Instrukcja obsługi Microchip HV9982DB1
Microchip
nieskategoryzowany
HV9982DB1
Przeczytaj poniżej 📖 instrukcję obsługi w języku polskim dla Microchip HV9982DB1 (11 stron) w kategorii nieskategoryzowany. Ta instrukcja była pomocna dla 17 osób i została oceniona przez 2 użytkowników na średnio 4.5 gwiazdek
Strona 1/11
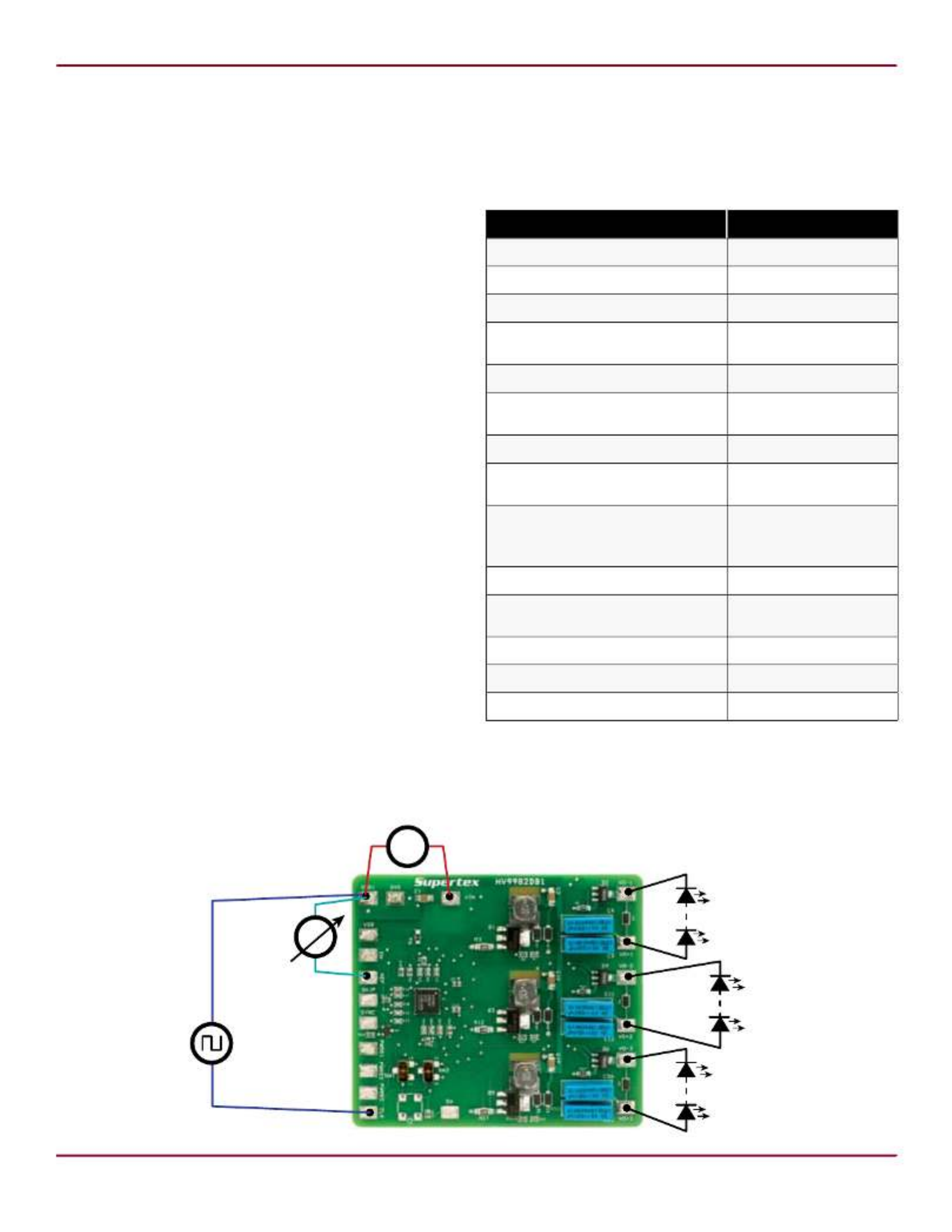
Supertex inc.
Supertex inc.
www.supertex.com
HV9982DB1
Doc.# DSDB-HV9982DB1
A032913
General Description
The HV9982DB1 is a three channel boost LED driver
demoboard using Supertex’s HV9982 LED Driver IC. The
LED driver can be used to drive RGB or multi channel
white LEDs from a 24V input. The LED string current can
be adjusted up to a maximum of 100mA. The demoboard
has good current matching between strings and an excellent
PWM dimming response, making it ideal for LED backlight
applications.
The HV9982DB1 uses the HV9982 LED driver IC to drive
three discontinuous conduction mode boost converters
at a 500kHz switching frequency. The clocks of the three
channels are phase shifted to provide ripple cancellation at
the input and thus reducing the input capacitor requirements.
The output current level can be adjusted using an external
voltage source at the REF terminal.
The HV9982DB1 includes hiccup mode protection for both
short circuit and open circuit conditions to ensure that it
recovers from a momentary fault condition. It also enables
the board to survive prolonged fault conditions without any
damage to both the driver as well as the LEDs.
The HV9982DB1 also includes an on-board PWM generator
for analog control for PWM dimming (for backward
compatibility with CCFL controllers). This feature enables
the user to PWM dim the driver with a 0 - 2.0V analog signal
input and helps to achieve zero LED current with an analog
dimming input
Connection Diagram
Three Channel
LED Driver Demoboard
Specications
Parameter Value
Input voltage 24V ± 10%
LED string voltage (all channels) 35V – 80V
LED current (all channels) 100mA (max)
Switching frequency of the
converter at FCLK = 6.0MHz 500kHz
External frequency at CLK pin 6MHz
Current matching between
channels ≤ ± 3%
Typical full load efciency 90%
PWM dimming
rise and fall times ≤1μs
PWM dimming frequency
(for analog control of PWM
dimming)
480Hz (typ)
Shutdown mode current ≤ 600μA
Typical IDD current
(for all three channels) 12mA (VDD = 8V)
Open LED drotection Included; hiccup-mode
Output short circuit protection Included; hiccup-mode
Hiccup time 1ms (typ)
24V DC source
0 - 0.5V
DC source
6MHz clock
(TTL compatible)
- +
+
-
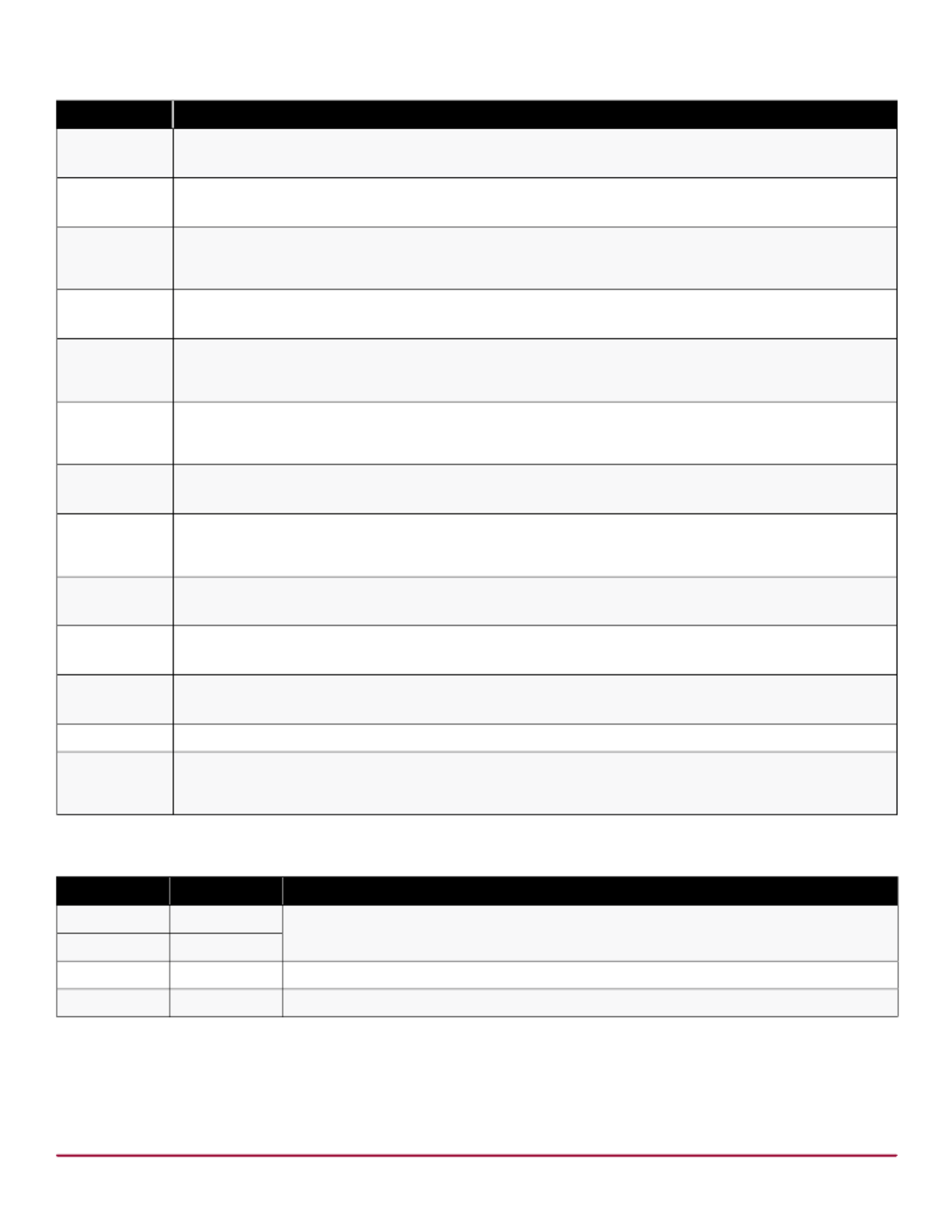
2
HV9982DB1
Supertex inc.
www.supertex.com
Doc.# DSDB-HV9982DB1
A032913
Connections
Pin Connection
VIN This terminal is the positive input of the 24V supply for the boost converters. It is also the input for the
internal regulator of the IC.
GND, GND1 These terminals are the return paths for all the input voltages and signals for the demoboard. All voltages
and signals (other than the output terminals) should be referenced to these two terminals.
VDD
This terminal is connected to the VDD pins of the IC. When left unconnected, the voltage at this terminal
will be regulated to 7.75V by the internal regulator of the HV9982. To supply the IC with an external VDD
supply, connect an 8-10V source to this terminal.
EN This terminal can be used to shut down the IC. Connecting this terminal to GND will cause the IC to go
into a standby mode and draw less than 500μA.
CLK
This terminal is the clock input to the IC. A TTL compatible 6MHz clock should be connected to this ter-
minal. In case an on-board clock is preferred, a 6MHz xed frequency oscillator can be soldered in at U2
(please refer to BOM for the part number).
5V
A 5.0V, 50mA source needs to be connected to this point, if an on-board clock is used. This provides
the power required for the xed frequency oscillator at U2. This terminal can be left open if an external
6.0MHz clock is used.
REF This terminal is the control input for adjusting the LED current level. A 0 – 500mV voltage source should
be connected to this terminal.
S1, S2
These two switches on the demoboard control the PWM dimming function. They can be used to enable
either direct PWM dimming of the channels using an external TTL signal or analog control of PWM dim-
ming using a 0-2.0V analog signal. The control logic for these switches is given in Table 1.
PWMD1-3 These terminals are the PWM dimming inputs. The inputs can be either TTL compatible square wave
signals or 0-2.0V analog signals depending on the conguration of switches S1 and S2.
VO+1-3 The anodes of the LED strings should be connected to these terminals as shown in the connection dia-
gram.
VO- 1-3 The cathodes of the LED strings should be connected to these terminals as shown in the connection
diagram.
SKIP This terminal is connected to the hiccup timing capacitor and can be used to measure the hiccup time.
SYNC
This terminal can be used to synchronize the internal PWM ramp to an external clock. A TTL compatible,
350 – 400Hz external clock with a pulse width less than 2% can be applied at this terminal to synchronize
the internal ramp to the external clock.
Table 1 : Truth Table for S1 and S2
S1 S2 PWMD Output
LO LO The output will follow PWMD input signal
LO HI
HI LO Input DC zero volt corresponds to 100% duty cycle output
HI HI Input DC two volt corresponds to 100% duty cycle output
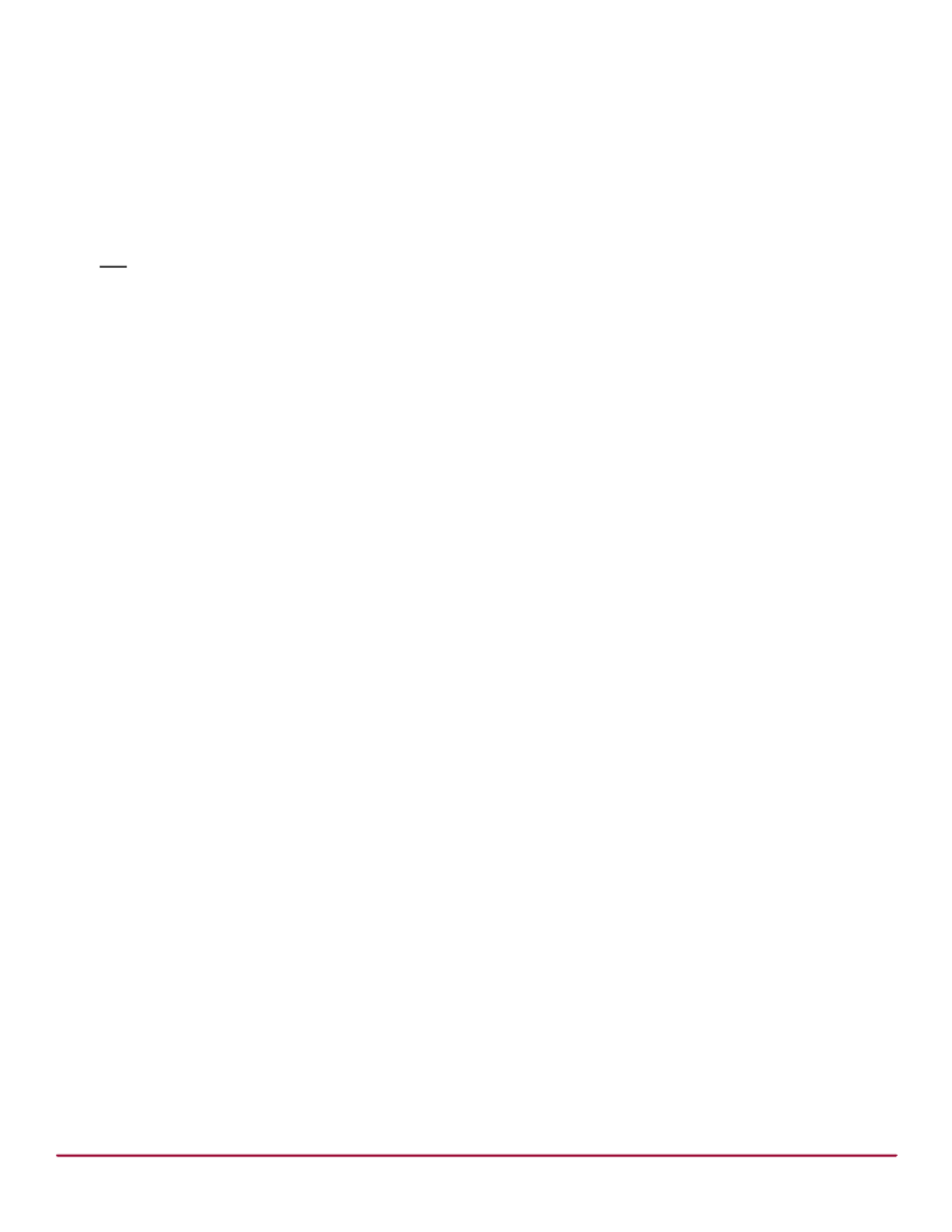
3
HV9982DB1
Supertex inc.
www.supertex.com
Doc.# DSDB-HV9982DB1
A032913
Normal Operation – Connect the board as shown in the
connection diagram. Ensure that switches S1 and S2 are
LO. Turn on the clock, 24V supply and the reference volt-
age. Connect any of the PWMD pins to VDD. The LEDs of
the corresponding channel will light up. Measure the LED
current using an ammeter and the reference voltage using a
voltmeter. The current will be:
ILED = VREF ± 3.0%
4.99
(1)
Current matching – Without changing the reference volt-
age, enable each channel individually and measure the cur-
rent (or, if possible, enable all channels and the three output
currents simultaneously). The error will be ≤ ± 3%.
Linear Dimming – Vary the reference voltage between 0
– 500mV and measure the LED current.
The current will vary as per Eqn.1. This variation is fairly lin-
ear until the REF voltage gets very low. As the voltage goes
below 50mV, the current will not match the reference voltage
as linearly.
PWM Dimming – With the reference voltage xed at 0.5V,
apply a TTL compatible square wave signal (≤1kHz). The
LED current will dim based on the duty cycle of the PWM
input.
Analog Control of PWM Dimming – Change S1 and S2 as
required using Table 1. Connect the analog 0-2V source at
the PWMD terminal and turn on the demoboard. The LEDs
will dim and the LED current can be adjusted by varying the
analog voltage.
Open LED protection – Connect a voltage probe between
the VO+ terminal of any channel and GND and disconnect
the LED string. The output voltage will rise up to 92V and
trip the over voltage protection. At this point, all three chan-
nels will shut down and the output voltage of the channel
with the open LED condition will be maintained hysteretically
between 92V and 82V until the output voltage of the fauly
channel falls below 82V or till the LED string is reconnected.
Once the LED string is reconnected, all three channels will
turn back on.
Short Circuit Protection – Short the output terminals of any
one channel using a jumper. All three channels shut down
and the IC tries restarting every 1.0ms. Once the short circuit
is removed, all three channels come back into regulation.
Testing the Demoboard
Specyfikacje produktu
Marka: | Microchip |
Kategoria: | nieskategoryzowany |
Model: | HV9982DB1 |
Potrzebujesz pomocy?
Jeśli potrzebujesz pomocy z Microchip HV9982DB1, zadaj pytanie poniżej, a inni użytkownicy Ci odpowiedzą
Instrukcje nieskategoryzowany Microchip

5 Lipca 2024

5 Lipca 2024

5 Lipca 2024

5 Lipca 2024

5 Lipca 2024

5 Lipca 2024

5 Lipca 2024

5 Lipca 2024

5 Lipca 2024

5 Lipca 2024
Instrukcje nieskategoryzowany
- nieskategoryzowany Sony
- nieskategoryzowany Bauknecht
- nieskategoryzowany Yamaha
- nieskategoryzowany Ikea
- nieskategoryzowany Hoshizaki
- nieskategoryzowany Samsung
- nieskategoryzowany Tesy
- nieskategoryzowany PeakTech
- nieskategoryzowany Bertazzoni
- nieskategoryzowany Electrolux
- nieskategoryzowany Gamdias
- nieskategoryzowany Tenda
- nieskategoryzowany DeLonghi
- nieskategoryzowany AEG
- nieskategoryzowany Fellowes
- nieskategoryzowany Balay
- nieskategoryzowany Leica
- nieskategoryzowany Beko
- nieskategoryzowany Teka
- nieskategoryzowany Sven
- nieskategoryzowany ChamSys
- nieskategoryzowany LG
- nieskategoryzowany Worx
- nieskategoryzowany Küppersbusch
- nieskategoryzowany Smeg
- nieskategoryzowany Motorola
- nieskategoryzowany Götze & Jensen
- nieskategoryzowany Dreame
- nieskategoryzowany Beurer
- nieskategoryzowany Stabo
- nieskategoryzowany Logitech
- nieskategoryzowany Gram
- nieskategoryzowany Spektrum
- nieskategoryzowany Xiaomi
- nieskategoryzowany Gorenje
- nieskategoryzowany Etna
- nieskategoryzowany Joy-It
- nieskategoryzowany LERAN
- nieskategoryzowany President
- nieskategoryzowany MyPhone
- nieskategoryzowany Sharp
- nieskategoryzowany BeamZ
- nieskategoryzowany Huawei
- nieskategoryzowany Supermicro
- nieskategoryzowany TCL
- nieskategoryzowany Braun
- nieskategoryzowany Russell Hobbs
- nieskategoryzowany Pioneer
- nieskategoryzowany Statron
- nieskategoryzowany Sage
- nieskategoryzowany Lenovo
- nieskategoryzowany Tefal
- nieskategoryzowany Honda
- nieskategoryzowany TP-Link
- nieskategoryzowany Voltcraft
- nieskategoryzowany Milwaukee
- nieskategoryzowany Philips
- nieskategoryzowany Livoo
- nieskategoryzowany SilverCrest
- nieskategoryzowany Simpson
- nieskategoryzowany Dometic
- nieskategoryzowany Gigabyte
- nieskategoryzowany Acer
- nieskategoryzowany Realme
- nieskategoryzowany Ultimate Speed
- nieskategoryzowany Stihl
- nieskategoryzowany Bosch
- nieskategoryzowany Yato
- nieskategoryzowany Xblitz
- nieskategoryzowany Epson
- nieskategoryzowany JBL
- nieskategoryzowany Parkside
- nieskategoryzowany Hikvision
- nieskategoryzowany Candy
- nieskategoryzowany GW Instek
- nieskategoryzowany Onkyo
- nieskategoryzowany Whirlpool
- nieskategoryzowany Grillmeister
- nieskategoryzowany IPGARD
- nieskategoryzowany Fujitsu
- nieskategoryzowany Ferroli
- nieskategoryzowany Thule
- nieskategoryzowany Roland
- nieskategoryzowany Miele
- nieskategoryzowany HyperX
- nieskategoryzowany Easy Home
- nieskategoryzowany LC-Power
- nieskategoryzowany Waterco
- nieskategoryzowany Geemarc
- nieskategoryzowany Scott
- nieskategoryzowany Brentwood
- nieskategoryzowany Midea
- nieskategoryzowany KEF
- nieskategoryzowany Festool
- nieskategoryzowany Kärcher
- nieskategoryzowany Bose
- nieskategoryzowany Severin
- nieskategoryzowany Hisense
- nieskategoryzowany Berg
- nieskategoryzowany Infiniton
- nieskategoryzowany EZVIZ
- nieskategoryzowany Conceptronic
- nieskategoryzowany Panasonic
- nieskategoryzowany StarTech.com
- nieskategoryzowany Promethean
- nieskategoryzowany Bavaria By Einhell
- nieskategoryzowany Theben
- nieskategoryzowany Liebherr
- nieskategoryzowany Canon
- nieskategoryzowany Mio
- nieskategoryzowany Crestron
- nieskategoryzowany Truetone
- nieskategoryzowany Bestway
- nieskategoryzowany Viewsonic
- nieskategoryzowany Behringer
- nieskategoryzowany Asus
- nieskategoryzowany Nedis
- nieskategoryzowany Stanley
- nieskategoryzowany Nexa
- nieskategoryzowany Jura
- nieskategoryzowany AG Neovo
- nieskategoryzowany Be Cool
- nieskategoryzowany Allen & Heath
- nieskategoryzowany Enphase
- nieskategoryzowany IK Multimedia
- nieskategoryzowany Reolink
- nieskategoryzowany American DJ
- nieskategoryzowany Medion
- nieskategoryzowany Tangent
- nieskategoryzowany Boss
- nieskategoryzowany Black & Decker
- nieskategoryzowany OK
- nieskategoryzowany Lenco
- nieskategoryzowany TRENDnet
- nieskategoryzowany Audioline
- nieskategoryzowany Max Pro
- nieskategoryzowany Scheppach
- nieskategoryzowany Fujifilm
- nieskategoryzowany Proxxon
- nieskategoryzowany Adler
- nieskategoryzowany Bluetti
- nieskategoryzowany BaByliss
- nieskategoryzowany Marquant
- nieskategoryzowany Subaru
- nieskategoryzowany MSI
- nieskategoryzowany Hoover
- nieskategoryzowany Tesla
- nieskategoryzowany Westinghouse
- nieskategoryzowany D-Link
- nieskategoryzowany Hendi
- nieskategoryzowany Jensen
- nieskategoryzowany Niceboy
- nieskategoryzowany Hazet
- nieskategoryzowany Vertiv
- nieskategoryzowany Conair
- nieskategoryzowany GE
- nieskategoryzowany ILive
- nieskategoryzowany Ardes
- nieskategoryzowany Taurus
- nieskategoryzowany VitalMaxx
- nieskategoryzowany RIKON
- nieskategoryzowany Ring
- nieskategoryzowany Orbegozo
- nieskategoryzowany Native Instruments
- nieskategoryzowany Garmin
- nieskategoryzowany Blaupunkt
- nieskategoryzowany Vivax
- nieskategoryzowany ATen
- nieskategoryzowany IOptron
- nieskategoryzowany Grizzly
- nieskategoryzowany Salora
- nieskategoryzowany Siemens
- nieskategoryzowany Teac
- nieskategoryzowany Speed-Link
- nieskategoryzowany Casio
- nieskategoryzowany Iiyama
- nieskategoryzowany Lincoln Electric
- nieskategoryzowany Metra
- nieskategoryzowany Thrustmaster
- nieskategoryzowany Evolveo
- nieskategoryzowany Ambiano
- nieskategoryzowany DeWalt
- nieskategoryzowany Bbf
- nieskategoryzowany Danby
- nieskategoryzowany Martin Logan
- nieskategoryzowany Dual
- nieskategoryzowany Einhell
- nieskategoryzowany Grundig
- nieskategoryzowany APC
- nieskategoryzowany Hegel
- nieskategoryzowany Kiloview
- nieskategoryzowany Haier
- nieskategoryzowany Sigma
- nieskategoryzowany Homedics
- nieskategoryzowany Remington
- nieskategoryzowany HP
- nieskategoryzowany KKT Kolbe
- nieskategoryzowany Cylinda
- nieskategoryzowany S.M.S.L
- nieskategoryzowany Genesis
- nieskategoryzowany Jocel
- nieskategoryzowany Soundmaster
- nieskategoryzowany Hyundai
- nieskategoryzowany Silverline
- nieskategoryzowany Blomberg
- nieskategoryzowany Line 6
- nieskategoryzowany Husqvarna
- nieskategoryzowany Honeywell
- nieskategoryzowany BLOW
- nieskategoryzowany DAP-Audio
- nieskategoryzowany Concept
- nieskategoryzowany Joie
- nieskategoryzowany Manhattan
- nieskategoryzowany Chauvet
- nieskategoryzowany Heritage Audio
- nieskategoryzowany Fisher & Paykel
- nieskategoryzowany Angelcare
- nieskategoryzowany Cotek
- nieskategoryzowany Durvet
- nieskategoryzowany Tripp Lite
- nieskategoryzowany Shure
- nieskategoryzowany EWON
- nieskategoryzowany ECG
- nieskategoryzowany IRobot
- nieskategoryzowany Indesit
- nieskategoryzowany Matsui
- nieskategoryzowany Amazfit
- nieskategoryzowany Steinel
- nieskategoryzowany Makita
- nieskategoryzowany Ilve
- nieskategoryzowany Mikrotik
- nieskategoryzowany Denon
- nieskategoryzowany Akasa
- nieskategoryzowany Perkins
- nieskategoryzowany Swann
- nieskategoryzowany Truma
- nieskategoryzowany Kwikset
- nieskategoryzowany Mercury
- nieskategoryzowany Empress Effects
- nieskategoryzowany Carel
- nieskategoryzowany Nikon
- nieskategoryzowany Shimano
- nieskategoryzowany Viking
- nieskategoryzowany Antari
- nieskategoryzowany Medela
- nieskategoryzowany Block
- nieskategoryzowany Ozito
- nieskategoryzowany Kodak
- nieskategoryzowany Phoenix Gold
- nieskategoryzowany Forza
- nieskategoryzowany CATA
- nieskategoryzowany Testo
- nieskategoryzowany Audac
- nieskategoryzowany Cisco
- nieskategoryzowany Revic
- nieskategoryzowany Primera
- nieskategoryzowany Draper
- nieskategoryzowany Aim TTi
- nieskategoryzowany Fuxtec
- nieskategoryzowany ORNO
- nieskategoryzowany Cooler Master
- nieskategoryzowany Sanus
- nieskategoryzowany TFA
- nieskategoryzowany Dyson
- nieskategoryzowany Chauvin Arnoux
- nieskategoryzowany Hotpoint
- nieskategoryzowany Kenwood
- nieskategoryzowany Scosche
- nieskategoryzowany Icy Box
- nieskategoryzowany Sungrow
- nieskategoryzowany NuPrime
- nieskategoryzowany Hasbro
- nieskategoryzowany Moxa
- nieskategoryzowany Trisa
- nieskategoryzowany DJI
- nieskategoryzowany RYOBI
- nieskategoryzowany Kugoo
- nieskategoryzowany Alpine
- nieskategoryzowany Wolf Garten
- nieskategoryzowany Knog
- nieskategoryzowany Gembird
- nieskategoryzowany Scala
- nieskategoryzowany ZTE
- nieskategoryzowany Godox
- nieskategoryzowany Røde
- nieskategoryzowany Zelmer
- nieskategoryzowany Hammersmith
- nieskategoryzowany Chicco
- nieskategoryzowany Chamberlain
- nieskategoryzowany Paradigm
- nieskategoryzowany Lindy
- nieskategoryzowany Olivetti
- nieskategoryzowany Ninja
- nieskategoryzowany Medisana
- nieskategoryzowany Minox
- nieskategoryzowany Cuisinart
- nieskategoryzowany Zebra
- nieskategoryzowany Wilfa
- nieskategoryzowany DSC
- nieskategoryzowany Cobra
- nieskategoryzowany JVC
- nieskategoryzowany ZyXEL
- nieskategoryzowany Auriol
- nieskategoryzowany Konig & Meyer
- nieskategoryzowany Trust
- nieskategoryzowany BLUEPALM
- nieskategoryzowany V7
- nieskategoryzowany Thor
- nieskategoryzowany LogiLink
- nieskategoryzowany Handy
- nieskategoryzowany Memphis Audio
- nieskategoryzowany Sandisk
- nieskategoryzowany Grohe
- nieskategoryzowany Dell
- nieskategoryzowany Polaris
- nieskategoryzowany GLORIA
- nieskategoryzowany IFM
- nieskategoryzowany Krups
- nieskategoryzowany Furrion
- nieskategoryzowany U-Line
- nieskategoryzowany Linksys
- nieskategoryzowany Moulinex
- nieskategoryzowany Cleanmaxx
- nieskategoryzowany Ursus Trotter
- nieskategoryzowany DEDRA
- nieskategoryzowany Corsair
- nieskategoryzowany Emerio
- nieskategoryzowany Owon
- nieskategoryzowany Focusrite
- nieskategoryzowany Baumr-AG
- nieskategoryzowany Patriot
- nieskategoryzowany Google
- nieskategoryzowany Create
- nieskategoryzowany Rega
- nieskategoryzowany Intex
- nieskategoryzowany Biltema
- nieskategoryzowany Oricom
- nieskategoryzowany B.E.G.
- nieskategoryzowany H.Koenig
- nieskategoryzowany MyPOS
- nieskategoryzowany CMI
- nieskategoryzowany Hilti
- nieskategoryzowany Steelseries
- nieskategoryzowany Digitus
- nieskategoryzowany Salewa
- nieskategoryzowany Oppo
- nieskategoryzowany Alesis
- nieskategoryzowany Lowrance
- nieskategoryzowany Anybus
- nieskategoryzowany Melissa
- nieskategoryzowany TechniSat
- nieskategoryzowany Vimar
- nieskategoryzowany Nubert
- nieskategoryzowany Dahua Technology
- nieskategoryzowany Schneider
- nieskategoryzowany Deutz
- nieskategoryzowany SABO
- nieskategoryzowany Ledlenser
- nieskategoryzowany Beper
- nieskategoryzowany Eurolite
- nieskategoryzowany LD Systems
- nieskategoryzowany Techno Line
- nieskategoryzowany Foppapedretti
- nieskategoryzowany Daikin
- nieskategoryzowany Kospel
- nieskategoryzowany EVOline
- nieskategoryzowany Kubota
- nieskategoryzowany Thetford
- nieskategoryzowany Oehlbach
- nieskategoryzowany TrueLife
- nieskategoryzowany Eufy
- nieskategoryzowany Ricoh
- nieskategoryzowany TOGU
- nieskategoryzowany SMART Technologies
- nieskategoryzowany NZXT
- nieskategoryzowany Audioengine
- nieskategoryzowany Hozelock
- nieskategoryzowany OneConcept
- nieskategoryzowany CDA
- nieskategoryzowany Emos
- nieskategoryzowany Sabrent
- nieskategoryzowany AVMATRIX
- nieskategoryzowany IMC Toys
- nieskategoryzowany Philco
- nieskategoryzowany Neff
- nieskategoryzowany Seiko
- nieskategoryzowany Renkforce
- nieskategoryzowany Rollei
- nieskategoryzowany Corbero
- nieskategoryzowany Zanussi
- nieskategoryzowany Sonel
- nieskategoryzowany NightStick
- nieskategoryzowany Instant
- nieskategoryzowany Crivit
- nieskategoryzowany Marshall
- nieskategoryzowany Osram
- nieskategoryzowany BaseTech
- nieskategoryzowany Thermex
- nieskategoryzowany Traxxas
- nieskategoryzowany Viessmann
- nieskategoryzowany Perel
- nieskategoryzowany Wagner
- nieskategoryzowany Fagor
- nieskategoryzowany GoldAir
- nieskategoryzowany Sena
- nieskategoryzowany Graco
- nieskategoryzowany Trotec
- nieskategoryzowany Autel
- nieskategoryzowany Uniden
- nieskategoryzowany Adder
- nieskategoryzowany Ansmann
- nieskategoryzowany Clarion
- nieskategoryzowany Netgear
- nieskategoryzowany Cellular Line
- nieskategoryzowany Thomson
- nieskategoryzowany DiO
- nieskategoryzowany Pro-Ject
- nieskategoryzowany Texas Instruments
- nieskategoryzowany Lastolite
- nieskategoryzowany AVM
- nieskategoryzowany La Crosse Technology
- nieskategoryzowany Growatt
- nieskategoryzowany Izzy
- nieskategoryzowany Little Tikes
- nieskategoryzowany Chipolino
- nieskategoryzowany Velleman
- nieskategoryzowany Ferguson
- nieskategoryzowany BT
- nieskategoryzowany Meec Tools
- nieskategoryzowany Fusion
- nieskategoryzowany BOYA
- nieskategoryzowany WMF
- nieskategoryzowany Korg
- nieskategoryzowany ProfiCook
- nieskategoryzowany Homematic IP
- nieskategoryzowany DataVideo
- nieskategoryzowany One For All
- nieskategoryzowany Klarstein
- nieskategoryzowany Safety 1st
- nieskategoryzowany Polti
- nieskategoryzowany Totolink
- nieskategoryzowany Danfoss
- nieskategoryzowany JYSK
- nieskategoryzowany Coyote
- nieskategoryzowany Intertechno
- nieskategoryzowany Black Box
- nieskategoryzowany Lowepro
- nieskategoryzowany Güde
- nieskategoryzowany Arendo
- nieskategoryzowany DreamGEAR
- nieskategoryzowany Victron Energy
- nieskategoryzowany Delta Dore
- nieskategoryzowany E-ast
- nieskategoryzowany Manta
- nieskategoryzowany Pyle
- nieskategoryzowany CTA Digital
- nieskategoryzowany Segway
- nieskategoryzowany Gem Toys
- nieskategoryzowany Texas
- nieskategoryzowany Lancom
- nieskategoryzowany Adviti
- nieskategoryzowany Crimson
- nieskategoryzowany Dymo
- nieskategoryzowany ATIKA
- nieskategoryzowany Hauck
- nieskategoryzowany Iogear
- nieskategoryzowany Cardo
- nieskategoryzowany Panduit
- nieskategoryzowany Intellinet
- nieskategoryzowany NGS
- nieskategoryzowany CRUX
- nieskategoryzowany Newline
- nieskategoryzowany Bavaria
- nieskategoryzowany Devolo
- nieskategoryzowany Juwel
- nieskategoryzowany Biostar
- nieskategoryzowany Dirt Devil
- nieskategoryzowany Midland
- nieskategoryzowany Marantz
- nieskategoryzowany KitchenAid
- nieskategoryzowany MARTOR
- nieskategoryzowany AFK
- nieskategoryzowany AOC
- nieskategoryzowany Monster
- nieskategoryzowany Sennheiser
- nieskategoryzowany EchoMaster
- nieskategoryzowany JANDY
- nieskategoryzowany Esoteric
- nieskategoryzowany Roidmi
- nieskategoryzowany Zipper
- nieskategoryzowany Vivotek
- nieskategoryzowany Eta
- nieskategoryzowany Mount-It!
- nieskategoryzowany Camry
- nieskategoryzowany Steba
- nieskategoryzowany Werma
- nieskategoryzowany Peerless-AV
- nieskategoryzowany Speco Technologies
- nieskategoryzowany Suunto
- nieskategoryzowany Showtec
- nieskategoryzowany Weber
- nieskategoryzowany Heckler Design
- nieskategoryzowany Lenoxx
- nieskategoryzowany Grundfos
- nieskategoryzowany Samson
- nieskategoryzowany EtiamPro
- nieskategoryzowany Faworyt
- nieskategoryzowany EA Elektro Automatik
- nieskategoryzowany Imperial
- nieskategoryzowany Helios
- nieskategoryzowany Scarlett
- nieskategoryzowany Microlife
- nieskategoryzowany PreSonus
- nieskategoryzowany Mercusys
- nieskategoryzowany Koss
- nieskategoryzowany Audio Pro
- nieskategoryzowany I-TEC
- nieskategoryzowany ARRI
- nieskategoryzowany Gossen Metrawatt
- nieskategoryzowany Sôlt
- nieskategoryzowany Eden
- nieskategoryzowany Fosi Audio
- nieskategoryzowany TC Electronic
- nieskategoryzowany Shelly
- nieskategoryzowany Revox
- nieskategoryzowany Fluke
- nieskategoryzowany Nevir
- nieskategoryzowany Kindermann
- nieskategoryzowany Megger
- nieskategoryzowany Kayser
- nieskategoryzowany Olympus
- nieskategoryzowany Navitel
- nieskategoryzowany Greisinger
- nieskategoryzowany MTD
- nieskategoryzowany Oliveri
- nieskategoryzowany Musical Fidelity
- nieskategoryzowany Master Lock
- nieskategoryzowany Bogen
- nieskategoryzowany Pulsar
- nieskategoryzowany PATLITE
- nieskategoryzowany Exquisit
- nieskategoryzowany Bartscher
- nieskategoryzowany Schaudt
- nieskategoryzowany Phanteks
- nieskategoryzowany Hestan
- nieskategoryzowany Gastroback
- nieskategoryzowany GYS
- nieskategoryzowany Mitsubishi
- nieskategoryzowany Edimax
- nieskategoryzowany Razer
- nieskategoryzowany Dimplex
- nieskategoryzowany Florabest
- nieskategoryzowany Harvia
- nieskategoryzowany Baxi
- nieskategoryzowany ADATA
- nieskategoryzowany Kidde
- nieskategoryzowany Chief
- nieskategoryzowany Peavey
- nieskategoryzowany GoClever
- nieskategoryzowany Baby Lock
- nieskategoryzowany Dehner
- nieskategoryzowany ION
- nieskategoryzowany Camille Bauer
- nieskategoryzowany Huion
- nieskategoryzowany Arçelik
- nieskategoryzowany ART
- nieskategoryzowany First Alert
- nieskategoryzowany Assa Abloy
- nieskategoryzowany Solo
- nieskategoryzowany Continental Edison
- nieskategoryzowany RCF
- nieskategoryzowany Topmove
- nieskategoryzowany Delta
- nieskategoryzowany Kerbl
- nieskategoryzowany Zhiyun
- nieskategoryzowany Gree
- nieskategoryzowany Fluval
- nieskategoryzowany Bissell
- nieskategoryzowany Rolls
- nieskategoryzowany Audio-Technica
- nieskategoryzowany Maginon
- nieskategoryzowany EnGenius
- nieskategoryzowany Atag
- nieskategoryzowany Rosieres
- nieskategoryzowany Franke
- nieskategoryzowany Planet
- nieskategoryzowany Adidas
- nieskategoryzowany GoGen
- nieskategoryzowany Accu-Chek
- nieskategoryzowany RCBS
- nieskategoryzowany Peg Perego
- nieskategoryzowany NEC
- nieskategoryzowany Brandson
- nieskategoryzowany Soundcraft
- nieskategoryzowany Parrot
- nieskategoryzowany Antec
- nieskategoryzowany Vornado
- nieskategoryzowany Polaroid
- nieskategoryzowany Rocktrail
- nieskategoryzowany Prestigio
- nieskategoryzowany Aiwa
- nieskategoryzowany G3 Ferrari
- nieskategoryzowany JL Audio
- nieskategoryzowany LevelOne
- nieskategoryzowany Konica Minolta
- nieskategoryzowany AKAI
- nieskategoryzowany Tunturi
- nieskategoryzowany Razor
- nieskategoryzowany Digi
- nieskategoryzowany Mobicool
- nieskategoryzowany Axis
- nieskategoryzowany Deity
- nieskategoryzowany Vivolink
- nieskategoryzowany Westfalia
- nieskategoryzowany Hamilton Beach
- nieskategoryzowany Majority
- nieskategoryzowany Hayward
- nieskategoryzowany Neumärker
- nieskategoryzowany Rigol
- nieskategoryzowany Bixolon
- nieskategoryzowany Ergotools Pattfield
- nieskategoryzowany Novy
- nieskategoryzowany Hartke
- nieskategoryzowany Clatronic
- nieskategoryzowany Healthy Choice
- nieskategoryzowany Tronic
- nieskategoryzowany Dali
- nieskategoryzowany NEO Tools
- nieskategoryzowany Oregon Scientific
- nieskategoryzowany Lorex
- nieskategoryzowany Eventide
- nieskategoryzowany Optoma
- nieskategoryzowany Kisag
- nieskategoryzowany Rommer
- nieskategoryzowany Ariete
- nieskategoryzowany Carrera
- nieskategoryzowany Flame
- nieskategoryzowany Hifonics
- nieskategoryzowany Vogel's
- nieskategoryzowany Heidemann
- nieskategoryzowany Fuzzix
- nieskategoryzowany Focal
- nieskategoryzowany OnePlus
- nieskategoryzowany Tepro
- nieskategoryzowany LiftMaster
- nieskategoryzowany Viper
- nieskategoryzowany Napoleon
- nieskategoryzowany DBX
- nieskategoryzowany Princess
- nieskategoryzowany Christmaxx
- nieskategoryzowany Baby Jogger
- nieskategoryzowany Kicker
- nieskategoryzowany Amazon
- nieskategoryzowany Carson
- nieskategoryzowany Doepfer
- nieskategoryzowany TDE Instruments
- nieskategoryzowany Aluratek
- nieskategoryzowany Abus
- nieskategoryzowany Thorens
- nieskategoryzowany Bresser
- nieskategoryzowany Omnitronic
- nieskategoryzowany Livarno Lux
- nieskategoryzowany Olympia
- nieskategoryzowany Hama
- nieskategoryzowany Mackie
- nieskategoryzowany Juki
- nieskategoryzowany Microsoft
- nieskategoryzowany Marmitek
- nieskategoryzowany Eltako
- nieskategoryzowany Palmer
- nieskategoryzowany Sanitaire
- nieskategoryzowany FiiO
- nieskategoryzowany SE Electronics
- nieskategoryzowany Western Digital
- nieskategoryzowany Princeton Tec
- nieskategoryzowany Baby Annabell
- nieskategoryzowany Taylor
- nieskategoryzowany Duronic
- nieskategoryzowany Vincent
- nieskategoryzowany Smart-AVI
- nieskategoryzowany Maximum
- nieskategoryzowany Omega
- nieskategoryzowany Medel
- nieskategoryzowany Fein
- nieskategoryzowany Mattel
- nieskategoryzowany Goobay
- nieskategoryzowany Optex
- nieskategoryzowany BC Acoustique
- nieskategoryzowany Bush
- nieskategoryzowany Siméo
- nieskategoryzowany Schwaiger
- nieskategoryzowany New Pol
- nieskategoryzowany 4Garden
- nieskategoryzowany Sharkoon
- nieskategoryzowany Eheim
- nieskategoryzowany Watson
- nieskategoryzowany Saramonic
- nieskategoryzowany Mean Well
- nieskategoryzowany Gravity
- nieskategoryzowany Equip
- nieskategoryzowany DeepCool
- nieskategoryzowany Boso
- nieskategoryzowany Kemo
- nieskategoryzowany Terraillon
- nieskategoryzowany Sera
- nieskategoryzowany Aerotec
- nieskategoryzowany GA.MA
- nieskategoryzowany Deaf Bonce
- nieskategoryzowany VOX
- nieskategoryzowany Ferm
- nieskategoryzowany Insignia
- nieskategoryzowany Pelgrim
- nieskategoryzowany Walrus Audio
- nieskategoryzowany Ambient Weather
- nieskategoryzowany Playtive
- nieskategoryzowany Arris
- nieskategoryzowany Navman
- nieskategoryzowany Gabor
- nieskategoryzowany ZKTeco
- nieskategoryzowany Frilec
- nieskategoryzowany Jane
- nieskategoryzowany Hager
- nieskategoryzowany Extech
- nieskategoryzowany NANO Modules
- nieskategoryzowany GVM
- nieskategoryzowany Ravensburger
- nieskategoryzowany True
- nieskategoryzowany ECS
- nieskategoryzowany Franklin
- nieskategoryzowany Victrola
- nieskategoryzowany XPG
- nieskategoryzowany Orima
- nieskategoryzowany Infinity
- nieskategoryzowany Pentair
- nieskategoryzowany Solis
- nieskategoryzowany Denver
- nieskategoryzowany Harley Benton
- nieskategoryzowany Anker
- nieskategoryzowany Testboy
- nieskategoryzowany Pentax
- nieskategoryzowany Bushnell
- nieskategoryzowany Horizon Fitness
- nieskategoryzowany Berger & Schröter
- nieskategoryzowany Dynacord
- nieskategoryzowany Aspes
- nieskategoryzowany Orion
- nieskategoryzowany Ashly
- nieskategoryzowany Hitachi
- nieskategoryzowany Blumfeldt
- nieskategoryzowany Yale
- nieskategoryzowany JIMMY
- nieskategoryzowany FED
- nieskategoryzowany InfaSecure
- nieskategoryzowany Em-Trak
- nieskategoryzowany Rapoo
- nieskategoryzowany Tracer
- nieskategoryzowany Salton
- nieskategoryzowany IStarUSA
- nieskategoryzowany Technika
- nieskategoryzowany Emerson
- nieskategoryzowany Enhance
- nieskategoryzowany SereneLife
- nieskategoryzowany JennAir
- nieskategoryzowany Craftsman
- nieskategoryzowany Silverstone
- nieskategoryzowany Mooer
- nieskategoryzowany Ernitec
- nieskategoryzowany AKG
- nieskategoryzowany Vemer
- nieskategoryzowany Frigidaire
- nieskategoryzowany CyberPower
- nieskategoryzowany Azden
- nieskategoryzowany FeiyuTech
- nieskategoryzowany Roccat
- nieskategoryzowany Barazza
- nieskategoryzowany Klein Tools
- nieskategoryzowany MEE Audio
- nieskategoryzowany Black Diamond
- nieskategoryzowany AJA
- nieskategoryzowany Electro Harmonix
- nieskategoryzowany Scotsman
- nieskategoryzowany Marvel
- nieskategoryzowany Media-Tech
- nieskategoryzowany Sodapop
- nieskategoryzowany Summit
- nieskategoryzowany Trevi
- nieskategoryzowany Technaxx
- nieskategoryzowany Atlona
- nieskategoryzowany Elektrobock
- nieskategoryzowany Thermaltake
- nieskategoryzowany Amer
- nieskategoryzowany Fibaro
- nieskategoryzowany Simrad
- nieskategoryzowany ENTES
- nieskategoryzowany Soundskins
- nieskategoryzowany Ridgid
- nieskategoryzowany Minn Kota
- nieskategoryzowany GPX
- nieskategoryzowany Gefen
- nieskategoryzowany Lanaform
- nieskategoryzowany Martin
- nieskategoryzowany Rommelsbacher
- nieskategoryzowany American International
- nieskategoryzowany Ixxat
- nieskategoryzowany SEADA
- nieskategoryzowany Vivanco
- nieskategoryzowany Inkbird
- nieskategoryzowany Radial Engineering
- nieskategoryzowany Fulgor Milano
- nieskategoryzowany Quantum
- nieskategoryzowany MDT
- nieskategoryzowany Kelvinator
- nieskategoryzowany Inface
- nieskategoryzowany Asaklitt
- nieskategoryzowany Sencor
- nieskategoryzowany Emko
- nieskategoryzowany BDI
- nieskategoryzowany Hobart
- nieskategoryzowany Mistral
- nieskategoryzowany Elica
- nieskategoryzowany Raymarine
- nieskategoryzowany Powerfix
- nieskategoryzowany HiKOKI
- nieskategoryzowany Workzone
- nieskategoryzowany Tempo
- nieskategoryzowany EasyMaxx
- nieskategoryzowany Stinger
- nieskategoryzowany BABY Born
- nieskategoryzowany Seaward
- nieskategoryzowany Power Dynamics
- nieskategoryzowany Blackmagic Design
- nieskategoryzowany AEA
- nieskategoryzowany Gustard
- nieskategoryzowany Asko
- nieskategoryzowany Kanto
- nieskategoryzowany Vacmaster
- nieskategoryzowany Kathrein
- nieskategoryzowany Kalorik
- nieskategoryzowany Rockford Fosgate
- nieskategoryzowany DOD
- nieskategoryzowany Steinberg
- nieskategoryzowany Impact
- nieskategoryzowany Microboards
- nieskategoryzowany JUNG
- nieskategoryzowany Xtorm
- nieskategoryzowany Burg Wächter
- nieskategoryzowany Honey-Can-Do
- nieskategoryzowany Flavel
- nieskategoryzowany Foscam
- nieskategoryzowany Lumens
- nieskategoryzowany Senal
- nieskategoryzowany TOA
- nieskategoryzowany Newland
- nieskategoryzowany Byron
- nieskategoryzowany Monacor
- nieskategoryzowany Aputure
- nieskategoryzowany HQ Power
- nieskategoryzowany Ferplast
- nieskategoryzowany Daewoo
- nieskategoryzowany ADE
- nieskategoryzowany Hotone
- nieskategoryzowany Neutrik
- nieskategoryzowany Livington
- nieskategoryzowany Electro-Voice
- nieskategoryzowany Consul
- nieskategoryzowany Etekcity
- nieskategoryzowany BioChef
- nieskategoryzowany Wiha
- nieskategoryzowany Proviel
- nieskategoryzowany Kunft
- nieskategoryzowany Robinhood
- nieskategoryzowany Tetra
- nieskategoryzowany Grunkel
- nieskategoryzowany SLV
- nieskategoryzowany Sonnet
- nieskategoryzowany Novation
- nieskategoryzowany Silver Cross
- nieskategoryzowany Vicoustic
- nieskategoryzowany Havis
- nieskategoryzowany Becken
- nieskategoryzowany Haeger
- nieskategoryzowany AudioControl
- nieskategoryzowany Karma
- nieskategoryzowany NOCO
- nieskategoryzowany HT Instruments
- nieskategoryzowany OKAY
- nieskategoryzowany Smartwares
- nieskategoryzowany Elgato
- nieskategoryzowany Traeger
- nieskategoryzowany Magmatic
- nieskategoryzowany Porter-Cable
- nieskategoryzowany Noctua
- nieskategoryzowany Masport
- nieskategoryzowany Metabo
- nieskategoryzowany Audiolab
- nieskategoryzowany KS Tools
- nieskategoryzowany Galcon
- nieskategoryzowany Positivo
- nieskategoryzowany Adj
- nieskategoryzowany Mauser
- nieskategoryzowany Starlink
- nieskategoryzowany Richgro
- nieskategoryzowany Varaluz
- nieskategoryzowany Carlo Gavazzi
- nieskategoryzowany Tactical Fiber Systems
- nieskategoryzowany MEPROLIGHT
- nieskategoryzowany Mellanox
- nieskategoryzowany ShieldRock
- nieskategoryzowany SMS
- nieskategoryzowany PurAthletics
- nieskategoryzowany Longfian
- nieskategoryzowany OLLO
- nieskategoryzowany Yuer
- nieskategoryzowany Teia
- nieskategoryzowany KNEKT
- nieskategoryzowany Favero
- nieskategoryzowany Contemporary Research
- nieskategoryzowany Gator Frameworks
- nieskategoryzowany Stages
- nieskategoryzowany HDFury
- nieskategoryzowany Absco
- nieskategoryzowany Schatten Design
- nieskategoryzowany Car Jack
- nieskategoryzowany LEDs-ON
- nieskategoryzowany Wachendorff
- nieskategoryzowany Euky Bear
- nieskategoryzowany SPL
- nieskategoryzowany SureFire
- nieskategoryzowany Fontastic
- nieskategoryzowany ISi
- nieskategoryzowany Cyrus
- nieskategoryzowany Gold Note
- nieskategoryzowany Ketron
- nieskategoryzowany ETC
- nieskategoryzowany Interstuhl
- nieskategoryzowany AURALiC
- nieskategoryzowany EZ Dupe
- nieskategoryzowany Trent & Steele
- nieskategoryzowany IBEAM
- nieskategoryzowany Terratec
- nieskategoryzowany Gastronoma
- nieskategoryzowany Hoberg
- nieskategoryzowany Aroma
- nieskategoryzowany Reer
- nieskategoryzowany Transcend
- nieskategoryzowany Edilkamin
- nieskategoryzowany Axxess
- nieskategoryzowany Crunch
- nieskategoryzowany Wilson
- nieskategoryzowany InnoGIO
- nieskategoryzowany Goki
- nieskategoryzowany Zoofari
- nieskategoryzowany EGO
- nieskategoryzowany Kingston Technology
- nieskategoryzowany WilTec
- nieskategoryzowany Toro
- nieskategoryzowany AstralPool
- nieskategoryzowany Campart
- nieskategoryzowany ZLine
- nieskategoryzowany Müller
- nieskategoryzowany Ditek
- nieskategoryzowany Cotech
- nieskategoryzowany Gre
- nieskategoryzowany Sport-Elec
- nieskategoryzowany Humminbird
- nieskategoryzowany Dataflex
- nieskategoryzowany Dormakaba
- nieskategoryzowany Stairville
- nieskategoryzowany Snom
- nieskategoryzowany Vitek
- nieskategoryzowany Skil
- nieskategoryzowany Xvive
- nieskategoryzowany Geneva
- nieskategoryzowany Miomare
- nieskategoryzowany SureFlap
- nieskategoryzowany Casaria
- nieskategoryzowany QOMO
- nieskategoryzowany Alfatron
- nieskategoryzowany APA
- nieskategoryzowany Mophie
- nieskategoryzowany Brady
- nieskategoryzowany WHD
- nieskategoryzowany Anton/Bauer
- nieskategoryzowany Sound Devices
- nieskategoryzowany Govee
- nieskategoryzowany Magic Chef
- nieskategoryzowany Eurom
- nieskategoryzowany Match
- nieskategoryzowany Nuki
- nieskategoryzowany Dot Line
- nieskategoryzowany Digitalinx
- nieskategoryzowany Easyrig
- nieskategoryzowany Bolt
- nieskategoryzowany Beha-Amprobe
- nieskategoryzowany Sebo
- nieskategoryzowany Enermax
- nieskategoryzowany SoundMagic
- nieskategoryzowany Maestro
- nieskategoryzowany Clas Ohlson
- nieskategoryzowany RADEMACHER
- nieskategoryzowany Arctic Cooling
- nieskategoryzowany Sauber
- nieskategoryzowany Krysiak
- nieskategoryzowany Salicru
- nieskategoryzowany Laserliner
- nieskategoryzowany Zotac
- nieskategoryzowany Cocraft
- nieskategoryzowany Reflexion
- nieskategoryzowany XQ-lite
- nieskategoryzowany MySoda
- nieskategoryzowany Sumiko
- nieskategoryzowany Smith&Brown
- nieskategoryzowany Megasat
- nieskategoryzowany Kopp
- nieskategoryzowany Sogo
- nieskategoryzowany Salter
- nieskategoryzowany Park Tool
- nieskategoryzowany George Foreman
- nieskategoryzowany Hikmicro
- nieskategoryzowany Waterpik
- nieskategoryzowany Maytronics
- nieskategoryzowany EAT
- nieskategoryzowany Sonnenkönig
- nieskategoryzowany REVO
- nieskategoryzowany Ugreen
- nieskategoryzowany DPA
- nieskategoryzowany Crosley
- nieskategoryzowany Varta
- nieskategoryzowany Nutrichef
- nieskategoryzowany Constructa
- nieskategoryzowany Proline
- nieskategoryzowany Atomos
- nieskategoryzowany Adventuridge
- nieskategoryzowany Howard Leight
- nieskategoryzowany Casa Deco
- nieskategoryzowany Kiev
- nieskategoryzowany EXIT
- nieskategoryzowany Euromaid
- nieskategoryzowany Reloop
- nieskategoryzowany Snow Joe
- nieskategoryzowany Primewire
- nieskategoryzowany Swissvoice
- nieskategoryzowany Lorelli
- nieskategoryzowany XCell
- nieskategoryzowany Schellenberg
- nieskategoryzowany Cherry
- nieskategoryzowany Char-Broil
- nieskategoryzowany Greenworks
- nieskategoryzowany Rittal
- nieskategoryzowany BSS Audio
- nieskategoryzowany Newstar
- nieskategoryzowany Oreck
- nieskategoryzowany Timbersled
- nieskategoryzowany Lasko
- nieskategoryzowany Chandler
- nieskategoryzowany Flama
- nieskategoryzowany Yellow Garden Line
- nieskategoryzowany Microair
- nieskategoryzowany Sevenoak
- nieskategoryzowany Vivitar
- nieskategoryzowany Belkin
- nieskategoryzowany SWIT
- nieskategoryzowany PTZ Optics
- nieskategoryzowany Zeiss
- nieskategoryzowany Bebob
- nieskategoryzowany Heckler
- nieskategoryzowany Morley
- nieskategoryzowany Generac
- nieskategoryzowany Sescom
- nieskategoryzowany Drake
- nieskategoryzowany Kramer
- nieskategoryzowany BLANCO
- nieskategoryzowany Gen Energy
- nieskategoryzowany KanexPro
- nieskategoryzowany Lian Li
- nieskategoryzowany Kahayan
- nieskategoryzowany Lewitt
- nieskategoryzowany Sky-Watcher
- nieskategoryzowany Wimberley
- nieskategoryzowany Kopul
- nieskategoryzowany BZBGear
- nieskategoryzowany K&M
- nieskategoryzowany Serpent
- nieskategoryzowany RGBlink
- nieskategoryzowany Glide Gear
- nieskategoryzowany Hosa
- nieskategoryzowany Vortex
- nieskategoryzowany Cranborne Audio
- nieskategoryzowany SmallRig
- nieskategoryzowany DEERSYNC
- nieskategoryzowany ToughTested
- nieskategoryzowany Arkon
- nieskategoryzowany Fiilex
- nieskategoryzowany Platinum Tools
- nieskategoryzowany Trijicon
- nieskategoryzowany Xcellon
- nieskategoryzowany Intellijel
- nieskategoryzowany CEDAR
- nieskategoryzowany Rupert Neve Designs
- nieskategoryzowany BirdDog
- nieskategoryzowany Pawa
- nieskategoryzowany Erica Synths
- nieskategoryzowany Key Digital
- nieskategoryzowany KJB Security Products
- nieskategoryzowany Whirlwind
- nieskategoryzowany Anywhere Cart
- nieskategoryzowany Soundsphere
- nieskategoryzowany Lemair
- nieskategoryzowany Toyotomi
- nieskategoryzowany TrekStor
- nieskategoryzowany Ideal
- nieskategoryzowany Apantac
- nieskategoryzowany AMX
- nieskategoryzowany Stamina
- nieskategoryzowany Spanninga
- nieskategoryzowany Pansam
- nieskategoryzowany NUK
- nieskategoryzowany JILONG
- nieskategoryzowany OBH Nordica
- nieskategoryzowany ABB
- nieskategoryzowany SRS
- nieskategoryzowany Thermador
- nieskategoryzowany Wolfcraft
- nieskategoryzowany Soler & Palau
- nieskategoryzowany Monzana
- nieskategoryzowany Finlux
- nieskategoryzowany Challenge
- nieskategoryzowany Goodis
- nieskategoryzowany Bestron
- nieskategoryzowany Rio
- nieskategoryzowany Oromed
- nieskategoryzowany Atosa
- nieskategoryzowany Twelve South
- nieskategoryzowany Rotel
- nieskategoryzowany Lexmark
- nieskategoryzowany Waterdrop
- nieskategoryzowany Atlas
- nieskategoryzowany Agfa
- nieskategoryzowany C2G
- nieskategoryzowany Sensiplast
- nieskategoryzowany Swan
- nieskategoryzowany Dangerous Music
- nieskategoryzowany Lumantek
- nieskategoryzowany Kluge
- nieskategoryzowany Devialet
- nieskategoryzowany IFi Audio
- nieskategoryzowany Crosscall
- nieskategoryzowany Cabasse
- nieskategoryzowany Acti
- nieskategoryzowany ACME
- nieskategoryzowany Anslut
- nieskategoryzowany Arthur Martin
- nieskategoryzowany Outwell
- nieskategoryzowany Sitecom
- nieskategoryzowany Logik
- nieskategoryzowany Fortinet
- nieskategoryzowany Profilo
- nieskategoryzowany Ernesto
- nieskategoryzowany Eldom
- nieskategoryzowany Maxxmee
- nieskategoryzowany Plant Craft
- nieskategoryzowany Celestron
- nieskategoryzowany Matrox
- nieskategoryzowany Kubo
- nieskategoryzowany Flir
- nieskategoryzowany Ergobaby
- nieskategoryzowany Geuther
- nieskategoryzowany Trixie
- nieskategoryzowany GeoVision
- nieskategoryzowany Chacon
- nieskategoryzowany Astro
- nieskategoryzowany InFocus
- nieskategoryzowany Glem Gas
- nieskategoryzowany Proctor Silex
- nieskategoryzowany Creda
- nieskategoryzowany Topeak
- nieskategoryzowany Intel
- nieskategoryzowany Kress
- nieskategoryzowany QSC
- nieskategoryzowany Beyerdynamic
- nieskategoryzowany Patching Panda
- nieskategoryzowany Kambrook
- nieskategoryzowany Berner
- nieskategoryzowany Cadac
- nieskategoryzowany Genaray
- nieskategoryzowany Cablexpert
- nieskategoryzowany Roxio
- nieskategoryzowany WHALE
- nieskategoryzowany Noveen
- nieskategoryzowany GMB Gaming
- nieskategoryzowany Blade
- nieskategoryzowany Ipevo
- nieskategoryzowany Waldbeck
- nieskategoryzowany Fanvil
- nieskategoryzowany IHome
- nieskategoryzowany Waves
- nieskategoryzowany Satechi
- nieskategoryzowany Xaoc
- nieskategoryzowany Syma
- nieskategoryzowany Lanberg
- nieskategoryzowany Butler
- nieskategoryzowany Vankyo
- nieskategoryzowany Arovec
- nieskategoryzowany Adam Hall
- nieskategoryzowany Murr Elektronik
- nieskategoryzowany TDK-Lambda
- nieskategoryzowany Ciclo
- nieskategoryzowany Sonoff
- nieskategoryzowany SecureSafe
- nieskategoryzowany CubuSynth
- nieskategoryzowany Yorkville
- nieskategoryzowany Neewer
- nieskategoryzowany Omnires
- nieskategoryzowany Klavis
- nieskategoryzowany Manitowoc
- nieskategoryzowany Joranalogue
- nieskategoryzowany Aconatic
- nieskategoryzowany WyreStorm
- nieskategoryzowany Artecta
- nieskategoryzowany NordicTrack
- nieskategoryzowany Eliminator Lighting
- nieskategoryzowany Christmas Time
- nieskategoryzowany ColorKey
- nieskategoryzowany Apollo Design
- nieskategoryzowany ChyTV
- nieskategoryzowany JoeCo
- nieskategoryzowany Holosun
- nieskategoryzowany Nureva
- nieskategoryzowany Panamax
- nieskategoryzowany Sonifex
- nieskategoryzowany Vertex
- nieskategoryzowany ARC
- nieskategoryzowany FBT
- nieskategoryzowany Andover
- nieskategoryzowany Black Lion Audio
- nieskategoryzowany Manfrotto
- nieskategoryzowany Crucial
- nieskategoryzowany Titanwolf
- nieskategoryzowany Uplink
- nieskategoryzowany Mybeo
- nieskategoryzowany Medicinalis
- nieskategoryzowany CSL
- nieskategoryzowany Bearware
- nieskategoryzowany Liam&Daan
- nieskategoryzowany Traco Power
- nieskategoryzowany Perfect Christmas
- nieskategoryzowany Core SWX
- nieskategoryzowany Universal Audio
- nieskategoryzowany 8BitDo
- nieskategoryzowany PCE
- nieskategoryzowany Warm Audio
- nieskategoryzowany Drawmer
- nieskategoryzowany Velbus
- nieskategoryzowany AirTurn
- nieskategoryzowany Orava
- nieskategoryzowany Holzmann
- nieskategoryzowany Blizzard
- nieskategoryzowany Inverx
- nieskategoryzowany Scanstrut
- nieskategoryzowany Jinbei
- nieskategoryzowany Expressive E
- nieskategoryzowany Gra-Vue
- nieskategoryzowany SurgeX
- nieskategoryzowany MuxLab
- nieskategoryzowany NuTone
- nieskategoryzowany Heitronic
- nieskategoryzowany Pentagram
- nieskategoryzowany RTS
- nieskategoryzowany Ocean Matrix
- nieskategoryzowany MAK
- nieskategoryzowany Dobot
- nieskategoryzowany Ocean Way Audio
- nieskategoryzowany Nearity
- nieskategoryzowany LifeSpan
- nieskategoryzowany Multibrackets
- nieskategoryzowany Urbanista
- nieskategoryzowany Hecate
- nieskategoryzowany ADDAC System
- nieskategoryzowany Hurricane
- nieskategoryzowany Inverto
- nieskategoryzowany Kitchen Brains
- nieskategoryzowany Leotec
- nieskategoryzowany Solplanet
- nieskategoryzowany Alutruss
- nieskategoryzowany AVPro Edge
- nieskategoryzowany Uniropa
- nieskategoryzowany Synco
- nieskategoryzowany Christie
- nieskategoryzowany Peak Design
- nieskategoryzowany MIOPS
- nieskategoryzowany JMAZ Lighting
- nieskategoryzowany Edelkrone
- nieskategoryzowany Amaran
- nieskategoryzowany Hortus
- nieskategoryzowany Enttec
- nieskategoryzowany Defender
- nieskategoryzowany Hawke
- nieskategoryzowany Feelworld
- nieskategoryzowany Bellari
- nieskategoryzowany Altman
- nieskategoryzowany FoxFury
- nieskategoryzowany JK Audio
- nieskategoryzowany Betty Bossi
- nieskategoryzowany Eller
- nieskategoryzowany Grimm Audio
- nieskategoryzowany Rotatrim
- nieskategoryzowany Aguilar
- nieskategoryzowany Claypaky
- nieskategoryzowany ESE
- nieskategoryzowany Digitech
- nieskategoryzowany CAD Audio
- nieskategoryzowany Altrad
- nieskategoryzowany Black Hydra
- nieskategoryzowany Merging
- nieskategoryzowany Orange
- nieskategoryzowany Digigram
- nieskategoryzowany Renogy
- nieskategoryzowany UDG Gear
- nieskategoryzowany Mutec
- nieskategoryzowany SunBriteTV
- nieskategoryzowany DMT
- nieskategoryzowany ICC
Najnowsze instrukcje dla nieskategoryzowany

28 Października 2024

28 Października 2024

27 Października 2024

27 Października 2024

27 Października 2024

27 Października 2024

27 Października 2024

27 Października 2024

27 Października 2024

27 Października 2024