Instrukcja obsługi Microchip HV9918DB1
Microchip
nieskategoryzowany
HV9918DB1
Przeczytaj poniżej 📖 instrukcję obsługi w języku polskim dla Microchip HV9918DB1 (9 stron) w kategorii nieskategoryzowany. Ta instrukcja była pomocna dla 18 osób i została oceniona przez 2 użytkowników na średnio 4.5 gwiazdek
Strona 1/9
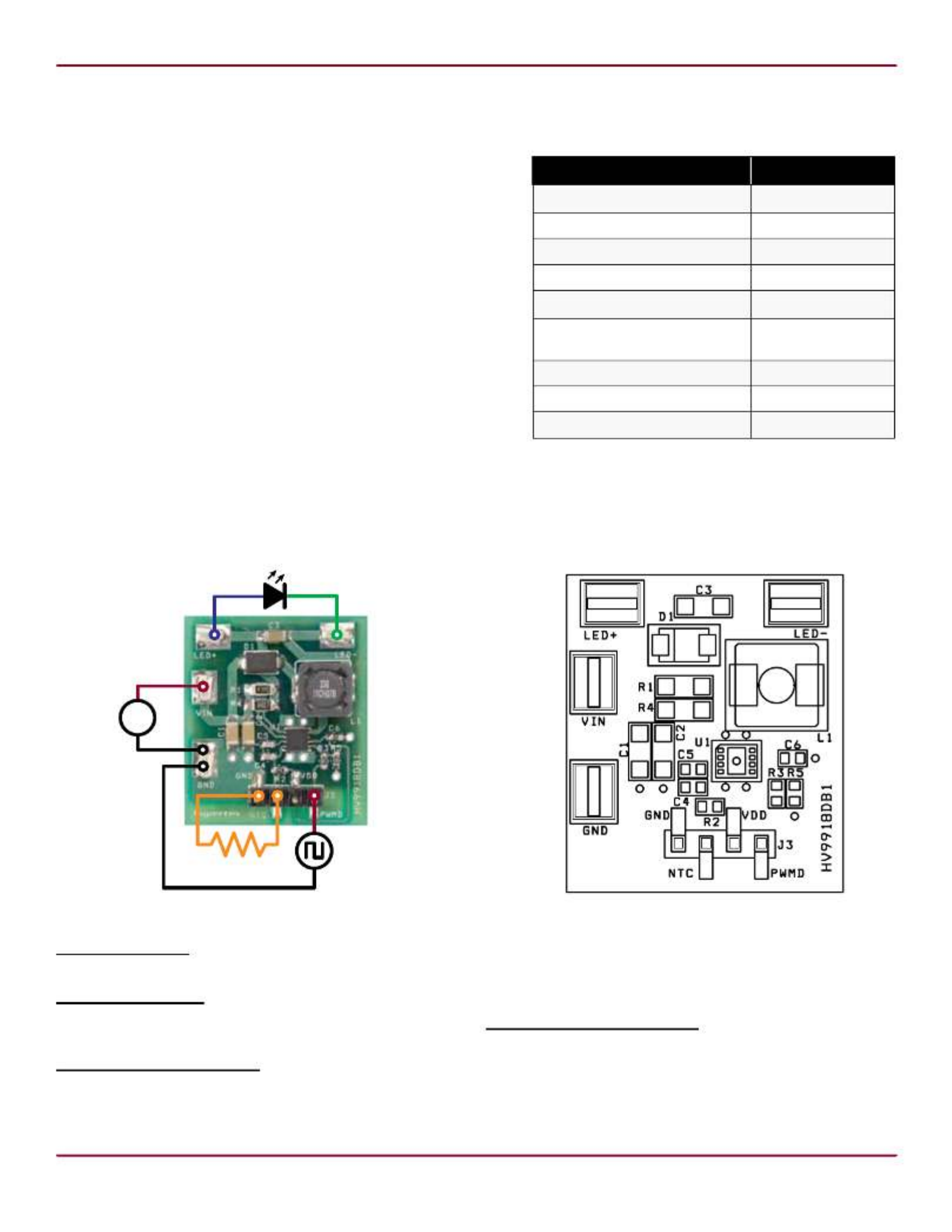
Supertex inc.
Supertex inc.
www.supertex.com
Doc.# DSDB-HV9918DB1
A032913
HV9918DB1
High Current LED Driver Demoboard
Specications
The HV9918DB1 demoboard is a high current LED driver designed
to drive one or two LEDs at 700mA from a 9.0 - 16VDC input. The
demoboard uses Supertex’s HV9918 hysteretic buck LED driver
IC.
The HV9918DB1 includes digital control of PWM dimming, which
allows the user to dim the LEDs using an external, TTL-compatible
square wave source applied between and . In this case, DIM GND
the PWM dimming frequency and duty ratio are set by the external
square wave source.
The demoboard is protected against short circuit and open LED
conditions. It also includes thermal derating of the LED current us-
ing an external NTC resistor to prevent over-heating.
The bottom of the HV9918DB1 is an exposed copper plane (con-
nected to the input ground) which can be connected to a 1” square
heatsink (eg: 374324B00035G from Aavid Thermalloy) to allow
for operation in higher ambient temperatures without tripping the
HV9918’s built-in over temperature protection.
Parameter Value
Input voltage 9.0 - 16VDC
Output voltage 2.0 - 7.0V
Output current 700mA ± 5%
Line and load regulation < ±2%
Output current ripple 5% (peak to peak)
Full load efciency
(@12.0V input) 87%
Open LED protection Yes
Output short circuit protection Yes
Dimensions 25.4mm X 29.2mm
General Description
Connection Diagram
Input Connection: Connect the input DC voltage between
VIN GND and terminals.
Output Connection: Connect the LED(s) between LED+
(anode of LED string) and (cathode of LED string) ter-LED-
minals.
PWM Dimming Connection:
1. If no PWM dimming is required, short PWMD and
VDD terminals.
2. If dimming using an external PWM dimming source,
connect the PWM source between the PWMD and
GND terminals.
NTC Thermistor Connection:
1. If no thermal derating is required, the terminal NTC
can be left open.
2. If thermal derating of the LED current is required, the
NTC thermistor can be connected between NTC
and GND terminals as shown.
Connections
Silk Screen
NTC
+
-
Supertex
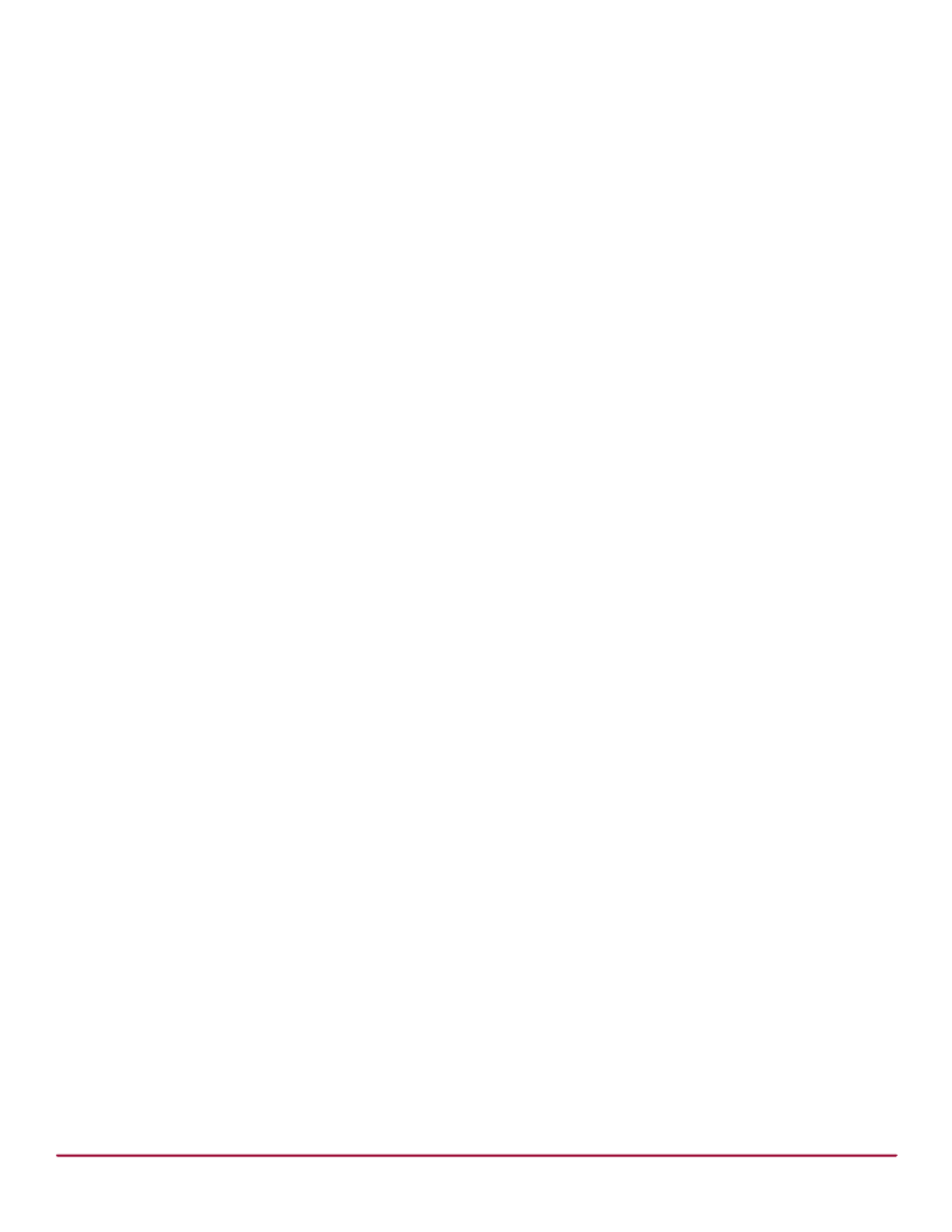
2
HV9918DB1
Supertex inc.
www.supertex.com
Doc.# DSDB-HV9918DB1
A032913
Operation of the Board
The HV9918DB1 uses Supertex’s HV9918 hysteretic buck
LED driver IC to control the LED current. Since the regula-
tion method controls both the peak and the valley current
in the inductor, the demoboard has excellent line and load
regulation.
The LED current can be controlled in by PWM dimming.
PWM dimming can be achieved in one of two ways:
1. Analog control of PWM dimming where a 0-2V source
can be applied between and terminals (the NTC GND
NTC terminal can also be used for thermal derating of
the LED current as explained in the next section).
2. Direct control of PWM dimming by applying a TTL com-
patible square wave source between and PWMD GND
terminals.
Analog Control of PWM Dimming / Thermal De-
rating
Analog Control of PWM dimming can be accomplished by
applying a 0 – 2.0V DC voltage between and (the NTC GND
DC voltage must have a 500μA source/sink capability). In
this case, is connected to and the LEDs are PWMD VDD
dimmed at 1.0kHz (as set by the capacitor at the RAMP pin
of the IC). The duty cycle of the LED current can be adjusted
by varying the external voltage at (0V = 0% LED curNTC -
rent and 2.0V = 100% LED current).
The same terminal can instead be used to de-rate the NTC
LED current based on the LED temperature, if desired. This
would reduce the LED current as the LED temperature rises
and prevents over-heating of the LED. An NTC resistor can
be used to sense the temperature of the LED and this resis-
tor can be connected between the and terminals NTC GND
of the HV9918DB1. The demoboard is designed to operate
with a 100k NTC thermistor which has a B-constant of 4250
(eg: NCP18WF104 from Murata). With this NTC thermistor,
the LED current will start dropping at 85ºC and will reach
about 350mA at 125ºC.
Thermal derating in the HV9918DB1 uses the analog control
of PWM dimming function to limit the LED current when the
LED temperature rises. During normal operating mode (con-
stant LED current; no PWM dimming), the LED current will
be PWM dimmed at 1.0kHz. During PWM dimming mode,
the thermal derating function limits the maximum PWM dim-
ming duty cycle so that the LED current does not exceed
the maximum allowable current determined by the thermal
derating circuit.
Direct Control of PWM Dimming
In the direct control method, the PWM dimming of the LEDs
is achieved by driving the terminal using an external PWMD
square wave source. In this case, PWM dimming frequency
and duty cycle are set by the external source.
In this mode, if the thermal derating function is not desired,
NTC terminal should be left open. In this case, the recom-
mended PWM dimming frequency can be anything up to
10kHz.
If thermal derating is desired, then the NTC thermistor should
be connected between the and terminals. In this NTC GND
case, the PWM dimming frequency should be greater than
1.2kHz.
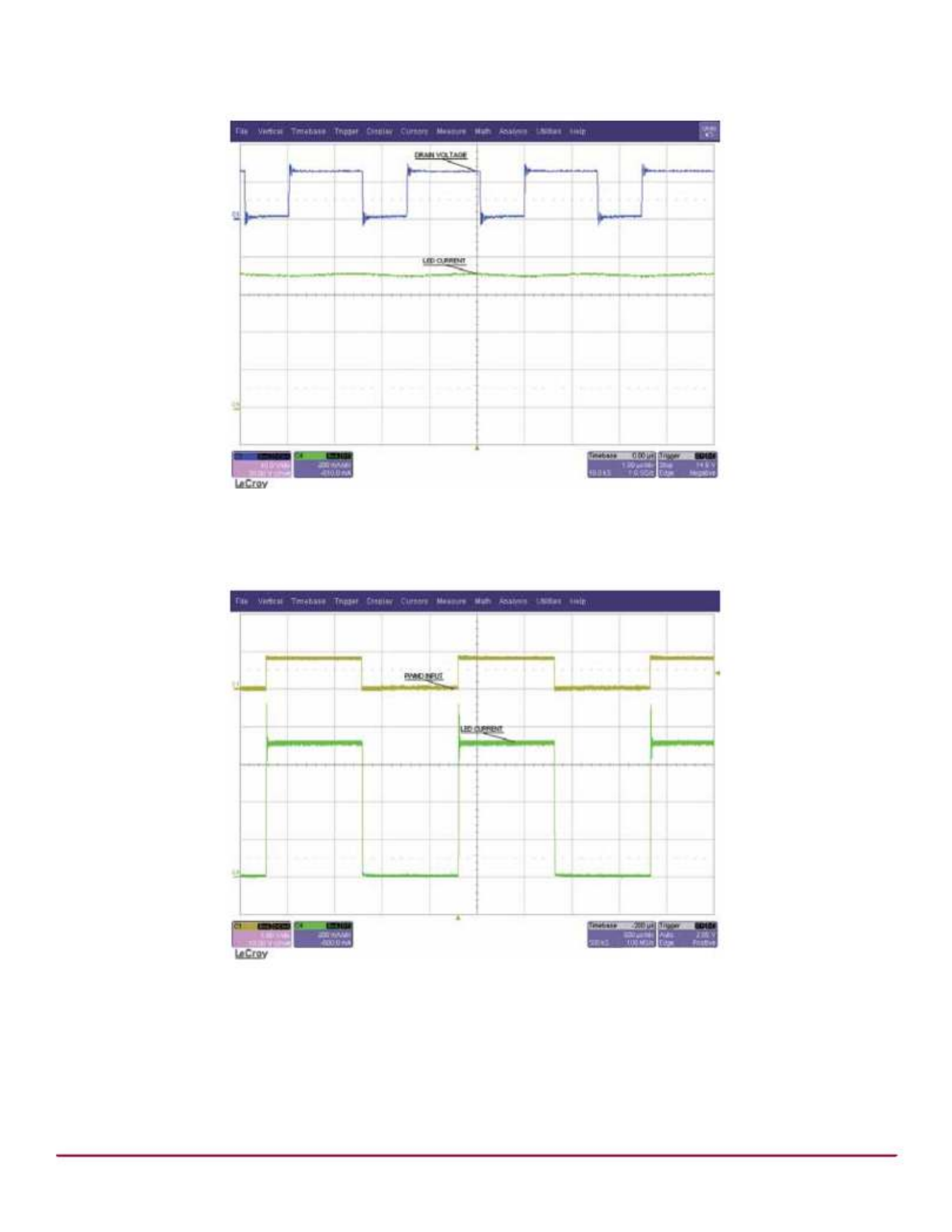
3
HV9918DB1
Supertex inc.
www.supertex.com
Doc.# DSDB-HV9918DB1
A032913
Typical Waveforms (All waveforms are at 12.0V input and 6.9V LED Voltage unless otherwise noted)
Fig. 1. ation – Drain Voltag Normal Oper e and LED Current
Fig. 2. PWM Dimming Waveform
Specyfikacje produktu
Marka: | Microchip |
Kategoria: | nieskategoryzowany |
Model: | HV9918DB1 |
Potrzebujesz pomocy?
Jeśli potrzebujesz pomocy z Microchip HV9918DB1, zadaj pytanie poniżej, a inni użytkownicy Ci odpowiedzą
Instrukcje nieskategoryzowany Microchip

5 Lipca 2024

5 Lipca 2024

5 Lipca 2024

5 Lipca 2024

5 Lipca 2024

5 Lipca 2024

5 Lipca 2024

5 Lipca 2024

5 Lipca 2024

5 Lipca 2024
Instrukcje nieskategoryzowany
- nieskategoryzowany Sony
- nieskategoryzowany Bauknecht
- nieskategoryzowany Yamaha
- nieskategoryzowany Ikea
- nieskategoryzowany Hoshizaki
- nieskategoryzowany Samsung
- nieskategoryzowany Tesy
- nieskategoryzowany PeakTech
- nieskategoryzowany Bertazzoni
- nieskategoryzowany Electrolux
- nieskategoryzowany Gamdias
- nieskategoryzowany Tenda
- nieskategoryzowany DeLonghi
- nieskategoryzowany AEG
- nieskategoryzowany Fellowes
- nieskategoryzowany Balay
- nieskategoryzowany Leica
- nieskategoryzowany Beko
- nieskategoryzowany Teka
- nieskategoryzowany Sven
- nieskategoryzowany ChamSys
- nieskategoryzowany LG
- nieskategoryzowany Worx
- nieskategoryzowany Küppersbusch
- nieskategoryzowany Smeg
- nieskategoryzowany Motorola
- nieskategoryzowany Götze & Jensen
- nieskategoryzowany Dreame
- nieskategoryzowany Beurer
- nieskategoryzowany Stabo
- nieskategoryzowany Logitech
- nieskategoryzowany Gram
- nieskategoryzowany Spektrum
- nieskategoryzowany Xiaomi
- nieskategoryzowany Gorenje
- nieskategoryzowany Etna
- nieskategoryzowany Joy-It
- nieskategoryzowany LERAN
- nieskategoryzowany President
- nieskategoryzowany MyPhone
- nieskategoryzowany Sharp
- nieskategoryzowany BeamZ
- nieskategoryzowany Huawei
- nieskategoryzowany Supermicro
- nieskategoryzowany TCL
- nieskategoryzowany Braun
- nieskategoryzowany Russell Hobbs
- nieskategoryzowany Pioneer
- nieskategoryzowany Statron
- nieskategoryzowany Sage
- nieskategoryzowany Lenovo
- nieskategoryzowany Tefal
- nieskategoryzowany Honda
- nieskategoryzowany TP-Link
- nieskategoryzowany Voltcraft
- nieskategoryzowany Milwaukee
- nieskategoryzowany Philips
- nieskategoryzowany Livoo
- nieskategoryzowany SilverCrest
- nieskategoryzowany Simpson
- nieskategoryzowany Dometic
- nieskategoryzowany Gigabyte
- nieskategoryzowany Acer
- nieskategoryzowany Realme
- nieskategoryzowany Ultimate Speed
- nieskategoryzowany Stihl
- nieskategoryzowany Bosch
- nieskategoryzowany Yato
- nieskategoryzowany Xblitz
- nieskategoryzowany Epson
- nieskategoryzowany JBL
- nieskategoryzowany Parkside
- nieskategoryzowany Hikvision
- nieskategoryzowany Candy
- nieskategoryzowany GW Instek
- nieskategoryzowany Onkyo
- nieskategoryzowany Whirlpool
- nieskategoryzowany Grillmeister
- nieskategoryzowany IPGARD
- nieskategoryzowany Fujitsu
- nieskategoryzowany Ferroli
- nieskategoryzowany Thule
- nieskategoryzowany Roland
- nieskategoryzowany Miele
- nieskategoryzowany HyperX
- nieskategoryzowany Easy Home
- nieskategoryzowany LC-Power
- nieskategoryzowany Waterco
- nieskategoryzowany Geemarc
- nieskategoryzowany Scott
- nieskategoryzowany Brentwood
- nieskategoryzowany Midea
- nieskategoryzowany KEF
- nieskategoryzowany Festool
- nieskategoryzowany Kärcher
- nieskategoryzowany Bose
- nieskategoryzowany Severin
- nieskategoryzowany Hisense
- nieskategoryzowany Berg
- nieskategoryzowany Infiniton
- nieskategoryzowany EZVIZ
- nieskategoryzowany Conceptronic
- nieskategoryzowany Panasonic
- nieskategoryzowany StarTech.com
- nieskategoryzowany Promethean
- nieskategoryzowany Bavaria By Einhell
- nieskategoryzowany Theben
- nieskategoryzowany Liebherr
- nieskategoryzowany Canon
- nieskategoryzowany Mio
- nieskategoryzowany Crestron
- nieskategoryzowany Truetone
- nieskategoryzowany Bestway
- nieskategoryzowany Viewsonic
- nieskategoryzowany Behringer
- nieskategoryzowany Asus
- nieskategoryzowany Nedis
- nieskategoryzowany Stanley
- nieskategoryzowany Nexa
- nieskategoryzowany Jura
- nieskategoryzowany AG Neovo
- nieskategoryzowany Be Cool
- nieskategoryzowany Allen & Heath
- nieskategoryzowany Enphase
- nieskategoryzowany IK Multimedia
- nieskategoryzowany Reolink
- nieskategoryzowany American DJ
- nieskategoryzowany Medion
- nieskategoryzowany Tangent
- nieskategoryzowany Boss
- nieskategoryzowany Black & Decker
- nieskategoryzowany OK
- nieskategoryzowany Lenco
- nieskategoryzowany TRENDnet
- nieskategoryzowany Audioline
- nieskategoryzowany Max Pro
- nieskategoryzowany Scheppach
- nieskategoryzowany Fujifilm
- nieskategoryzowany Proxxon
- nieskategoryzowany Adler
- nieskategoryzowany Bluetti
- nieskategoryzowany BaByliss
- nieskategoryzowany Marquant
- nieskategoryzowany Subaru
- nieskategoryzowany MSI
- nieskategoryzowany Hoover
- nieskategoryzowany Tesla
- nieskategoryzowany Westinghouse
- nieskategoryzowany D-Link
- nieskategoryzowany Hendi
- nieskategoryzowany Jensen
- nieskategoryzowany Niceboy
- nieskategoryzowany Hazet
- nieskategoryzowany Vertiv
- nieskategoryzowany Conair
- nieskategoryzowany GE
- nieskategoryzowany ILive
- nieskategoryzowany Ardes
- nieskategoryzowany Taurus
- nieskategoryzowany VitalMaxx
- nieskategoryzowany RIKON
- nieskategoryzowany Ring
- nieskategoryzowany Orbegozo
- nieskategoryzowany Native Instruments
- nieskategoryzowany Garmin
- nieskategoryzowany Blaupunkt
- nieskategoryzowany Vivax
- nieskategoryzowany ATen
- nieskategoryzowany IOptron
- nieskategoryzowany Grizzly
- nieskategoryzowany Salora
- nieskategoryzowany Siemens
- nieskategoryzowany Teac
- nieskategoryzowany Speed-Link
- nieskategoryzowany Casio
- nieskategoryzowany Iiyama
- nieskategoryzowany Lincoln Electric
- nieskategoryzowany Metra
- nieskategoryzowany Thrustmaster
- nieskategoryzowany Evolveo
- nieskategoryzowany Ambiano
- nieskategoryzowany DeWalt
- nieskategoryzowany Bbf
- nieskategoryzowany Danby
- nieskategoryzowany Martin Logan
- nieskategoryzowany Dual
- nieskategoryzowany Einhell
- nieskategoryzowany Grundig
- nieskategoryzowany APC
- nieskategoryzowany Hegel
- nieskategoryzowany Kiloview
- nieskategoryzowany Haier
- nieskategoryzowany Sigma
- nieskategoryzowany Homedics
- nieskategoryzowany Remington
- nieskategoryzowany HP
- nieskategoryzowany KKT Kolbe
- nieskategoryzowany Cylinda
- nieskategoryzowany S.M.S.L
- nieskategoryzowany Genesis
- nieskategoryzowany Jocel
- nieskategoryzowany Soundmaster
- nieskategoryzowany Hyundai
- nieskategoryzowany Silverline
- nieskategoryzowany Blomberg
- nieskategoryzowany Line 6
- nieskategoryzowany Husqvarna
- nieskategoryzowany Honeywell
- nieskategoryzowany BLOW
- nieskategoryzowany DAP-Audio
- nieskategoryzowany Concept
- nieskategoryzowany Joie
- nieskategoryzowany Manhattan
- nieskategoryzowany Chauvet
- nieskategoryzowany Heritage Audio
- nieskategoryzowany Fisher & Paykel
- nieskategoryzowany Angelcare
- nieskategoryzowany Cotek
- nieskategoryzowany Durvet
- nieskategoryzowany Tripp Lite
- nieskategoryzowany Shure
- nieskategoryzowany EWON
- nieskategoryzowany ECG
- nieskategoryzowany IRobot
- nieskategoryzowany Indesit
- nieskategoryzowany Matsui
- nieskategoryzowany Amazfit
- nieskategoryzowany Steinel
- nieskategoryzowany Makita
- nieskategoryzowany Ilve
- nieskategoryzowany Mikrotik
- nieskategoryzowany Denon
- nieskategoryzowany Akasa
- nieskategoryzowany Perkins
- nieskategoryzowany Swann
- nieskategoryzowany Truma
- nieskategoryzowany Kwikset
- nieskategoryzowany Mercury
- nieskategoryzowany Empress Effects
- nieskategoryzowany Carel
- nieskategoryzowany Nikon
- nieskategoryzowany Shimano
- nieskategoryzowany Viking
- nieskategoryzowany Antari
- nieskategoryzowany Medela
- nieskategoryzowany Block
- nieskategoryzowany Ozito
- nieskategoryzowany Kodak
- nieskategoryzowany Phoenix Gold
- nieskategoryzowany Forza
- nieskategoryzowany CATA
- nieskategoryzowany Testo
- nieskategoryzowany Audac
- nieskategoryzowany Cisco
- nieskategoryzowany Revic
- nieskategoryzowany Primera
- nieskategoryzowany Draper
- nieskategoryzowany Aim TTi
- nieskategoryzowany Fuxtec
- nieskategoryzowany ORNO
- nieskategoryzowany Cooler Master
- nieskategoryzowany Sanus
- nieskategoryzowany TFA
- nieskategoryzowany Dyson
- nieskategoryzowany Chauvin Arnoux
- nieskategoryzowany Hotpoint
- nieskategoryzowany Kenwood
- nieskategoryzowany Scosche
- nieskategoryzowany Icy Box
- nieskategoryzowany Sungrow
- nieskategoryzowany NuPrime
- nieskategoryzowany Hasbro
- nieskategoryzowany Moxa
- nieskategoryzowany Trisa
- nieskategoryzowany DJI
- nieskategoryzowany RYOBI
- nieskategoryzowany Kugoo
- nieskategoryzowany Alpine
- nieskategoryzowany Wolf Garten
- nieskategoryzowany Knog
- nieskategoryzowany Gembird
- nieskategoryzowany Scala
- nieskategoryzowany ZTE
- nieskategoryzowany Godox
- nieskategoryzowany Røde
- nieskategoryzowany Zelmer
- nieskategoryzowany Hammersmith
- nieskategoryzowany Chicco
- nieskategoryzowany Chamberlain
- nieskategoryzowany Paradigm
- nieskategoryzowany Lindy
- nieskategoryzowany Olivetti
- nieskategoryzowany Ninja
- nieskategoryzowany Medisana
- nieskategoryzowany Minox
- nieskategoryzowany Cuisinart
- nieskategoryzowany Zebra
- nieskategoryzowany Wilfa
- nieskategoryzowany DSC
- nieskategoryzowany Cobra
- nieskategoryzowany JVC
- nieskategoryzowany ZyXEL
- nieskategoryzowany Auriol
- nieskategoryzowany Konig & Meyer
- nieskategoryzowany Trust
- nieskategoryzowany BLUEPALM
- nieskategoryzowany V7
- nieskategoryzowany Thor
- nieskategoryzowany LogiLink
- nieskategoryzowany Handy
- nieskategoryzowany Memphis Audio
- nieskategoryzowany Sandisk
- nieskategoryzowany Grohe
- nieskategoryzowany Dell
- nieskategoryzowany Polaris
- nieskategoryzowany GLORIA
- nieskategoryzowany IFM
- nieskategoryzowany Krups
- nieskategoryzowany Furrion
- nieskategoryzowany U-Line
- nieskategoryzowany Linksys
- nieskategoryzowany Moulinex
- nieskategoryzowany Cleanmaxx
- nieskategoryzowany Ursus Trotter
- nieskategoryzowany DEDRA
- nieskategoryzowany Corsair
- nieskategoryzowany Emerio
- nieskategoryzowany Owon
- nieskategoryzowany Focusrite
- nieskategoryzowany Baumr-AG
- nieskategoryzowany Patriot
- nieskategoryzowany Google
- nieskategoryzowany Create
- nieskategoryzowany Rega
- nieskategoryzowany Intex
- nieskategoryzowany Biltema
- nieskategoryzowany Oricom
- nieskategoryzowany B.E.G.
- nieskategoryzowany H.Koenig
- nieskategoryzowany MyPOS
- nieskategoryzowany CMI
- nieskategoryzowany Hilti
- nieskategoryzowany Steelseries
- nieskategoryzowany Digitus
- nieskategoryzowany Salewa
- nieskategoryzowany Oppo
- nieskategoryzowany Alesis
- nieskategoryzowany Lowrance
- nieskategoryzowany Anybus
- nieskategoryzowany Melissa
- nieskategoryzowany TechniSat
- nieskategoryzowany Vimar
- nieskategoryzowany Nubert
- nieskategoryzowany Dahua Technology
- nieskategoryzowany Schneider
- nieskategoryzowany Deutz
- nieskategoryzowany SABO
- nieskategoryzowany Ledlenser
- nieskategoryzowany Beper
- nieskategoryzowany Eurolite
- nieskategoryzowany LD Systems
- nieskategoryzowany Techno Line
- nieskategoryzowany Foppapedretti
- nieskategoryzowany Daikin
- nieskategoryzowany Kospel
- nieskategoryzowany EVOline
- nieskategoryzowany Kubota
- nieskategoryzowany Thetford
- nieskategoryzowany Oehlbach
- nieskategoryzowany TrueLife
- nieskategoryzowany Eufy
- nieskategoryzowany Ricoh
- nieskategoryzowany TOGU
- nieskategoryzowany SMART Technologies
- nieskategoryzowany NZXT
- nieskategoryzowany Audioengine
- nieskategoryzowany Hozelock
- nieskategoryzowany OneConcept
- nieskategoryzowany CDA
- nieskategoryzowany Emos
- nieskategoryzowany Sabrent
- nieskategoryzowany AVMATRIX
- nieskategoryzowany IMC Toys
- nieskategoryzowany Philco
- nieskategoryzowany Neff
- nieskategoryzowany Seiko
- nieskategoryzowany Renkforce
- nieskategoryzowany Rollei
- nieskategoryzowany Corbero
- nieskategoryzowany Zanussi
- nieskategoryzowany Sonel
- nieskategoryzowany NightStick
- nieskategoryzowany Instant
- nieskategoryzowany Crivit
- nieskategoryzowany Marshall
- nieskategoryzowany Osram
- nieskategoryzowany BaseTech
- nieskategoryzowany Thermex
- nieskategoryzowany Traxxas
- nieskategoryzowany Viessmann
- nieskategoryzowany Perel
- nieskategoryzowany Wagner
- nieskategoryzowany Fagor
- nieskategoryzowany GoldAir
- nieskategoryzowany Sena
- nieskategoryzowany Graco
- nieskategoryzowany Trotec
- nieskategoryzowany Autel
- nieskategoryzowany Uniden
- nieskategoryzowany Adder
- nieskategoryzowany Ansmann
- nieskategoryzowany Clarion
- nieskategoryzowany Netgear
- nieskategoryzowany Cellular Line
- nieskategoryzowany Thomson
- nieskategoryzowany DiO
- nieskategoryzowany Pro-Ject
- nieskategoryzowany Texas Instruments
- nieskategoryzowany Lastolite
- nieskategoryzowany AVM
- nieskategoryzowany La Crosse Technology
- nieskategoryzowany Growatt
- nieskategoryzowany Izzy
- nieskategoryzowany Little Tikes
- nieskategoryzowany Chipolino
- nieskategoryzowany Velleman
- nieskategoryzowany Ferguson
- nieskategoryzowany BT
- nieskategoryzowany Meec Tools
- nieskategoryzowany Fusion
- nieskategoryzowany BOYA
- nieskategoryzowany WMF
- nieskategoryzowany Korg
- nieskategoryzowany ProfiCook
- nieskategoryzowany Homematic IP
- nieskategoryzowany DataVideo
- nieskategoryzowany One For All
- nieskategoryzowany Klarstein
- nieskategoryzowany Safety 1st
- nieskategoryzowany Polti
- nieskategoryzowany Totolink
- nieskategoryzowany Danfoss
- nieskategoryzowany JYSK
- nieskategoryzowany Coyote
- nieskategoryzowany Intertechno
- nieskategoryzowany Black Box
- nieskategoryzowany Lowepro
- nieskategoryzowany Güde
- nieskategoryzowany Arendo
- nieskategoryzowany DreamGEAR
- nieskategoryzowany Victron Energy
- nieskategoryzowany Delta Dore
- nieskategoryzowany E-ast
- nieskategoryzowany Manta
- nieskategoryzowany Pyle
- nieskategoryzowany CTA Digital
- nieskategoryzowany Segway
- nieskategoryzowany Gem Toys
- nieskategoryzowany Texas
- nieskategoryzowany Lancom
- nieskategoryzowany Adviti
- nieskategoryzowany Crimson
- nieskategoryzowany Dymo
- nieskategoryzowany ATIKA
- nieskategoryzowany Hauck
- nieskategoryzowany Iogear
- nieskategoryzowany Cardo
- nieskategoryzowany Panduit
- nieskategoryzowany Intellinet
- nieskategoryzowany NGS
- nieskategoryzowany CRUX
- nieskategoryzowany Newline
- nieskategoryzowany Bavaria
- nieskategoryzowany Devolo
- nieskategoryzowany Juwel
- nieskategoryzowany Biostar
- nieskategoryzowany Dirt Devil
- nieskategoryzowany Midland
- nieskategoryzowany Marantz
- nieskategoryzowany KitchenAid
- nieskategoryzowany MARTOR
- nieskategoryzowany AFK
- nieskategoryzowany AOC
- nieskategoryzowany Monster
- nieskategoryzowany Sennheiser
- nieskategoryzowany EchoMaster
- nieskategoryzowany JANDY
- nieskategoryzowany Esoteric
- nieskategoryzowany Roidmi
- nieskategoryzowany Zipper
- nieskategoryzowany Vivotek
- nieskategoryzowany Eta
- nieskategoryzowany Mount-It!
- nieskategoryzowany Camry
- nieskategoryzowany Steba
- nieskategoryzowany Werma
- nieskategoryzowany Peerless-AV
- nieskategoryzowany Speco Technologies
- nieskategoryzowany Suunto
- nieskategoryzowany Showtec
- nieskategoryzowany Weber
- nieskategoryzowany Heckler Design
- nieskategoryzowany Lenoxx
- nieskategoryzowany Grundfos
- nieskategoryzowany Samson
- nieskategoryzowany EtiamPro
- nieskategoryzowany Faworyt
- nieskategoryzowany EA Elektro Automatik
- nieskategoryzowany Imperial
- nieskategoryzowany Helios
- nieskategoryzowany Scarlett
- nieskategoryzowany Microlife
- nieskategoryzowany PreSonus
- nieskategoryzowany Mercusys
- nieskategoryzowany Koss
- nieskategoryzowany Audio Pro
- nieskategoryzowany I-TEC
- nieskategoryzowany ARRI
- nieskategoryzowany Gossen Metrawatt
- nieskategoryzowany Sôlt
- nieskategoryzowany Eden
- nieskategoryzowany Fosi Audio
- nieskategoryzowany TC Electronic
- nieskategoryzowany Shelly
- nieskategoryzowany Revox
- nieskategoryzowany Fluke
- nieskategoryzowany Nevir
- nieskategoryzowany Kindermann
- nieskategoryzowany Megger
- nieskategoryzowany Kayser
- nieskategoryzowany Olympus
- nieskategoryzowany Navitel
- nieskategoryzowany Greisinger
- nieskategoryzowany MTD
- nieskategoryzowany Oliveri
- nieskategoryzowany Musical Fidelity
- nieskategoryzowany Master Lock
- nieskategoryzowany Bogen
- nieskategoryzowany Pulsar
- nieskategoryzowany PATLITE
- nieskategoryzowany Exquisit
- nieskategoryzowany Bartscher
- nieskategoryzowany Schaudt
- nieskategoryzowany Phanteks
- nieskategoryzowany Hestan
- nieskategoryzowany Gastroback
- nieskategoryzowany GYS
- nieskategoryzowany Mitsubishi
- nieskategoryzowany Edimax
- nieskategoryzowany Razer
- nieskategoryzowany Dimplex
- nieskategoryzowany Florabest
- nieskategoryzowany Harvia
- nieskategoryzowany Baxi
- nieskategoryzowany ADATA
- nieskategoryzowany Kidde
- nieskategoryzowany Chief
- nieskategoryzowany Peavey
- nieskategoryzowany GoClever
- nieskategoryzowany Baby Lock
- nieskategoryzowany Dehner
- nieskategoryzowany ION
- nieskategoryzowany Camille Bauer
- nieskategoryzowany Huion
- nieskategoryzowany Arçelik
- nieskategoryzowany ART
- nieskategoryzowany First Alert
- nieskategoryzowany Assa Abloy
- nieskategoryzowany Solo
- nieskategoryzowany Continental Edison
- nieskategoryzowany RCF
- nieskategoryzowany Topmove
- nieskategoryzowany Delta
- nieskategoryzowany Kerbl
- nieskategoryzowany Zhiyun
- nieskategoryzowany Gree
- nieskategoryzowany Fluval
- nieskategoryzowany Bissell
- nieskategoryzowany Rolls
- nieskategoryzowany Audio-Technica
- nieskategoryzowany Maginon
- nieskategoryzowany EnGenius
- nieskategoryzowany Atag
- nieskategoryzowany Rosieres
- nieskategoryzowany Franke
- nieskategoryzowany Planet
- nieskategoryzowany Adidas
- nieskategoryzowany GoGen
- nieskategoryzowany Accu-Chek
- nieskategoryzowany RCBS
- nieskategoryzowany Peg Perego
- nieskategoryzowany NEC
- nieskategoryzowany Brandson
- nieskategoryzowany Soundcraft
- nieskategoryzowany Parrot
- nieskategoryzowany Antec
- nieskategoryzowany Vornado
- nieskategoryzowany Polaroid
- nieskategoryzowany Rocktrail
- nieskategoryzowany Prestigio
- nieskategoryzowany Aiwa
- nieskategoryzowany G3 Ferrari
- nieskategoryzowany JL Audio
- nieskategoryzowany LevelOne
- nieskategoryzowany Konica Minolta
- nieskategoryzowany AKAI
- nieskategoryzowany Tunturi
- nieskategoryzowany Razor
- nieskategoryzowany Digi
- nieskategoryzowany Mobicool
- nieskategoryzowany Axis
- nieskategoryzowany Deity
- nieskategoryzowany Vivolink
- nieskategoryzowany Westfalia
- nieskategoryzowany Hamilton Beach
- nieskategoryzowany Majority
- nieskategoryzowany Hayward
- nieskategoryzowany Neumärker
- nieskategoryzowany Rigol
- nieskategoryzowany Bixolon
- nieskategoryzowany Ergotools Pattfield
- nieskategoryzowany Novy
- nieskategoryzowany Hartke
- nieskategoryzowany Clatronic
- nieskategoryzowany Healthy Choice
- nieskategoryzowany Tronic
- nieskategoryzowany Dali
- nieskategoryzowany NEO Tools
- nieskategoryzowany Oregon Scientific
- nieskategoryzowany Lorex
- nieskategoryzowany Eventide
- nieskategoryzowany Optoma
- nieskategoryzowany Kisag
- nieskategoryzowany Rommer
- nieskategoryzowany Ariete
- nieskategoryzowany Carrera
- nieskategoryzowany Flame
- nieskategoryzowany Hifonics
- nieskategoryzowany Vogel's
- nieskategoryzowany Heidemann
- nieskategoryzowany Fuzzix
- nieskategoryzowany Focal
- nieskategoryzowany OnePlus
- nieskategoryzowany Tepro
- nieskategoryzowany LiftMaster
- nieskategoryzowany Viper
- nieskategoryzowany Napoleon
- nieskategoryzowany DBX
- nieskategoryzowany Princess
- nieskategoryzowany Christmaxx
- nieskategoryzowany Baby Jogger
- nieskategoryzowany Kicker
- nieskategoryzowany Amazon
- nieskategoryzowany Carson
- nieskategoryzowany Doepfer
- nieskategoryzowany TDE Instruments
- nieskategoryzowany Aluratek
- nieskategoryzowany Abus
- nieskategoryzowany Thorens
- nieskategoryzowany Bresser
- nieskategoryzowany Omnitronic
- nieskategoryzowany Livarno Lux
- nieskategoryzowany Olympia
- nieskategoryzowany Hama
- nieskategoryzowany Mackie
- nieskategoryzowany Juki
- nieskategoryzowany Microsoft
- nieskategoryzowany Marmitek
- nieskategoryzowany Eltako
- nieskategoryzowany Palmer
- nieskategoryzowany Sanitaire
- nieskategoryzowany FiiO
- nieskategoryzowany SE Electronics
- nieskategoryzowany Western Digital
- nieskategoryzowany Princeton Tec
- nieskategoryzowany Baby Annabell
- nieskategoryzowany Taylor
- nieskategoryzowany Duronic
- nieskategoryzowany Vincent
- nieskategoryzowany Smart-AVI
- nieskategoryzowany Maximum
- nieskategoryzowany Omega
- nieskategoryzowany Medel
- nieskategoryzowany Fein
- nieskategoryzowany Mattel
- nieskategoryzowany Goobay
- nieskategoryzowany Optex
- nieskategoryzowany BC Acoustique
- nieskategoryzowany Bush
- nieskategoryzowany Siméo
- nieskategoryzowany Schwaiger
- nieskategoryzowany New Pol
- nieskategoryzowany 4Garden
- nieskategoryzowany Sharkoon
- nieskategoryzowany Eheim
- nieskategoryzowany Watson
- nieskategoryzowany Saramonic
- nieskategoryzowany Mean Well
- nieskategoryzowany Gravity
- nieskategoryzowany Equip
- nieskategoryzowany DeepCool
- nieskategoryzowany Boso
- nieskategoryzowany Kemo
- nieskategoryzowany Terraillon
- nieskategoryzowany Sera
- nieskategoryzowany Aerotec
- nieskategoryzowany GA.MA
- nieskategoryzowany Deaf Bonce
- nieskategoryzowany VOX
- nieskategoryzowany Ferm
- nieskategoryzowany Insignia
- nieskategoryzowany Pelgrim
- nieskategoryzowany Walrus Audio
- nieskategoryzowany Ambient Weather
- nieskategoryzowany Playtive
- nieskategoryzowany Arris
- nieskategoryzowany Navman
- nieskategoryzowany Gabor
- nieskategoryzowany ZKTeco
- nieskategoryzowany Frilec
- nieskategoryzowany Jane
- nieskategoryzowany Hager
- nieskategoryzowany Extech
- nieskategoryzowany NANO Modules
- nieskategoryzowany GVM
- nieskategoryzowany Ravensburger
- nieskategoryzowany True
- nieskategoryzowany ECS
- nieskategoryzowany Franklin
- nieskategoryzowany Victrola
- nieskategoryzowany XPG
- nieskategoryzowany Orima
- nieskategoryzowany Infinity
- nieskategoryzowany Pentair
- nieskategoryzowany Solis
- nieskategoryzowany Denver
- nieskategoryzowany Harley Benton
- nieskategoryzowany Anker
- nieskategoryzowany Testboy
- nieskategoryzowany Pentax
- nieskategoryzowany Bushnell
- nieskategoryzowany Horizon Fitness
- nieskategoryzowany Berger & Schröter
- nieskategoryzowany Dynacord
- nieskategoryzowany Aspes
- nieskategoryzowany Orion
- nieskategoryzowany Ashly
- nieskategoryzowany Hitachi
- nieskategoryzowany Blumfeldt
- nieskategoryzowany Yale
- nieskategoryzowany JIMMY
- nieskategoryzowany FED
- nieskategoryzowany InfaSecure
- nieskategoryzowany Em-Trak
- nieskategoryzowany Rapoo
- nieskategoryzowany Tracer
- nieskategoryzowany Salton
- nieskategoryzowany IStarUSA
- nieskategoryzowany Technika
- nieskategoryzowany Emerson
- nieskategoryzowany Enhance
- nieskategoryzowany SereneLife
- nieskategoryzowany JennAir
- nieskategoryzowany Craftsman
- nieskategoryzowany Silverstone
- nieskategoryzowany Mooer
- nieskategoryzowany Ernitec
- nieskategoryzowany AKG
- nieskategoryzowany Vemer
- nieskategoryzowany Frigidaire
- nieskategoryzowany CyberPower
- nieskategoryzowany Azden
- nieskategoryzowany FeiyuTech
- nieskategoryzowany Roccat
- nieskategoryzowany Barazza
- nieskategoryzowany Klein Tools
- nieskategoryzowany MEE Audio
- nieskategoryzowany Black Diamond
- nieskategoryzowany AJA
- nieskategoryzowany Electro Harmonix
- nieskategoryzowany Scotsman
- nieskategoryzowany Marvel
- nieskategoryzowany Media-Tech
- nieskategoryzowany Sodapop
- nieskategoryzowany Summit
- nieskategoryzowany Trevi
- nieskategoryzowany Technaxx
- nieskategoryzowany Atlona
- nieskategoryzowany Elektrobock
- nieskategoryzowany Thermaltake
- nieskategoryzowany Amer
- nieskategoryzowany Fibaro
- nieskategoryzowany Simrad
- nieskategoryzowany ENTES
- nieskategoryzowany Soundskins
- nieskategoryzowany Ridgid
- nieskategoryzowany Minn Kota
- nieskategoryzowany GPX
- nieskategoryzowany Gefen
- nieskategoryzowany Lanaform
- nieskategoryzowany Martin
- nieskategoryzowany Rommelsbacher
- nieskategoryzowany American International
- nieskategoryzowany Ixxat
- nieskategoryzowany SEADA
- nieskategoryzowany Vivanco
- nieskategoryzowany Inkbird
- nieskategoryzowany Radial Engineering
- nieskategoryzowany Fulgor Milano
- nieskategoryzowany Quantum
- nieskategoryzowany MDT
- nieskategoryzowany Kelvinator
- nieskategoryzowany Inface
- nieskategoryzowany Asaklitt
- nieskategoryzowany Sencor
- nieskategoryzowany Emko
- nieskategoryzowany BDI
- nieskategoryzowany Hobart
- nieskategoryzowany Mistral
- nieskategoryzowany Elica
- nieskategoryzowany Raymarine
- nieskategoryzowany Powerfix
- nieskategoryzowany HiKOKI
- nieskategoryzowany Workzone
- nieskategoryzowany Tempo
- nieskategoryzowany EasyMaxx
- nieskategoryzowany Stinger
- nieskategoryzowany BABY Born
- nieskategoryzowany Seaward
- nieskategoryzowany Power Dynamics
- nieskategoryzowany Blackmagic Design
- nieskategoryzowany AEA
- nieskategoryzowany Gustard
- nieskategoryzowany Asko
- nieskategoryzowany Kanto
- nieskategoryzowany Vacmaster
- nieskategoryzowany Kathrein
- nieskategoryzowany Kalorik
- nieskategoryzowany Rockford Fosgate
- nieskategoryzowany DOD
- nieskategoryzowany Steinberg
- nieskategoryzowany Impact
- nieskategoryzowany Microboards
- nieskategoryzowany JUNG
- nieskategoryzowany Xtorm
- nieskategoryzowany Burg Wächter
- nieskategoryzowany Honey-Can-Do
- nieskategoryzowany Flavel
- nieskategoryzowany Foscam
- nieskategoryzowany Lumens
- nieskategoryzowany Senal
- nieskategoryzowany TOA
- nieskategoryzowany Newland
- nieskategoryzowany Byron
- nieskategoryzowany Monacor
- nieskategoryzowany Aputure
- nieskategoryzowany HQ Power
- nieskategoryzowany Ferplast
- nieskategoryzowany Daewoo
- nieskategoryzowany ADE
- nieskategoryzowany Hotone
- nieskategoryzowany Neutrik
- nieskategoryzowany Livington
- nieskategoryzowany Electro-Voice
- nieskategoryzowany Consul
- nieskategoryzowany Etekcity
- nieskategoryzowany BioChef
- nieskategoryzowany Wiha
- nieskategoryzowany Proviel
- nieskategoryzowany Kunft
- nieskategoryzowany Robinhood
- nieskategoryzowany Tetra
- nieskategoryzowany Grunkel
- nieskategoryzowany SLV
- nieskategoryzowany Sonnet
- nieskategoryzowany Novation
- nieskategoryzowany Silver Cross
- nieskategoryzowany Vicoustic
- nieskategoryzowany Havis
- nieskategoryzowany Becken
- nieskategoryzowany Haeger
- nieskategoryzowany AudioControl
- nieskategoryzowany Karma
- nieskategoryzowany NOCO
- nieskategoryzowany HT Instruments
- nieskategoryzowany OKAY
- nieskategoryzowany Smartwares
- nieskategoryzowany Elgato
- nieskategoryzowany Traeger
- nieskategoryzowany Magmatic
- nieskategoryzowany Porter-Cable
- nieskategoryzowany Noctua
- nieskategoryzowany Masport
- nieskategoryzowany Metabo
- nieskategoryzowany Audiolab
- nieskategoryzowany KS Tools
- nieskategoryzowany Galcon
- nieskategoryzowany Positivo
- nieskategoryzowany Adj
- nieskategoryzowany Mauser
- nieskategoryzowany Starlink
- nieskategoryzowany Richgro
- nieskategoryzowany Varaluz
- nieskategoryzowany Carlo Gavazzi
- nieskategoryzowany Tactical Fiber Systems
- nieskategoryzowany MEPROLIGHT
- nieskategoryzowany Mellanox
- nieskategoryzowany ShieldRock
- nieskategoryzowany SMS
- nieskategoryzowany PurAthletics
- nieskategoryzowany Longfian
- nieskategoryzowany OLLO
- nieskategoryzowany Yuer
- nieskategoryzowany Teia
- nieskategoryzowany KNEKT
- nieskategoryzowany Favero
- nieskategoryzowany Contemporary Research
- nieskategoryzowany Gator Frameworks
- nieskategoryzowany Stages
- nieskategoryzowany HDFury
- nieskategoryzowany Absco
- nieskategoryzowany Schatten Design
- nieskategoryzowany Car Jack
- nieskategoryzowany LEDs-ON
- nieskategoryzowany Wachendorff
- nieskategoryzowany Euky Bear
- nieskategoryzowany SPL
- nieskategoryzowany SureFire
- nieskategoryzowany Fontastic
- nieskategoryzowany ISi
- nieskategoryzowany Cyrus
- nieskategoryzowany Gold Note
- nieskategoryzowany Ketron
- nieskategoryzowany ETC
- nieskategoryzowany Interstuhl
- nieskategoryzowany AURALiC
- nieskategoryzowany EZ Dupe
- nieskategoryzowany Trent & Steele
- nieskategoryzowany IBEAM
- nieskategoryzowany Terratec
- nieskategoryzowany Gastronoma
- nieskategoryzowany Hoberg
- nieskategoryzowany Aroma
- nieskategoryzowany Reer
- nieskategoryzowany Transcend
- nieskategoryzowany Edilkamin
- nieskategoryzowany Axxess
- nieskategoryzowany Crunch
- nieskategoryzowany Wilson
- nieskategoryzowany InnoGIO
- nieskategoryzowany Goki
- nieskategoryzowany Zoofari
- nieskategoryzowany EGO
- nieskategoryzowany Kingston Technology
- nieskategoryzowany WilTec
- nieskategoryzowany Toro
- nieskategoryzowany AstralPool
- nieskategoryzowany Campart
- nieskategoryzowany ZLine
- nieskategoryzowany Müller
- nieskategoryzowany Ditek
- nieskategoryzowany Cotech
- nieskategoryzowany Gre
- nieskategoryzowany Sport-Elec
- nieskategoryzowany Humminbird
- nieskategoryzowany Dataflex
- nieskategoryzowany Dormakaba
- nieskategoryzowany Stairville
- nieskategoryzowany Snom
- nieskategoryzowany Vitek
- nieskategoryzowany Skil
- nieskategoryzowany Xvive
- nieskategoryzowany Geneva
- nieskategoryzowany Miomare
- nieskategoryzowany SureFlap
- nieskategoryzowany Casaria
- nieskategoryzowany QOMO
- nieskategoryzowany Alfatron
- nieskategoryzowany APA
- nieskategoryzowany Mophie
- nieskategoryzowany Brady
- nieskategoryzowany WHD
- nieskategoryzowany Anton/Bauer
- nieskategoryzowany Sound Devices
- nieskategoryzowany Govee
- nieskategoryzowany Magic Chef
- nieskategoryzowany Eurom
- nieskategoryzowany Match
- nieskategoryzowany Nuki
- nieskategoryzowany Dot Line
- nieskategoryzowany Digitalinx
- nieskategoryzowany Easyrig
- nieskategoryzowany Bolt
- nieskategoryzowany Beha-Amprobe
- nieskategoryzowany Sebo
- nieskategoryzowany Enermax
- nieskategoryzowany SoundMagic
- nieskategoryzowany Maestro
- nieskategoryzowany Clas Ohlson
- nieskategoryzowany RADEMACHER
- nieskategoryzowany Arctic Cooling
- nieskategoryzowany Sauber
- nieskategoryzowany Krysiak
- nieskategoryzowany Salicru
- nieskategoryzowany Laserliner
- nieskategoryzowany Zotac
- nieskategoryzowany Cocraft
- nieskategoryzowany Reflexion
- nieskategoryzowany XQ-lite
- nieskategoryzowany MySoda
- nieskategoryzowany Sumiko
- nieskategoryzowany Smith&Brown
- nieskategoryzowany Megasat
- nieskategoryzowany Kopp
- nieskategoryzowany Sogo
- nieskategoryzowany Salter
- nieskategoryzowany Park Tool
- nieskategoryzowany George Foreman
- nieskategoryzowany Hikmicro
- nieskategoryzowany Waterpik
- nieskategoryzowany Maytronics
- nieskategoryzowany EAT
- nieskategoryzowany Sonnenkönig
- nieskategoryzowany REVO
- nieskategoryzowany Ugreen
- nieskategoryzowany DPA
- nieskategoryzowany Crosley
- nieskategoryzowany Varta
- nieskategoryzowany Nutrichef
- nieskategoryzowany Constructa
- nieskategoryzowany Proline
- nieskategoryzowany Atomos
- nieskategoryzowany Adventuridge
- nieskategoryzowany Howard Leight
- nieskategoryzowany Casa Deco
- nieskategoryzowany Kiev
- nieskategoryzowany EXIT
- nieskategoryzowany Euromaid
- nieskategoryzowany Reloop
- nieskategoryzowany Snow Joe
- nieskategoryzowany Primewire
- nieskategoryzowany Swissvoice
- nieskategoryzowany Lorelli
- nieskategoryzowany XCell
- nieskategoryzowany Schellenberg
- nieskategoryzowany Cherry
- nieskategoryzowany Char-Broil
- nieskategoryzowany Greenworks
- nieskategoryzowany Rittal
- nieskategoryzowany BSS Audio
- nieskategoryzowany Newstar
- nieskategoryzowany Oreck
- nieskategoryzowany Timbersled
- nieskategoryzowany Lasko
- nieskategoryzowany Chandler
- nieskategoryzowany Flama
- nieskategoryzowany Yellow Garden Line
- nieskategoryzowany Microair
- nieskategoryzowany Sevenoak
- nieskategoryzowany Vivitar
- nieskategoryzowany Belkin
- nieskategoryzowany SWIT
- nieskategoryzowany PTZ Optics
- nieskategoryzowany Zeiss
- nieskategoryzowany Bebob
- nieskategoryzowany Heckler
- nieskategoryzowany Morley
- nieskategoryzowany Generac
- nieskategoryzowany Sescom
- nieskategoryzowany Drake
- nieskategoryzowany Kramer
- nieskategoryzowany BLANCO
- nieskategoryzowany Gen Energy
- nieskategoryzowany KanexPro
- nieskategoryzowany Lian Li
- nieskategoryzowany Kahayan
- nieskategoryzowany Lewitt
- nieskategoryzowany Sky-Watcher
- nieskategoryzowany Wimberley
- nieskategoryzowany Kopul
- nieskategoryzowany BZBGear
- nieskategoryzowany K&M
- nieskategoryzowany Serpent
- nieskategoryzowany RGBlink
- nieskategoryzowany Glide Gear
- nieskategoryzowany Hosa
- nieskategoryzowany Vortex
- nieskategoryzowany Cranborne Audio
- nieskategoryzowany SmallRig
- nieskategoryzowany DEERSYNC
- nieskategoryzowany ToughTested
- nieskategoryzowany Arkon
- nieskategoryzowany Fiilex
- nieskategoryzowany Platinum Tools
- nieskategoryzowany Trijicon
- nieskategoryzowany Xcellon
- nieskategoryzowany Intellijel
- nieskategoryzowany CEDAR
- nieskategoryzowany Rupert Neve Designs
- nieskategoryzowany BirdDog
- nieskategoryzowany Pawa
- nieskategoryzowany Erica Synths
- nieskategoryzowany Key Digital
- nieskategoryzowany KJB Security Products
- nieskategoryzowany Whirlwind
- nieskategoryzowany Anywhere Cart
- nieskategoryzowany Soundsphere
- nieskategoryzowany Lemair
- nieskategoryzowany Toyotomi
- nieskategoryzowany TrekStor
- nieskategoryzowany Ideal
- nieskategoryzowany Apantac
- nieskategoryzowany AMX
- nieskategoryzowany Stamina
- nieskategoryzowany Spanninga
- nieskategoryzowany Pansam
- nieskategoryzowany NUK
- nieskategoryzowany JILONG
- nieskategoryzowany OBH Nordica
- nieskategoryzowany ABB
- nieskategoryzowany SRS
- nieskategoryzowany Thermador
- nieskategoryzowany Wolfcraft
- nieskategoryzowany Soler & Palau
- nieskategoryzowany Monzana
- nieskategoryzowany Finlux
- nieskategoryzowany Challenge
- nieskategoryzowany Goodis
- nieskategoryzowany Bestron
- nieskategoryzowany Rio
- nieskategoryzowany Oromed
- nieskategoryzowany Atosa
- nieskategoryzowany Twelve South
- nieskategoryzowany Rotel
- nieskategoryzowany Lexmark
- nieskategoryzowany Waterdrop
- nieskategoryzowany Atlas
- nieskategoryzowany Agfa
- nieskategoryzowany C2G
- nieskategoryzowany Sensiplast
- nieskategoryzowany Swan
- nieskategoryzowany Dangerous Music
- nieskategoryzowany Lumantek
- nieskategoryzowany Kluge
- nieskategoryzowany Devialet
- nieskategoryzowany IFi Audio
- nieskategoryzowany Crosscall
- nieskategoryzowany Cabasse
- nieskategoryzowany Acti
- nieskategoryzowany ACME
- nieskategoryzowany Anslut
- nieskategoryzowany Arthur Martin
- nieskategoryzowany Outwell
- nieskategoryzowany Sitecom
- nieskategoryzowany Logik
- nieskategoryzowany Fortinet
- nieskategoryzowany Profilo
- nieskategoryzowany Ernesto
- nieskategoryzowany Eldom
- nieskategoryzowany Maxxmee
- nieskategoryzowany Plant Craft
- nieskategoryzowany Celestron
- nieskategoryzowany Matrox
- nieskategoryzowany Kubo
- nieskategoryzowany Flir
- nieskategoryzowany Ergobaby
- nieskategoryzowany Geuther
- nieskategoryzowany Trixie
- nieskategoryzowany GeoVision
- nieskategoryzowany Chacon
- nieskategoryzowany Astro
- nieskategoryzowany InFocus
- nieskategoryzowany Glem Gas
- nieskategoryzowany Proctor Silex
- nieskategoryzowany Creda
- nieskategoryzowany Topeak
- nieskategoryzowany Intel
- nieskategoryzowany Kress
- nieskategoryzowany QSC
- nieskategoryzowany Beyerdynamic
- nieskategoryzowany Patching Panda
- nieskategoryzowany Kambrook
- nieskategoryzowany Berner
- nieskategoryzowany Cadac
- nieskategoryzowany Genaray
- nieskategoryzowany Cablexpert
- nieskategoryzowany Roxio
- nieskategoryzowany WHALE
- nieskategoryzowany Noveen
- nieskategoryzowany GMB Gaming
- nieskategoryzowany Blade
- nieskategoryzowany Ipevo
- nieskategoryzowany Waldbeck
- nieskategoryzowany Fanvil
- nieskategoryzowany IHome
- nieskategoryzowany Waves
- nieskategoryzowany Satechi
- nieskategoryzowany Xaoc
- nieskategoryzowany Syma
- nieskategoryzowany Lanberg
- nieskategoryzowany Butler
- nieskategoryzowany Vankyo
- nieskategoryzowany Arovec
- nieskategoryzowany Adam Hall
- nieskategoryzowany Murr Elektronik
- nieskategoryzowany TDK-Lambda
- nieskategoryzowany Ciclo
- nieskategoryzowany Sonoff
- nieskategoryzowany SecureSafe
- nieskategoryzowany CubuSynth
- nieskategoryzowany Yorkville
- nieskategoryzowany Neewer
- nieskategoryzowany Omnires
- nieskategoryzowany Klavis
- nieskategoryzowany Manitowoc
- nieskategoryzowany Joranalogue
- nieskategoryzowany Aconatic
- nieskategoryzowany WyreStorm
- nieskategoryzowany Artecta
- nieskategoryzowany NordicTrack
- nieskategoryzowany Eliminator Lighting
- nieskategoryzowany Christmas Time
- nieskategoryzowany ColorKey
- nieskategoryzowany Apollo Design
- nieskategoryzowany ChyTV
- nieskategoryzowany JoeCo
- nieskategoryzowany Holosun
- nieskategoryzowany Nureva
- nieskategoryzowany Panamax
- nieskategoryzowany Sonifex
- nieskategoryzowany Vertex
- nieskategoryzowany ARC
- nieskategoryzowany FBT
- nieskategoryzowany Andover
- nieskategoryzowany Black Lion Audio
- nieskategoryzowany Manfrotto
- nieskategoryzowany Crucial
- nieskategoryzowany Titanwolf
- nieskategoryzowany Uplink
- nieskategoryzowany Mybeo
- nieskategoryzowany Medicinalis
- nieskategoryzowany CSL
- nieskategoryzowany Bearware
- nieskategoryzowany Liam&Daan
- nieskategoryzowany Traco Power
- nieskategoryzowany Perfect Christmas
- nieskategoryzowany Core SWX
- nieskategoryzowany Universal Audio
- nieskategoryzowany 8BitDo
- nieskategoryzowany PCE
- nieskategoryzowany Warm Audio
- nieskategoryzowany Drawmer
- nieskategoryzowany Velbus
- nieskategoryzowany AirTurn
- nieskategoryzowany Orava
- nieskategoryzowany Holzmann
- nieskategoryzowany Blizzard
- nieskategoryzowany Inverx
- nieskategoryzowany Scanstrut
- nieskategoryzowany Jinbei
- nieskategoryzowany Expressive E
- nieskategoryzowany Gra-Vue
- nieskategoryzowany SurgeX
- nieskategoryzowany MuxLab
- nieskategoryzowany NuTone
- nieskategoryzowany Heitronic
- nieskategoryzowany Pentagram
- nieskategoryzowany RTS
- nieskategoryzowany Ocean Matrix
- nieskategoryzowany MAK
- nieskategoryzowany Dobot
- nieskategoryzowany Ocean Way Audio
- nieskategoryzowany Nearity
- nieskategoryzowany LifeSpan
- nieskategoryzowany Multibrackets
- nieskategoryzowany Urbanista
- nieskategoryzowany Hecate
- nieskategoryzowany ADDAC System
- nieskategoryzowany Hurricane
- nieskategoryzowany Inverto
- nieskategoryzowany Kitchen Brains
- nieskategoryzowany Leotec
- nieskategoryzowany Solplanet
- nieskategoryzowany Alutruss
- nieskategoryzowany AVPro Edge
- nieskategoryzowany Uniropa
- nieskategoryzowany Synco
- nieskategoryzowany Christie
- nieskategoryzowany Peak Design
- nieskategoryzowany MIOPS
- nieskategoryzowany JMAZ Lighting
- nieskategoryzowany Edelkrone
- nieskategoryzowany Amaran
- nieskategoryzowany Hortus
- nieskategoryzowany Enttec
- nieskategoryzowany Defender
- nieskategoryzowany Hawke
- nieskategoryzowany Feelworld
- nieskategoryzowany Bellari
- nieskategoryzowany Altman
- nieskategoryzowany FoxFury
- nieskategoryzowany JK Audio
- nieskategoryzowany Betty Bossi
- nieskategoryzowany Eller
- nieskategoryzowany Grimm Audio
- nieskategoryzowany Rotatrim
- nieskategoryzowany Aguilar
- nieskategoryzowany Claypaky
- nieskategoryzowany ESE
- nieskategoryzowany Digitech
- nieskategoryzowany CAD Audio
- nieskategoryzowany Altrad
- nieskategoryzowany Black Hydra
- nieskategoryzowany Merging
- nieskategoryzowany Orange
- nieskategoryzowany Digigram
- nieskategoryzowany Renogy
- nieskategoryzowany UDG Gear
- nieskategoryzowany Mutec
- nieskategoryzowany SunBriteTV
- nieskategoryzowany DMT
- nieskategoryzowany ICC
Najnowsze instrukcje dla nieskategoryzowany

28 Października 2024

28 Października 2024

27 Października 2024

27 Października 2024

27 Października 2024

27 Października 2024

27 Października 2024

27 Października 2024

27 Października 2024

27 Października 2024