Instrukcja obsługi AMX Epica DGX 288 Enclosure
AMX
nieskategoryzowany
Epica DGX 288 Enclosure
Przeczytaj poniżej 📖 instrukcję obsługi w języku polskim dla AMX Epica DGX 288 Enclosure (2 stron) w kategorii nieskategoryzowany. Ta instrukcja była pomocna dla 13 osób i została oceniona przez 2 użytkowników na średnio 4.5 gwiazdek
Strona 1/2
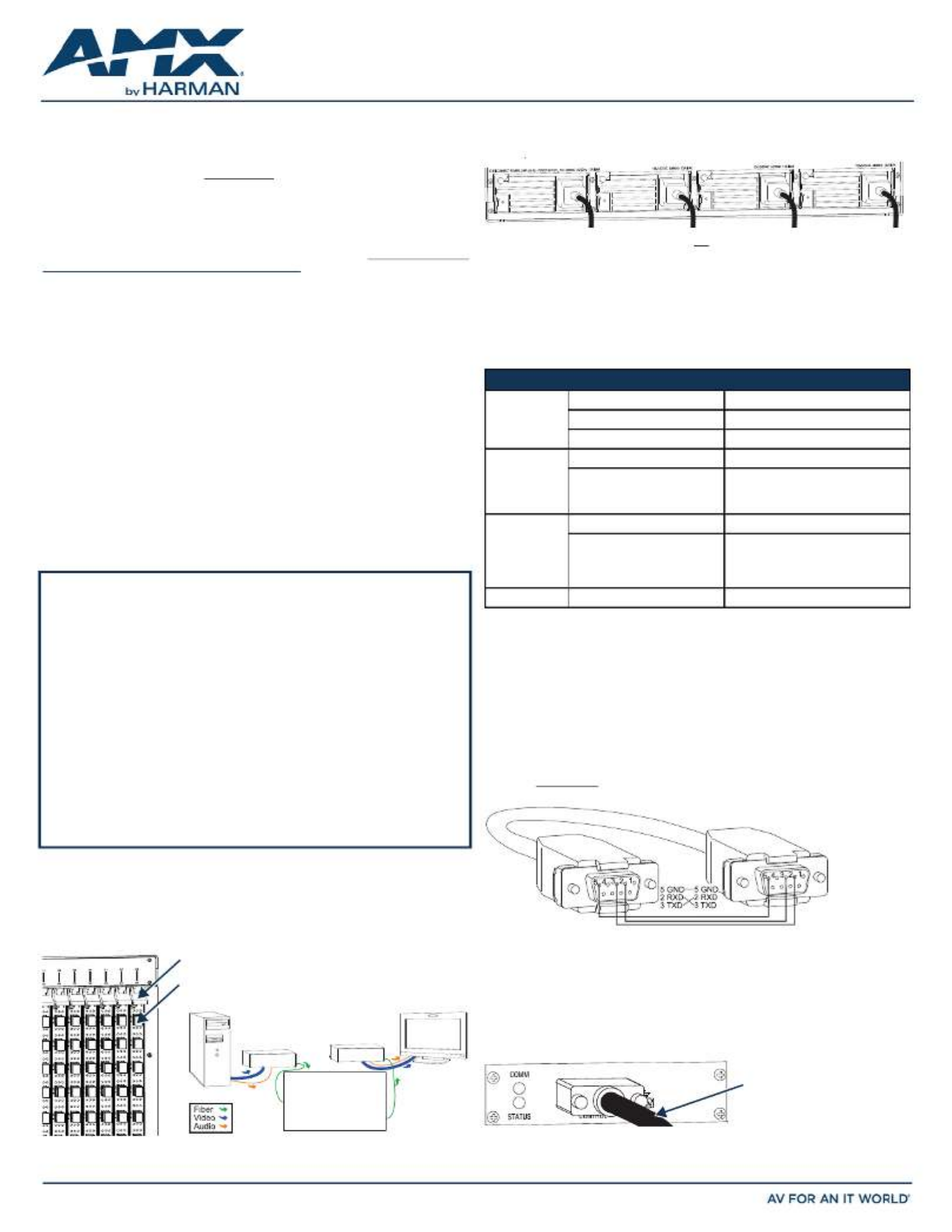
QUICK START GUIDE
Epica DGX 288 Matrix Switcher
Overview
The Epica DGX 288 Matrix Switcher with Simplex DXLink Fiber I/O Boards is
configurable by size up to 288 inputs/outputs. The Hardware Reference Manual – Epica
DGX 288 Matrix Switcher contains complete documentation (including specifications
and supported resolutions); visit www.amx.com.
Installation
IMPORTANT: This product must be installed within a restricted access location where
access is through the use of a tool, lock and key, or other means of security, and is
controlled by the authority responsible for the location. (This is due to access to
hazardous energy levels from power supplies if boards are removed.) This product must be
installed and maintained only by qualified technicians.
Rack Mounting
CAUTION: To prevent overheating, avoid placing high heat-producing equipment directly
above/below enclosure. The system requires a minimum of 2 empty rack units above.
Verify that the openings on top, front, and sides of enclosure are not blocked and do not
have restricted airflow.
To rack mount the enclosure (requires a minimum of 3 people):
1. While the shipping box containing the enclosure is still on the pallet, cut loose and
remove the outer straps.
2. Remove the cardboard tray from the top of the reusable shipping box.
(The shipping box is mounted on wheels.)
3. Lift the shipping box off of the pallet and unlock the 4 latches on the box’s sides.
4. Lift the top of the shipping box straight up and over the enclosure and set aside.
5. Using the bottom of the shipping box, roll the enclosure into position.
IMPORTANT: Do not use board extractor handles (FIG. 1) to lift or maneuver enclosure.
6. Using the hand-hold insets on the sides of the enclosure, lift and push the
enclosure into the rack. Screw in 4 rack ear screws on each side, spread evenly.
7. Supporting the enclosure as needed, screw in the remaining rack ear screws.
CAUTION: For Input/Output boards, we recommend using cable management bars or
some other type of cable management system to avoid damage to fiber cables.
Safety Recommendations for Laser Products
WARNING: DXLink Fiber units use laser transceivers, which are Class 1 Eye Safe per
IEC 60825-1/CDRH requirements. While the Class 1 category indicates that the
invisible laser used is safe, we recommend avoiding direct eye exposure when using
any optical fiber products (see the OSHA directive in the product’s manual).
CAUTION: Use of controls or adjustments or performance of procedures other than those
specified herein may result in hazardous radiation exposure.
Exercise caution to avoid direct eye exposure to invisible laser radiation. Follow the
recommendations below whenever installing or working with fiber products.
Be sure to apply the power only after all fiber connections are made and no fiber
ends are exposed.
Do remove dust plugs from fiber connectors or the dust caps from the fiber not
cables until establishing connections; avoid direct eye exposure.
Make sure all cables, including fiber cables, are correctly connected and/or
terminated.
Before you unplug a fiber cable on an input port, disconnect the power on the
Transmitter that is connected to the input.
Before you unplug a fiber cable on an output port, disconnect the switch for that
output.
CAUTION: Do not severely bend or kink the fiber cable. Irreversible damage can occur.
Refer to the physical limitations specified for the cable.
DXLink Fiber, Simplex Input/Output Boards – Transceiver Ports
The Simplex DXLink Fiber boards support Simplex or Duplex DXLink Fiber TXs and RXs;
see applicable Quick Start Guide for details. Each board contains 16 fiber transceivers
with one pair of IN/OUT ports per transceiver for connection to the appropriate Fiber
TX or RX. Set up units according to the directions in their Quick Start Guide, installing a
TX between each IN port and source device and an RX between each OUT port and
destination device (FIG. 1).
Applying Power and Control Startup
To apply power simultaneously to power supplies:
1. Plug power cords into all power receptacles.
2. Plug the other ends of the power cords into power sources (via surge protector or
line conditioner).
3. Turn on the power to all and wait until the system status indicator flashes green.
4. Check the Indicator LEDs on front and rear of the enclosure; see table below.
5. Apply power to endpoints and the source and destination devices.
If indicator lights do not respond with a normal display as stated in the table below,
check power connections and see the troubleshooting information in the manual before
contacting technical support.
Establishing Serial Control
The Epica DGX 288 can be controlled by attaching an external control device/system to
the serial port (DB-9 connector) or to the USB port* (USB Mini-B connector).
* Controlling the Epica DGX 288 using a USB connection requires the creation of a virtual COM
port, which acts as a serial port.
PC Requirements for BCS** via Terminal Emulator:
• Windows 7® or later
• Serial port or USB port
** For information on BCS (Basic Control Structure), a programming language used for
programming control operations and for diagnostic purposes, see the Programming Guide – BCS
Protocol at www.amx.com.
Serial Port – Serial Control (PCs, AMX control devices, & third-party controllers)
To establish external serial control from serial port for RS-232:
1. Apply power to the Epica DGX 288 (see previous page).
2. Plug the null modem cable into the serial port on the enclosure (FIG. 4 and 5).
3. Plug the other end of the cable into the serial port on the serial controller/device.
4. Open the serial communication software and set port settings to match the Epica
DGX 288 default settings:
baud rate = 9600, data bits = 8, stop bit = 1, parity = none, flow control = none.
FIG. 1 FASTEN FIBER CABLES TO INPUT AND OUTPUT PORTS
DXLink Fiber, Simplex port
(remove plug to attach cable)
System Setup
DXLink Fiber Input
DXLink Fiber Output
Epica DGX Switcher
DXLink Fiber TX DXLink Fiber RX
Board extractor handle
FIG. 2 POWER CORDS MUST BE PLUGGED INTO ALL POWER RECEPTACLES
INDICATOR LEDS – NORMAL DISPLAY
Front Panel POWER – power status Green
RPS – redundant power supplies Green
COMM – communication status Reserved for future functionality
Power Supplies
(DC is Tri-color)
AC Power Green
• DC Power
• Temperature
• Fault status
Green
(amber = over temperature;
red = fault state)
CPU COMM – communication status Reserved for future functionality
STATUS Green during boot up
(approx. 10 to 30 seconds, depending
on load)
Blinking green when ready
Rear Fan Tray Fan speed status Green – Fan RPS within normal range
FIG. 3 RS-232 NULL MODEM CABLE PIN DIAGRAM
FIG. 4 ATTACH NULL MODEM SERIAL CABLE TO DB-9 SERIAL PORT
AC
DC
FLT
AC
DC
FLT
AC
DC
FLT
AC
DC
FLT
PC: DB-9 AMX: DB-9
Null modem serial cable
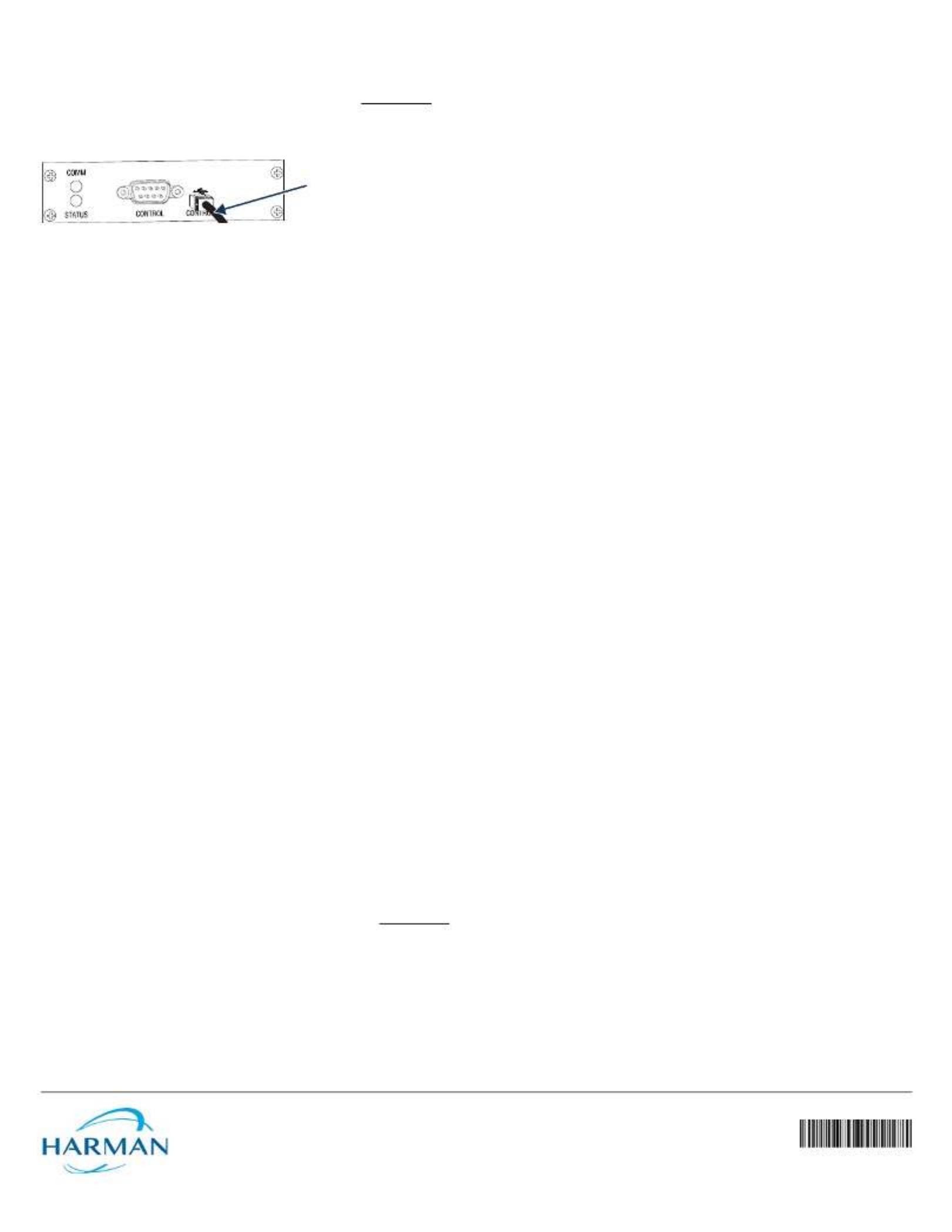
© 2016 Harman. All rights reserved. SmartScale, NetLinx, Epica, AMX, AV FOR AN IT WORLD, and HARMAN, and their respective logos are
registered trademarks of HARMAN. Oracle, Java and any other company or brand name referenced may be trademarks/registered trademarks of
their respective companies.
AMX does not assume responsibility for errors or omissions. AMX also reserves the right to alter specifications without prior notice at any time.
The AMX Warranty and Return Policy and related documents can be viewed/downloaded at www.amx.com.
3000 RESEARCH DRIVE, RICHARDSON, TX 75082 AMX.com | 800.222.0193 | 469.624.8000 | +1.469.624.7400 | fax 469.624.7153
AMX (UK) LTD, AMX by HARMAN - Unit C, Auster Road, Clifton Moor, York, YO30 4GD United Kingdom • +44 1904-343-100 • www.amx.com/eu/
93-1055-001 REV: A
A
Last Revised: 10/05/2016
To establish external serial control from USB (Mini-B) port:
IMPORTANT:
You must have adequate rights for the PC to install a USB driver. Check with
your System Administrator to be sure you have the required access.
1. Download the APBridge.inf hardware device driver file from www.amx.com.
2. Apply power to the Epica DGX 288 (see instructions on previous page).
3. Plug one end of the USB cable into the USB (Mini-B) port on the enclosure and the
other end to the USB port on the PC.
IMPORTANT:
You must identify the virtual COM port assigned to the USB connector to
enable communication between the control application on the PC and the enclosure.
4. Open the Device Manager window (Start/Control Panel/ Device Manager), open
Other devices and right-click on the Unknown device icon.
Select Properties from the menu items. The Unknown device Properties window
opens.
The Device Manager may have a different location depending on the operating system
and theme selected.
5. In the driver tab, select the Update Driver button.
6. Browse for the APBridge.inf file and select the Next button. Another Update Driver
Software window appears. Click Close.
A Windows Security window may open and ask if you wish to install a driver with an
unverified publisher. Select the “Install this driver software anyway” option.
7. Make note of AutoPatch USB Bridge COM port number in Device Manager window.
(If port number doesn’t show, right click and check Properties.
This port number will remain the same unless a different USB port is used on the PC or a
different device is attached to the PC through this USB port.
8. Open the control application.
When establishing communication between the control application on the PC and the
Epica DGX 288, be sure to check application’s serial port settings and select correct
virtual COM port for AutoPatch USB Bridge. Epica DGX 288 default settings are:
baud rate = 9600, data bits = 8, stop bit = 1, parity = none, and flow control = none.
Completing the Installation
We recommend completing the installation by executing a test switch routing Input 1 to
Output 2. Connect a DXLink Fiber TX to the IN port of Input 1 and a DXLink Fiber RX to
the OUT port of Output 2. The method of executing the switch will depend on the
control option used. Control options and switching information are provided below.
• BCS Commands (via terminal emulator such as TeraTerm, PuTTY, or
HyperTerminal) – When power is applied, a short splash screen appears. Enter
CI1O2T into the terminal emulation program (routes Input 1 to Output 2 on the
default level). When appears, the switch is successful.CI1O2T
• AMX Control Devices – The Epica DGX 288 is compatible with a number of AMX
control devices. For control programming information, see the Hardware
Reference Manual for the specific device.
The system is now ready to attach the remaining source and destination devices and
any applicable DXLink Fiber Transmitters and Receivers.
Basic BCS Commands
To execute a switch:
CL#I#O#T CL#O#I#T or
To disconnect a switch:
DL#I#T DL#O#T or
To verify switch status:
SL#O#T SL#I#T or The result is in , e.g., ( ) SL0O3T(12)
Additional Information in the switcher’s Hardware Reference Manual
See the Epica DGX 288 Matrix Switcher Hardware Reference Manual at www.amx.com for
information on the following:
• System and board specifications
• APDiagnostics software (monitors/displays advanced diagnostic data)
• Redundant power supplies
• Adding or replacing boards
FIG. 5 ATTACH USB CABLE TO USB (MINI-B) PORT
USB cable
Specyfikacje produktu
Marka: | AMX |
Kategoria: | nieskategoryzowany |
Model: | Epica DGX 288 Enclosure |
Potrzebujesz pomocy?
Jeśli potrzebujesz pomocy z AMX Epica DGX 288 Enclosure, zadaj pytanie poniżej, a inni użytkownicy Ci odpowiedzą
Instrukcje nieskategoryzowany AMX

2 Sierpnia 2024

2 Sierpnia 2024

2 Sierpnia 2024

2 Sierpnia 2024

2 Sierpnia 2024

2 Sierpnia 2024

2 Sierpnia 2024

10 Lipca 2024

10 Lipca 2024

21 Czerwca 2024
Instrukcje nieskategoryzowany
- nieskategoryzowany Sony
- nieskategoryzowany Bauknecht
- nieskategoryzowany Yamaha
- nieskategoryzowany Ikea
- nieskategoryzowany Hoshizaki
- nieskategoryzowany Samsung
- nieskategoryzowany Tesy
- nieskategoryzowany PeakTech
- nieskategoryzowany Bertazzoni
- nieskategoryzowany Electrolux
- nieskategoryzowany Gamdias
- nieskategoryzowany Tenda
- nieskategoryzowany DeLonghi
- nieskategoryzowany AEG
- nieskategoryzowany Fellowes
- nieskategoryzowany Balay
- nieskategoryzowany Leica
- nieskategoryzowany Beko
- nieskategoryzowany Teka
- nieskategoryzowany Sven
- nieskategoryzowany ChamSys
- nieskategoryzowany LG
- nieskategoryzowany Worx
- nieskategoryzowany Küppersbusch
- nieskategoryzowany Smeg
- nieskategoryzowany Motorola
- nieskategoryzowany Götze & Jensen
- nieskategoryzowany Dreame
- nieskategoryzowany Beurer
- nieskategoryzowany Stabo
- nieskategoryzowany Logitech
- nieskategoryzowany Gram
- nieskategoryzowany Spektrum
- nieskategoryzowany Xiaomi
- nieskategoryzowany Gorenje
- nieskategoryzowany Etna
- nieskategoryzowany Joy-It
- nieskategoryzowany LERAN
- nieskategoryzowany President
- nieskategoryzowany MyPhone
- nieskategoryzowany Sharp
- nieskategoryzowany BeamZ
- nieskategoryzowany Huawei
- nieskategoryzowany Supermicro
- nieskategoryzowany TCL
- nieskategoryzowany Braun
- nieskategoryzowany Russell Hobbs
- nieskategoryzowany Pioneer
- nieskategoryzowany Statron
- nieskategoryzowany Sage
- nieskategoryzowany Lenovo
- nieskategoryzowany Tefal
- nieskategoryzowany Honda
- nieskategoryzowany TP-Link
- nieskategoryzowany Voltcraft
- nieskategoryzowany Milwaukee
- nieskategoryzowany Philips
- nieskategoryzowany Livoo
- nieskategoryzowany SilverCrest
- nieskategoryzowany Simpson
- nieskategoryzowany Dometic
- nieskategoryzowany Gigabyte
- nieskategoryzowany Acer
- nieskategoryzowany Realme
- nieskategoryzowany Ultimate Speed
- nieskategoryzowany Stihl
- nieskategoryzowany Bosch
- nieskategoryzowany Yato
- nieskategoryzowany Xblitz
- nieskategoryzowany Epson
- nieskategoryzowany JBL
- nieskategoryzowany Parkside
- nieskategoryzowany Hikvision
- nieskategoryzowany Candy
- nieskategoryzowany GW Instek
- nieskategoryzowany Onkyo
- nieskategoryzowany Whirlpool
- nieskategoryzowany Grillmeister
- nieskategoryzowany IPGARD
- nieskategoryzowany Fujitsu
- nieskategoryzowany Ferroli
- nieskategoryzowany Thule
- nieskategoryzowany Roland
- nieskategoryzowany Miele
- nieskategoryzowany HyperX
- nieskategoryzowany Easy Home
- nieskategoryzowany LC-Power
- nieskategoryzowany Waterco
- nieskategoryzowany Geemarc
- nieskategoryzowany Scott
- nieskategoryzowany Brentwood
- nieskategoryzowany Midea
- nieskategoryzowany KEF
- nieskategoryzowany Festool
- nieskategoryzowany Kärcher
- nieskategoryzowany Bose
- nieskategoryzowany Severin
- nieskategoryzowany Hisense
- nieskategoryzowany Berg
- nieskategoryzowany Infiniton
- nieskategoryzowany EZVIZ
- nieskategoryzowany Conceptronic
- nieskategoryzowany Panasonic
- nieskategoryzowany StarTech.com
- nieskategoryzowany Promethean
- nieskategoryzowany Bavaria By Einhell
- nieskategoryzowany Theben
- nieskategoryzowany Liebherr
- nieskategoryzowany Canon
- nieskategoryzowany Mio
- nieskategoryzowany Crestron
- nieskategoryzowany Truetone
- nieskategoryzowany Bestway
- nieskategoryzowany Viewsonic
- nieskategoryzowany Behringer
- nieskategoryzowany Asus
- nieskategoryzowany Nedis
- nieskategoryzowany Stanley
- nieskategoryzowany Nexa
- nieskategoryzowany Jura
- nieskategoryzowany AG Neovo
- nieskategoryzowany Be Cool
- nieskategoryzowany Allen & Heath
- nieskategoryzowany Enphase
- nieskategoryzowany IK Multimedia
- nieskategoryzowany Reolink
- nieskategoryzowany American DJ
- nieskategoryzowany Medion
- nieskategoryzowany Tangent
- nieskategoryzowany Boss
- nieskategoryzowany Black & Decker
- nieskategoryzowany OK
- nieskategoryzowany Lenco
- nieskategoryzowany TRENDnet
- nieskategoryzowany Audioline
- nieskategoryzowany Max Pro
- nieskategoryzowany Scheppach
- nieskategoryzowany Fujifilm
- nieskategoryzowany Proxxon
- nieskategoryzowany Adler
- nieskategoryzowany Bluetti
- nieskategoryzowany BaByliss
- nieskategoryzowany Marquant
- nieskategoryzowany Subaru
- nieskategoryzowany MSI
- nieskategoryzowany Hoover
- nieskategoryzowany Tesla
- nieskategoryzowany Westinghouse
- nieskategoryzowany D-Link
- nieskategoryzowany Hendi
- nieskategoryzowany Jensen
- nieskategoryzowany Niceboy
- nieskategoryzowany Hazet
- nieskategoryzowany Vertiv
- nieskategoryzowany Conair
- nieskategoryzowany GE
- nieskategoryzowany ILive
- nieskategoryzowany Ardes
- nieskategoryzowany Taurus
- nieskategoryzowany VitalMaxx
- nieskategoryzowany RIKON
- nieskategoryzowany Ring
- nieskategoryzowany Orbegozo
- nieskategoryzowany Native Instruments
- nieskategoryzowany Garmin
- nieskategoryzowany Blaupunkt
- nieskategoryzowany Vivax
- nieskategoryzowany ATen
- nieskategoryzowany IOptron
- nieskategoryzowany Grizzly
- nieskategoryzowany Salora
- nieskategoryzowany Siemens
- nieskategoryzowany Teac
- nieskategoryzowany Speed-Link
- nieskategoryzowany Casio
- nieskategoryzowany Iiyama
- nieskategoryzowany Lincoln Electric
- nieskategoryzowany Metra
- nieskategoryzowany Thrustmaster
- nieskategoryzowany Evolveo
- nieskategoryzowany Ambiano
- nieskategoryzowany DeWalt
- nieskategoryzowany Bbf
- nieskategoryzowany Danby
- nieskategoryzowany Martin Logan
- nieskategoryzowany Dual
- nieskategoryzowany Einhell
- nieskategoryzowany Grundig
- nieskategoryzowany APC
- nieskategoryzowany Hegel
- nieskategoryzowany Kiloview
- nieskategoryzowany Haier
- nieskategoryzowany Sigma
- nieskategoryzowany Homedics
- nieskategoryzowany Remington
- nieskategoryzowany HP
- nieskategoryzowany KKT Kolbe
- nieskategoryzowany Cylinda
- nieskategoryzowany S.M.S.L
- nieskategoryzowany Genesis
- nieskategoryzowany Jocel
- nieskategoryzowany Soundmaster
- nieskategoryzowany Hyundai
- nieskategoryzowany Silverline
- nieskategoryzowany Blomberg
- nieskategoryzowany Line 6
- nieskategoryzowany Husqvarna
- nieskategoryzowany Honeywell
- nieskategoryzowany BLOW
- nieskategoryzowany DAP-Audio
- nieskategoryzowany Concept
- nieskategoryzowany Joie
- nieskategoryzowany Manhattan
- nieskategoryzowany Chauvet
- nieskategoryzowany Microchip
- nieskategoryzowany Heritage Audio
- nieskategoryzowany Fisher & Paykel
- nieskategoryzowany Angelcare
- nieskategoryzowany Cotek
- nieskategoryzowany Durvet
- nieskategoryzowany Tripp Lite
- nieskategoryzowany Shure
- nieskategoryzowany EWON
- nieskategoryzowany ECG
- nieskategoryzowany IRobot
- nieskategoryzowany Indesit
- nieskategoryzowany Matsui
- nieskategoryzowany Amazfit
- nieskategoryzowany Steinel
- nieskategoryzowany Makita
- nieskategoryzowany Ilve
- nieskategoryzowany Mikrotik
- nieskategoryzowany Denon
- nieskategoryzowany Akasa
- nieskategoryzowany Perkins
- nieskategoryzowany Swann
- nieskategoryzowany Truma
- nieskategoryzowany Kwikset
- nieskategoryzowany Mercury
- nieskategoryzowany Empress Effects
- nieskategoryzowany Carel
- nieskategoryzowany Nikon
- nieskategoryzowany Shimano
- nieskategoryzowany Viking
- nieskategoryzowany Antari
- nieskategoryzowany Medela
- nieskategoryzowany Block
- nieskategoryzowany Ozito
- nieskategoryzowany Kodak
- nieskategoryzowany Phoenix Gold
- nieskategoryzowany Forza
- nieskategoryzowany CATA
- nieskategoryzowany Testo
- nieskategoryzowany Audac
- nieskategoryzowany Cisco
- nieskategoryzowany Revic
- nieskategoryzowany Primera
- nieskategoryzowany Draper
- nieskategoryzowany Aim TTi
- nieskategoryzowany Fuxtec
- nieskategoryzowany ORNO
- nieskategoryzowany Cooler Master
- nieskategoryzowany Sanus
- nieskategoryzowany TFA
- nieskategoryzowany Dyson
- nieskategoryzowany Chauvin Arnoux
- nieskategoryzowany Hotpoint
- nieskategoryzowany Kenwood
- nieskategoryzowany Scosche
- nieskategoryzowany Icy Box
- nieskategoryzowany Sungrow
- nieskategoryzowany NuPrime
- nieskategoryzowany Hasbro
- nieskategoryzowany Moxa
- nieskategoryzowany Trisa
- nieskategoryzowany DJI
- nieskategoryzowany RYOBI
- nieskategoryzowany Kugoo
- nieskategoryzowany Alpine
- nieskategoryzowany Wolf Garten
- nieskategoryzowany Knog
- nieskategoryzowany Gembird
- nieskategoryzowany Scala
- nieskategoryzowany ZTE
- nieskategoryzowany Godox
- nieskategoryzowany Røde
- nieskategoryzowany Zelmer
- nieskategoryzowany Hammersmith
- nieskategoryzowany Chicco
- nieskategoryzowany Chamberlain
- nieskategoryzowany Paradigm
- nieskategoryzowany Lindy
- nieskategoryzowany Olivetti
- nieskategoryzowany Ninja
- nieskategoryzowany Medisana
- nieskategoryzowany Minox
- nieskategoryzowany Cuisinart
- nieskategoryzowany Zebra
- nieskategoryzowany Wilfa
- nieskategoryzowany DSC
- nieskategoryzowany Cobra
- nieskategoryzowany JVC
- nieskategoryzowany ZyXEL
- nieskategoryzowany Auriol
- nieskategoryzowany Konig & Meyer
- nieskategoryzowany Trust
- nieskategoryzowany BLUEPALM
- nieskategoryzowany V7
- nieskategoryzowany Thor
- nieskategoryzowany LogiLink
- nieskategoryzowany Handy
- nieskategoryzowany Memphis Audio
- nieskategoryzowany Sandisk
- nieskategoryzowany Grohe
- nieskategoryzowany Dell
- nieskategoryzowany Polaris
- nieskategoryzowany GLORIA
- nieskategoryzowany IFM
- nieskategoryzowany Krups
- nieskategoryzowany Furrion
- nieskategoryzowany U-Line
- nieskategoryzowany Linksys
- nieskategoryzowany Moulinex
- nieskategoryzowany Cleanmaxx
- nieskategoryzowany Ursus Trotter
- nieskategoryzowany DEDRA
- nieskategoryzowany Corsair
- nieskategoryzowany Emerio
- nieskategoryzowany Owon
- nieskategoryzowany Focusrite
- nieskategoryzowany Baumr-AG
- nieskategoryzowany Patriot
- nieskategoryzowany Google
- nieskategoryzowany Create
- nieskategoryzowany Rega
- nieskategoryzowany Intex
- nieskategoryzowany Biltema
- nieskategoryzowany Oricom
- nieskategoryzowany B.E.G.
- nieskategoryzowany H.Koenig
- nieskategoryzowany MyPOS
- nieskategoryzowany CMI
- nieskategoryzowany Hilti
- nieskategoryzowany Steelseries
- nieskategoryzowany Digitus
- nieskategoryzowany Salewa
- nieskategoryzowany Oppo
- nieskategoryzowany Alesis
- nieskategoryzowany Lowrance
- nieskategoryzowany Anybus
- nieskategoryzowany Melissa
- nieskategoryzowany TechniSat
- nieskategoryzowany Vimar
- nieskategoryzowany Nubert
- nieskategoryzowany Dahua Technology
- nieskategoryzowany Schneider
- nieskategoryzowany Deutz
- nieskategoryzowany SABO
- nieskategoryzowany Ledlenser
- nieskategoryzowany Beper
- nieskategoryzowany Eurolite
- nieskategoryzowany LD Systems
- nieskategoryzowany Techno Line
- nieskategoryzowany Foppapedretti
- nieskategoryzowany Daikin
- nieskategoryzowany Kospel
- nieskategoryzowany EVOline
- nieskategoryzowany Kubota
- nieskategoryzowany Thetford
- nieskategoryzowany Oehlbach
- nieskategoryzowany TrueLife
- nieskategoryzowany Eufy
- nieskategoryzowany Ricoh
- nieskategoryzowany TOGU
- nieskategoryzowany SMART Technologies
- nieskategoryzowany NZXT
- nieskategoryzowany Audioengine
- nieskategoryzowany Hozelock
- nieskategoryzowany OneConcept
- nieskategoryzowany CDA
- nieskategoryzowany Emos
- nieskategoryzowany Sabrent
- nieskategoryzowany AVMATRIX
- nieskategoryzowany IMC Toys
- nieskategoryzowany Philco
- nieskategoryzowany Neff
- nieskategoryzowany Seiko
- nieskategoryzowany Renkforce
- nieskategoryzowany Rollei
- nieskategoryzowany Corbero
- nieskategoryzowany Zanussi
- nieskategoryzowany Sonel
- nieskategoryzowany NightStick
- nieskategoryzowany Instant
- nieskategoryzowany Crivit
- nieskategoryzowany Marshall
- nieskategoryzowany Osram
- nieskategoryzowany BaseTech
- nieskategoryzowany Thermex
- nieskategoryzowany Traxxas
- nieskategoryzowany Viessmann
- nieskategoryzowany Perel
- nieskategoryzowany Wagner
- nieskategoryzowany Fagor
- nieskategoryzowany GoldAir
- nieskategoryzowany Sena
- nieskategoryzowany Graco
- nieskategoryzowany Trotec
- nieskategoryzowany Autel
- nieskategoryzowany Uniden
- nieskategoryzowany Adder
- nieskategoryzowany Ansmann
- nieskategoryzowany Clarion
- nieskategoryzowany Netgear
- nieskategoryzowany Cellular Line
- nieskategoryzowany Thomson
- nieskategoryzowany DiO
- nieskategoryzowany Pro-Ject
- nieskategoryzowany Texas Instruments
- nieskategoryzowany Lastolite
- nieskategoryzowany AVM
- nieskategoryzowany La Crosse Technology
- nieskategoryzowany Growatt
- nieskategoryzowany Izzy
- nieskategoryzowany Little Tikes
- nieskategoryzowany Chipolino
- nieskategoryzowany Velleman
- nieskategoryzowany Ferguson
- nieskategoryzowany BT
- nieskategoryzowany Meec Tools
- nieskategoryzowany Fusion
- nieskategoryzowany BOYA
- nieskategoryzowany WMF
- nieskategoryzowany Korg
- nieskategoryzowany ProfiCook
- nieskategoryzowany Homematic IP
- nieskategoryzowany DataVideo
- nieskategoryzowany One For All
- nieskategoryzowany Klarstein
- nieskategoryzowany Safety 1st
- nieskategoryzowany Polti
- nieskategoryzowany Totolink
- nieskategoryzowany Danfoss
- nieskategoryzowany JYSK
- nieskategoryzowany Coyote
- nieskategoryzowany Intertechno
- nieskategoryzowany Black Box
- nieskategoryzowany Lowepro
- nieskategoryzowany Güde
- nieskategoryzowany Arendo
- nieskategoryzowany DreamGEAR
- nieskategoryzowany Victron Energy
- nieskategoryzowany Delta Dore
- nieskategoryzowany E-ast
- nieskategoryzowany Manta
- nieskategoryzowany Pyle
- nieskategoryzowany CTA Digital
- nieskategoryzowany Segway
- nieskategoryzowany Gem Toys
- nieskategoryzowany Texas
- nieskategoryzowany Lancom
- nieskategoryzowany Adviti
- nieskategoryzowany Crimson
- nieskategoryzowany Dymo
- nieskategoryzowany ATIKA
- nieskategoryzowany Hauck
- nieskategoryzowany Iogear
- nieskategoryzowany Cardo
- nieskategoryzowany Panduit
- nieskategoryzowany Intellinet
- nieskategoryzowany NGS
- nieskategoryzowany CRUX
- nieskategoryzowany Newline
- nieskategoryzowany Bavaria
- nieskategoryzowany Devolo
- nieskategoryzowany Juwel
- nieskategoryzowany Biostar
- nieskategoryzowany Dirt Devil
- nieskategoryzowany Midland
- nieskategoryzowany Marantz
- nieskategoryzowany KitchenAid
- nieskategoryzowany MARTOR
- nieskategoryzowany AFK
- nieskategoryzowany AOC
- nieskategoryzowany Monster
- nieskategoryzowany Sennheiser
- nieskategoryzowany EchoMaster
- nieskategoryzowany JANDY
- nieskategoryzowany Esoteric
- nieskategoryzowany Roidmi
- nieskategoryzowany Zipper
- nieskategoryzowany Vivotek
- nieskategoryzowany Eta
- nieskategoryzowany Mount-It!
- nieskategoryzowany Camry
- nieskategoryzowany Steba
- nieskategoryzowany Werma
- nieskategoryzowany Peerless-AV
- nieskategoryzowany Speco Technologies
- nieskategoryzowany Suunto
- nieskategoryzowany Showtec
- nieskategoryzowany Weber
- nieskategoryzowany Heckler Design
- nieskategoryzowany Lenoxx
- nieskategoryzowany Grundfos
- nieskategoryzowany Samson
- nieskategoryzowany EtiamPro
- nieskategoryzowany Faworyt
- nieskategoryzowany EA Elektro Automatik
- nieskategoryzowany Imperial
- nieskategoryzowany Helios
- nieskategoryzowany Scarlett
- nieskategoryzowany Microlife
- nieskategoryzowany PreSonus
- nieskategoryzowany Mercusys
- nieskategoryzowany Koss
- nieskategoryzowany Audio Pro
- nieskategoryzowany I-TEC
- nieskategoryzowany ARRI
- nieskategoryzowany Gossen Metrawatt
- nieskategoryzowany Sôlt
- nieskategoryzowany Eden
- nieskategoryzowany Fosi Audio
- nieskategoryzowany TC Electronic
- nieskategoryzowany Shelly
- nieskategoryzowany Revox
- nieskategoryzowany Fluke
- nieskategoryzowany Nevir
- nieskategoryzowany Kindermann
- nieskategoryzowany Megger
- nieskategoryzowany Kayser
- nieskategoryzowany Olympus
- nieskategoryzowany Navitel
- nieskategoryzowany Greisinger
- nieskategoryzowany MTD
- nieskategoryzowany Oliveri
- nieskategoryzowany Musical Fidelity
- nieskategoryzowany Master Lock
- nieskategoryzowany Bogen
- nieskategoryzowany Pulsar
- nieskategoryzowany PATLITE
- nieskategoryzowany Exquisit
- nieskategoryzowany Bartscher
- nieskategoryzowany Schaudt
- nieskategoryzowany Phanteks
- nieskategoryzowany Hestan
- nieskategoryzowany Gastroback
- nieskategoryzowany GYS
- nieskategoryzowany Mitsubishi
- nieskategoryzowany Edimax
- nieskategoryzowany Razer
- nieskategoryzowany Dimplex
- nieskategoryzowany Florabest
- nieskategoryzowany Harvia
- nieskategoryzowany Baxi
- nieskategoryzowany ADATA
- nieskategoryzowany Kidde
- nieskategoryzowany Chief
- nieskategoryzowany Peavey
- nieskategoryzowany GoClever
- nieskategoryzowany Baby Lock
- nieskategoryzowany Dehner
- nieskategoryzowany ION
- nieskategoryzowany Camille Bauer
- nieskategoryzowany Huion
- nieskategoryzowany Arçelik
- nieskategoryzowany ART
- nieskategoryzowany First Alert
- nieskategoryzowany Assa Abloy
- nieskategoryzowany Solo
- nieskategoryzowany Continental Edison
- nieskategoryzowany RCF
- nieskategoryzowany Topmove
- nieskategoryzowany Delta
- nieskategoryzowany Kerbl
- nieskategoryzowany Zhiyun
- nieskategoryzowany Gree
- nieskategoryzowany Fluval
- nieskategoryzowany Bissell
- nieskategoryzowany Rolls
- nieskategoryzowany Audio-Technica
- nieskategoryzowany Maginon
- nieskategoryzowany EnGenius
- nieskategoryzowany Atag
- nieskategoryzowany Rosieres
- nieskategoryzowany Franke
- nieskategoryzowany Planet
- nieskategoryzowany Adidas
- nieskategoryzowany GoGen
- nieskategoryzowany Accu-Chek
- nieskategoryzowany RCBS
- nieskategoryzowany Peg Perego
- nieskategoryzowany NEC
- nieskategoryzowany Brandson
- nieskategoryzowany Soundcraft
- nieskategoryzowany Parrot
- nieskategoryzowany Antec
- nieskategoryzowany Vornado
- nieskategoryzowany Polaroid
- nieskategoryzowany Rocktrail
- nieskategoryzowany Prestigio
- nieskategoryzowany Aiwa
- nieskategoryzowany G3 Ferrari
- nieskategoryzowany JL Audio
- nieskategoryzowany LevelOne
- nieskategoryzowany Konica Minolta
- nieskategoryzowany AKAI
- nieskategoryzowany Tunturi
- nieskategoryzowany Razor
- nieskategoryzowany Digi
- nieskategoryzowany Mobicool
- nieskategoryzowany Axis
- nieskategoryzowany Deity
- nieskategoryzowany Vivolink
- nieskategoryzowany Westfalia
- nieskategoryzowany Hamilton Beach
- nieskategoryzowany Majority
- nieskategoryzowany Hayward
- nieskategoryzowany Neumärker
- nieskategoryzowany Rigol
- nieskategoryzowany Bixolon
- nieskategoryzowany Ergotools Pattfield
- nieskategoryzowany Novy
- nieskategoryzowany Hartke
- nieskategoryzowany Clatronic
- nieskategoryzowany Healthy Choice
- nieskategoryzowany Tronic
- nieskategoryzowany Dali
- nieskategoryzowany NEO Tools
- nieskategoryzowany Oregon Scientific
- nieskategoryzowany Lorex
- nieskategoryzowany Eventide
- nieskategoryzowany Optoma
- nieskategoryzowany Kisag
- nieskategoryzowany Rommer
- nieskategoryzowany Ariete
- nieskategoryzowany Carrera
- nieskategoryzowany Flame
- nieskategoryzowany Hifonics
- nieskategoryzowany Vogel's
- nieskategoryzowany Heidemann
- nieskategoryzowany Fuzzix
- nieskategoryzowany Focal
- nieskategoryzowany OnePlus
- nieskategoryzowany Tepro
- nieskategoryzowany LiftMaster
- nieskategoryzowany Viper
- nieskategoryzowany Napoleon
- nieskategoryzowany DBX
- nieskategoryzowany Princess
- nieskategoryzowany Christmaxx
- nieskategoryzowany Baby Jogger
- nieskategoryzowany Kicker
- nieskategoryzowany Amazon
- nieskategoryzowany Carson
- nieskategoryzowany Doepfer
- nieskategoryzowany TDE Instruments
- nieskategoryzowany Aluratek
- nieskategoryzowany Abus
- nieskategoryzowany Thorens
- nieskategoryzowany Bresser
- nieskategoryzowany Omnitronic
- nieskategoryzowany Livarno Lux
- nieskategoryzowany Olympia
- nieskategoryzowany Hama
- nieskategoryzowany Mackie
- nieskategoryzowany Juki
- nieskategoryzowany Microsoft
- nieskategoryzowany Marmitek
- nieskategoryzowany Eltako
- nieskategoryzowany Palmer
- nieskategoryzowany Sanitaire
- nieskategoryzowany FiiO
- nieskategoryzowany SE Electronics
- nieskategoryzowany Western Digital
- nieskategoryzowany Princeton Tec
- nieskategoryzowany Baby Annabell
- nieskategoryzowany Taylor
- nieskategoryzowany Duronic
- nieskategoryzowany Vincent
- nieskategoryzowany Smart-AVI
- nieskategoryzowany Maximum
- nieskategoryzowany Omega
- nieskategoryzowany Medel
- nieskategoryzowany Fein
- nieskategoryzowany Mattel
- nieskategoryzowany Goobay
- nieskategoryzowany Optex
- nieskategoryzowany BC Acoustique
- nieskategoryzowany Bush
- nieskategoryzowany Siméo
- nieskategoryzowany Schwaiger
- nieskategoryzowany New Pol
- nieskategoryzowany 4Garden
- nieskategoryzowany Sharkoon
- nieskategoryzowany Eheim
- nieskategoryzowany Watson
- nieskategoryzowany Saramonic
- nieskategoryzowany Mean Well
- nieskategoryzowany Gravity
- nieskategoryzowany Equip
- nieskategoryzowany DeepCool
- nieskategoryzowany Boso
- nieskategoryzowany Kemo
- nieskategoryzowany Terraillon
- nieskategoryzowany Sera
- nieskategoryzowany Aerotec
- nieskategoryzowany GA.MA
- nieskategoryzowany Deaf Bonce
- nieskategoryzowany VOX
- nieskategoryzowany Ferm
- nieskategoryzowany Insignia
- nieskategoryzowany Pelgrim
- nieskategoryzowany Walrus Audio
- nieskategoryzowany Ambient Weather
- nieskategoryzowany Playtive
- nieskategoryzowany Arris
- nieskategoryzowany Navman
- nieskategoryzowany Gabor
- nieskategoryzowany ZKTeco
- nieskategoryzowany Frilec
- nieskategoryzowany Jane
- nieskategoryzowany Hager
- nieskategoryzowany Extech
- nieskategoryzowany NANO Modules
- nieskategoryzowany GVM
- nieskategoryzowany Ravensburger
- nieskategoryzowany True
- nieskategoryzowany ECS
- nieskategoryzowany Franklin
- nieskategoryzowany Victrola
- nieskategoryzowany XPG
- nieskategoryzowany Orima
- nieskategoryzowany Infinity
- nieskategoryzowany Pentair
- nieskategoryzowany Solis
- nieskategoryzowany Denver
- nieskategoryzowany Harley Benton
- nieskategoryzowany Anker
- nieskategoryzowany Testboy
- nieskategoryzowany Pentax
- nieskategoryzowany Bushnell
- nieskategoryzowany Horizon Fitness
- nieskategoryzowany Berger & Schröter
- nieskategoryzowany Dynacord
- nieskategoryzowany Aspes
- nieskategoryzowany Orion
- nieskategoryzowany Ashly
- nieskategoryzowany Hitachi
- nieskategoryzowany Blumfeldt
- nieskategoryzowany Yale
- nieskategoryzowany JIMMY
- nieskategoryzowany FED
- nieskategoryzowany InfaSecure
- nieskategoryzowany Em-Trak
- nieskategoryzowany Rapoo
- nieskategoryzowany Tracer
- nieskategoryzowany Salton
- nieskategoryzowany IStarUSA
- nieskategoryzowany Technika
- nieskategoryzowany Emerson
- nieskategoryzowany Enhance
- nieskategoryzowany SereneLife
- nieskategoryzowany JennAir
- nieskategoryzowany Craftsman
- nieskategoryzowany Silverstone
- nieskategoryzowany Mooer
- nieskategoryzowany Ernitec
- nieskategoryzowany AKG
- nieskategoryzowany Vemer
- nieskategoryzowany Frigidaire
- nieskategoryzowany CyberPower
- nieskategoryzowany Azden
- nieskategoryzowany FeiyuTech
- nieskategoryzowany Roccat
- nieskategoryzowany Barazza
- nieskategoryzowany Klein Tools
- nieskategoryzowany MEE Audio
- nieskategoryzowany Black Diamond
- nieskategoryzowany AJA
- nieskategoryzowany Electro Harmonix
- nieskategoryzowany Scotsman
- nieskategoryzowany Marvel
- nieskategoryzowany Media-Tech
- nieskategoryzowany Sodapop
- nieskategoryzowany Summit
- nieskategoryzowany Trevi
- nieskategoryzowany Technaxx
- nieskategoryzowany Atlona
- nieskategoryzowany Elektrobock
- nieskategoryzowany Thermaltake
- nieskategoryzowany Amer
- nieskategoryzowany Fibaro
- nieskategoryzowany Simrad
- nieskategoryzowany ENTES
- nieskategoryzowany Soundskins
- nieskategoryzowany Ridgid
- nieskategoryzowany Minn Kota
- nieskategoryzowany GPX
- nieskategoryzowany Gefen
- nieskategoryzowany Lanaform
- nieskategoryzowany Martin
- nieskategoryzowany Rommelsbacher
- nieskategoryzowany American International
- nieskategoryzowany Ixxat
- nieskategoryzowany SEADA
- nieskategoryzowany Vivanco
- nieskategoryzowany Inkbird
- nieskategoryzowany Radial Engineering
- nieskategoryzowany Fulgor Milano
- nieskategoryzowany Quantum
- nieskategoryzowany MDT
- nieskategoryzowany Kelvinator
- nieskategoryzowany Inface
- nieskategoryzowany Asaklitt
- nieskategoryzowany Sencor
- nieskategoryzowany Emko
- nieskategoryzowany BDI
- nieskategoryzowany Hobart
- nieskategoryzowany Mistral
- nieskategoryzowany Elica
- nieskategoryzowany Raymarine
- nieskategoryzowany Powerfix
- nieskategoryzowany HiKOKI
- nieskategoryzowany Workzone
- nieskategoryzowany Tempo
- nieskategoryzowany EasyMaxx
- nieskategoryzowany Stinger
- nieskategoryzowany BABY Born
- nieskategoryzowany Seaward
- nieskategoryzowany Power Dynamics
- nieskategoryzowany Blackmagic Design
- nieskategoryzowany AEA
- nieskategoryzowany Gustard
- nieskategoryzowany Asko
- nieskategoryzowany Kanto
- nieskategoryzowany Vacmaster
- nieskategoryzowany Kathrein
- nieskategoryzowany Kalorik
- nieskategoryzowany Rockford Fosgate
- nieskategoryzowany DOD
- nieskategoryzowany Steinberg
- nieskategoryzowany Impact
- nieskategoryzowany Microboards
- nieskategoryzowany JUNG
- nieskategoryzowany Xtorm
- nieskategoryzowany Burg Wächter
- nieskategoryzowany Honey-Can-Do
- nieskategoryzowany Flavel
- nieskategoryzowany Foscam
- nieskategoryzowany Lumens
- nieskategoryzowany Senal
- nieskategoryzowany TOA
- nieskategoryzowany Newland
- nieskategoryzowany Byron
- nieskategoryzowany Monacor
- nieskategoryzowany Aputure
- nieskategoryzowany HQ Power
- nieskategoryzowany Ferplast
- nieskategoryzowany Daewoo
- nieskategoryzowany ADE
- nieskategoryzowany Hotone
- nieskategoryzowany Neutrik
- nieskategoryzowany Livington
- nieskategoryzowany Electro-Voice
- nieskategoryzowany Consul
- nieskategoryzowany Etekcity
- nieskategoryzowany BioChef
- nieskategoryzowany Wiha
- nieskategoryzowany Proviel
- nieskategoryzowany Kunft
- nieskategoryzowany Robinhood
- nieskategoryzowany Tetra
- nieskategoryzowany Grunkel
- nieskategoryzowany SLV
- nieskategoryzowany Sonnet
- nieskategoryzowany Novation
- nieskategoryzowany Silver Cross
- nieskategoryzowany Vicoustic
- nieskategoryzowany Havis
- nieskategoryzowany Becken
- nieskategoryzowany Haeger
- nieskategoryzowany AudioControl
- nieskategoryzowany Karma
- nieskategoryzowany NOCO
- nieskategoryzowany HT Instruments
- nieskategoryzowany OKAY
- nieskategoryzowany Smartwares
- nieskategoryzowany Elgato
- nieskategoryzowany Traeger
- nieskategoryzowany Magmatic
- nieskategoryzowany Porter-Cable
- nieskategoryzowany Noctua
- nieskategoryzowany Masport
- nieskategoryzowany Metabo
- nieskategoryzowany Audiolab
- nieskategoryzowany KS Tools
- nieskategoryzowany Galcon
- nieskategoryzowany Positivo
- nieskategoryzowany Adj
- nieskategoryzowany Mauser
- nieskategoryzowany Starlink
- nieskategoryzowany Richgro
- nieskategoryzowany Varaluz
- nieskategoryzowany Carlo Gavazzi
- nieskategoryzowany Tactical Fiber Systems
- nieskategoryzowany MEPROLIGHT
- nieskategoryzowany Mellanox
- nieskategoryzowany ShieldRock
- nieskategoryzowany SMS
- nieskategoryzowany PurAthletics
- nieskategoryzowany Longfian
- nieskategoryzowany OLLO
- nieskategoryzowany Yuer
- nieskategoryzowany Teia
- nieskategoryzowany KNEKT
- nieskategoryzowany Favero
- nieskategoryzowany Contemporary Research
- nieskategoryzowany Gator Frameworks
- nieskategoryzowany Stages
- nieskategoryzowany HDFury
- nieskategoryzowany Absco
- nieskategoryzowany Schatten Design
- nieskategoryzowany Car Jack
- nieskategoryzowany LEDs-ON
- nieskategoryzowany Wachendorff
- nieskategoryzowany Euky Bear
- nieskategoryzowany SPL
- nieskategoryzowany SureFire
- nieskategoryzowany Fontastic
- nieskategoryzowany ISi
- nieskategoryzowany Cyrus
- nieskategoryzowany Gold Note
- nieskategoryzowany Ketron
- nieskategoryzowany ETC
- nieskategoryzowany Interstuhl
- nieskategoryzowany AURALiC
- nieskategoryzowany EZ Dupe
- nieskategoryzowany Trent & Steele
- nieskategoryzowany IBEAM
- nieskategoryzowany Terratec
- nieskategoryzowany Gastronoma
- nieskategoryzowany Hoberg
- nieskategoryzowany Aroma
- nieskategoryzowany Reer
- nieskategoryzowany Transcend
- nieskategoryzowany Edilkamin
- nieskategoryzowany Axxess
- nieskategoryzowany Crunch
- nieskategoryzowany Wilson
- nieskategoryzowany InnoGIO
- nieskategoryzowany Goki
- nieskategoryzowany Zoofari
- nieskategoryzowany EGO
- nieskategoryzowany Kingston Technology
- nieskategoryzowany WilTec
- nieskategoryzowany Toro
- nieskategoryzowany AstralPool
- nieskategoryzowany Campart
- nieskategoryzowany ZLine
- nieskategoryzowany Müller
- nieskategoryzowany Ditek
- nieskategoryzowany Cotech
- nieskategoryzowany Gre
- nieskategoryzowany Sport-Elec
- nieskategoryzowany Humminbird
- nieskategoryzowany Dataflex
- nieskategoryzowany Dormakaba
- nieskategoryzowany Stairville
- nieskategoryzowany Snom
- nieskategoryzowany Vitek
- nieskategoryzowany Skil
- nieskategoryzowany Xvive
- nieskategoryzowany Geneva
- nieskategoryzowany Miomare
- nieskategoryzowany SureFlap
- nieskategoryzowany Casaria
- nieskategoryzowany QOMO
- nieskategoryzowany Alfatron
- nieskategoryzowany APA
- nieskategoryzowany Mophie
- nieskategoryzowany Brady
- nieskategoryzowany WHD
- nieskategoryzowany Anton/Bauer
- nieskategoryzowany Sound Devices
- nieskategoryzowany Govee
- nieskategoryzowany Magic Chef
- nieskategoryzowany Eurom
- nieskategoryzowany Match
- nieskategoryzowany Nuki
- nieskategoryzowany Dot Line
- nieskategoryzowany Digitalinx
- nieskategoryzowany Easyrig
- nieskategoryzowany Bolt
- nieskategoryzowany Beha-Amprobe
- nieskategoryzowany Sebo
- nieskategoryzowany Enermax
- nieskategoryzowany SoundMagic
- nieskategoryzowany Maestro
- nieskategoryzowany Clas Ohlson
- nieskategoryzowany RADEMACHER
- nieskategoryzowany Arctic Cooling
- nieskategoryzowany Sauber
- nieskategoryzowany Krysiak
- nieskategoryzowany Salicru
- nieskategoryzowany Laserliner
- nieskategoryzowany Zotac
- nieskategoryzowany Cocraft
- nieskategoryzowany Reflexion
- nieskategoryzowany XQ-lite
- nieskategoryzowany MySoda
- nieskategoryzowany Sumiko
- nieskategoryzowany Smith&Brown
- nieskategoryzowany Megasat
- nieskategoryzowany Kopp
- nieskategoryzowany Sogo
- nieskategoryzowany Salter
- nieskategoryzowany Park Tool
- nieskategoryzowany George Foreman
- nieskategoryzowany Hikmicro
- nieskategoryzowany Waterpik
- nieskategoryzowany Maytronics
- nieskategoryzowany EAT
- nieskategoryzowany Sonnenkönig
- nieskategoryzowany REVO
- nieskategoryzowany Ugreen
- nieskategoryzowany DPA
- nieskategoryzowany Crosley
- nieskategoryzowany Varta
- nieskategoryzowany Nutrichef
- nieskategoryzowany Constructa
- nieskategoryzowany Proline
- nieskategoryzowany Atomos
- nieskategoryzowany Adventuridge
- nieskategoryzowany Howard Leight
- nieskategoryzowany Casa Deco
- nieskategoryzowany Kiev
- nieskategoryzowany EXIT
- nieskategoryzowany Euromaid
- nieskategoryzowany Reloop
- nieskategoryzowany Snow Joe
- nieskategoryzowany Primewire
- nieskategoryzowany Swissvoice
- nieskategoryzowany Lorelli
- nieskategoryzowany XCell
- nieskategoryzowany Schellenberg
- nieskategoryzowany Cherry
- nieskategoryzowany Char-Broil
- nieskategoryzowany Greenworks
- nieskategoryzowany Rittal
- nieskategoryzowany BSS Audio
- nieskategoryzowany Newstar
- nieskategoryzowany Oreck
- nieskategoryzowany Timbersled
- nieskategoryzowany Lasko
- nieskategoryzowany Chandler
- nieskategoryzowany Flama
- nieskategoryzowany Yellow Garden Line
- nieskategoryzowany Microair
- nieskategoryzowany Sevenoak
- nieskategoryzowany Vivitar
- nieskategoryzowany Belkin
- nieskategoryzowany SWIT
- nieskategoryzowany PTZ Optics
- nieskategoryzowany Zeiss
- nieskategoryzowany Bebob
- nieskategoryzowany Heckler
- nieskategoryzowany Morley
- nieskategoryzowany Generac
- nieskategoryzowany Sescom
- nieskategoryzowany Drake
- nieskategoryzowany Kramer
- nieskategoryzowany BLANCO
- nieskategoryzowany Gen Energy
- nieskategoryzowany KanexPro
- nieskategoryzowany Lian Li
- nieskategoryzowany Kahayan
- nieskategoryzowany Lewitt
- nieskategoryzowany Sky-Watcher
- nieskategoryzowany Wimberley
- nieskategoryzowany Kopul
- nieskategoryzowany BZBGear
- nieskategoryzowany K&M
- nieskategoryzowany Serpent
- nieskategoryzowany RGBlink
- nieskategoryzowany Glide Gear
- nieskategoryzowany Hosa
- nieskategoryzowany Vortex
- nieskategoryzowany Cranborne Audio
- nieskategoryzowany SmallRig
- nieskategoryzowany DEERSYNC
- nieskategoryzowany ToughTested
- nieskategoryzowany Arkon
- nieskategoryzowany Fiilex
- nieskategoryzowany Platinum Tools
- nieskategoryzowany Trijicon
- nieskategoryzowany Xcellon
- nieskategoryzowany Intellijel
- nieskategoryzowany CEDAR
- nieskategoryzowany Rupert Neve Designs
- nieskategoryzowany BirdDog
- nieskategoryzowany Pawa
- nieskategoryzowany Erica Synths
- nieskategoryzowany Key Digital
- nieskategoryzowany KJB Security Products
- nieskategoryzowany Whirlwind
- nieskategoryzowany Anywhere Cart
- nieskategoryzowany Soundsphere
- nieskategoryzowany Lemair
- nieskategoryzowany Toyotomi
- nieskategoryzowany TrekStor
- nieskategoryzowany Ideal
- nieskategoryzowany Apantac
- nieskategoryzowany Stamina
- nieskategoryzowany Spanninga
- nieskategoryzowany Pansam
- nieskategoryzowany NUK
- nieskategoryzowany JILONG
- nieskategoryzowany OBH Nordica
- nieskategoryzowany ABB
- nieskategoryzowany SRS
- nieskategoryzowany Thermador
- nieskategoryzowany Wolfcraft
- nieskategoryzowany Soler & Palau
- nieskategoryzowany Monzana
- nieskategoryzowany Finlux
- nieskategoryzowany Challenge
- nieskategoryzowany Goodis
- nieskategoryzowany Bestron
- nieskategoryzowany Rio
- nieskategoryzowany Oromed
- nieskategoryzowany Atosa
- nieskategoryzowany Twelve South
- nieskategoryzowany Rotel
- nieskategoryzowany Lexmark
- nieskategoryzowany Waterdrop
- nieskategoryzowany Atlas
- nieskategoryzowany Agfa
- nieskategoryzowany C2G
- nieskategoryzowany Sensiplast
- nieskategoryzowany Swan
- nieskategoryzowany Dangerous Music
- nieskategoryzowany Lumantek
- nieskategoryzowany Kluge
- nieskategoryzowany Devialet
- nieskategoryzowany IFi Audio
- nieskategoryzowany Crosscall
- nieskategoryzowany Cabasse
- nieskategoryzowany Acti
- nieskategoryzowany ACME
- nieskategoryzowany Anslut
- nieskategoryzowany Arthur Martin
- nieskategoryzowany Outwell
- nieskategoryzowany Sitecom
- nieskategoryzowany Logik
- nieskategoryzowany Fortinet
- nieskategoryzowany Profilo
- nieskategoryzowany Ernesto
- nieskategoryzowany Eldom
- nieskategoryzowany Maxxmee
- nieskategoryzowany Plant Craft
- nieskategoryzowany Celestron
- nieskategoryzowany Matrox
- nieskategoryzowany Kubo
- nieskategoryzowany Flir
- nieskategoryzowany Ergobaby
- nieskategoryzowany Geuther
- nieskategoryzowany Trixie
- nieskategoryzowany GeoVision
- nieskategoryzowany Chacon
- nieskategoryzowany Astro
- nieskategoryzowany InFocus
- nieskategoryzowany Glem Gas
- nieskategoryzowany Proctor Silex
- nieskategoryzowany Creda
- nieskategoryzowany Topeak
- nieskategoryzowany Intel
- nieskategoryzowany Kress
- nieskategoryzowany QSC
- nieskategoryzowany Beyerdynamic
- nieskategoryzowany Patching Panda
- nieskategoryzowany Kambrook
- nieskategoryzowany Berner
- nieskategoryzowany Cadac
- nieskategoryzowany Genaray
- nieskategoryzowany Cablexpert
- nieskategoryzowany Roxio
- nieskategoryzowany WHALE
- nieskategoryzowany Noveen
- nieskategoryzowany GMB Gaming
- nieskategoryzowany Blade
- nieskategoryzowany Ipevo
- nieskategoryzowany Waldbeck
- nieskategoryzowany Fanvil
- nieskategoryzowany IHome
- nieskategoryzowany Waves
- nieskategoryzowany Satechi
- nieskategoryzowany Xaoc
- nieskategoryzowany Syma
- nieskategoryzowany Lanberg
- nieskategoryzowany Butler
- nieskategoryzowany Vankyo
- nieskategoryzowany Arovec
- nieskategoryzowany Adam Hall
- nieskategoryzowany Murr Elektronik
- nieskategoryzowany TDK-Lambda
- nieskategoryzowany Ciclo
- nieskategoryzowany Sonoff
- nieskategoryzowany SecureSafe
- nieskategoryzowany CubuSynth
- nieskategoryzowany Yorkville
- nieskategoryzowany Neewer
- nieskategoryzowany Omnires
- nieskategoryzowany Klavis
- nieskategoryzowany Manitowoc
- nieskategoryzowany Joranalogue
- nieskategoryzowany Aconatic
- nieskategoryzowany WyreStorm
- nieskategoryzowany Artecta
- nieskategoryzowany NordicTrack
- nieskategoryzowany Eliminator Lighting
- nieskategoryzowany Christmas Time
- nieskategoryzowany ColorKey
- nieskategoryzowany Apollo Design
- nieskategoryzowany ChyTV
- nieskategoryzowany JoeCo
- nieskategoryzowany Holosun
- nieskategoryzowany Nureva
- nieskategoryzowany Panamax
- nieskategoryzowany Sonifex
- nieskategoryzowany Vertex
- nieskategoryzowany ARC
- nieskategoryzowany FBT
- nieskategoryzowany Andover
- nieskategoryzowany Black Lion Audio
- nieskategoryzowany Manfrotto
- nieskategoryzowany Crucial
- nieskategoryzowany Titanwolf
- nieskategoryzowany Uplink
- nieskategoryzowany Mybeo
- nieskategoryzowany Medicinalis
- nieskategoryzowany CSL
- nieskategoryzowany Bearware
- nieskategoryzowany Liam&Daan
- nieskategoryzowany Traco Power
- nieskategoryzowany Perfect Christmas
- nieskategoryzowany Core SWX
- nieskategoryzowany Universal Audio
- nieskategoryzowany 8BitDo
- nieskategoryzowany PCE
- nieskategoryzowany Warm Audio
- nieskategoryzowany Drawmer
- nieskategoryzowany Velbus
- nieskategoryzowany AirTurn
- nieskategoryzowany Orava
- nieskategoryzowany Holzmann
- nieskategoryzowany Blizzard
- nieskategoryzowany Inverx
- nieskategoryzowany Scanstrut
- nieskategoryzowany Jinbei
- nieskategoryzowany Expressive E
- nieskategoryzowany Gra-Vue
- nieskategoryzowany SurgeX
- nieskategoryzowany MuxLab
- nieskategoryzowany NuTone
- nieskategoryzowany Heitronic
- nieskategoryzowany Pentagram
- nieskategoryzowany RTS
- nieskategoryzowany Ocean Matrix
- nieskategoryzowany MAK
- nieskategoryzowany Dobot
- nieskategoryzowany Ocean Way Audio
- nieskategoryzowany Nearity
- nieskategoryzowany LifeSpan
- nieskategoryzowany Multibrackets
- nieskategoryzowany Urbanista
- nieskategoryzowany Hecate
- nieskategoryzowany ADDAC System
- nieskategoryzowany Hurricane
- nieskategoryzowany Inverto
- nieskategoryzowany Kitchen Brains
- nieskategoryzowany Leotec
- nieskategoryzowany Solplanet
- nieskategoryzowany Alutruss
- nieskategoryzowany AVPro Edge
- nieskategoryzowany Uniropa
- nieskategoryzowany Synco
- nieskategoryzowany Christie
- nieskategoryzowany Peak Design
- nieskategoryzowany MIOPS
- nieskategoryzowany JMAZ Lighting
- nieskategoryzowany Edelkrone
- nieskategoryzowany Amaran
- nieskategoryzowany Hortus
- nieskategoryzowany Enttec
- nieskategoryzowany Defender
- nieskategoryzowany Hawke
- nieskategoryzowany Feelworld
- nieskategoryzowany Bellari
- nieskategoryzowany Altman
- nieskategoryzowany FoxFury
- nieskategoryzowany JK Audio
- nieskategoryzowany Betty Bossi
- nieskategoryzowany Eller
- nieskategoryzowany Grimm Audio
- nieskategoryzowany Rotatrim
- nieskategoryzowany Aguilar
- nieskategoryzowany Claypaky
- nieskategoryzowany ESE
- nieskategoryzowany Digitech
- nieskategoryzowany CAD Audio
- nieskategoryzowany Altrad
- nieskategoryzowany Black Hydra
- nieskategoryzowany Merging
- nieskategoryzowany Orange
- nieskategoryzowany Digigram
- nieskategoryzowany Renogy
- nieskategoryzowany UDG Gear
- nieskategoryzowany Mutec
- nieskategoryzowany SunBriteTV
- nieskategoryzowany DMT
- nieskategoryzowany ICC
Najnowsze instrukcje dla nieskategoryzowany

28 Października 2024

28 Października 2024

27 Października 2024

27 Października 2024

27 Października 2024

27 Października 2024

27 Października 2024

27 Października 2024

27 Października 2024

27 Października 2024