Instrukcja obsługi Microchip dsPIC33CK128MP208
Microchip
Niesklasyfikowane
dsPIC33CK128MP208
Przeczytaj poniżej 📖 instrukcję obsługi w języku polskim dla Microchip dsPIC33CK128MP208 (131 stron) w kategorii Niesklasyfikowane. Ta instrukcja była pomocna dla 14 osób i została oceniona przez 7.5 użytkowników na średnio 4.5 gwiazdek
Strona 1/131
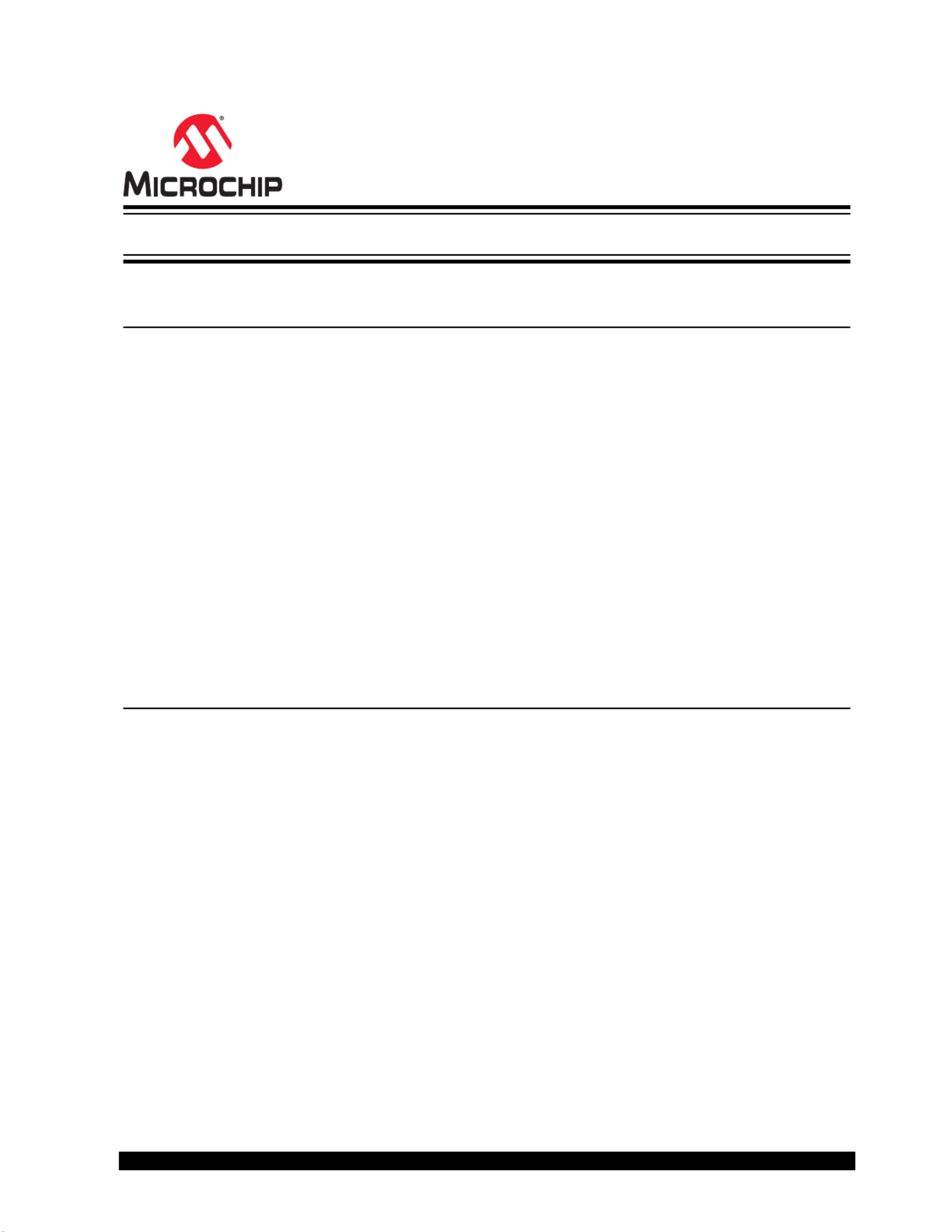
HRPWM with Fine Edge
Placement
dsPIC33/PIC24 Family Reference Manual
Introduction
Note: This family reference manual section is meant to serve as a complement to device data sheets. Depending on
the device variant, this manual section may not apply to all dsPIC33 devices. Please consult the note at the
beginning of the chapter in the specific device data sheet to check whether this document supports the device you
are using.
Device data sheets and family reference manual sections are available for download from the Microchip Worldwide
Website at: www.microchip.com.
This document describes the features and use of the High-Resolution Pulse-Width Modulated (PWM) with Fine Edge
Placement. This flexible module provides features to support many types of Motor Control (MC) and Power Control
(PC) applications, including:
• AC-to-DC Converters
• DC-to-DC Converters
• AC and DC Motor Control: Brushed DC, BLDC, PMSM, ACIM, SRM, Stepper, etc.
• Inverters
• Battery Chargers
• Digital Lighting
• Power Factor Correction (PFC)
High-Level Features
• Up to Eight Independent PWM Generators, each with Dual Outputs
• Operating modes:
– Independent Edge PWM mode
– Variable Phase PWM mode
– Independent Edge PWM mode, Dual Output
– Center-Aligned PWM mode
– Double Update Center-Aligned PWM mode
– Dual Edge Center-Aligned PWM mode
• Output modes:
– Complementary
– Independent
– Push-Pull
• Dead-Time Generator
• Dead-Time Compensation
• Leading-Edge Blanking (LEB)
• Output Override for Fault Handling
• Flexible Period/Duty Cycle Updating Options
• PWM Control Inputs (PCI) for PWM Pin Overrides and External PWM Synchronization
• Advanced Triggering Options
• Combinatorial Logic Output
© 2017-2020 Microchip Technology Inc. Functional Reference Manuals (FRM) DS70005320D-page 1
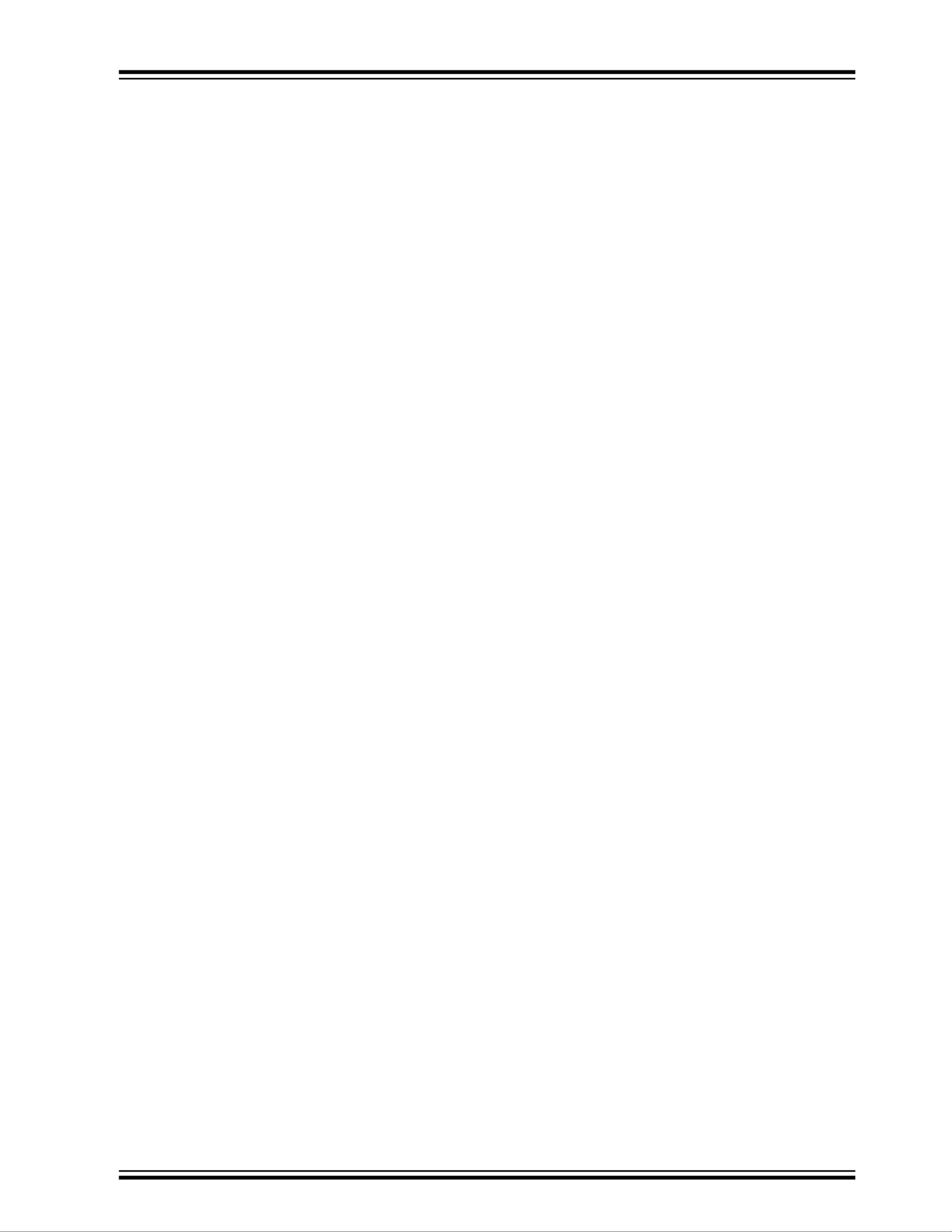
• PWM Event Outputs
HRPWM with Fine Edge Placement
© 2017-2020 Microchip Technology Inc. Functional Reference Manuals (FRM) DS70005320D-page 2
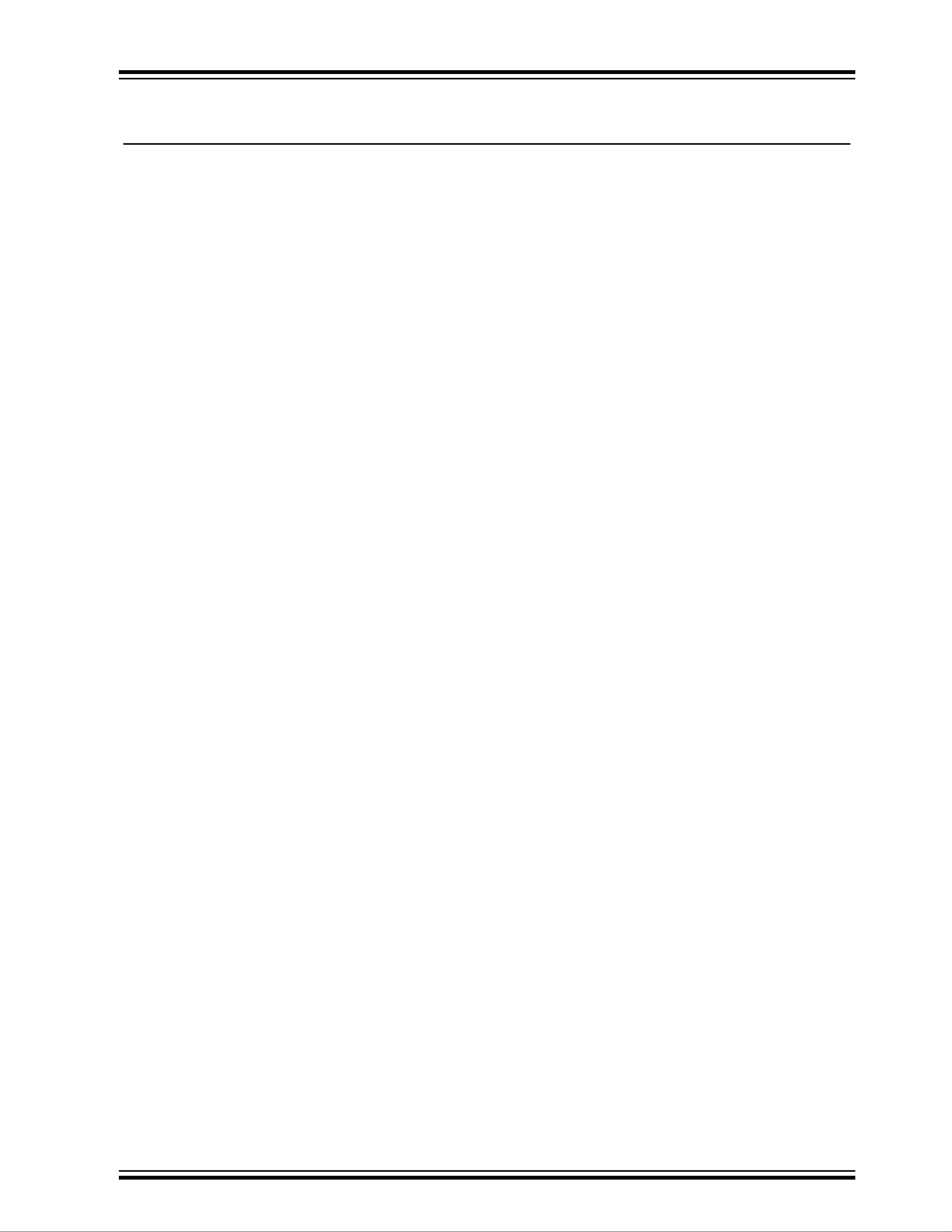
Table of Contents
Introduction.....................................................................................................................................................1
High-Level Features....................................................................................................................................... 1
1. Registers................................................................................................................................................. 5
2. Register Maps......................................................................................................................................... 6
2.1. Common Functions Register Map................................................................................................7
2.2. PWM Generator Register Map................................................................................................... 21
3. Architecture Overview...........................................................................................................................51
4. Operation.............................................................................................................................................. 54
4.1. PWM Clocking............................................................................................................................54
4.2. PWM Generator (PG) Features..................................................................................................59
4.3. Common Features......................................................................................................................95
4.4. Lock and Write Restrictions......................................................................................................100
5. Application Examples..........................................................................................................................105
5.1. Six-Step Commutation of Three-Phase BLDC Motor...............................................................105
5.2. Three-Phase Sinusoidal Control of PMSM/ACIM Motors.........................................................114
5.3. Simple Complementary PWM Output.......................................................................................117
5.4. Cycle-by-Cycle Current Limit Mode..........................................................................................118
5.5. External Period Reset Mode.................................................................................................... 120
6. Interrupts............................................................................................................................................. 123
7. Operation in Power-Saving Modes..................................................................................................... 124
7.1. Operation in Sleep Mode..........................................................................................................124
7.2. Operation in Idle Mode............................................................................................................. 124
8. Related Application Notes...................................................................................................................125
9. Revision History.................................................................................................................................. 126
9.1. Revision A (August 2017).........................................................................................................126
9.2. Revision B (February 2018)..................................................................................................... 126
9.3. Revision C (February 2019)..................................................................................................... 126
9.4. Revision D (December 2020)................................................................................................... 126
The Microchip Website...............................................................................................................................128
Product Change Notification Service..........................................................................................................128
Customer Support...................................................................................................................................... 128
Microchip Devices Code Protection Feature..............................................................................................128
Legal Notice............................................................................................................................................... 129
Trademarks................................................................................................................................................ 129
Quality Management System..................................................................................................................... 130
HRPWM with Fine Edge Placement
© 2017-2020 Microchip Technology Inc. Functional Reference Manuals (FRM) DS70005320D-page 3
Specyfikacje produktu
Marka: | Microchip |
Kategoria: | Niesklasyfikowane |
Model: | dsPIC33CK128MP208 |
Potrzebujesz pomocy?
Jeśli potrzebujesz pomocy z Microchip dsPIC33CK128MP208, zadaj pytanie poniżej, a inni użytkownicy Ci odpowiedzą
Instrukcje Niesklasyfikowane Microchip
15 Stycznia 2025
15 Stycznia 2025
15 Stycznia 2025
15 Stycznia 2025
15 Stycznia 2025
15 Stycznia 2025
15 Stycznia 2025
15 Stycznia 2025
15 Stycznia 2025
15 Stycznia 2025
Instrukcje Niesklasyfikowane
- Niesklasyfikowane Trumeter
- Niesklasyfikowane Healthy Choice
- Niesklasyfikowane Celexon
- Niesklasyfikowane Approx
- Niesklasyfikowane Stiebel Eltron
- Niesklasyfikowane Vermona Modular
- Niesklasyfikowane Bose
- Niesklasyfikowane 4ms
- Niesklasyfikowane Truma
- Niesklasyfikowane X-Sense
- Niesklasyfikowane Euro Cuisine
- Niesklasyfikowane Lümme
- Niesklasyfikowane EPH Elektronik
- Niesklasyfikowane Maturmeat
- Niesklasyfikowane Elite Force
Najnowsze instrukcje dla Niesklasyfikowane
29 Stycznia 2025
29 Stycznia 2025
29 Stycznia 2025
29 Stycznia 2025
29 Stycznia 2025
29 Stycznia 2025
29 Stycznia 2025
29 Stycznia 2025
29 Stycznia 2025
29 Stycznia 2025