane Shoprider
- Niesklasyfikowane WHALE
- Niesklasyfikowane Shuttle
- Niesklasyfikowane Furuno
- Niesklasyfikowane HQ
- Niesklasyfikowane Max
- Niesklasyfikowane Clage
- Niesklasyfikowane Vorago
- Niesklasyfikowane GMB Gaming
- Niesklasyfikowane Cre8audio
- Niesklasyfikowane Nanlite
- Niesklasyfikowane Kupper
- Niesklasyfikowane Ledger
- Niesklasyfikowane Koenig
- Niesklasyfikowane Contour
- Niesklasyfikowane BakkerElkhuizen
- Niesklasyfikowane Lupilu
- Niesklasyfikowane Outdoorchef
- Niesklasyfikowane Boyo
- Niesklasyfikowane IKRA
- Niesklasyfikowane Turmix
- Niesklasyfikowane Fakir
- Niesklasyfikowane IOttie
- Niesklasyfikowane Verizon
- Niesklasyfikowane Trio Lighting
- Niesklasyfikowane Integra
- Niesklasyfikowane Upo
- Niesklasyfikowane Vitamix
- Niesklasyfikowane Cadel
- Niesklasyfikowane Ipevo
- Niesklasyfikowane Miggo
- Niesklasyfikowane Urrea
- Niesklasyfikowane Iget
- Niesklasyfikowane Emtec
- Niesklasyfikowane Ranex
- Niesklasyfikowane Russound
- Niesklasyfikowane Truper
- Niesklasyfikowane ISDT
- Niesklasyfikowane Debel
- Niesklasyfikowane Abac
- Niesklasyfikowane Stannah
- Niesklasyfikowane Comelit
- Niesklasyfikowane Slik
- Niesklasyfikowane Celly
- Niesklasyfikowane Skan Holz
- Niesklasyfikowane Comica
- Niesklasyfikowane Tommee Tippee
- Niesklasyfikowane Globo
- Niesklasyfikowane EverFocus
- Niesklasyfikowane Audient
- Niesklasyfikowane Adesso
- Niesklasyfikowane Infantino
- Niesklasyfikowane C3
- Niesklasyfikowane EMSA
- Niesklasyfikowane Eurospec
- Niesklasyfikowane Waldbeck
- Niesklasyfikowane Natuzzi
- Niesklasyfikowane Satel
- Niesklasyfikowane Bazooka
- Niesklasyfikowane K&K Sound
- Niesklasyfikowane Dutchbone
- Niesklasyfikowane Fanvil
- Niesklasyfikowane Noise Engineering
- Niesklasyfikowane PAC
- Niesklasyfikowane Beretta
- Niesklasyfikowane Wentronic
- Niesklasyfikowane Peerless
- Niesklasyfikowane Xtreme
- Niesklasyfikowane RAVPower
- Niesklasyfikowane Hooker
- Niesklasyfikowane IHome
- Niesklasyfikowane Luxman
- Niesklasyfikowane Gitzo
- Niesklasyfikowane M-Audio
- Niesklasyfikowane SeaLife
- Niesklasyfikowane Nesco
- Niesklasyfikowane Wago
- Niesklasyfikowane AIC
- Niesklasyfikowane Concept2
- Niesklasyfikowane Brydge
- Niesklasyfikowane Selec
- Niesklasyfikowane Aiphone
- Niesklasyfikowane Tivoli Audio
- Niesklasyfikowane JETI
- Niesklasyfikowane Waves
- Niesklasyfikowane EQ3
- Niesklasyfikowane Karlik
- Niesklasyfikowane Comark
- Niesklasyfikowane Coline
- Niesklasyfikowane N8WERK
- Niesklasyfikowane Petri
- Niesklasyfikowane Calex
- Niesklasyfikowane REV
- Niesklasyfikowane Skullcandy
- Niesklasyfikowane Dymond
- Niesklasyfikowane 4smarts
- Niesklasyfikowane Learning Resources
- Niesklasyfikowane Xaoc
- Niesklasyfikowane SVAT
- Niesklasyfikowane Qute
- Niesklasyfikowane BabyGO
- Niesklasyfikowane Schwinn
- Niesklasyfikowane Friedland
- Niesklasyfikowane Proaim
- Niesklasyfikowane Megableu
- Niesklasyfikowane Nexxt
- Niesklasyfikowane Coleman
- Niesklasyfikowane Magic Care
- Niesklasyfikowane Raclet
- Niesklasyfikowane Weishaupt
- Niesklasyfikowane Glock
- Niesklasyfikowane Linn
- Niesklasyfikowane Iluv
- Niesklasyfikowane Monoprice
- Niesklasyfikowane Echo
- Niesklasyfikowane Croozer
- Niesklasyfikowane TELEX
- Niesklasyfikowane Dynamic
- Niesklasyfikowane Sauter
- Niesklasyfikowane Eve Audio
- Niesklasyfikowane Café
- Niesklasyfikowane Adam Hall
- Niesklasyfikowane Murr Elektronik
- Niesklasyfikowane Baja Mobility
- Niesklasyfikowane Yorkville
- Niesklasyfikowane Neewer
- Niesklasyfikowane Meross
- Niesklasyfikowane Könner & Söhnen
- Niesklasyfikowane Klavis
- Niesklasyfikowane Manitowoc
- Niesklasyfikowane Aconatic
- Niesklasyfikowane Advance
- Niesklasyfikowane Artecta
- Niesklasyfikowane NordicTrack
- Niesklasyfikowane Eliminator Lighting
- Niesklasyfikowane Buzz Rack
- Niesklasyfikowane CAME-TV
- Niesklasyfikowane ColorKey
- Niesklasyfikowane ChyTV
- Niesklasyfikowane Holosun
- Niesklasyfikowane Panamax
- Niesklasyfikowane Sonifex
- Niesklasyfikowane TV One
- Niesklasyfikowane Vertex
- Niesklasyfikowane Home Easy
- Niesklasyfikowane Basil
- Niesklasyfikowane Munchkin
- Niesklasyfikowane Nxg
- Niesklasyfikowane AGM
- Niesklasyfikowane Ambient Recording
- Niesklasyfikowane Bruder Mannesmann
- Niesklasyfikowane Autodesk
- Niesklasyfikowane Diana
- Niesklasyfikowane Tandberg Data
- Niesklasyfikowane Fostex
- Niesklasyfikowane Viridian
- Niesklasyfikowane Plustek
- Niesklasyfikowane Prowise
- Niesklasyfikowane Mousetrapper
- Niesklasyfikowane SKROSS
- Niesklasyfikowane Sikkens
- Niesklasyfikowane DEXP
- Niesklasyfikowane Burris
- Niesklasyfikowane GolfBuddy
- Niesklasyfikowane Lynx
- Niesklasyfikowane Vantec
- Niesklasyfikowane FBT
- Niesklasyfikowane Tiptel
- Niesklasyfikowane Thermor
- Niesklasyfikowane NodOn
- Niesklasyfikowane Edge
- Niesklasyfikowane Endorphin.es
- Niesklasyfikowane Crofton
- Niesklasyfikowane MIPRO
- Niesklasyfikowane Bravilor
- Niesklasyfikowane Bracketron
- Niesklasyfikowane Solid State Logic
- Niesklasyfikowane Pointer
- Niesklasyfikowane XYZprinting
- Niesklasyfikowane Computherm
- Niesklasyfikowane ICE Watch
- Niesklasyfikowane Carmen
- Niesklasyfikowane MTM
- Niesklasyfikowane De Buyer
- Niesklasyfikowane Metapace
- Niesklasyfikowane Exo-Terra
- Niesklasyfikowane Neets
- Niesklasyfikowane OutNowTech
- Niesklasyfikowane NAV-TV
- Niesklasyfikowane Wooden Camera
- Niesklasyfikowane Maclaren
- Niesklasyfikowane AdHoc
- Niesklasyfikowane AudioQuest
- Niesklasyfikowane Powerblade
- Niesklasyfikowane HiFi ROSE
- Niesklasyfikowane Hayter
- Niesklasyfikowane Gianni Ferrari
- Niesklasyfikowane OSD Audio
- Niesklasyfikowane WMD
- Niesklasyfikowane Simpark
- Niesklasyfikowane Beafon
- Niesklasyfikowane Maruyama
- Niesklasyfikowane 3B
- Niesklasyfikowane Ergotron
- Niesklasyfikowane Zepter
- Niesklasyfikowane Giordani
- Niesklasyfikowane Black Lion Audio
- Niesklasyfikowane Cowon
- Niesklasyfikowane Soundstream
- Niesklasyfikowane Cruz
- Niesklasyfikowane Khind
- Niesklasyfikowane Crayola
- Niesklasyfikowane Fischer
- Niesklasyfikowane Xoro
- Niesklasyfikowane Maze
- Niesklasyfikowane CTOUCH
- Niesklasyfikowane Adastra
- Niesklasyfikowane Meister Craft
- Niesklasyfikowane Meade
- Niesklasyfikowane Unify
- Niesklasyfikowane Yeastar
- Niesklasyfikowane Laserworld
- Niesklasyfikowane Billow
- Niesklasyfikowane Chuango
- Niesklasyfikowane Kelty
- Niesklasyfikowane West Elm
- Niesklasyfikowane Keter
- Niesklasyfikowane Ozone
- Niesklasyfikowane Clearblue
- Niesklasyfikowane Garden Lights
- Niesklasyfikowane ETiger
- Niesklasyfikowane Bison
- Niesklasyfikowane Jabsco
- Niesklasyfikowane Foxconn
- Niesklasyfikowane Icy Dock
- Niesklasyfikowane Wasco
- Niesklasyfikowane Make Noise
- Niesklasyfikowane Telstra
- Niesklasyfikowane TeachLogic
- Niesklasyfikowane Sole Fitness
- Niesklasyfikowane Lumag
- Niesklasyfikowane Charge Amps
- Niesklasyfikowane Berker
- Niesklasyfikowane Eufab
- Niesklasyfikowane Manfrotto
- Niesklasyfikowane Crucial
- Niesklasyfikowane Premier
- Niesklasyfikowane Aeon Labs
- Niesklasyfikowane Ibm
- Niesklasyfikowane Unilux
- Niesklasyfikowane Citronic
- Niesklasyfikowane Pontec
- Niesklasyfikowane TEF
- Niesklasyfikowane Maxell
- Niesklasyfikowane Cosatto
- Niesklasyfikowane Weasy
- Niesklasyfikowane Datacard
- Niesklasyfikowane Nordea
- Niesklasyfikowane Life Gear
- Niesklasyfikowane ZYCOO
- Niesklasyfikowane Macrom
- Niesklasyfikowane Kontakt Chemie
- Niesklasyfikowane Purell
- Niesklasyfikowane Riccar
- Niesklasyfikowane BabyHome
- Niesklasyfikowane Contax
- Niesklasyfikowane OpenVox
- Niesklasyfikowane Atdec
- Niesklasyfikowane Batavia
- Niesklasyfikowane Klarfit
- Niesklasyfikowane Bruynzeel
- Niesklasyfikowane MSpa
- Niesklasyfikowane View Quest
- Niesklasyfikowane Drayton
- Niesklasyfikowane Titanwolf
- Niesklasyfikowane Uplink
- Niesklasyfikowane Mybeo
- Niesklasyfikowane CSL
- Niesklasyfikowane Bearware
- Niesklasyfikowane Perfect Christmas
- Niesklasyfikowane Core SWX
- Niesklasyfikowane Formuler
- Niesklasyfikowane Oertli
- Niesklasyfikowane UX
- Niesklasyfikowane Moog
- Niesklasyfikowane Nerf
- Niesklasyfikowane KidKraft
- Niesklasyfikowane Metrel
- Niesklasyfikowane Multimetrix
- Niesklasyfikowane Solid
- Niesklasyfikowane Morris
- Niesklasyfikowane 8BitDo
- Niesklasyfikowane Ruger
- Niesklasyfikowane Hubelino
- Niesklasyfikowane Gerni
- Niesklasyfikowane Jupio
- Niesklasyfikowane PCE
- Niesklasyfikowane MedFolio
- Niesklasyfikowane Warm Audio
- Niesklasyfikowane Blaser
- Niesklasyfikowane Heatit
- Niesklasyfikowane ProForm
- Niesklasyfikowane UTEPO
- Niesklasyfikowane Purpleline
- Niesklasyfikowane Think Tank
- Niesklasyfikowane Portech
- Niesklasyfikowane Lec
- Niesklasyfikowane Geomag
- Niesklasyfikowane LTC
- Niesklasyfikowane Koala
- Niesklasyfikowane Drawmer
- Niesklasyfikowane Audeze
- Niesklasyfikowane Blue Sky
- Niesklasyfikowane Dunlop
- Niesklasyfikowane Valeo
- Niesklasyfikowane Velbus
- Niesklasyfikowane Babyzen
- Niesklasyfikowane Woonexpress
- Niesklasyfikowane IQAir
- Niesklasyfikowane Sanus Systems
- Niesklasyfikowane BabyDan
- Niesklasyfikowane Tormatic
- Niesklasyfikowane After Later Audio
- Niesklasyfikowane Aqara
- Niesklasyfikowane 2hp
- Niesklasyfikowane Energizer
- Niesklasyfikowane IXS
- Niesklasyfikowane Samlex
- Niesklasyfikowane Navionics
- Niesklasyfikowane Zalman
- Niesklasyfikowane Turbo Air
- Niesklasyfikowane Zega
- Niesklasyfikowane Leatherman
- Niesklasyfikowane CreativeWorKs
- Niesklasyfikowane Horizon
- Niesklasyfikowane Ultimate Support
- Niesklasyfikowane Rösle
- Niesklasyfikowane Interphone
- Niesklasyfikowane Prince
- Niesklasyfikowane AXI
- Niesklasyfikowane Inter-Tech
- Niesklasyfikowane Thomann
- Niesklasyfikowane Holzmann
- Niesklasyfikowane EMG
- Niesklasyfikowane James
- Niesklasyfikowane Bicker Elektronik
- Niesklasyfikowane Iadea
- Niesklasyfikowane Blizzard
- Niesklasyfikowane Nimble
- Niesklasyfikowane SIIG
- Niesklasyfikowane Reginox
- Niesklasyfikowane BIOS Medical
- Niesklasyfikowane Advantech
- Niesklasyfikowane PSSO
- Niesklasyfikowane Wise
- Niesklasyfikowane SIG Sauer
- Niesklasyfikowane Merkel
- Niesklasyfikowane Biohort
- Niesklasyfikowane Crest Audio
- Niesklasyfikowane Globe
- Niesklasyfikowane Rossi
- Niesklasyfikowane Hercules
- Niesklasyfikowane Grace Design
- Niesklasyfikowane Contour Design
- Niesklasyfikowane Propellerhead
- Niesklasyfikowane Nanuk
- Niesklasyfikowane Digital Watchdog
- Niesklasyfikowane Riviera And Bar
- Niesklasyfikowane Apelson
- Niesklasyfikowane Kreiling
- Niesklasyfikowane Xantech
- Niesklasyfikowane Scanstrut
- Niesklasyfikowane Marker
- Niesklasyfikowane Kohler
- Niesklasyfikowane Safco
- Niesklasyfikowane Xunzel
- Niesklasyfikowane Oklahoma Sound
- Niesklasyfikowane Thames & Kosmos
- Niesklasyfikowane Betso
- Niesklasyfikowane Fortia
- Niesklasyfikowane Moen
- Niesklasyfikowane Babysense
- Niesklasyfikowane Namco Bandai Games
- Niesklasyfikowane Sealy
- Niesklasyfikowane Wet Sounds
- Niesklasyfikowane CRU
- Niesklasyfikowane Avantone Pro
- Niesklasyfikowane Umarex
- Niesklasyfikowane Televés
- Niesklasyfikowane AbleNet
- Niesklasyfikowane Exalux
- Niesklasyfikowane IBasso
- Niesklasyfikowane Gtech
- Niesklasyfikowane Leap Frog
- Niesklasyfikowane Sightmark
- Niesklasyfikowane Eissound
- Niesklasyfikowane Ganz
- Niesklasyfikowane Hughes & Kettner
- Niesklasyfikowane Manley
- Niesklasyfikowane Micro Matic
- Niesklasyfikowane Thermomate
- Niesklasyfikowane Steiner
- Niesklasyfikowane Graphite
- Niesklasyfikowane Gosund
- Niesklasyfikowane HMS Premium
- Niesklasyfikowane TVLogic
- Niesklasyfikowane Gamber-Johnson
- Niesklasyfikowane Acard
- Niesklasyfikowane Burigotto
- Niesklasyfikowane T.I.P.
- Niesklasyfikowane Gra-Vue
- Niesklasyfikowane Doffler
- Niesklasyfikowane On-Stage
- Niesklasyfikowane SurgeX
- Niesklasyfikowane MuxLab
- Niesklasyfikowane Sencys
- Niesklasyfikowane Norton Clipper
- Niesklasyfikowane Extron
- Niesklasyfikowane Avocent
- Niesklasyfikowane Geze
- Niesklasyfikowane RTS
- Niesklasyfikowane Ontech
- Niesklasyfikowane HyperJuice
- Niesklasyfikowane Swingline
- Niesklasyfikowane RaySafe
- Niesklasyfikowane Di4
- Niesklasyfikowane Hohner
- Niesklasyfikowane Ocean Matrix
- Niesklasyfikowane MAK
- Niesklasyfikowane Dobot
- Niesklasyfikowane Ocean Way Audio
- Niesklasyfikowane Nearity
- Niesklasyfikowane Comprehensive
- Niesklasyfikowane Sanli
- Niesklasyfikowane Husky
- Niesklasyfikowane Philos
- Niesklasyfikowane Legamaster
- Niesklasyfikowane Siemon
- Niesklasyfikowane Block & Block
- Niesklasyfikowane Brondell
- Niesklasyfikowane NutriBullet
- Niesklasyfikowane Four Hands
- Niesklasyfikowane Oben
- Niesklasyfikowane ASA
- Niesklasyfikowane Thronmax
- Niesklasyfikowane Botex
- Niesklasyfikowane Maxsa
- Niesklasyfikowane Tripp
- Niesklasyfikowane TRIUS
- Niesklasyfikowane Ankarsrum
- Niesklasyfikowane Etymotic
- Niesklasyfikowane Fine Dine
- Niesklasyfikowane ClearOne
- Niesklasyfikowane Superrollo
- Niesklasyfikowane Goldtouch
- Niesklasyfikowane Gamewright
- Niesklasyfikowane Braun Phototechnik
- Niesklasyfikowane Black Decker
- Niesklasyfikowane SXT
- Niesklasyfikowane Essenza
- Niesklasyfikowane Seecode
- Niesklasyfikowane Thomas
- Niesklasyfikowane Rugged Geek
- Niesklasyfikowane Dave Smith
- Niesklasyfikowane Skymaster
- Niesklasyfikowane Gardol
- Niesklasyfikowane Helix
- Niesklasyfikowane TFA Dostmann
- Niesklasyfikowane Durable
- Niesklasyfikowane Zenza Bronica
- Niesklasyfikowane Spypoint
- Niesklasyfikowane Suprema
- Niesklasyfikowane Ziehl
- Niesklasyfikowane VAIS
- Niesklasyfikowane Perma
- Niesklasyfikowane Scandes
- Niesklasyfikowane Testec
- Niesklasyfikowane Quadro
- Niesklasyfikowane Enovate
- Niesklasyfikowane Lofrans
- Niesklasyfikowane Winegard
- Niesklasyfikowane Pigtronix
- Niesklasyfikowane ProTeam
- Niesklasyfikowane Wagner SprayTech
- Niesklasyfikowane Libec
- Niesklasyfikowane Pardini
- Niesklasyfikowane KWC
- Niesklasyfikowane Soul
- Niesklasyfikowane Laney
- Niesklasyfikowane Compex
- Niesklasyfikowane Theragun
- Niesklasyfikowane Weil
- Niesklasyfikowane Plantiflor
- Niesklasyfikowane LAS
- Niesklasyfikowane Rosseto
- Niesklasyfikowane Redrock Micro
- Niesklasyfikowane Motu
- Niesklasyfikowane Kata
- Niesklasyfikowane Minix
- Niesklasyfikowane Lazer
- Niesklasyfikowane EarthQuaker Devices
- Niesklasyfikowane The Grainfather
- Niesklasyfikowane Kessler
- Niesklasyfikowane Emga
- Niesklasyfikowane Briggs & Stratton
- Niesklasyfikowane USAopoly
- Niesklasyfikowane Gami
- Niesklasyfikowane Igloohome
- Niesklasyfikowane Rothenberger
- Niesklasyfikowane Creamsource
- Niesklasyfikowane Kenko
- Niesklasyfikowane Zennio
- Niesklasyfikowane Vixen
- Niesklasyfikowane B-tech
- Niesklasyfikowane Praktica
- Niesklasyfikowane Elinchrom
- Niesklasyfikowane Boori
- Niesklasyfikowane CamRanger
- Niesklasyfikowane Hasselblad
- Niesklasyfikowane Madrix
- Niesklasyfikowane Q Acoustics
- Niesklasyfikowane Spacedec
- Niesklasyfikowane Auray
- Niesklasyfikowane Bontempi
- Niesklasyfikowane Furman
- Niesklasyfikowane Summer Infant
- Niesklasyfikowane Cooper & Quint
- Niesklasyfikowane Deltex
- Niesklasyfikowane Adax
- Niesklasyfikowane Xplora
- Niesklasyfikowane Eonon
- Niesklasyfikowane Calligaris .com
- Niesklasyfikowane SMC
- Niesklasyfikowane Ibico
- Niesklasyfikowane OXO Good Grips
- Niesklasyfikowane Exit Toys
- Niesklasyfikowane Triton
- Niesklasyfikowane Profizelt24
- Niesklasyfikowane Helios Preisser
- Niesklasyfikowane YSI
- Niesklasyfikowane Yeyian
- Niesklasyfikowane Paulmann
- Niesklasyfikowane Nitek
- Niesklasyfikowane Snoes
- Niesklasyfikowane Alpatronix
- Niesklasyfikowane Labelmate
- Niesklasyfikowane Martin Audio
- Niesklasyfikowane Schertler
- Niesklasyfikowane Teradek
- Niesklasyfikowane Sissel
- Niesklasyfikowane Kunath
- Niesklasyfikowane Penclic
- Niesklasyfikowane SolarEdge
- Niesklasyfikowane ViewCast
- Niesklasyfikowane Crown
- Niesklasyfikowane Kogan
- Niesklasyfikowane Tennsco
- Niesklasyfikowane FireKing
- Niesklasyfikowane RAM Mounts
- Niesklasyfikowane Novus
- Niesklasyfikowane Getac
- Niesklasyfikowane Arebos
- Niesklasyfikowane Kreg
- Niesklasyfikowane Bentley
- Niesklasyfikowane Morningstar
- Niesklasyfikowane DMax
- Niesklasyfikowane Backyard Discovery
- Niesklasyfikowane Minuteman
- Niesklasyfikowane Ortofon
- Niesklasyfikowane RéVive
- Niesklasyfikowane Mega
- Niesklasyfikowane Star Micronics
- Niesklasyfikowane Woodland Scenics
- Niesklasyfikowane Chapin
- Niesklasyfikowane Morel
- Niesklasyfikowane J. Rockett Audio Designs
- Niesklasyfikowane Pancontrol
- Niesklasyfikowane Satisfyer
- Niesklasyfikowane Hämmerli
- Niesklasyfikowane Verto
- Niesklasyfikowane Soma
- Niesklasyfikowane Posiflex
- Niesklasyfikowane Little Giant
- Niesklasyfikowane Point 65
- Niesklasyfikowane ReTrak
- Niesklasyfikowane Avantree
- Niesklasyfikowane LYYT
- Niesklasyfikowane Old Blood Noise
- Niesklasyfikowane Vulcan
- Niesklasyfikowane CradlePoint
- Niesklasyfikowane GAO
- Niesklasyfikowane Rovo Kids
- Niesklasyfikowane Catalyst
- Niesklasyfikowane Dension
- Niesklasyfikowane Antelope Audio
- Niesklasyfikowane Brinno
- Niesklasyfikowane Venom
- Niesklasyfikowane CE Labs
- Niesklasyfikowane Legrand
- Niesklasyfikowane Z CAM
- Niesklasyfikowane Digium
- Niesklasyfikowane Giardino
- Niesklasyfikowane Mulex
- Niesklasyfikowane Socomec
- Niesklasyfikowane System Sensor
- Niesklasyfikowane San Jamar
- Niesklasyfikowane IPort
- Niesklasyfikowane X-Rite
- Niesklasyfikowane Wetelux
- Niesklasyfikowane Talkaphone
- Niesklasyfikowane Merax
- Niesklasyfikowane GermGuardian
- Niesklasyfikowane R-Go Tools
- Niesklasyfikowane Urbanista
- Niesklasyfikowane Sagitter
- Niesklasyfikowane Rainbow
- Niesklasyfikowane Duracell
- Niesklasyfikowane Riello
- Niesklasyfikowane Gagato
- Niesklasyfikowane General
- Niesklasyfikowane ECTIVE
- Niesklasyfikowane Gymform
- Niesklasyfikowane Ebro
- Niesklasyfikowane Tzumi
- Niesklasyfikowane BERTSCHAT
- Niesklasyfikowane Schumacher
- Niesklasyfikowane Michael Todd Beauty
- Niesklasyfikowane Cygnett
- Niesklasyfikowane Germania
- Niesklasyfikowane Victorio
- Niesklasyfikowane Platinum
- Niesklasyfikowane Trimble
- Niesklasyfikowane Sensei
- Niesklasyfikowane Playtive Junior
- Niesklasyfikowane Parklands
- Niesklasyfikowane Avid
- Niesklasyfikowane Vipack
- Niesklasyfikowane EKO
- Niesklasyfikowane BIG
- Niesklasyfikowane Emeril Lagasse
- Niesklasyfikowane POGS
- Niesklasyfikowane Graflex
- Niesklasyfikowane Coolaroo
- Niesklasyfikowane Wurth
- Niesklasyfikowane Mebus
- Niesklasyfikowane Gioteck
- Niesklasyfikowane Kenton
- Niesklasyfikowane Cypress
- Niesklasyfikowane Foliatec
- Niesklasyfikowane Silhouette
- Niesklasyfikowane South Shore
- Niesklasyfikowane Discovery
- Niesklasyfikowane T4E
- Niesklasyfikowane Speck
- Niesklasyfikowane Generation
- Niesklasyfikowane Iseki
- Niesklasyfikowane MOZA
- Niesklasyfikowane Ecler
- Niesklasyfikowane Turbosound
- Niesklasyfikowane Phase One
- Niesklasyfikowane Röhm
- Niesklasyfikowane ADDAC System
- Niesklasyfikowane Roadinger
- Niesklasyfikowane Ulanzi
- Niesklasyfikowane Anova
- Niesklasyfikowane Viscount
- Niesklasyfikowane Hurricane
- Niesklasyfikowane DAB
- Niesklasyfikowane Anex
- Niesklasyfikowane Majella
- Niesklasyfikowane GMB Audio
- Niesklasyfikowane Ashdown Engineering
- Niesklasyfikowane Century
- Niesklasyfikowane Unger
- Niesklasyfikowane Anthro
- Niesklasyfikowane Inverto
- Niesklasyfikowane Special-T
- Niesklasyfikowane Ygnis
- Niesklasyfikowane Esotec
- Niesklasyfikowane True & Tidy
- Niesklasyfikowane NovaStar
- Niesklasyfikowane Petkit
- Niesklasyfikowane Icon
- Niesklasyfikowane Kitchen Brains
- Niesklasyfikowane Challenge Xtreme
- Niesklasyfikowane Best
- Niesklasyfikowane Flycam
- Niesklasyfikowane NetAlly
- Niesklasyfikowane Triax
- Niesklasyfikowane XS Power
- Niesklasyfikowane Peltor
- Niesklasyfikowane JAR Systems
- Niesklasyfikowane Moleskine
- Niesklasyfikowane Bytecc
- Niesklasyfikowane Strex
- Niesklasyfikowane Xlyne
- Niesklasyfikowane Premier Mounts
- Niesklasyfikowane One Stop Systems
- Niesklasyfikowane Cool Maker
- Niesklasyfikowane Neo
- Niesklasyfikowane Mtx Audio
- Niesklasyfikowane DoughXpress
- Niesklasyfikowane Aquatic AV
- Niesklasyfikowane Parasound
- Niesklasyfikowane MSR
- Niesklasyfikowane Cabstone
- Niesklasyfikowane SPT
- Niesklasyfikowane DB Technologies
- Niesklasyfikowane Promate
- Niesklasyfikowane Tru Components
- Niesklasyfikowane Step2
- Niesklasyfikowane Crystal Quest
- Niesklasyfikowane Pit Boss
- Niesklasyfikowane Needit
- Niesklasyfikowane MiPow
- Niesklasyfikowane GoldenEar Technology
- Niesklasyfikowane Colt
- Niesklasyfikowane Elite Screens
- Niesklasyfikowane Ultron
- Niesklasyfikowane Choice
- Niesklasyfikowane Roswell
- Niesklasyfikowane King Craft
- Niesklasyfikowane FOX ESS
- Niesklasyfikowane Airman
- Niesklasyfikowane Cascade Audio Engineering
- Niesklasyfikowane B-Speech
- Niesklasyfikowane Vanish
- Niesklasyfikowane Nostalgia
- Niesklasyfikowane Grosfillex
- Niesklasyfikowane Solplanet
- Niesklasyfikowane Beemoo
- Niesklasyfikowane Platinet
- Niesklasyfikowane Santos
- Niesklasyfikowane Evoc
- Niesklasyfikowane Versare
- Niesklasyfikowane Alutruss
- Niesklasyfikowane Tractive
- Niesklasyfikowane SpeakerCraft
- Niesklasyfikowane Celexon
- Niesklasyfikowane Epcom
- Niesklasyfikowane ZeeVee
- Niesklasyfikowane Siku
- Niesklasyfikowane Viatek
- Niesklasyfikowane Simplicity
- Niesklasyfikowane Doomoo
- Niesklasyfikowane MBZ
- Niesklasyfikowane Davey
- Niesklasyfikowane Mettler
- Niesklasyfikowane Metalux
- Niesklasyfikowane Potenza
- Niesklasyfikowane LOQED
- Niesklasyfikowane Hatco
- Niesklasyfikowane KONFTEL
- Niesklasyfikowane Canicom
- Niesklasyfikowane Mitsai
- Niesklasyfikowane Selfsat
- Niesklasyfikowane Leef
- Niesklasyfikowane Tusa
- Niesklasyfikowane Hovicon
- Niesklasyfikowane Starlyf
- Niesklasyfikowane Point Source Audio
- Niesklasyfikowane American BioTech Supply
- Niesklasyfikowane Noris
- Niesklasyfikowane Schmidt & Bender
- Niesklasyfikowane Mesa Boogie
- Niesklasyfikowane Improv
- Niesklasyfikowane LandRoller
- Niesklasyfikowane Wegman
- Niesklasyfikowane Lockncharge
- Niesklasyfikowane Merlin
- Niesklasyfikowane Standard Horizon
- Niesklasyfikowane Goal Zero
- Niesklasyfikowane HealthPostures
- Niesklasyfikowane CYP
- Niesklasyfikowane Heaven Fresh
- Niesklasyfikowane Lutec
- Niesklasyfikowane Champion Sports
- Niesklasyfikowane Molotow
- Niesklasyfikowane Herlag
- Niesklasyfikowane Dux
- Niesklasyfikowane JMAZ Lighting
- Niesklasyfikowane Hortus
- Niesklasyfikowane FALLER
- Niesklasyfikowane Miditech
- Niesklasyfikowane TTM
- Niesklasyfikowane Paw Patrol
- Niesklasyfikowane LELO
- Niesklasyfikowane Mermade
- Niesklasyfikowane MXR
- Niesklasyfikowane SKLZ
- Niesklasyfikowane Herma
- Niesklasyfikowane BWT
- Niesklasyfikowane Syrp
- Niesklasyfikowane Ugolini
- Niesklasyfikowane Cosina
- Niesklasyfikowane Heckler & Koch
- Niesklasyfikowane Whistler
- Niesklasyfikowane Twisper
- Niesklasyfikowane J5create
- Niesklasyfikowane Hushmat
- Niesklasyfikowane Xigmatek
- Niesklasyfikowane Tema
- Niesklasyfikowane ALM
- Niesklasyfikowane Topaz
- Niesklasyfikowane Toddy
- Niesklasyfikowane Aicon
- Niesklasyfikowane Astell&Kern
- Niesklasyfikowane Fun Generation
- Niesklasyfikowane Berkel
- Niesklasyfikowane Glorious
- Niesklasyfikowane Ciarra
- Niesklasyfikowane Bellari
- Niesklasyfikowane Beghelli
- Niesklasyfikowane Hugo Muller
- Niesklasyfikowane Vinci
- Niesklasyfikowane Jordan
- Niesklasyfikowane Duromax
- Niesklasyfikowane DataComm
- Niesklasyfikowane Powercube
- Niesklasyfikowane Kasp
- Niesklasyfikowane Dimavery
- Niesklasyfikowane WestBend
- Niesklasyfikowane Mr Coffee
- Niesklasyfikowane Sherlock
- Niesklasyfikowane SEA-PRO
- Niesklasyfikowane Omiindustriies
- Niesklasyfikowane Weltevree
- Niesklasyfikowane Phoenix Contact
- Niesklasyfikowane AMS Neve
- Niesklasyfikowane LVSUN
- Niesklasyfikowane Aston Microphones
- Niesklasyfikowane Netsys
- Niesklasyfikowane Alfi
- Niesklasyfikowane Polarlite
- Niesklasyfikowane Companion
- Niesklasyfikowane Mr. Beams
- Niesklasyfikowane Morphor
- Niesklasyfikowane Lapp
- Niesklasyfikowane XO
- Niesklasyfikowane PcDuino
- Niesklasyfikowane LECO
- Niesklasyfikowane Maretron
- Niesklasyfikowane Razorri
- Niesklasyfikowane Fetch
- Niesklasyfikowane Zoetis
- Niesklasyfikowane Prem-i-air
- Niesklasyfikowane NWS
- Niesklasyfikowane GAM
- Niesklasyfikowane EXO
- Niesklasyfikowane Altman
- Niesklasyfikowane FoxFury
- Niesklasyfikowane Eller
- Niesklasyfikowane Grimm Audio
- Niesklasyfikowane A-NeuVideo
- Niesklasyfikowane Best Service
- Niesklasyfikowane Arylic
- Niesklasyfikowane Aguilar
- Niesklasyfikowane Alogic
- Niesklasyfikowane Scale Computing
- Niesklasyfikowane Naturn Living
- Niesklasyfikowane Aeotec
- Niesklasyfikowane Catlink
- Niesklasyfikowane FitterFirst
- Niesklasyfikowane Raveland
- Niesklasyfikowane Mr. Heater
- Niesklasyfikowane Welltech
- Niesklasyfikowane Trumeter
- Niesklasyfikowane Seidio
- Niesklasyfikowane Sincreative
- Niesklasyfikowane JDC
- Niesklasyfikowane Hidrate
- Niesklasyfikowane Sonicware
- Niesklasyfikowane Nexibo
- Niesklasyfikowane Jolin
- Niesklasyfikowane MoTip
- Niesklasyfikowane Stenda
- Niesklasyfikowane Pro-Lift
- Niesklasyfikowane HIOAZO
- Niesklasyfikowane Malstrom
- Niesklasyfikowane Laserluchs
- Niesklasyfikowane Powersoft
- Niesklasyfikowane Casetastic
- Niesklasyfikowane UClear
- Niesklasyfikowane BikeLogger
- Niesklasyfikowane Tor Rey
- Niesklasyfikowane Momo Design
- Niesklasyfikowane Esdec
- Niesklasyfikowane Ruark Audio
- Niesklasyfikowane AJH Synth
- Niesklasyfikowane LifeStraw
- Niesklasyfikowane Magnavox
- Niesklasyfikowane Toolit
- Niesklasyfikowane Egnater
- Niesklasyfikowane DutchOne
- Niesklasyfikowane Feitian
- Niesklasyfikowane Ergie
- Niesklasyfikowane Reltech
- Niesklasyfikowane Armcross
- Niesklasyfikowane Focus Electrics
- Niesklasyfikowane Huntleigh
- Niesklasyfikowane Beeletix
- Niesklasyfikowane Claypaky
- Niesklasyfikowane EOTech
- Niesklasyfikowane Gehmann
- Niesklasyfikowane Batronix
- Niesklasyfikowane Franzis
- Niesklasyfikowane Gridbyt
- Niesklasyfikowane LONQ
- Niesklasyfikowane Wonky Monkey
- Niesklasyfikowane Dresden Elektronik
- Niesklasyfikowane Atmel
- Niesklasyfikowane Flavour Blaster
- Niesklasyfikowane SmartAVI
- Niesklasyfikowane EPH Elektronik
- Niesklasyfikowane InfiRay
- Niesklasyfikowane Markbass
- Niesklasyfikowane IMG Stage Line
- Niesklasyfikowane IMAC
- Niesklasyfikowane Metz Connect
- Niesklasyfikowane MGL Avionics
- Niesklasyfikowane Eikon
- Niesklasyfikowane Casablanca
- Niesklasyfikowane Nemco
- Niesklasyfikowane Wireless Solution
- Niesklasyfikowane Beverage-Air
- Niesklasyfikowane Sparco
- Niesklasyfikowane Barber Tech
- Niesklasyfikowane Estella
- Niesklasyfikowane EarFun
- Niesklasyfikowane Minkels
- Niesklasyfikowane Kipor
- Niesklasyfikowane Lenmar
- Niesklasyfikowane Arduino
- Niesklasyfikowane Ave Six
- Niesklasyfikowane Bestar
- Niesklasyfikowane Pelco
- Niesklasyfikowane Gardigo
- Niesklasyfikowane Highpoint
- Niesklasyfikowane Puls Dimension
- Niesklasyfikowane Studiologic
- Niesklasyfikowane Fischer Amps
- Niesklasyfikowane CHINT
- Niesklasyfikowane Sirus
- Niesklasyfikowane Digitech
- Niesklasyfikowane Leviton
- Niesklasyfikowane Gretsch
- Niesklasyfikowane Pentacon
- Niesklasyfikowane Winia
- Niesklasyfikowane Bolsey
- Niesklasyfikowane Louis Tellier
- Niesklasyfikowane Baracuda
- Niesklasyfikowane Kstar
- Niesklasyfikowane Air Guard
- Niesklasyfikowane MediaMatrix
- Niesklasyfikowane ESX
- Niesklasyfikowane Tuur
- Niesklasyfikowane ONE Smart Control
- Niesklasyfikowane OBSBOT
- Niesklasyfikowane InSinkErator
- Niesklasyfikowane AREXX
- Niesklasyfikowane Elite Force
- Niesklasyfikowane DEHN
- Niesklasyfikowane Piko
- Niesklasyfikowane Lifan
- Niesklasyfikowane Jomox
- Niesklasyfikowane Pentatech
- Niesklasyfikowane Burley
- Niesklasyfikowane Lexicon
- Niesklasyfikowane Icarus Blue
- Niesklasyfikowane Command
- Niesklasyfikowane IRIS
- Niesklasyfikowane Neno
- Niesklasyfikowane Starburst
- Niesklasyfikowane Fluance
- Niesklasyfikowane PCE Instruments
- Niesklasyfikowane Garden Place
- Niesklasyfikowane Moldex
- Niesklasyfikowane MaximaVida
- Niesklasyfikowane Firefriend
- Niesklasyfikowane LightZone
- Niesklasyfikowane Bliss Outdoors
- Niesklasyfikowane Fontiso
- Niesklasyfikowane Varytec
- Niesklasyfikowane Altra
- Niesklasyfikowane Omnilux
- Niesklasyfikowane Quartet
- Niesklasyfikowane Shadow
- Niesklasyfikowane IP-COM
- Niesklasyfikowane Comtek
- Niesklasyfikowane Digital Juice
- Niesklasyfikowane Eschenbach
- Niesklasyfikowane ASM
- Niesklasyfikowane Elektron
- Niesklasyfikowane Ltech
- Niesklasyfikowane RetroSound
- Niesklasyfikowane Caroline
- Niesklasyfikowane Zomo
- Niesklasyfikowane VAIS Technology
- Niesklasyfikowane Buchla & TipTop Audio
- Niesklasyfikowane Pyramid
- Niesklasyfikowane Maico
- Niesklasyfikowane On-Q
- Niesklasyfikowane SetonixSynth
- Niesklasyfikowane Horex
- Niesklasyfikowane Inno-Hit
- Niesklasyfikowane Sime
- Niesklasyfikowane AvaValley
- Niesklasyfikowane INTIMINA
- Niesklasyfikowane FCC BBQ
- Niesklasyfikowane Auto XS
- Niesklasyfikowane Toomax
- Niesklasyfikowane Aqua Marina
- Niesklasyfikowane Hameg
- Niesklasyfikowane Greemotion
- Niesklasyfikowane Winter Modular
- Niesklasyfikowane Synamodec
- Niesklasyfikowane Grotime
- Niesklasyfikowane Pico Macom
- Niesklasyfikowane RadonTec
- Niesklasyfikowane Katrin
- Niesklasyfikowane Kendau
- Niesklasyfikowane NUX
- Niesklasyfikowane Coxreels
- Niesklasyfikowane Overade
- Niesklasyfikowane Liemke
- Niesklasyfikowane Copco
- Niesklasyfikowane Vanson
- Niesklasyfikowane Canyon
- Niesklasyfikowane Carcomm
- Niesklasyfikowane Style Me Up
- Niesklasyfikowane Swedish Posture
- Niesklasyfikowane Melnor
- Niesklasyfikowane CDVI
- Niesklasyfikowane Excalibur
- Niesklasyfikowane Holman
- Niesklasyfikowane HomePilot
- Niesklasyfikowane Leaptel
- Niesklasyfikowane Lifenaxx
- Niesklasyfikowane Powertec
- Niesklasyfikowane Waterbird
- Niesklasyfikowane Dreambaby
- Niesklasyfikowane AOpen
- Niesklasyfikowane Angler
- Niesklasyfikowane GP
- Niesklasyfikowane Akrobat
- Niesklasyfikowane Selleys
- Niesklasyfikowane WindFall
- Niesklasyfikowane Ameristep
- Niesklasyfikowane KM-fit
- Niesklasyfikowane X Rocker
- Niesklasyfikowane Mircom
- Niesklasyfikowane ESUN
- Niesklasyfikowane Durex
- Niesklasyfikowane ZWO
- Niesklasyfikowane AeroCool
- Niesklasyfikowane Vantage Point
- Niesklasyfikowane Jokari
- Niesklasyfikowane Engel
- Niesklasyfikowane BeeSecure
- Niesklasyfikowane MantelMount
- Niesklasyfikowane Unicol
- Niesklasyfikowane Fisher Paykel
- Niesklasyfikowane Lasita Maja
- Niesklasyfikowane Meccano
- Niesklasyfikowane Parallels
- Niesklasyfikowane Oatey
- Niesklasyfikowane QUIO
- Niesklasyfikowane Fisher
- Niesklasyfikowane Gretsch Guitars
- Niesklasyfikowane Banoch
- Niesklasyfikowane XP-PEN
- Niesklasyfikowane Atmotube
- Niesklasyfikowane Sun Pumps
- Niesklasyfikowane Electrify
- Niesklasyfikowane Leatt
- Niesklasyfikowane Bleep Labs
- Niesklasyfikowane FontaFit
- Niesklasyfikowane Gossmann
- Niesklasyfikowane Comatec
- Niesklasyfikowane Jonard Tools
- Niesklasyfikowane WEG
- Niesklasyfikowane Atech Flash Technology
- Niesklasyfikowane AutoParkTime
- Niesklasyfikowane Hudora
- Niesklasyfikowane Facal
- Niesklasyfikowane Planet Audio
- Niesklasyfikowane Datacolor
- Niesklasyfikowane Silicon Power
- Niesklasyfikowane JAXY
- Niesklasyfikowane WARN
- Niesklasyfikowane Aarke
- Niesklasyfikowane TikkTokk
- Niesklasyfikowane Roco
- Niesklasyfikowane Flexson
- Niesklasyfikowane Camec
- Niesklasyfikowane Wibrain
- Niesklasyfikowane Rolly Toys
- Niesklasyfikowane CAD Audio
- Niesklasyfikowane Altrad
- Niesklasyfikowane Black Hydra
- Niesklasyfikowane Level Mount
- Niesklasyfikowane Teenage Engineering
- Niesklasyfikowane Elipson
- Niesklasyfikowane STANDIVARIUS
- Niesklasyfikowane CommScope
- Niesklasyfikowane Orange
- Niesklasyfikowane Extralife Instruments
- Niesklasyfikowane Genki Instruments
- Niesklasyfikowane Industrial Music Electronics
- Niesklasyfikowane Mauser Sitzkultur
- Niesklasyfikowane Accezz
- Niesklasyfikowane A4 Tech
- Niesklasyfikowane Full Boar
- Niesklasyfikowane Zedar
- Niesklasyfikowane Yli Electronic
- Niesklasyfikowane Dals
- Niesklasyfikowane Bulman
- Niesklasyfikowane TOOLMATE
- Niesklasyfikowane SleepPro
- Niesklasyfikowane Muama
- Niesklasyfikowane Lepu Medical
- Niesklasyfikowane Michigan
- Niesklasyfikowane Beringer
- Niesklasyfikowane Phonic
- Niesklasyfikowane ZCover
- Niesklasyfikowane Vasagle
- Niesklasyfikowane Aquatica
- Niesklasyfikowane Girmi
- Niesklasyfikowane Goaliath
- Niesklasyfikowane 909 Outdoor
- Niesklasyfikowane Viomi
- Niesklasyfikowane Better Life
- Niesklasyfikowane Dayclocks
- Niesklasyfikowane Phidgets
- Niesklasyfikowane TK Audio
- Niesklasyfikowane Hawk-Woods
- Niesklasyfikowane Novo
- Niesklasyfikowane Commercial Chef
- Niesklasyfikowane Dexibell
- Niesklasyfikowane IsoAcoustics
- Niesklasyfikowane Memphis
- Niesklasyfikowane Clifford
- Niesklasyfikowane Cambo
- Niesklasyfikowane Hedbox
- Niesklasyfikowane Lansinoh
- Niesklasyfikowane Maclean
- Niesklasyfikowane 9.solutions
- Niesklasyfikowane WEN
- Niesklasyfikowane Trace Elliot
- Niesklasyfikowane Lockwood
- Niesklasyfikowane Nexera
- Niesklasyfikowane Goodway
- Niesklasyfikowane BlueDri
- Niesklasyfikowane Seenergy
- Niesklasyfikowane Meinl
- Niesklasyfikowane Analogis
- Niesklasyfikowane BBQ Premium
- Niesklasyfikowane Stäubli
- Niesklasyfikowane RAB
- Niesklasyfikowane Schabus
- Niesklasyfikowane Eoslift
- Niesklasyfikowane Bron-Coucke
- Niesklasyfikowane Steelton
- Niesklasyfikowane FeinTech
- Niesklasyfikowane Masterbuilt
- Niesklasyfikowane T-Rex
- Niesklasyfikowane Koolatron
- Niesklasyfikowane Euro Cuisine
- Niesklasyfikowane GFM
- Niesklasyfikowane Tot Tutors
- Niesklasyfikowane X4 Life
- Niesklasyfikowane Tonar
- Niesklasyfikowane Peterson
- Niesklasyfikowane CFH
- Niesklasyfikowane Emeril Everyday
- Niesklasyfikowane Rockboard
- Niesklasyfikowane Nivian
- Niesklasyfikowane L.R.Baggs
- Niesklasyfikowane Millennia
- Niesklasyfikowane Vermona Modular
- Niesklasyfikowane Adventure Kings
- Niesklasyfikowane Drive Medical
- Niesklasyfikowane Hitron
- Niesklasyfikowane Bliss Hammocks
- Niesklasyfikowane Singular Sound
- Niesklasyfikowane Maneco Labs
- Niesklasyfikowane BISWIND
- Niesklasyfikowane ABE Arnhold
- Niesklasyfikowane Mermade Hair
- Niesklasyfikowane Hover-1
- Niesklasyfikowane VCM
- Niesklasyfikowane BodyCraft
- Niesklasyfikowane Auer Signal
- Niesklasyfikowane BrightSign
- Niesklasyfikowane Mamas & Papas
- Niesklasyfikowane Manduca
- Niesklasyfikowane HELGI
- Niesklasyfikowane Forge Adour
- Niesklasyfikowane Darkglass
- Niesklasyfikowane Paasche
- Niesklasyfikowane Vistus
- Niesklasyfikowane GMW
- Niesklasyfikowane AER
- Niesklasyfikowane Dynavox
- Niesklasyfikowane Columbus
- Niesklasyfikowane IWH
- Niesklasyfikowane Code Mercenaries
- Niesklasyfikowane Diamex
- Niesklasyfikowane Sunset
- Niesklasyfikowane Avital
- Niesklasyfikowane Ondis24
- Niesklasyfikowane D'Addario
- Niesklasyfikowane BBE
- Niesklasyfikowane Warwick
- Niesklasyfikowane MyAVR
- Niesklasyfikowane EBS
- Niesklasyfikowane WEICON
- Niesklasyfikowane Rotronic
- Niesklasyfikowane Edsyn
- Niesklasyfikowane Urban Glide
- Niesklasyfikowane EISL
- Niesklasyfikowane RCS
- Niesklasyfikowane Nicai Systems
- Niesklasyfikowane IDENTsmart
- Niesklasyfikowane Sharper Image
- Niesklasyfikowane Revier Manager
- Niesklasyfikowane Homak
- Niesklasyfikowane Tycon Systems
- Niesklasyfikowane Selve
- Niesklasyfikowane Lumel
- Niesklasyfikowane Digigram
- Niesklasyfikowane Paingone
- Niesklasyfikowane Plugwise
- Niesklasyfikowane Martens
- Niesklasyfikowane Palmako
- Niesklasyfikowane Desview
- Niesklasyfikowane ActiveJet
- Niesklasyfikowane Global Water
- Niesklasyfikowane Allsee
- Niesklasyfikowane Softing
- Niesklasyfikowane Pulse ShowerSpas
- Niesklasyfikowane GFB
- Niesklasyfikowane Sonicsmith
- Niesklasyfikowane Toraiz
- Niesklasyfikowane Ergodyne
- Niesklasyfikowane Maturmeat
- Niesklasyfikowane D-Jix
- Niesklasyfikowane Orbsmart
- Niesklasyfikowane Eowave
- Niesklasyfikowane Imperia
- Niesklasyfikowane Nature2
- Niesklasyfikowane Baby Trend
- Niesklasyfikowane AMERRY
- Niesklasyfikowane Walther
- Niesklasyfikowane ShelterLogic
- Niesklasyfikowane Varad
- Niesklasyfikowane Dr. Browns
- Niesklasyfikowane KMA Machines
- Niesklasyfikowane Elcom
- Niesklasyfikowane Source Audio
- Niesklasyfikowane AtomoSynth
- Niesklasyfikowane Innr
- Niesklasyfikowane Benidub
- Niesklasyfikowane Protector
- Niesklasyfikowane Winston
- Niesklasyfikowane Solidsteel
- Niesklasyfikowane Dracast
- Niesklasyfikowane Dream
- Niesklasyfikowane Malouf
- Niesklasyfikowane Roba
- Niesklasyfikowane Ravelli
- Niesklasyfikowane Piet Boon
- Niesklasyfikowane PureTools
- Niesklasyfikowane JML
- Niesklasyfikowane Reber
- Niesklasyfikowane SiriusXM
- Niesklasyfikowane Earthwise
- Niesklasyfikowane DoubleSight
- Niesklasyfikowane Raya
- Niesklasyfikowane Artex
- Niesklasyfikowane Bobrick
- Niesklasyfikowane Verbos Electronics
- Niesklasyfikowane Ark
- Niesklasyfikowane DLO
- Niesklasyfikowane ENS
- Niesklasyfikowane Listen
- Niesklasyfikowane Oscium
- Niesklasyfikowane Benchmark USA
- Niesklasyfikowane Python
- Niesklasyfikowane Littelfuse
- Niesklasyfikowane Game Factor
- Niesklasyfikowane NComputing
- Niesklasyfikowane Mode Machines
- Niesklasyfikowane Legends
- Niesklasyfikowane AS Synthesizers
- Niesklasyfikowane Itechworld
- Niesklasyfikowane Nexcom
- Niesklasyfikowane SatKing
- Niesklasyfikowane Fulltone
- Niesklasyfikowane Advantix
- Niesklasyfikowane Wampler
- Niesklasyfikowane VAEMI
- Niesklasyfikowane Narva
- Niesklasyfikowane DOK
- Niesklasyfikowane OzCharge
- Niesklasyfikowane MIYO
- Niesklasyfikowane Cioks
- Niesklasyfikowane Neopower
- Niesklasyfikowane AvMap
- Niesklasyfikowane Arlec
- Niesklasyfikowane Sanwa
- Niesklasyfikowane REDARC
- Niesklasyfikowane Guardian
- Niesklasyfikowane Radio Flyer
- Niesklasyfikowane Gaslock
- Niesklasyfikowane Gaffgun
- Niesklasyfikowane AquaMAX
- Niesklasyfikowane DigitSole
- Niesklasyfikowane Portsmith
- Niesklasyfikowane Rome
- Niesklasyfikowane DW
- Niesklasyfikowane BEA
- Niesklasyfikowane Disty
- Niesklasyfikowane OXI Instruments
- Niesklasyfikowane AvaTime
- Niesklasyfikowane Xhose
- Niesklasyfikowane MYVU
- Niesklasyfikowane Kopykake
- Niesklasyfikowane Konstant Lab
- Niesklasyfikowane Turbo Scrub
- Niesklasyfikowane Tenderfoot Electronics
- Niesklasyfikowane Kask
- Niesklasyfikowane Callpod
- Niesklasyfikowane Dorman
- Niesklasyfikowane 2box
- Niesklasyfikowane Enlight
- Niesklasyfikowane Franken
- Niesklasyfikowane RUBI
- Niesklasyfikowane Europa Leisure
- Niesklasyfikowane GAMO
- Niesklasyfikowane Musser
- Niesklasyfikowane Edge Products
- Niesklasyfikowane IClever
- Niesklasyfikowane HN-Power
- Niesklasyfikowane BIONIK
- Niesklasyfikowane King Canopy
- Niesklasyfikowane HeadRush
- Niesklasyfikowane Flover
- Niesklasyfikowane Milestone Systems
- Niesklasyfikowane Micsig
- Niesklasyfikowane Dodow
- Niesklasyfikowane Spring
- Niesklasyfikowane Red Panda
- Niesklasyfikowane OJ ELECTRONICS
- Niesklasyfikowane Aquasure
- Niesklasyfikowane Banana Pi
- Niesklasyfikowane Ilford
- Niesklasyfikowane Crazy Tube Circuits
- Niesklasyfikowane J.P. Instruments
- Niesklasyfikowane Proclip
- Niesklasyfikowane SainSmart
- Niesklasyfikowane Kaona
- Niesklasyfikowane DPW Design
- Niesklasyfikowane SinuPulse
- Niesklasyfikowane The T.bone
- Niesklasyfikowane DIEZEL
- Niesklasyfikowane VMB
- Niesklasyfikowane Z.Vex
- Niesklasyfikowane Seymour Duncan
- Niesklasyfikowane BluGuitar
- Niesklasyfikowane Lehle
- Niesklasyfikowane Bricasti Design
- Niesklasyfikowane T.akustik
- Niesklasyfikowane Dwarf Connection
- Niesklasyfikowane JL Cooper
- Niesklasyfikowane StrikeMaster
- Niesklasyfikowane ProUser
- Niesklasyfikowane Bēm Wireless
- Niesklasyfikowane Aqua-Vu
- Niesklasyfikowane Millecroquettes
- Niesklasyfikowane GR Bass
- Niesklasyfikowane Sure-Fi
- Niesklasyfikowane Copernicus
- Niesklasyfikowane Gumdrop
- Niesklasyfikowane Tellur
- Niesklasyfikowane Woox
- Niesklasyfikowane Gallien-Krueger
- Niesklasyfikowane Jetway
- Niesklasyfikowane Texsport
- Niesklasyfikowane SSV Works
- Niesklasyfikowane Terre
- Niesklasyfikowane Sanitec
- Niesklasyfikowane Pangea Audio
- Niesklasyfikowane Hogue
- Niesklasyfikowane ATP
- Niesklasyfikowane Pfannenberg
- Niesklasyfikowane Scytek
- Niesklasyfikowane MotorScrubber
- Niesklasyfikowane Krone
- Niesklasyfikowane Kraftmax
- Niesklasyfikowane Steelplay
- Niesklasyfikowane PCTV Systems
- Niesklasyfikowane Cooper Lighting
- Niesklasyfikowane Code Corporation
- Niesklasyfikowane Now TV
- Niesklasyfikowane Best Fitness
- Niesklasyfikowane Voodoo Lab
- Niesklasyfikowane Strymon
- Niesklasyfikowane Insect Lore
- Niesklasyfikowane Faytech
- Niesklasyfikowane Chrome-Q
- Niesklasyfikowane Tektronix
- Niesklasyfikowane Kitronik
- Niesklasyfikowane Trasman
- Niesklasyfikowane Hamlet
- Niesklasyfikowane SumUp
- Niesklasyfikowane Microlab
- Niesklasyfikowane Rotolight
- Niesklasyfikowane Mr Gardener
- Niesklasyfikowane Lumu
- Niesklasyfikowane WAYDOO
- Niesklasyfikowane Fimer
- Niesklasyfikowane ASIWO
- Niesklasyfikowane Lexar
- Niesklasyfikowane Vent-Axia
- Niesklasyfikowane Firefield
- Niesklasyfikowane E-Power
- Niesklasyfikowane RectorSeal
- Niesklasyfikowane Kaiser Nienhaus
- Niesklasyfikowane Freeplay
- Niesklasyfikowane Roller Grill
- Niesklasyfikowane Zaor
- Niesklasyfikowane Cleco
- Niesklasyfikowane AVTech
- Niesklasyfikowane Bugera
- Niesklasyfikowane Handy Lux
- Niesklasyfikowane Rossum Electro-Music
- Niesklasyfikowane Panta
- Niesklasyfikowane Pentel
- Niesklasyfikowane Wallas
- Niesklasyfikowane Gima
- Niesklasyfikowane MagnaPool
- Niesklasyfikowane Aquadon
- Niesklasyfikowane Raidsonic
- Niesklasyfikowane Approx
- Niesklasyfikowane Gamesir
- Niesklasyfikowane Neunaber
- Niesklasyfikowane DPM
- Niesklasyfikowane VOREL
- Niesklasyfikowane DayStar Filters
- Niesklasyfikowane Flexispot
- Niesklasyfikowane OP/TECH
- Niesklasyfikowane Cinderella
- Niesklasyfikowane Bauhn
- Niesklasyfikowane Aspen
- Niesklasyfikowane Cottons
- Niesklasyfikowane Frequency Central
- Niesklasyfikowane Sacrament
- Niesklasyfikowane The Box
- Niesklasyfikowane AudioThing
- Niesklasyfikowane Cambium Networks
- Niesklasyfikowane Trident
- Niesklasyfikowane Schoeps
- Niesklasyfikowane HPI Racing
- Niesklasyfikowane Favini
- Niesklasyfikowane Dnipro
- Niesklasyfikowane IFootage
- Niesklasyfikowane Sonuus
- Niesklasyfikowane Jonsered
- Niesklasyfikowane Saint Algue
- Niesklasyfikowane Cactus
- Niesklasyfikowane Oecolux
- Niesklasyfikowane SoundLAB
- Niesklasyfikowane ACL
- Niesklasyfikowane Mars Gaming
- Niesklasyfikowane Radiant
- Niesklasyfikowane G.Skill
- Niesklasyfikowane Edbak
- Niesklasyfikowane DMT
- Niesklasyfikowane Integral LED
- Niesklasyfikowane Integral
- Niesklasyfikowane Roline
- Niesklasyfikowane Virax
- Niesklasyfikowane MSW
- Niesklasyfikowane Gill
- Niesklasyfikowane AMC
- Niesklasyfikowane Triangle
- Niesklasyfikowane Tumbleweed
- Niesklasyfikowane Sunpentown
- Niesklasyfikowane Hamstra
- Niesklasyfikowane PVI
- Niesklasyfikowane Avenview
- Niesklasyfikowane Grendel
- Niesklasyfikowane Coravin
- Niesklasyfikowane O&O Software
- Niesklasyfikowane Wasp
- Niesklasyfikowane Chef's Choice
- Niesklasyfikowane Warmup
- Niesklasyfikowane Brastemp
- Niesklasyfikowane Wavtech
- Niesklasyfikowane Satco
- Niesklasyfikowane AMT
- Niesklasyfikowane Royal Catering
- Niesklasyfikowane Artrom
- Niesklasyfikowane Lowell
- Niesklasyfikowane Adonit
- Niesklasyfikowane ANDYCINE
- Niesklasyfikowane AmpliVox
- Niesklasyfikowane Pippi
- Niesklasyfikowane Casalux
- Niesklasyfikowane CyberData Systems
- Niesklasyfikowane Omnitron Systems
- Niesklasyfikowane Stewart Systems
- Niesklasyfikowane SwitchBot
- Niesklasyfikowane Qubino
- Niesklasyfikowane Eurosound
- Niesklasyfikowane Williams Sound
- Niesklasyfikowane ICC
- Niesklasyfikowane Magewell
- Niesklasyfikowane Globalo
- Niesklasyfikowane SoundTube
- Niesklasyfikowane Therabody
- Niesklasyfikowane Infortrend
- Niesklasyfikowane STI
- Niesklasyfikowane Rug Doctor
- Niesklasyfikowane Raspberry Pi
- Niesklasyfikowane Bals
- Niesklasyfikowane Balt
- Niesklasyfikowane AJ.BA
- Niesklasyfikowane ESKA
- Niesklasyfikowane Lascar Electronics
- Niesklasyfikowane Sport-Tronic
- Niesklasyfikowane Alga
- Niesklasyfikowane WesAudio
- Niesklasyfikowane Hamron
- Niesklasyfikowane Robust
- Niesklasyfikowane Quik Lok
- Niesklasyfikowane Tsakalis AudioWorks
- Niesklasyfikowane MagTek
- Niesklasyfikowane Jupiter
- Niesklasyfikowane Sony Optiarc
- Niesklasyfikowane Colortone
- Niesklasyfikowane Super Rod
- Niesklasyfikowane Carnielli
- Niesklasyfikowane Luminex
- Niesklasyfikowane Epiphan
- Niesklasyfikowane Deltaco Gaming
- Niesklasyfikowane P3 International
- Niesklasyfikowane Idec
- Niesklasyfikowane Beckmann & Egle
- Niesklasyfikowane Seek Thermal
- Niesklasyfikowane VintageView
- Niesklasyfikowane Alfresco
- Niesklasyfikowane Bintec-elmeg
- Niesklasyfikowane Crane Song
- Niesklasyfikowane W'eau
- Niesklasyfikowane Belena
- Niesklasyfikowane Fanox
- Niesklasyfikowane Crouzet
- Niesklasyfikowane Megarevo
- Niesklasyfikowane Tech 21
- Niesklasyfikowane Petmate
- Niesklasyfikowane BlendMount
- Niesklasyfikowane Perlick
- Niesklasyfikowane Sedona
- Niesklasyfikowane Tecnoinox
- Niesklasyfikowane CaterRacks
- Niesklasyfikowane Besco
- Niesklasyfikowane Prologue
- Niesklasyfikowane Nanoleaf
- Niesklasyfikowane Mach Power
- Niesklasyfikowane Soltection
- Niesklasyfikowane Kool-It
- Niesklasyfikowane Cool Head
- Niesklasyfikowane KeepOut
- Niesklasyfikowane LawnMaster
- Niesklasyfikowane Deltronic
- Niesklasyfikowane Eligent
- Niesklasyfikowane Meris
- Niesklasyfikowane Procare
- Niesklasyfikowane AmerBox
- Niesklasyfikowane Qu-Bit
- Niesklasyfikowane Blue Lantern
- Niesklasyfikowane DivKid
- Niesklasyfikowane Uniross
- Niesklasyfikowane FaseLunare
- Niesklasyfikowane (Recovery)
- Niesklasyfikowane Twinkly
- Niesklasyfikowane Squarp Instruments
- Niesklasyfikowane EtherWAN
- Niesklasyfikowane Econ Connect
- Niesklasyfikowane META
- Niesklasyfikowane Shimbol
- Niesklasyfikowane GC Audio
- Niesklasyfikowane Einhell Bavaria
- Niesklasyfikowane Motrona
- Niesklasyfikowane Thalheimer
- Niesklasyfikowane FeiYu-Tech
- Niesklasyfikowane Aida
- Niesklasyfikowane VisionTek
- Niesklasyfikowane Accsoon
- Niesklasyfikowane Losi
- Niesklasyfikowane Bessey
- Niesklasyfikowane A3
- Niesklasyfikowane Serge
- Niesklasyfikowane Gladiator
- Niesklasyfikowane Mobli
- Niesklasyfikowane G-Technology
- Niesklasyfikowane Caroma
- Niesklasyfikowane Sungale
- Niesklasyfikowane Befaco
- Niesklasyfikowane Waltec
- Niesklasyfikowane Eartec
- Niesklasyfikowane Portkeys
- Niesklasyfikowane Westcott
- Niesklasyfikowane EXSYS
- Niesklasyfikowane Digiquest
- Niesklasyfikowane Gewiss
- Niesklasyfikowane Hagor
- Niesklasyfikowane Glyph
- Niesklasyfikowane Seco-Larm
- Niesklasyfikowane Massoth
- Niesklasyfikowane Envitec
- Niesklasyfikowane Mimo Monitors
- Niesklasyfikowane Alula
- Niesklasyfikowane Blebox
- Niesklasyfikowane VS Sassoon
- Niesklasyfikowane Redsbaby
- Niesklasyfikowane Bright Spark
- Niesklasyfikowane Algo
- Niesklasyfikowane Peloton
- Niesklasyfikowane Gentrax
- Niesklasyfikowane Brocade
- Niesklasyfikowane Insteon
- Niesklasyfikowane Altronix
- Niesklasyfikowane Warner Bros
- Niesklasyfikowane Vinotemp
- Niesklasyfikowane Silent Knight
- Niesklasyfikowane Mosconi
- Niesklasyfikowane CGV
- Niesklasyfikowane My Arcade
- Niesklasyfikowane Tescoma
- Niesklasyfikowane RF Elements
- Niesklasyfikowane ALC
- Niesklasyfikowane Holland Electronics
- Niesklasyfikowane Arista
- Niesklasyfikowane Triumph Sports
- Niesklasyfikowane Gasmate
- Niesklasyfikowane Crelando
- Niesklasyfikowane Novo Nordisk
- Niesklasyfikowane Seville Classics
- Niesklasyfikowane TechLogix Networx
- Niesklasyfikowane Thermalright
- Niesklasyfikowane Bxterra
- Niesklasyfikowane Bea-fon
- Niesklasyfikowane Babylonia
- Niesklasyfikowane HeartSine
- Niesklasyfikowane Bullet
- Niesklasyfikowane Morrison
- Niesklasyfikowane Ordo
- Niesklasyfikowane Alphacool
- Niesklasyfikowane Asetek
- Niesklasyfikowane AZZA
- Niesklasyfikowane Audibax
- Niesklasyfikowane TechN
- Niesklasyfikowane Davita
- Niesklasyfikowane Giga Copper
- Niesklasyfikowane Elsner
- Niesklasyfikowane Séura
- Niesklasyfikowane Cube Controls
- Niesklasyfikowane Meridian
- Niesklasyfikowane Donexon
- Niesklasyfikowane Linq
- Niesklasyfikowane Wortmann AG
- Niesklasyfikowane DiGiGrid
- Niesklasyfikowane Sanofi
- Niesklasyfikowane Mitzu
- Niesklasyfikowane Avteq
- Niesklasyfikowane Fizzics
- Niesklasyfikowane XFX
- Niesklasyfikowane Leynew
- Niesklasyfikowane Lauten Audio
- Niesklasyfikowane Cropico
- Niesklasyfikowane Sunwoda
- Niesklasyfikowane Schleich
- Niesklasyfikowane Unitech
- Niesklasyfikowane FXLab
- Niesklasyfikowane Middle Atlantic
- Niesklasyfikowane Kincrome
- Niesklasyfikowane Brockhaus HEUER
- Niesklasyfikowane Reishunger
- Niesklasyfikowane Ergotec
- Niesklasyfikowane Dupla
- Niesklasyfikowane APSystems
- Niesklasyfikowane IODD
- Niesklasyfikowane BYD
- Niesklasyfikowane Aqua Medic
- Niesklasyfikowane Pylontech
- Niesklasyfikowane Fire Sense
- Niesklasyfikowane Grüniq
- Niesklasyfikowane Goodwe
- Niesklasyfikowane Moki
- Niesklasyfikowane Enertex
- Niesklasyfikowane Ovation
- Niesklasyfikowane Enviroswim
- Niesklasyfikowane Dobar
- Niesklasyfikowane Vevor
- Niesklasyfikowane Ovente
- Niesklasyfikowane PowerColor
- Niesklasyfikowane ISpring
- Niesklasyfikowane WeFix
- Niesklasyfikowane BCA
- Niesklasyfikowane Saki
- Niesklasyfikowane Smart365
- Niesklasyfikowane ChargeHub
- Niesklasyfikowane Eldat
- Niesklasyfikowane SoundSwitch
- Niesklasyfikowane Dostmann Electronic
- Niesklasyfikowane JBC
- Niesklasyfikowane DV Mark
- Niesklasyfikowane MOON
- Niesklasyfikowane Cuggl
- Niesklasyfikowane HABAU
- Niesklasyfikowane CVW
- Niesklasyfikowane Earbreeze
- Niesklasyfikowane Möhlenhoff
- Niesklasyfikowane Taqua
- Niesklasyfikowane Brainstorm
- Niesklasyfikowane Colonial Elegance
- Niesklasyfikowane Overtone Labs
- Niesklasyfikowane Bühnen
- Niesklasyfikowane Blukac
- Niesklasyfikowane BendixKing
- Niesklasyfikowane Tube-Tech
- Niesklasyfikowane TCW Technologies
- Niesklasyfikowane UNITEK
- Niesklasyfikowane CoolerMaster
- Niesklasyfikowane Rexing
- Niesklasyfikowane The T.mix
- Niesklasyfikowane Regula-Werk King
- Niesklasyfikowane MIDI Solutions
- Niesklasyfikowane Positive Grid
- Niesklasyfikowane Amgrow
- Niesklasyfikowane Xaphoon
- Niesklasyfikowane Winchester
- Niesklasyfikowane Lampa
- Niesklasyfikowane Sinus Live
- Niesklasyfikowane Sureguard
- Niesklasyfikowane QuickCool
- Niesklasyfikowane Smit Visual
- Niesklasyfikowane NZR
- Niesklasyfikowane Toparc
- Niesklasyfikowane Oro-Med
- Niesklasyfikowane Hex
- Niesklasyfikowane Baby Cakes
- Niesklasyfikowane Deflecto
- Niesklasyfikowane ELMEKO
- Niesklasyfikowane Tesseract Modular
- Niesklasyfikowane Sport Dog
- Niesklasyfikowane Nowsonic
- Niesklasyfikowane On Air
- Niesklasyfikowane Acoustic Solutions
- Niesklasyfikowane Hubble Connected
- Niesklasyfikowane ELTA Music
- Niesklasyfikowane Dragonshock
- Niesklasyfikowane We-Vibe
- Niesklasyfikowane Electronics International
- Niesklasyfikowane Lamar
- Niesklasyfikowane Atlantis Land
- Niesklasyfikowane White Lightning
- Niesklasyfikowane GEV
- Niesklasyfikowane Frient
- Niesklasyfikowane Kaiser Fototechnik
- Niesklasyfikowane Vishay
- Niesklasyfikowane Rooboost
- Niesklasyfikowane Bitspower
- Niesklasyfikowane Comar
- Niesklasyfikowane Freedor
- Niesklasyfikowane Start International
- Niesklasyfikowane AXITEC
- Niesklasyfikowane Lingg & Janke
- Niesklasyfikowane Auralex
- Niesklasyfikowane Pieps
- Niesklasyfikowane Innovative
- Niesklasyfikowane Lynx Technik
- Niesklasyfikowane Yuede
- Niesklasyfikowane ClimeMET
- Niesklasyfikowane Pliant Technologies
- Niesklasyfikowane Prompter People
- Niesklasyfikowane Astropet
- Niesklasyfikowane Canopia
- Niesklasyfikowane Wabeco
- Niesklasyfikowane Swingline GBC
- Niesklasyfikowane Staudte-Hirsch
- Niesklasyfikowane Universal Remote Control
- Niesklasyfikowane Lantronix
- Niesklasyfikowane Kino Flo
- Niesklasyfikowane Aqua Computer
- Niesklasyfikowane HEDD
- Niesklasyfikowane Vinpower Digital
- Niesklasyfikowane Lindemann
- Niesklasyfikowane Silent Angel
- Niesklasyfikowane Club 3D
- Niesklasyfikowane Sprolink
- Niesklasyfikowane Thermionic Culture
- Niesklasyfikowane Watercool
- Niesklasyfikowane Moultrie
- Niesklasyfikowane Skaarhoj
- Niesklasyfikowane Whitestone
- Niesklasyfikowane BMB
- Niesklasyfikowane Cloud
- Niesklasyfikowane Sandia Aerospace
- Niesklasyfikowane EK Water Blocks
- Niesklasyfikowane Lamptron
- Niesklasyfikowane Gudsen
- Niesklasyfikowane Zendure
- Niesklasyfikowane Envertech
- Niesklasyfikowane Prism Sound
- Niesklasyfikowane MoFi
- Niesklasyfikowane ID-Tech
- Niesklasyfikowane FSP/Fortron
- Niesklasyfikowane IDIS
- Niesklasyfikowane Fixpoint
- Niesklasyfikowane Enerdrive
- Niesklasyfikowane Respironics
- Niesklasyfikowane TESLA Electronics
- Niesklasyfikowane Intesis
- Niesklasyfikowane Nethix
- Niesklasyfikowane Pluto
- Niesklasyfikowane Laine
- Niesklasyfikowane 3Doodler
- Niesklasyfikowane Middle Atlantic Products
- Niesklasyfikowane Doepke
- Niesklasyfikowane Loctite
- Niesklasyfikowane Antelope
- Niesklasyfikowane Astera
- Niesklasyfikowane Polyend
- Niesklasyfikowane Sabco
- Niesklasyfikowane Sensative
- Niesklasyfikowane Plasma Cloud
- Niesklasyfikowane Flo
- Niesklasyfikowane Sheeran Looper
- Niesklasyfikowane Applico
- Niesklasyfikowane Jungle Gym
- Niesklasyfikowane Smart Media
- Niesklasyfikowane Code
- Niesklasyfikowane Mivar
- Niesklasyfikowane The Joy Factory
- Niesklasyfikowane Veber
- Niesklasyfikowane Edwards
- Niesklasyfikowane Grand Effects
- Niesklasyfikowane SunPower
- Niesklasyfikowane Westland
- Niesklasyfikowane Black Line
- Niesklasyfikowane Enbrighten
- Niesklasyfikowane Albert Heijn
- Niesklasyfikowane Yphix
- Niesklasyfikowane TAURUS Titanium
- Niesklasyfikowane Magliner
- Niesklasyfikowane Comfortisse
- Niesklasyfikowane Cayin
- Niesklasyfikowane Videotel Digital
- Niesklasyfikowane Zylight
- Niesklasyfikowane Smith-Victor
- Niesklasyfikowane HuddleCamHD
- Niesklasyfikowane MooreCo
- Niesklasyfikowane BIOS Living
- Niesklasyfikowane Connection
- Niesklasyfikowane Blind Spot
- Niesklasyfikowane Badiona
- Niesklasyfikowane VMV
- Niesklasyfikowane Telmax
- Niesklasyfikowane Exelpet
- Niesklasyfikowane Aplic
- Niesklasyfikowane Imarflex
- Niesklasyfikowane Tempmate
- Niesklasyfikowane Stalco
- Niesklasyfikowane Carlsbro
- Niesklasyfikowane Ventev
- Niesklasyfikowane Mobotix
- Niesklasyfikowane Steelbody
- Niesklasyfikowane PureLink
- Niesklasyfikowane UNYKAch
- Niesklasyfikowane VAVA
- Niesklasyfikowane Mammut
- Niesklasyfikowane Modbap Modular
- Niesklasyfikowane Bluestork
- Niesklasyfikowane INOGENI
- Niesklasyfikowane Carry-on
- Niesklasyfikowane AddLiving
- Niesklasyfikowane IOIO
- Niesklasyfikowane Nimbus
- Niesklasyfikowane Coca-Cola
- Niesklasyfikowane City Theatrical
- Niesklasyfikowane Acros
- Niesklasyfikowane Redback Technologies
- Niesklasyfikowane Vent-A-Hood
- Niesklasyfikowane GoXtreme
- Niesklasyfikowane Bome
- Niesklasyfikowane One Control
- Niesklasyfikowane EQ Acoustics
- Niesklasyfikowane AV Tool
- Niesklasyfikowane Aquael
- Niesklasyfikowane NEXTO DI
- Niesklasyfikowane Thermarest
- Niesklasyfikowane Fortinge
- Niesklasyfikowane RF-Links
- Niesklasyfikowane LiveU
- Niesklasyfikowane Austral
- Niesklasyfikowane Luxul
- Niesklasyfikowane Cherub
- Niesklasyfikowane ProLights
- Niesklasyfikowane Xinfrared
- Niesklasyfikowane Brizo
- Niesklasyfikowane Europalms
- Niesklasyfikowane DuroStar
- Niesklasyfikowane Waterstone
- Niesklasyfikowane Huslog
- Niesklasyfikowane Mr Steam
- Niesklasyfikowane DVDO
- Niesklasyfikowane A-Designs
- Niesklasyfikowane Henry Engineering
- Niesklasyfikowane Primacoustic
- Niesklasyfikowane HomeCraft
- Niesklasyfikowane Heusinkveld
- Niesklasyfikowane EnOcean
- Niesklasyfikowane Storcube
- Niesklasyfikowane Varia
- Niesklasyfikowane Gurari
- Niesklasyfikowane Fezz
- Niesklasyfikowane ASI
- Niesklasyfikowane Lexivon
- Niesklasyfikowane Swiss Eye
- Niesklasyfikowane Cane Creek
- Niesklasyfikowane EPEVER
- Niesklasyfikowane KED
- Niesklasyfikowane Caberg
- Niesklasyfikowane Exped
- Niesklasyfikowane Lawn Star
- Niesklasyfikowane Edouard Rousseau
- Niesklasyfikowane GameDay
- Niesklasyfikowane Sparkle
- Niesklasyfikowane Söll
- Niesklasyfikowane X-Lite
- Niesklasyfikowane AXESS
- Niesklasyfikowane Glemm
- Niesklasyfikowane Ridem
- Niesklasyfikowane StarIink
- Niesklasyfikowane Noyafa
- Niesklasyfikowane Envertec
- Niesklasyfikowane Nordic Winter
- Niesklasyfikowane Volcano
- Niesklasyfikowane Wire Technologies
- Niesklasyfikowane Taco Tuesday
- Niesklasyfikowane CEEM
- Niesklasyfikowane IMM Photonics
- Niesklasyfikowane Field Optics
- Niesklasyfikowane Robern
- Niesklasyfikowane Signature Hardware
- Niesklasyfikowane GRAUGEAR
- Niesklasyfikowane Sure Petcare
- Niesklasyfikowane Sortimo
- Niesklasyfikowane Livall
- Niesklasyfikowane Beaphar
- Niesklasyfikowane Catit
- Niesklasyfikowane WarmlyYours
- Niesklasyfikowane Mebby
- Niesklasyfikowane TONI&GUY
- Niesklasyfikowane Balam Rush
- Niesklasyfikowane Roesle
- Niesklasyfikowane Oreg
- Niesklasyfikowane Karran
- Niesklasyfikowane OOONO
- Niesklasyfikowane CaviLock
- Niesklasyfikowane Origin Storage
- Niesklasyfikowane Kostal
- Niesklasyfikowane Stamos
- Niesklasyfikowane Ulsonix
- Niesklasyfikowane Stamony
- Niesklasyfikowane Uniprodo
- Niesklasyfikowane Triplett
- Niesklasyfikowane RC Allen
- Niesklasyfikowane Bulgin
- Niesklasyfikowane Pure 100
- Niesklasyfikowane STANDARD
- Niesklasyfikowane BigBlue
- Niesklasyfikowane Plastkon
- Niesklasyfikowane Tele Vue
- Niesklasyfikowane Wiesenfield
- Niesklasyfikowane Ferrofish
- Niesklasyfikowane Luxli
- Niesklasyfikowane Blonder Tongue
- Niesklasyfikowane Crystal Video
- Niesklasyfikowane HPRC
- Niesklasyfikowane Platypus
- Niesklasyfikowane Petite Chérie
- Niesklasyfikowane Njoy
- Niesklasyfikowane Studio Titan
- Niesklasyfikowane AstrHori
- Niesklasyfikowane Icron
- Niesklasyfikowane Pyrex
- Niesklasyfikowane ProFlo
- Niesklasyfikowane Trezor
- Niesklasyfikowane Yamazen
- Niesklasyfikowane Really Right Stuff
- Niesklasyfikowane Decimator
- Niesklasyfikowane Chimera
- Niesklasyfikowane ButtKicker
- Niesklasyfikowane Tilta
- Niesklasyfikowane PAG
- Niesklasyfikowane NeoMounts
- Niesklasyfikowane Western Co.
- Niesklasyfikowane Ruggard
- Niesklasyfikowane DiversiTech
- Niesklasyfikowane Violectric
- Niesklasyfikowane Aalberg Audio
- Niesklasyfikowane OM SYSTEM
- Niesklasyfikowane PoLabs
- Niesklasyfikowane Bolin Technology
- Niesklasyfikowane Taiji
- Niesklasyfikowane Total Chef
- Niesklasyfikowane Evooch
- Niesklasyfikowane Total
- Niesklasyfikowane Kolcraft
- Niesklasyfikowane Fellow
- Niesklasyfikowane Digi-Pas
- Niesklasyfikowane Klauke
- Niesklasyfikowane Axler
- Niesklasyfikowane Pfister
- Niesklasyfikowane Symmons
- Niesklasyfikowane Gerber
- Niesklasyfikowane Royale
- Niesklasyfikowane Venicci
- Niesklasyfikowane Das Keyboard
- Niesklasyfikowane Schaffner
- Niesklasyfikowane Vitec
- Niesklasyfikowane Nicols
- Niesklasyfikowane Matterport
- Niesklasyfikowane Physa
- Niesklasyfikowane ARNOLD Lichttechnik
- Niesklasyfikowane Moomin
- Niesklasyfikowane Belulu
- Niesklasyfikowane Jedo
- Niesklasyfikowane Bayco
- Niesklasyfikowane Dinstar
- Niesklasyfikowane Noordi
- Niesklasyfikowane Corona
- Niesklasyfikowane Coors Light
- Niesklasyfikowane Arco
- Niesklasyfikowane KoolScapes
- Niesklasyfikowane Netter Vibration
- Niesklasyfikowane Califone
- Niesklasyfikowane Dynon Avionics
- Niesklasyfikowane Uvex
- Niesklasyfikowane UAvionix
- Niesklasyfikowane LARQ
- Niesklasyfikowane ORCA
- Niesklasyfikowane YA-MAN
- Niesklasyfikowane CRAFT + MAIN
- Niesklasyfikowane V-Tone
- Niesklasyfikowane Hellberg
- Niesklasyfikowane Stelzner
- Niesklasyfikowane LightKeeper Pro
- Niesklasyfikowane Cressi
- Niesklasyfikowane Singercon
- Niesklasyfikowane BMAX
- Niesklasyfikowane Pivo
- Niesklasyfikowane Sharkbite
- Niesklasyfikowane CatSynth
- Niesklasyfikowane Lantus
- Niesklasyfikowane Pitsos
- Niesklasyfikowane Lively
- Niesklasyfikowane Ember
- Niesklasyfikowane ACOPower
- Niesklasyfikowane Sifflus
Najnowsze instrukcje dla Niesklasyfikowane

15 Stycznia 2025

15 Stycznia 2025

15 Stycznia 2025

15 Stycznia 2025

15 Stycznia 2025

15 Stycznia 2025

15 Stycznia 2025

15 Stycznia 2025

15 Stycznia 2025

15 Stycznia 2025